Has anyone constructed a “wood” basement floor over dirt?

Im redoing my partial basement, to make it all into usable living space, which involves digging out half of it and removing a current half slab to increase headroom, and adding to the foundation/footing as needed. Is there any real reason to pour a slab after this is all done?
I would love input from someone who has put a vapor/water barrier, some foam insulation between 2=4 sleepers, and then used some form of wood flooring that would work for higher humidity situations.
l am unable to see any code about it in wa, and more than that want to know peoples long term experience. concrete is soooo not environmentally correct if not necessary
thanks
rob
GBA Detail Library
A collection of one thousand construction details organized by climate and house part
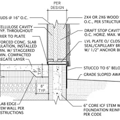
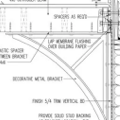
Replies
Rob,
From a moisture perspective, it's the rigid foam and the vapor barrier that are doing the work. (Generally, you want to install the rigid foam first, and then install the polyethylene vapor barrier above the rigid foam.) Above the polyethylene, the finish materials are up to you -- and your local code inspector, of course.
I think that concrete is the best material to install above the polyethylene, in terms of durability and price. But if you are willing to replace any components that rot, or if you don't mind introducing pressure-treated lumber (with associated chemicals) into the interior of your house, go ahead and experiment. If these materials rot in the future, you'll need to replace them. You'll have to consider the wooden components as sacrificial layers.
Obviously a slab would be typical and helpful as a support for the lumber, but I think you can do what you are considering. As Martin says, the most important part is stopping upcoming moisture from the ground, which can be done with a good job of sealing with poly and rigid foam (and the foam is not critical but a good idea for insulation value). The concrete does little to block moisture, and since you are covering the slab and making it an internal, I think you could save the money and effort.
Thanks.
this was my thinking, that it was about vapor and concrete doesn't stop that anyway...and just because it is conventional doesn't mean it makes sense...
and
i'm wondering if anyone has practical experience with something like this inplace for a number of years...in my head i wouldn't think there would be any additional moisture issues, perhaps less than a slab that isn't vapor barriered, but that doesnt mean that is what really happens on the ground.
the earth is mostly sand with some clay and is humid. i plan on wrapping the floor and going up the walls that are buried prior to framing/sinsulaitng and then sheetrock. i was thinking of putting support "ribbons" of concrete every 8' or so for the 2x material on 16" centers, , 1/2" ply and then straight over with flooring, the 2x would be supported by the earth and the concrete in case things shifted...
i don't believe that i can use pressure treated wood on interior living space, and don't really know that code guys would be happy with this setup....only because it's atypical.
any practical application feedback greatly appreciated
rob
http://www.americanpoleandtimber.com/pdf/treated_wood_specguide.pdf
Just make sure you use lumber stamped for ground contact; and that you let it dry before building; make sure its properly stacked (so it won't twist and curl) and out of sun and wind as it dries.
http://www.popularmechanics.com/home/how-to-plans/woodworking/4217636
That is a lot of copper, by weight ... making it heavy and dense ... a real bear on saw blades. Use only stainless steel fasteners; preferably hex heads and star drives. Fasteners are expensive. Galvanized is not reliable and who wants to use a hammer anyway, these days.
Sto-cote industries makes a cross linked water barrier but like all water barriers, a great deal of care and gentle handling is needed to prevent punctures. Polyurethane caulks will work just fine for seam and joint sealing; once the lumber dries.
http://www.goodcommonsense.net/tutuffxf9x100.html
You will be making a big investment but I would be concerned about the resale value and the marketability of the home. You might call an appraiser, a real estate agent and if you have a good relationship with a lender.
What would happen if a lender would not make a loan on the home, Without a mortgage you will not be able to sell it, A common request for the underwriter is for the appraiser to provide at least one comparable sale with the same feature.
Ask the professionals if they know of any homes with a wood basement floor. If the answer is no then think about how potential buyers would react. Personally I would walk out of the house and not make an offer, Ask the RE agent how hard it would be to sell, Ask the appraiser how hard it would be to appraise,
Appraiser would be none-the-wiser. Now a home inspector hired by the buyer might bring it up, and there could be state laws regarding the disclosure of the work to the buyers. Unfortunately the majority of sellers choose to roll the dice and not disclose such things. After all there are thousands of homes in the US which have had non-permitted (ie, no permit obtained) work done on the them which in many cases were not done to code.
I know the experts will correct me if I'm wrong, -I'm a DIYer and not a building scientist. I don't think the pressure treated lumber, under the plywood or other floor is a problem, unless tests have shown chemicals are emitted through the air. Pressure treated is quite expensive, and I wonder if you actually need it. I don't think you are planning for the wood to be in actual ground contact, just near it, but above layers that will be excluding most moisture. It sounds like you will be using concrete piers for support of the wood. Make sure something non-permeable is between the wood and concrete since the concrete wicks moisture to the wood.
It might be good advice to check with an appraiser, as suggested, but I have a problem with doing all things with selling in mind and for some institutions interests (i.e. banks) more than your own.
