Tips for Cutting Rigid Foam Insulation

What are people doing to cut EPS foam and control the dust and debris generated, considering the toxicity of the fire retardant chemicals in it?
Some argue the fire retardants are OK, because they don’t leach out of the foam much. But it seems to me that the environmental release is probably dominated by the dust and debris generated.
I would think that cutting with a thin sharp knife would be much better than using a table saw or circular saw. But are there easy ways to get as good as straight cut? What kind of knife? One made for foam, or a utility knife, or a bread knife? What about a hot-wire knife?
Thanks!
GBA Detail Library
A collection of one thousand construction details organized by climate and house part
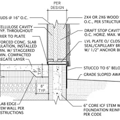
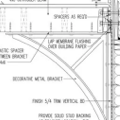
Replies
http://www.finehomebuilding.com/how-to/video/cutting-rigid-insulation.aspx
Charlie,
Many years ago, I reviewed a bunch of insulation knives. The Insul-Knife was the best one I found:
http://www.demandproducts.com/item.php?=&sku=GROUPINSUL
However, I made a sharpened taping knife years ago, as suggested in the Fine Homebuilding video, and it's still the easiest tool to use -- because it's the right length, and not as unwieldy as the Insul-Knife.
Thank Malcolm! That's perfect.
Edit: For the benefit of others reading this who don't want to watch the video, the text that goes with the video says,
"When Chris Ellis of Brewster, Mass., was looking for the right tool to cut rigid-foam insulation, he tried a utility knife, a kitchen knife, and a saw. None of those options worked especially well. So Chris created something that works beautifully. As Chuck Miller demonstrates in this video tip, a 3-in. or 4-in. putty knife with a sharpened blade cuts through the foam like butter. "
He cuts against a straight edge clamped to the foam.
Thanks Martin. Sounds like a sharpened putty knife is the way to go.
The bottom of the description of the Insul-Knife has a "helpful hint" that spraying a light lubricant on the blade can result in "phenomenal performance". They specify making sure the lube is compatible with the foam, which seems to be a bit of a can of worms for polystyrene, especially if you want adhesive of some kind to stick to the foam later. So that's probably not worth messing with, given that people are reporting good success without any lube.
Does anyone know if this works for low density EPS foam?
I've tried lots of knives and what worked best for me was to use a 7.25" thin curb blade on a table saw. This works well for a clean cut, but it's messy. The dust is hard to capture because of static electricity.
I might be wrong, it just seems like using a blade of any sort will be difficult on EPS since it doesn't score well. As long as I'm asking, do the 15 & 25 psi versions of EPS cut better?
Rick,
Type I density foam is a PIA to work it. If you lean on it wrong it falls apart. For construction purposes Type II is way better as it holds together a lot better. 95% of all ICF's out there are Type II
Hot knives work best but they are slow going but when you take into account the mess that cutting knives leave behind and the time it take to clean up that mess. Hot knives come out ahead.
It all depends where the foam is going and if a clean site is needed. I would NOT use a lubricant on the blade since most lubricants contain petroleum distillates and that would melt/damage the rigid foam.
You could use a lubricant like DuPont Teflon Non-Stick. It's pure Teflon with resin binders- no petroleum. I know- I used to sell the stuff.
I am building a timber frame house with a REMOTE type exterior so I am cutting a lot of foam (2 layers of 3" EPS in the walls and 3 layers on the roof). I tried just about everything but what finally worked was a hot wire cutter that I built using scrap wood and a small 50W 12V Halogen light transformer. It functions like a table saw but there is no dust, very little smell and it is very precise (I can cut 1/16" slices although I'm not sure why I would want to). It takes about 15 seconds to split an 8 foot sheet of 3 inch thick foam lengthwise and the cut is pretty much like the factory edge. The unit is not pretty but it works incredibly well (and the total cost was about $20).
I like your hot knife idea. What do you use for cutting wire and how do you wire to the transformer? Is it wired as a dead short and the transformer limits the current? Can you control the temperature or is that unimportant?
Thanks,
Chris
I read down the post and see answers to some of my questions!
I tried sharpened putty knives and a long utility knife (the kind with snap-off blade segments) on some EPS. The long utility knife cut much more cleanly. Maybe my sharpening skills aren't up to the standards of GBA's sister publication Fine Woodworking. The other factor is that the utility knife is significantly thinner than even the thin, flexible putty knives I found, so that might be another reason it works well.
The segmented utility knife I used: http://www.dewalt.com/tools/hand-tools-cutting-tools-knives-dwht10038.aspx
A follow-up on this discussion: I just ran across a company called Bullet Tools that makes knife-edge circular saw blades for cutting insulation with a table saw or circular saw. They call them "CenterFire" blades.
http://www.bullettools.com/insulation/insulation-tools-rigid-foam-cutters
From the reviews on Amazon I gather that people find it works well on EPS and XPS, but generates a small amount of very fine dust if you use it on polyiso
They also have knife blades for reciprocating saws. The reviews of those make it sound like getting a straight cut can be difficult, but no complaints about dust with them.
