Planning a new double-stud house — what should I change?

My wife and I are planning a 2,100-square-foot house in Massachusetts. Here’s the plan: a south-facing wall with glazing equal to 13% of the 1st floor area. A 5″ radiant slab on grade with 4′ frost wall on footings insulated with 4″ of xps underneath with a stepped foundation top to minimize thermal bridging.
We were planning a 10 1/2″ cavity double-stud wall with dense-pack damp-spray cellulose and lots of air sealing. Huber Zip System exterior sheathing with strapping and vertical pine siding sealed on all sides for a rainscreen wall.
The ceiling on the second floor would be mostly vaulted with 2×12 rafters with dense-packed cellulose. Our plan was to put 2″ of isocyanurate on the outside of the sheathing and do a cold roof of exposed fastener metal roofing.
For systems we would have all radiant upstairs and down, heated by a Polaris propane water heater. Hot water would be tankless on-demand propane. We would install an HRV system with intakes in the upstairs and downstairs baths as well as the kitchen and supply lines in the bedrooms and living room.
We are also toying with doing photovoltaics due to the availability of Solar Renewable Energy Credits here, and also a solar hot water pre-heat system, in which case we would eliminate the tankless and use a heat exchanger with the Polaris.
I don’t really know what I’m doing so any and all advice would be appreciated before we start and I royally screw this up!
Thanks in advance. – Noah Kaput
GBA Detail Library
A collection of one thousand construction details organized by climate and house part
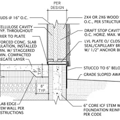
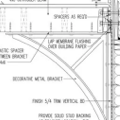
Replies
I should also mention that we have appropriately angled awnings on the south face and plan to do cellular blinds on the interior as added insulation. The windows will be Pella architect series unless Marvin beats them,
Noah,
Some feedback:
1. I'm not in favor of in-floor hydronic heat. It's a very expensive way to heat a house. If you improve your thermal envelope, you can install a much cheaper heating system.
2. Propane is a very expensive fuel -- much more expensive than fuel oil.
3. If you buy a Polaris water heater for space heat, you don't need to buy an on-demand water heater for domestic hot water. The Polaris can do both. (It better -- it's really expensive.)
4. You don't mention what type of windows you are installing. Think about air sealing; think about thick insulation; think about really good windows; and then you can have a much cheaper mechanical system.
Thanks for the response! Everything ties together so that if we don't do radiant heat then we'll have to eliminate the slab so we're not walking around on a cold stone all winter. If we eliminate the slab then we need a crawlspace and 1st floor deck with it's associated costs and we need to raise the house higher due to a high water table, more fill, foundation, etc.
Propane was chosen in the hopes that not much would be needed! I was under the assumption that it burns cleaner but also, due to space concerns, I liked that the fuel is stored outdoors.
My thoughts on the on demand was that it would be more efficient than heating a tank full of water all year round for us to use a pretty small amount of hot water. Here in Mass., we would need a heat exchanger to use the same appliance for heat and hot water and the costs for the heat exchanger is similar to that of the on demand unit.
As far as the windows go, I would love to have triple pane, krypton filled windows but I have always been scared off by the price, the style/size/color selection, and the time-testedness of the products as well as the longevity of the manufacturers.
Thanks again, I've already gotten so much useful info from this site! What a resource!
Noah,
If you install continuous horizontal foam insulation under your slab, as well as vertical insulation at the perimeter of the slab, you won't need in-floor heat.
If your house is well designed, your in-floor heat won't come on for very many hours each day anyway, so don't expect the "warm-toes" phenomenon. The slab will just be at room temperature for most of the time anyway -- unless you've made some serious errors with your envelope.
With radiant heat, here's the rule: The warmer the floor, the worse the house.
That is great to hear! What type of heat would you recommend then? Regular old baseboard? or Runtal style radiators? We are not into mini-splits, and need something thermostatically controlled for the bank. If not for the bank, I'd have a sealed combustion wood stove and call it a day!
Also, do you think my use of Pella or Marvin windows is going to be a weak enough link to really hurt my envelope?
Noah,
A furnace is cheaper than a boiler, so there is no reason to install hydronic heat.
I wouldn't build a house in Massachusetts without triple-glazed windows. I'd make the house smaller if I had to, and I'd order the windows I wanted.
