Low-slope metal roof over car decking and rigid polyiso

Remodel of early 60’s modern house on Puget Sound. Shed-style roof with 1.5 in 12 pitch. Private drive is elevated above house so roof is visible as you approach it. House is L-shaped with attached garage. Garage and L wing roofs are oriented for solar exposure with a substantial PV installation (Solar World 235) on both. Panels will be angled to 30° using either off-the-shelf Unirac components or custom aluminum racks that we plan on attaching with S-5 clips. Central portion of roof is low on the east and slopes up towards the west, where we get the most weather. There is one valley and (3) 2′ x 4′ skylights.
Much of the roof will be 2×6 T&G car decking over beams. We plan on having no insulation on the living space side so the T&G and beams are visible. On top is where we need help in creating the best (hopefully simple and straightforward) insulated roof system.
Because of the visibility of the roof and the PV arrays, I’d really like to stay with a standing seam metal roof. AEP Span has a number of styles rated for low-slope roofs. The current recommendations from a roof consultant has an entire Sarnifi roof placed over a ribbed deck (to create a drainage plane) with the metal roof on top. I can’t stand by quietly while my money and sanity are pushed to the limits. From what I’ve read in Fine Homebuilding and GBA, it seems we can build up a roof with closed-cell or foil-faced polyiso without any air space and achieve a sound envelope. I’d like some recommendations on what the makeup of this roof should be. I’m looking for an insulation (as opposed to total roof material) R-value between 30 and 40.
GBA Detail Library
A collection of one thousand construction details organized by climate and house part
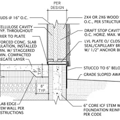
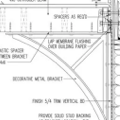
Replies
Greg,
There are two issues here:
1. Coming up with an adequate insulation layer, and
2. Making sure that your standing-seam roof is watertight (in light of the roof's very low slope).
Issue #1 is trivial. Choose your foam product and install it thick enough. On top of your T&G boards, you can either install multiple layers of rigid foam, nailbase (or a combination of rigid foam and nailbase), or SIPs. Your choice.
Your roofer probably wants a layer of continuous sheathing under the standing seam roof, so you need to install OSB or plywood on top of the foam if you are insulating with mutliple layers of rigid foam. If you are installing nailbase or SIPs, you end up with OSB on top.
I would leave it to the roofer to determine the details of the roofing installation, for two reasons:
1. The roofer provides the warranty.
2. Your roof has a very low slope, so steep-slope details may not work.
If you don't like the details suggested by your roofer, call up two or three more roofers to get other bids.
Thanks Martin. I agree. Respected roofers aren't going to put their warranty and reputation at stake. Do you know where I might find a section view of something similar with an explanation of the layers and how condensation is prevented or taken care of? My builder had an experience 30 years ago with a furred out deck, fiberglass batting, and a metal roof. It was traumatic enough that he's under the firm impression that no roof, no matter what type, is built without a drainage plain and/or air gap. Right now the design has both. I met with a metal roof installer yesterday and he couldn't believe what the roof consultant had come up with, saying the word "crazy" a dozen times. He didn't score points with my builder. It could be that I have to be the one to talk him down so any ammunition I can bring to the table is appreciated.
Greg,
Something to bear in mind here is that your roof assembly is much less risky than the nightmare scenario this consultant cited, because even in the event of leakage you may get water in the foam insulation (nothing to worry about really) or possibly water reaching the wood decking which can readily dry to the room below. You will see the evidence of any such wetting and the worst case scenario is not a catastrophe.
The metal plus membrane plus metal scheme does seem excessive, not sensible. Here's a less nutty way to allow venting below the metal: use a profile that does not require continuous plywood backup and install over cross-hatched 1x4 furring. Run the first course with the slope (allowing drainage across the surface of the foam) and the second course perpendicular (spaced as needed for the roof profile).
