Proper materials for moisture control with a SIP roof

Hi,
I’m building a house north of Stowe VT using SIP over timber frame construction with R-40 walls, and R-48 to R-53 roof SIPs (different thickness are being used in order to make the ridge line heights match on roof areas with differing pitches).
There seems to be some confusion among my contractor, the SIP installers and myself about what to use for 2 parts of the roof system:
1) material to use over the top of the T&G ceiling boards and under the roof SIPs
2) material to use over the top of the roof SIPs and under the standing seam metal roof
Issues involved include moisture migration from inside to outside and water proofing from outside to inside.
Material options suggested so far are either felt paper, RoofTopGuard for #1 and those plus Ice & Water Shield for #2.
Is there any Energy Star requirement wrt these materials?
Any experiences folks might have heard from anyone having used these and/or any info about their relative merits and/or drawbacks?
thanks,
Jay
GBA Detail Library
A collection of one thousand construction details organized by climate and house part
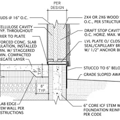
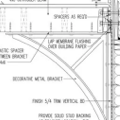
Replies
Jay,
I assume you are using conventional SIPs, with OSB facings on both sides.
The most important step is to get a good air barrier. I like redundant systems -- spray foam in the SIP seams, plus high quality interior tape at every seam.
Once that is done, you don't have to worry. As long as your finish carpenter doesn't mind fastening ceiling boards to OSB, you are all set.
I don't like to see roofs completely covered with Ice & Water Shield. Such a barrier prevents the OSB from drying out if it ever gets wet, and makes future repairs very difficult. For a top-notch roof, install #30 asphalt felt, followed by 1x4 nailers installed to meet the requirements of your roofing contractor.
Jay,
I'd like to suggest a specific assembly for a SIP roof in your climate. A SIP roof, while performing very well, is extremely sensitive to moisture in the panel seams. Air infiltration can is still a problem in this assembly when the steps that Martin outlined are followed correctly: "The most important step is to get a good air barrier. I like redundant systems -- spray foam in the SIP seams, plus high quality interior tape at every seam."
Further air infiltration problems can exist in three significant ways over the life of the building: 1, The SIP panel has an internal network of wire chase's that make air-sealing below 1.5 ACH a significant challenge to many builders. Interior vapor laden air can travel this network and reach the interior side of the exterior OSB skins of the roof panel. 2, Building movement over time can affect the interior joint "foaming" beyond what the spray foam will tolerate without "cracking" and opening up additional pathways for air movement inside the seam. 3, failure to establish and air-tight joint at the seam between SIP's and the foundation at both the interior and exterior, can result in interior or exterior air entering the chase network at the SIP base. Once vapor laden air reaches the inside of the exterior OSB in a heating climate like yours, it will condense and form liquid water.
The assembly that I'd like to suggest was formed by the product manager of the Swiss Company SIGA, Patrick Haacke and myself specifically for American SIPS. It rely's on two strategies:
1-A: The interior foaming and taping at every joint (including the base joint) exactly as Martin suggested. This really needs to be done well and with an eye to limit air penetration into both the panel joints, and the electrical outlets and therefore the network of internal chases. For the tape, we suggest SIGA Rissan 60 and 100 for a base joint.
1-B: Do the same on all of the panel joints, window & door cutouts on the exterior with SIGA Wigluv 60 & 100 (60 = 2.375" wide, 100 = 4" wide tape). More about Wigluv below… Then on with the house wrap…etc..
2, Do not use vapor closed material on the roof deck. Use materials that are water proof and have a high diffusion rating. Especially since you are talking about a standing seam metal roof. The OSB skin has a perm rating of 0.6 to 0.7 depending on the specific 1/2" product and manufacturer. This means that it does have the ability to "dry through" when the concentrations of vapor are higher inside than outside. The key to maintaining that ability is to not place anything above it that is vapor closed.
The roof assembly that I'd like to suggest is: Tape all seam joints directly onto the OSB with SIGA Wigluv 60 or 100. SIGA Wigluv has a perm rating of 1.2 US Perms, but is still airtight and waterproof. The next layer is SIGA Majcoat. It is a vapor open roof membrane with a perm rating of 34, but is completely air-tight and water proof. I suggest this over Martin's #30 asphalt felt due to the felts' having a low perm rating of 1.75. See: https://www.greenbuildingadvisor.com/community/forum/general-questions/14623/standard-30-asphalt-felt-vs-astm-30-asphalt-felt-astm-d-266. The key to the assembly is keeping the permeability increasing as you go up in layers: It will increase the OSB's ability to "dry out" any internal moisture.