I would definitely not do all radiant floor up and down but rather limit the radiant slab to 30-50% of the floor area, smaller as the envelope improves. I like doing radiant in the entry, kitchen, bathrooms and in front of the fireplace in the living area. It creates a "virtual wood stove" where you have warm areas that send heat out to cooler areas through natural air circulation. If you want more slab area for thermal mass consider having warmer areas and cooler areas where you have some radiant manifolds circulating warm water and some circulating the return water on the way back to the heat exchanger. Too much radiant floor area means that if the floor feels warm your house is over heating.
I agree that propane is expensive fuel. Ted Clifton has been using split heat pump water heaters with a COP in the range of 4 to heat a tank of water to heat the floor. This combines well with grid-tie solar PV but I've found it challenging to implement. If sticking with propane take a look at A O Smith's Vertex condensing heater. If you separate the floor from the water in the tank with a flat plate heat exchanger you can use a single water heater to do the floor as well as the domestic hot water.
I'm guessing that the 10 1/2" wall thickness is from two 2x4 walls with a 2x4 purlin at the mid-level. I prefer to use a split 2x6 purlin so I can use 2x10 lumber for the upper top plate which gives me a 9 1/2" wall 9 1/2" also rips conveniently out of 4x8 plywood but I think 2x10 top plates are easier to work with in the field (and I prefer JM Spider but I'm in the south) I very much agree with Martin about the importance of the windows.
Just a few immediate thoughts, I hope they are helpful.
We've built several double-wall homes. I would make the walls thicker - we build them completely separately, no common plates. And I would size the rafters for structure and then gusset down for insulation - you can eliminate both the bridging & the foam that way. And I'd use dense-pack instead of damp-spray.
I wrote a piece in Journal of Light Construction a while ago on one of our houses - e-mail me at dan at kolbertbuilding dotcom and I'll send you a pdf. Or you can find it here - http://www.jlconline.com/cgi-bin/jlconline.storefront/4e751b980022e98e271a0a323cb40668/Product/View/0906buil
what are people's thought on cellulose vs blown fiberglass? I know the obvious 'greener' aspect, as well as densities, however fiberglass carries a slightly higher r per inch, and I know every insulator I have talked to will blow fiberglass any day over cellulose, so around here they tend to price it almost the same.
will an r-40+ double stud cellulose perform better then similar thickness fiberglass however?
Jesse,
Choosing a contractor with experience installing blown-in insulation in a double-stud wall is more important than whether the insulation is cellulose or blown-in fiberglass. There are several ways that such installations can go wrong -- so get a good contractor.
Noah,
I am guessing you don't have Natural gas where you are building and are relying on propane and electric.
Here is the BEST method to keep operating costs down. Solar on roof is great idea. Nothing beats free electric!!! Follow by installing 300 Amp electric service to heat your systems and hot water also for your AC system. Electrify everything then JUMP the meter and install a second service panel that runs OFF THE METER so everything tied into it is free. Heck with NSTAR or EVERSOURCE, they have been screwing us for years!!! Screw them right back. double lug the min meter pan and one panel is paid for and the other is free. :) I do this for elderly clients all the time up here. Those poor people get next to nothing for SS and huge bills in the winter for heating and sweat like dogs in summer because they cant afford cooling. Well, Robin Hood to the rescue!!! We jump them out and improve their lives.
The higher R/inch of fiberglass vs. cellulose isn't worth much in a double-studwall. The R/$ is probably more important, since it frees up budget to apply toward other performance aspects with a higher return. The thermal mass of 10.5" of 3-3.5lbs density cellulose also has a measureable hermal benefit, and the hygric buffering capacity of cellulose is protective of the structural wood. Stick with cellulose, unless bids for fiberglass come in cheaper, and don't sweat the R-value.
Even though having rainscreened siding would meet code in MA without an interior vapor retarder (other than standard latex paint), Kohta Ueno's data on double-studwalls in Devens MA done for Building Science Corp show that the peak sheathing moisture in those assemblies can be quite high- high enough to be concern well into May where it's warm enough to support mold. The higher the R, the colder the wintertime temp at the sheathing, and a code prescriptive based on R20 cavity fill isn't necessarily valid for the ~R40 wall you're building. An interior side smart vapor retarder like MemBrain under the wallboard is cheap insurance.