Thomas, could you expand more on the layers you would recommend, starting with the top surface of the decking? The metal roof company representative suggested the following:
1) Decking (existing)
2) 30 lb felt as a vapor retarder
3) 5" Polyiso rigid in 2 layers, staggered joints
4) 1/2" CDX with long screws tying into decking
5) Watershield membrane
6) Roof clips with AEP Span Klip-Rib 24 gauge roofing
Again, this is a 1.5 in 12 pitch with 3 skylights and a valley. Will this be substantial enough to anchor the PV racks with S-5 clips and can we reasonably expect water/moisture to not be a problem with a metal roof on this low of a pitch?
Greg,
Your code minimum for the vaulted roof is probably R-38, so make that 6" polyiso. That type of roofing does not require a plywood backup so you could substitute the two courses of 1x4 furring as described before. There would be some risk in sealing plywood between impermeable foam insulation and a waterproof membrane, because any leakage (or initial wetness) would be trapped permanently.
Also, I'm not sure there's any point to the 30 lb felt below the polyiso. In many cases it makes sense to install plywood over T&G decking to improve shear strength and air tightness.
Your question about PV mounting hardware would be best directed to the PV supplier or installer, because it depends on the specifics of the clip and the roof profile (hard to guess whether they are compatible). At a glance I would think the S-5 clip is not compatible because it's designed for a standing seam profile, which is a narrow and dense roll of metal rather than the hollow seam of the "Klip-Rib" profile.
Thomas,
The roofer did say S-5 had a clip for Klip-Rib and he was right.
http://www.s-5.com/clamps/index_913.cfm
I also have a concern about a hollow profile being clamped, compressing slightly over time, and loosening up. I have a sample of the 24 gauge Klip-Rib and it's pretty stout. This combination might work okay.
I believe our structural engineer does recommend 1/2" plywood sheathing over the decking for shear strength. I'm assuming all butt joints would be either sealed with caulking or tape? Vapor barrier next? We're trying for R-38 and with 5" Polyiso plus sheathing plus decking and air-sealed, I think we're okay. The building dept. told us they won't hold us to the latest code requirements if we're insulating over an existing deck. I think we're going to be there anyway and may go with 6" per your recommendation. With polyiso in place with taped and staggered seams, I'd like to know how best to complete this "stack". As with previous posts I've read here, it seems I'm building SIPs on site.
- Decking
- 1/2" Sheathing
- Vapor retarder or vapor barrier?
- 5" to 6" Polyiso rigid foam.
- ?
- 1/2" or 5/8" Sheathing?
- Water/Ice shield membrane?
- Clips and roofing?
I can't quite seem to get the "experts" to fully diagram this out, especially when I mention the PV arrays and accommodating the loads. Colder, wetter weather is just around the corner and I need to get a roof over my head for the winter interior work.
Greg,
Now that you mention it, the "Klip" in Klip-Rib appears to refer to those S-5-K clips and they were designed to work together. That's a good sign.
FYI, 5" thick polyiso would get you to R-32. 6" would be almost R-39. A vapor barrier under the foam wouldn't do much because the foam itself is not permeable, or at least not including the facing on the panels. You could get good airtightness from the sheathing layer (directly over the decking) by taping the joints with 3M 8067 flashing tape, or something similar. The same tape would also work for the foam boards. With foil faced polyiso and taped joints, the surface below the roof could already shed water from any minor leak or from condensation. Adding a membrane like ice & water shield wouldn't hurt but you could skip it.
I don't think there's a structural need for a layer of plywood above the insulation. Think of it this way: if there were 1x4 furring at 24" on center, that would mean a surface area 3.5" wide over the foam every other foot, or approximately 21 square inches per square foot of roof. You can bear easily 15 PSI on the foam, so call that 300 PSF that could be supported through the furring into the foam. That's well beyond what the beams could support, and the PV setup won't weigh much per square foot anyway.
With any luck someone with more specific knowledge about PV attachment (or metal roofs) may chime in here.
If they are rating the metal down to 1.5, then ok, but the big problem is going to be roof penetrations. I would make those skylights curb mount. Use ice and water around and down hill from all penetrations. specify very carefully flashing for plumbing and all other penetrations. Be onsite when they do it to make sure it is done per the drawings
Personally would try to fall in love with the look of white EPDM or PVC, you have a very close to flat roof. With all that PV, who will be looking at the roof surface?