Anyone tried these?
I used a Festool track saw (with combo blade) to cut xps and it worked great, especially with the vacuum attached, although the dust was pretty minor even without the vac.
Rob can you post some pictures of your contraption? It sounds awesome.
The sharpened taping knife looks like it would be hard to beat...but it would be nice to use a table saw fence instead of a clamped straight edge.
Here's a few photos Jim (and they certainly are contraptions!). The table is a 2x4 frame with OSB top (originally a concrete form). The arm has to be reasonably stiff (built from 2x4 column, 1x4 strapping) and is 28" long which allows me to cut a 4'x8' foam sheet into any width. The cutter is nichrome wire (jacobs-online.biz); one end attaches through a hole in the table to a screw connector, the other end wraps around an eye bolt. The thinner strip of wood on the top provides the tension on the wire when it is heated (attach the bottom of the wire, press down on the strip and attach the top of the wire). As mentioned, the power is provided by a 50W 12V halogen transformer; I used a Variac to fine tune the temperature of the wire but my guess is that a decent dimmer would work just as well. The fence has a single screw at one end and pivots to adjust the width of the cut. When I make an adjustment I just screw the other end of the fence to the tabletop. Not pretty but it works! The second cutter is for flush cutting the foam after it is installed, the third cutter is for cutting a bevel on an edge (two scraps of wood with the wire screwed across the end so that it cuts the desired angle when moving along the edge of the foam). All just plug in to the same power supply. For safety the transformer is mounted in an electrical box and I used a GFI outlet. Let me know if you need any further information.
Rob,
Thanks for your photos and detailed explanation. Your post is a great example of why I love the GBA community.
Alright...I'm just building one house, so I'm going to sharpen a taping knife. Rob, if I were you, I'd be refining and patenting that cutting set. I'm already in too far over my head to think about making one...but if I could have one for just three easy payments of $39.99...:)
Thanks for the pictures!
Martin: I feel that I should be the one thanking you. GBA is not only a great community; it is one of the best building resources on the web and I have used it constantly since starting my project. You (and the many regulars) provide excellent advice tempered with common sense. It is nice to be able to contribute a little back.
Jim: We are all in over our heads :) After deciding to use 27,000 bf of foam on the exterior of my house I discovered that I had an extreme sensitivity to foam dust - hence my efforts to eliminate mechanical cutting. If the foam is an inch thick then a knife works great. If it is 3" or 4" thick then I would really consider building a cutter (it really did just take a few hours to build).
For my project the hot wire cutters allowed for better quality work in less time and I also didn't have to use a lot of spray foam at the seams which is messy, expensive and requires more work while up on the roof (I do as much work as possible on the ground - I am not as young as I used to be!). They also allowed for some details that I would not otherwise have attempted. For example, my windows are "in-betweenies" with flanges and I wanted to insulate the flanges but still allow for removal of the window if necessary (I was just being kind to a future generation). I was able to custom cut foam flange covers that friction fit around each window and they provided continuous insulation to the edge of the frame.
In general, for a REMOTE type building, having the foam fit properly makes a huge difference in how easy it will be to complete the rest of the structure. I have attached a few images. Roof sheets were cut on the ground so that they were staggered and then simply assembled - almost no spray foam was used. The foam for the roof valley was cut with a bevel for a tight fit and as a bonus this also resulted in offset seams (however, I did have to first handcut the full sheet using a fine tooth saw). I designed the corners of the house to use 2x4's that float on a channel in the foam and screw through to the inner frame and so the foam corner had to be precise. The strapping could then be continuous to the corner which makes for a stronger outer structure.
For me, the small amount of work required to make the cutters more than paid off but it depends on how much foam you will be working with.
I realize it's an older post, but what gauge wire did you use Rob? Thanks.
Jaccen,
The GBA site does not send out notifications, so Rob may not see your question. Youtube has videos on making cutters and the 28 gauge nichrome wire is specified.
Hi Jaccen,
I did happen to see this post. I used 24 GA wire, 28 would be fine but may break more often. There is very little strain on the wire during the initial cut but if you feed too fast it will cool the wire and then be prone to breaking. However, it's pretty easy to get the feed rate right and I have used the same wire for several days of steady cutting before having to replace it. Also, make sure you have a good way to adjust the temperature of the wire.
Hi Rob. Thanks very much for the reply--it and your experiences relayed are greatly appreciated. Cheers.
Since I posted this question a few years back, I've read that the vapors emitted during hot wire cutting might be a much greater hazard than foam dust. Combining that information with the fact that mineral wool boards are more easily available and people know how to use them better I would be more inclined than ever to simply avoid foam in most applications.