What others have said about radiant floors and propane in a high-R house. At recent years' pricing heating with mini-splits is less than half the cost of heating with propane, and with a 13% glazing fraction facing south you'll need the air conditioning even if you have reasonable overhangs shading. It's not that there is NO comfort benefit to a radiant slab in a high-R house, only that it's quite subtle compared to the cushy comfort of radiant floors you would get in a code-min house. Even though the heating bills will be small, is it worth doubling the cost? And with New England's grid-mix heating with mini-splits is substantially lower-carb than condensing propane.
It doesn't take anything LIKE a 300 amp service to heat & cool and provide domestic hot water to a 2100' high-R house in MA. Unless you are going to heat all that hot water with on-demand tankless electric HW heaters (bad idea on a number of accounts) most homes would do fine with 100A or less. Net metered PV at full retail is still in effect in MA (though in some regions the cap has been met, but should be raised fairly soon, given that it's such a conservatively low number to begin with), and would be more useful to both you and the local grid if you opt to install solar. The value of the SRECs will probably be close to nothing by 2025, but for the time being they're still worth something.
A heat pump water heater would be cheaper to install and cheaper to run than a propane tankless. They also provide a modest amount of "free" dehumidifcation/cooling during the warmer months out of the year. The half of the heat going into the water from conditioned space is a modest "extra" heat load in winter, but not enough to affect heating equipment sizing in a house with a tiny load like yours. If that fraction of the water-heating heat is being supplied by a mini-split, it's half the cost of heating that fraction with propane. If sized so that it can fill the biggest tub in the house, the large majority of homes would be satisfied with a heat pump water heater. From both an up-front cost and maintenance/reliability point of view, value of a solar thermal pre-heating isn't there unless your hot water heating needs are quite high. At typical HW heating needs most people would be better off spending that money on increasing the size of the PV array. Even when it's offsetting a high-cost fuel like propane or resistance electricity it's really tough to make the solar thermal numbers work in your favor.
At 2" of above-the-deck polyiso you would be WOEFULLY short of the minimum 40% of total R you'd need for dew point control on an unvented roof in a MA climate. A code-min R49 total-R would require R20 of that to be above the roof deck. If you went with 2x8 rafters and cellulose cavity fill ( about R27) with 2" of polyiso (R13) followed by 2" of EPS (R8.4) above that you'd be just shy of code-min from an R-value point of view, but would would still meet code on a U-factor basis. The reason for the dual foam types is that if it were all polyiso the outer couple inches would under-perform it's labeled R in mid-winter in a MA climate by quite a bit, but if EPS it would over-perform it's labeled R, while keeping the other 2" of polyiso warm enough to still do OK. The labeled R of that stackup would be about R21, while 4" of polyiso would be R25-ish, but during cold weather the EPS/polyiso stackup always performs at R20 or better all year long, whereas all-polyiso might average as low as R17-ish in January, even though it would average R25 or better in April. In terms of dew-point control, the wintertime performance matters.
We also build double wall houses. I agree with Dan about using plywood "plates" on the wall to minimize thermal bridging as well as building down the rafters to minimize thermal bridging in the roof. Also there is no reason to have any thermal bridging in your floor; insulate the sides as well as the bottom of the slab (and the sides of the frost wall to keep the temperature of the soil under the floor warmer). Use triple glazed windows! Harvey Industries sells their triple glazed for about $40 more than the standard double glazed. When you eliminate the thermal bridging in the floor, it will stay close to room temperature, not "stone cold". At this point your house is perfect for mini split heat pumps which runs on electricity; no fuel to store and with a properly sized PV system, you can be paying $0 for your heat and everything else.
I left out the fact that a tight house is a must. Our first house after we started paying attention to air leaks was under 1ACH50, so it's not that difficult if you pay attention. And definitely do a blower door test after framing and windows, prior to insulation, so leaky areas can be fixed. The easiest way with a truss roof is either drywall the ceiling prior to building the interior partitions, or install an air barrier at the bottom of the trusses - again prior to interior walls.
Bob,
I've seen the suggestion of drywalling the trusses before framing the interior partitions a couple of times but can't get my head around the logistics.
How do you deal with the difference in heights of the interior and exterior walls? How do you stand them and lap the top plates? How does the electrician run his wires in and out of the truss space? How do you deal with truss uplift. It sounds like like an intriguing idea, but a nightmare to actually do.