From the Majcoat up it is battens and counter battens or sheeting to carry the metal roofing. The ticker the batten, the better the air movement and evaporation potential. if the roof pitch is on the low side, or you want to reduce the possibility of water penetration through the SIGA Majcoat (or felt), you can add SIGA nail sealing tape to the bottom of the battens and apply the batten with a course threaded screw to retain compression at the fastener penetration. if you need help with the SIGA products for this assembly, try http://www.smallplanetworkshop.com.
You've gotten some good advice re: your question. I would just add that with these tight SIP shells, water vapor management is crucial and I trust you or your builder is/has considered the necessity for Heat Recovery/Ventilation System.
To answer Jim's question yes we are planning an HRV. Leaning towards the FanTech 1505R at present. Seemed like a good unit and the intermittent and over ride controllers available for it seem like they will suit our needs. Still need to find an HVAC person in the Stowe VT area.
To Albert, there won't be any wire chases in any of the roof or wall panels. Half of the footprint is cathedral ceiling so the second floor only has 2 rooms and a balcony. I plan to put lighting in those rooms into either interior walls or in the bathroom possibly the false framed wall which will hide plumbing.
The SIP installer intends to put the T&G ceiling boards down on top of the frame before the roof SIPs go on since it's a lot cheaper, faster and easier to do it that way than to install them on the underside of the SIPs. Also it means the SIP doesn't get perforated.
So I'm confused about the suggestions to tape & foam the interior since I don't see how the interior seams can be accessed if the SIPs are going down over the T&G boards. I'm pretty sure that's why they recommended some type of material be placed over the T&G boards.
They will definitely be foaming the seams (and taping them too I believe) from the outside in a 3/8in gap they leave between panels for this purpose.
So if I understand correctly a good approach would be
A) use a material that is not vapor permeable over the T&G ceiling boards and under the roof SIPs to prevent moisture migration from inside the building to the underside of the roof SIPs
B) use a WRB that is vapor permeable on the top of the roof SIPs underneath the standing seam metal roof so that if somehow any moisture does get down to the roof SIPs it has the ability to permeate outward
BTW given the relatively high R values of the roof I was planning on going with an unvented roof. Any comments about the wisdom of that?
thanks,
Jay
Jay,
The installation approach you will be using will make it difficult to achieve an airtight shell, since you won't be able to tape the interior seams of your SIPs. Experience has shown that foaming the seams is insufficient to attain high levels of airtightness. Although taping the exterior seams is a good idea, you could still end up with interior air circulation through convective loops at your SIP seams; when this looping interior air contacts cold surfaces -- the exterior tape -- condensation and rot can occur.
In theory, you can try to establish an airtight layer by installing Tyvek on top of the board ceiling before the roof SIPs are installed. In practice, however, this will be difficult. The Tyvek will be slippery; it will require many nails to install properly, and each nail hole is a potential air leak; and the perimeter of the Tyvek will need to be connected to the air barrier of your walls -- flawlessly. That idea contains a lot of opportunities for failure.
Jay,
If you are looking for a heat-recovery ventilation contractor in Stowe, Vermont, you should contact:
David Hansen
Memphremagog Heat Exchangers
460 Sparrow Farm Road
East Montpelier, Vermont 05651
802-229-2722
He's been in the business for at least 26 years, and is the best HRV guy in the state.
Jay,
I get the complication of SIP assembly. It's difficult to reach the underside joints. It's more challenging on a Timber Frame. For my project, we assembled the panels into larger components on the ground and put the drywall onto the panels before placing onto the Timber Frame. I didn't understand how much I needed to pay attention to air-sealing the interior joints at the time but I hopefully did a good job.
Martin's comments are true. Placing the T&G onto the frame, while expedient, will not make for good joint sealing. I don't know how big your roof assemblies are, or even if you've got girts running between bays at the wall to roof joint, thereby eliminating access to those as well.
It's hard to imagine a specific plan without knowing what the project looks like. However, here are the comments I can offer:
1, You do understand the theory. Air-sealing the underside at the joints is critical. I can't stress that enough. Failure to do so will lead to a panel replacement eventually. We just recently had the Timber Framers Guild Western Conference out here (WA State) in April and one session was a "searching" discussion with SIPA (SIP Trade Association) about joint failures in the roof. The consensus remains that the entire roof panel needs to be replaced. It's not a simple matter of just replacing the OSB skin.