I don't agree at all that a PT wood foundation or cellar is more expensive than concrete. That is just plain silly. And insulation, air and vapor sealing of PT foundations is much more efficient than it is for concrete.
And it is irresponsible to recommend a lesser grade of PT lumber than .40 PCF for any construction that is in continuous contact with moisture or ground . It is special order materials, not on the shelves of your local hardware store. If it is marine construction, the standard is even higher.
The resale and mortgage issues are a different and valid concern. PT lumber has a bad rap but the basements are fully code compliant if they follow the engineering and materials standards.
While there is an ignorance of PT lumber, timber and sheeting material applications and building methods in the residential sector, PT lumber is used widely in water and ground contact commercial, industrial and heavy duty building settings.
hi FP
in this case it is not the foundation but the flooring slab we are speaking of the foundation walls are/will be of concrete, adding insulation and hydrocourt water barrier on the outside...
It is a good point about the public acceptance of this and that is why i was wondering if anyone had long term knowledge of the efficacy...
it just doesn't make sense to me that wood would rot over vapor barrier but not over a standard concrete slab...
rob
I don't think Rob is talking about wood being "in contact" with ground. As far as the expense, as a DIYer the issue is not always the cost of the material, but the fact that you can do it yourself vs not. Some projects are unlikely as a diy project (although I did pour my slab, years after original structure was in place, myself). One could spend more on materials and still have the project be less expensive by doing it oneself.
You mention being in Wa, in your first post. I don't have any experience building a floor the way that you have described, but I would definitely check with the building inspector for your area. From how I understand your description, accurate or not I think an inspector would want to call that a crawl space, and require your framing to be 18" (not 100% on the height) above the grade. Just a gut feeling from working with the inspectors in the greater Seattle area.
thanks all for the feedback...haven't decided...maybe talk to the code guys...
if anyone has tried this pls get hold of me
rob
PolyCore Canada makes a floor system similar to what you've described, except they use galvanized sheet-steel sleepers instead of pressure-treated wood. I suspect PT wood would work okay too.
http://www.polycorecanada.com/products/residential-foundation-floors
The use of concrete is mainly because it can handle bulk water, and water vapor issues, IMHO. As long as those are 100% taken care of I see no reason wood won't work. My dad used to have a house in Florida (that my great grandfather built) that had a wood foundation. Parts of that foundation were still there when he sold the place. It lasted 90 some years only because that soil was extremely well drained. The parts that had to be replaced were due to adding plumbing to the house and having it subsequently leak.
Sto-cote businesses makes a cross connected water obstruction however like all water boundaries, a lot of consideration and delicate taking care of is expected to avert punctures. Polyurethane caulks will work fine and dandy for crease and joint fixing; when the wood dries.
https://protoolsadviser.com/ buyer's guide
I did a lot of research into permanent wood foundations. I never understood the resistance by GBA principles considering the considerable embodied energy of concrete. Anyway, the key to any PWF is drainage. This means 4" crushed stone. Somewhere there should be a sump crock. this is usually a 2' cube pressure treated open bottom plywood box surrounded by 4" of rock including the bottom. 6 mill poly is laid over the rock. Rigid insulation, if desired, goes under the poly. The poly seams are modestly overlapped but not taped or otherwise sealed. Water on top must be able to drain. Now the wood. It must be CCA treated. Just look for wood rated for PWFs. Around these parts it is available from Menards. Lay 2X4 sleepers on the flat 4' OC. Next go the 2X4 floor joists followed by PT plywood. Above this, untreated wood is acceptable.
A couple years ago I tore out a rotted wood floor over dirt without any concrete in Seattle. There was some shredded plastic that was an attempt at a moisture barrier but my guess is the bugs and or rats got to it. Once that was gone the moisture made quick work of rotting the floor, and the room wasn't too comfortable either.
I understand the reluctance for concrete, but you might want to consider at least a "rat slab" (a thinner and typically lesser finished quality layer of concrete meant to stop bugs and rodents) as part of your assembly.
Building a wood floor over dirt can involve several challenges not found when constructing a wood floor over traditional constructed surfaces, such as concrete, sand or gravel. Soil shifts and is affected easily by environmental conditions outside the floor area. Because of this, the dirt floor requires additional preparation not necessary with other floor types. These preparations create issues of their own, forcing you to build a floor on unanchored floor joists. Once completed though, the combination of joists and floorboards holds together the whole in a stable level floor suitable for further covering in anything from carpeting to floor tiles.
An older discussion which talks about how Michael Maines and Steve Baszek do basements with no slabs: https://www.greenbuildingadvisor.com/question/can-the-concrete-slab-be-eliminated-in-a-super-insulated-slab
Two links from GBA apply:
https://www.greenbuildingadvisor.com/article/the-concrete-free-floating-plywood-slab-assembly
https://www.greenbuildingadvisor.com/article/concrete-free-slab-foundation-to-wall-connection
Cheers!
There's this article from the Journal of Light Construction with Steve Baczek that discusses how to do it.
https://www.jlconline.com/how-to/foundations/a-basement-floor-without-concrete_o
You can create a free account to read their prime articles.