2, If you choose to place sheet material over the T&G, Consider two things: 1, Don't use a Tyvek like material that is typically used on the exterior. In my opinion, the permeability is too high. My suggestion remains at keeping the interior line at a very low permeability. In the range of 0.5 to 1 perms. For this, I like SIGA Majpell (.68 perms). Do not use PE sheeting. While the permeability needs to be low, there does need to be some permeability. A product like Membrain (http://www.certainteed.com/products/insulation/mold-prevention/317391) will work if your extremely careful and a bit lucky. It's not very "robust" like the SIGA Majpell and could tear fairly easily.
3, Don't nail or staple the membrane to the T&G. Do use SIGA Twinet. This may seem a little out of left field… SIGA Twinet is a really aggressive double stick tape. It's made for placing interior membranes on wall framing without fasteners in order to eliminate membrane penetrations. It works really well. Create a pattern of Twinet around all of the edges and then in the field at 24" to 36" OC of your roof T&G. Leave the backing paper on the "upside" as you do this. Lay out the SIGA Majpell onto the deck to cover the whole area. Tape all Majpell joints with SIGA Sicrall 60. Let the membrane overhang all of the edges of the roof so that it can be connected by tape (SIGA Rissan 60) down well past, the wall-to-roof-joint, down the wall. Start at one end, and lift the Majpell enough to pull the "upside" release paper and stick the Majpell onto the roof T&G. In this way perhaps you can get past your TF frame ridge (if you have one), purlins and bay girts and bring the air barrier well down the walls. I'm only guessing that the T&G can support (or can be supported) while this work is going on. I really like the SIGA Majpell for this application. It's the "toughest" low perm vapor control that I know of off hand. It should resist the abrasions that are bound to occur in this assembly plan.
4, You said: "B) use a WRB that is vapor permeable on the top of the roof SIPs underneath the standing seam metal roof so that if somehow any moisture does get down to the roof SIPs it has the ability to permeate outward BTW given the relatively high R values of the roof I was planning on going with an unvented roof. Any comments about the wisdom of that?"
Jay, I'm not a roofing expert so please take my comments from the standpoint of moisture and SIPS… Since the exterior OSB is the most sensitive layer in the assembly, and what all of the other steps are done to ensure long term protection, then to me a vented roof is very important. 1, Air movement above the OSB and WRB is what is needed to take any "dry through" vapor out of the assembly. 2, A vented roof, especially with steel, adds a layer of protection from liquid water intrusion and condensation on the underside of the steel. The extra layer really is really more important in 10+ years than the first few. Adding that layer of air will help in buffering the temperature and moisture swings and will enhance the longevity of the exterior OSB skin (in my opinion). I'm a big fan of ventilated rainscreens for both wall and warm roof.
Btw… It's interesting and probably controversial to note that European rainscreens on the wall or roof begin at 1" thick. Not .375" or .75", but the standard is 1" or more. This is from a recent trip to the Passive House (or Passivhaus) conference in Austria. The sources were both builders and material suppliers, who state that the 25mm (1") standard is now well past 15 years old and were based on air movement and saturation rate capacities of the air within the rainscreen.
Jay, if you're a Dad… Happy Fathers Day. The one day a year we get somethin'… :)
Jay,
I added a picture of an attic retro-fit we just did in a new development with some really forward thinking production builders seeking better blower door numbers. Removed and replaced the Lamtec barrier with SIGA Majpell. The reason I posted the pic is that the Majpell is held on to the framing by the SIGA Twinet double stick tape. The adhesive is surprisingly thick and has a high tack. For your application it would hold a membrane in place onto of the frame. The yellow tape is the Sicrall for membrane joints.
To Martin. Thanks for the HRV recommendation. The contractor we're going with also lives on Sparrow Farm Rd and he said he had a neighbor who did HRV work but he didn't have his phone # handy and said he would just ask him to call me. That was only a day or two ago. I'm guessing that Dave Hansen is probably that neighbor.
To all participating...
I don't know if it makes any difference wrt the subject of this discussion, but we are going to use the StoGuard liquid applied membranes on the walls. So it had just occurred to me to do what Albert suggested which is to wrap the membrane that goes over the T&G boards over the top edge of the wall SIPs then adhere it down to the top of the wall SIPs. That would have to get done after the gap between the wall SIPs and the T&& boards has been foam sealed. By doing it this way, when the liquid applied WRB goes over the membrane's edge at the top of the SIP walls it would hopefully create an airtight seal at the point where the walls meet the ceiling T&G.
WRT roof venting, I had thought that the reason for using a vented roof was to reduce or eliminate ice build up due to thawing & freezing resulting from heat loss through the roof. Given the higher levels of insulation we will have on the roof it had initially seemed to me that this wouldn't be a consideration for us so I thought an unvented roof would be a little simpler to construct. However it's now sounding like a vented roof is a better approach to allow for any moisture which might permeate the roof SIPs to be able to escape then I'm willing to rethink the decision to use an unvented roof.
Albert's suggestions about attaching the membrane to top of the T&G boards with tape or adhesive rather than staples or nails had also just occurred to me. I was thinking of using RoofTopGuard for this location, which unlike Tyvek does have a slip resistant upper surface. Not sure if it's possible to apply that with tape or an adhesive. I'll also look into the MajPell though.
Martin raised the issue of what to do about moisture possibly migrating in through the soffits, eaves & gables and condensing on the underside of the tape. I'm amenable to using something more permeable on the top of the roof SIPs like the Majcoat suggested by Albert as that would hopefully address this problem. It does sound like using Majcoat would work best with a vented roof instead of an unvented one so I'll have to change the plan wrt that.
One other thing I'm considering doing is using Grace Ice & Water Shield around the areas where the dormer walls meet the pitched roof and any other spots between vertical & "horizontal" surfaces. I might also use it the first few feet in on the dormer roofs. If I understand correctly this stuff is not permeable but it has a self healing membrane so it seals arouud fasteners and is therefore well suited for areas where there is a possibility of ice & water buildup. The lack of permeability and the fact that it is a bit more expensive would seem to not make it well suited for the entire roof however.
To summarize would the following potentially work?
- use RoofTopGuard, MajPell or something similar over the T&G and adhere it to the boards with tape or an adhesive making sure to seal the seams. In addition after the gap between the wall SIPs & T&G boards has been foamed wrap the chosen material over the top of the SIP walls and adhere it down along the edges then when the StoCorp liquid applied WRB (Emerald Coat in our case) is applied to the walls make sure to seal the edges of this material where they attach to the top of the walls.
- foam & tape the seams of the roof SIPs from above as best as possibly can be acheived
- use a permeable barrier like Majcoat on top of the roof SIPs so that any moisture which might get in can permeate upwards through it
- use a vented standing seam metal roof over the top of the whole thing
Boy does this stuff get really tricky....
I started installing SIPs over timber frame in 1988 in Wisconsin. For many years we simply sealed the double OSB splined joints well, from above, with expanding foam. We rarely encountered issues with this installation technique, but on a few occasions we saw, in time, "shingle ridging": composite shingles ridging up over panel joints in cold weather. Investigation found frost on the under-side of the shingles directly above SIP joints, indicating moisture moving through what appeared to be a well sealed joint.
In the late '90's, the SIP manufacturer I worked with, Insulspan, developed a method for sealing joints on the inside surface using seal tape: strips of peel-and-stick membrane. This certainly added a level of complexity to the installation, but it seems to make for a better and more durable job. Seal tape comes in a variety of widths, used in different locations. The trickiest locations are over timbers. Seal tape is draped over the timber, paper side up; the SIP is installed; the paper is then peeled back and adhered to the SIP skin from below.
You indicate the use of T&G ceiling boards. These are usually 3/4" thick. We prepare for them by nailing 7/8" thick strips of firring on top of the timbers before the SIPs are installed. (seal tape goes on top of the firring). This acts as a spacer, shimming the SIP up off the timbers, so that T&G can be installed later from below. 2 layers of 7/16" ply, ripped to 2" narrower than the timber width (creating space for the T&G to lap over the top of the timber) works well.
Seal tape seems to have cured shingle ridging, but many feel SIP roof decks should still be vented. Certainly with metal roofing I agree: metal tends to cause condensation to occur below it more readily than other roofing materials. There are many ways to accomplish this. Felt and strapping are perhaps the most common. Some municipalities require cross strapping (vertical then horizontal) so that any water that makes its way through the metal can drain to the eve unimpeded. Mat products are emerging, such as R-vent, and these appear to work also. They have the added advantage of keeping the roof profile a bit thinner in appearance.
Chris Koehn
TimberGuides Design & Build
Chris,
Good advice.
Chris,
Do you know what manufacturer or product Insulspan is supplying. The Wide joint tape supplied out here in the Northwest, just falls down after a coupe of days. Hence it hasn't been successful at sealing.
Jay,
The sequencing looks good. Be sure to tape the deck below the Majcoat.
The undersized spacers have always worked well on frames for adding the interior finish layers after the SIPS are down. Even though it takes longer than strapping the entire length, it gives you access to the underside much longer.
Hi,
Based on Chris and Albert's replies I will discuss the approach of standing off the SIPs over the rafters so they can be taped underneath and then sealed from below with the contractors involved. I expect they'll push back since it would be more work but I could always do the T&G board installation on my own at a later date along the lines Chris suggested.
I am definitely looking into the MajPell & Majcoat materials.
I also sent an email to the maker of the R-Vent mat (Advanced Finishing) to see about pricing and purchase info. The thickness of the SIPs we're using for the roof (11-1/4 foam core on the pitched parts and 13-3/8 foam core on the dormers) is pretty thick so the R-Vent seems like a good option for the material to achieve the stand off for the roof vent since it would add less to that. Also, since I'm a little concerned that if not correctly installed using strapping for the standoff could trap water so the R-Vent seems suited to address that since it appears to let air circulate through and water to drain out.
Thanks to everyone for the info and suggestions.
Jay
I have a novel idea:
Skip the SIP walls and roof.
Why the hell do people use these? They are super expensive and far from green. I'm so tired of these topics popping up on GREEN building websites. You all know they are pumped chuck-full of petrochemical foams right?
Use a double wall and frame the cathedral ceilings with raised-heel scissor trusses... Airtight Drywall Approach for your air barrier.
I guarantee this will be a cheaper and certainly much greener strategy.
I personally don't feel Mr Hersh deserves that level of negativity. He has spent many months asking articulate questions and working much harder to make his new house energy efficient than 99 percent of the populace would. That his plan does not meet your level of 'greenness' is unfortunate.
Look, you have a good point, if you spent the time to produce an eloquent defense of your design proposal, it would be much more likely to actually affect his decision making than just spouting off.
Obviously many disagree with your opinion on foam.
I don't believe a green purity test is useful.
I don't think my comments were harsh.
It's frustrating to see people get hung up on the darlings of the green building industry, and then have other professionals encourage this behavior.
In 14 responses to the OP's question, no one said anything along the lines of "hey SIPS are expensive-- have you ever considered...."
Nope, just "yeah, SIPS are a pain to air seal...."
Lets put the "greeness" of SIPS aside. Has anyone ever done the cost analysis of R-40, R-53 SIP panels vs other wall and roof assemblies?? Uh, yeah I can confidently say that there are more cost effective ways to achieve these R-vaules.
And look, you don't need to do this analysis with a complicated Excel spreadsheet. It's an obvious conclusion. R-40 SIPs are ridiculously expensive, let alone R-53 panels?!
So again, why do people continue to use SIPs when there are cheaper and greener (sorry this is not up for debate) strategies out there?
Brett,
Perhaps you should understand the evolution of the project. We initially sought to build a log cabin home because we liked the look until we realized that they might not be that energy efficient especially for a vacation home which we wouldn't be living in all the time (i.e. the thermal mass of log cabin walls would work against us since we wouldn't be there to constantly keep the place heated).
So we chose to go with a post & beam design instead because it has similar aesthetics to the log cabin looks. In addition we've thought through a lot of things and are choosing our materials so that we'll be building an energy efficient home finished in a way that gives it a very rustic cabin look (though not "log" cabin) inside & out.
In addition, the house has been designed and sited to take as much advantage of passive solar heating as is possible and I've been careful in choosing and locating windows, thermal mass, etc. in the design to try to maximize this.
I have done some reading up on various approaches (one very good article called "Six Proven Ways to Build Energy-Smart Walls" by Bruce Coldham that I got on the finehomebuilding.com web page) talked about many ways to do this, including the double wall approach.
After considering various options the double wall approach seemed to be pretty labor intensive. A 3 man crew costs around $110/hr where I'm building and my impression was that, aesthetics aside, when all was said and done the framing costs would add up and the cost of the SIP approach wasn't as much of a premium as it might initially seem.
I do plan to do a very large portion of the interior finish work myself. Right now I'm still on track to get the whole thing built for $105/sf finished cost with the weather tight shell amounting to about $83/sf of that.
We've registered with the Efficiency VT program and their consultant who is working with us thinks we're on track to meet the Energy Star v3 standard which is what will be in force by the time we complete construction.
All dogma aside I think our approach is reasonably sound and as of today ground breaking is due to start any day now (it would have already been underway if it hadn't been raining so much recently) and we're at the point where we're working out final details and are not in a position to scrap the whole design and start over.
I am curious though about real world feedback on the number of man hours constructing a double walled raised scissor heel truss structure such as you suggest would require so if you have any please post it.
BTW If anyone is curious as to approximately what the home will look like there are some renderings at http://www.doctorbeer.com/VT/ they're not exact though. We plan to use wavy edge siding and there are a number of interior details (such as the stairs) where we'll be using a more rustic approach crafted out of lumber off our lot.
thanks again to all.
Brett,
Yes! a study has been done to compare cost between SIPs and conventional framing. The Cradle to Grave analysis was recently presented at the SIPA annual meeting. It can be found on the SIPA web site at http://www.sips.org/elements/uploads/fckeditor/file/SIPs%20Life%20Cycle%20Analysis%20brochure%20(EPSMA).pdf
The study identified higher initial cost and embedded energy to build with SIPs. It also shows the return on investment to be relatively short and dependent on the region you build.
A higher performing system (like SIPs or double wall construction) almost always starts with a higher price. However, just as you frame a double wall for lower overall cost, many elect to use SIPs for the same reason.
I'll let the salesmen of the building industry debate the use of the term "green". Meanwhile, I'll continue to use and promote SIPs as a way to quickly erect a durable and energy efficient structure.
Getting back to the topic I originally posted on this I put together a CAD drawing showing what I'm planning to do for the roof and have attached it.
I think the only remaining issues right now were raised by the contractor who is supposed to be installing the boards, membrane and roof SIPs. If I understood him correctly he indicated that typically the way they install the roof SIPs is to put down a plumb line across the roof, then nail a 2x4 or similar board along it and use this as a bunk in order to position the SIPs properly and make sure they leave the correct gap between them to do the foam sealing. They work from bottom to top and apparently using a bunk in this manner helps them keep things lined up because leaving the gap means they can't just butt the SIPs against each other.
This raised 2 issues.
1) the contractor was worried about his crew needing to walk on the membrane going over the ceiling boards. This was both because some membranes (like Tyvek) are don't have good gripping surface and that the use of double sided tape to secure the membrane would leave it susceptible to sliding if there was weight on it. He prefers to use staples.
2) nailing down the bunks puts holes in the membrane.
My thoughts are that if I use RoofTopGuard as the membrane over the top of the ceiling boards this addresses the issue of the membrane not having grip because in addition to having the low permeability I'm looking for at this layer it has a friction coat on the underside and a grip coat on the top.
In order to deal with the holes created by the stapling and nailing, and to seal the seams on the RoofTopGuard, I was thinking that if the staples and holes are kept inline then it wouldn't be too much work to cover them over with the same kind of sealing tape that would get used on the seams, like Siga Wigluv for example.
Does this seem like a practical solution to address the SIP contractor's concerns while still making sure that the membrane going over the ceiling boards gets properly sealed?
thanks,
Jay
not to stir the pot but one of my contractors (not the one that is currently supposed to do the ceiling board, roof membrane, and SIP install) sent me this link
http://www.buildingscience.com/doctypes/enclosures-that-work/etw-high-r-value-enclosure-assemblie
in which they use a numerical rating system to rate 12 different wall construction techniques, SIP and double stud among them. I don't know their methodology or if this group has any vested interest in one approach or the other so take it for what it's worth but it seemed apropos to the off topic discussion that crept in to this thread.
Jay,
Now that we're back on topic, I'll offer this thought. The use of SIP joint tape should be viewed as a belt & suspenders approach to air sealing. If the joint is perfectly sealed internally, no air moves and the tape becomes unnecessary. The introduction of tape by several (Not All) SIP manufacturers was to address the issues resulting from untrained installers. It is noteworthy to point out that thousands of SIP structures were completed pre-tape and continue to perform without problems. My experience has shown that the type of joint is as important as the skill of the installer. If your design uses lumber in the panel joints, the inevitable drying, cracking, or checking can result in a potential path of air leakage. Hence, this joint should be sealed both internally and with tape on the "warm side". However, if your design allows the panels to do all the work structurally without embedded lumber, you have a joint that is relatively easy to seal. The injection of expanding foam will completely fill any void created by the joint. When 2-part foam is used properly, the seal is permanent, pliable, and has similar air-sealing properties as the field of the panel.
When we install SIPs over timber frames, the panel span usually allows for a surface spline joint that can be sealed by foam injection. If the ceiling calls for T&G to be applied, I have no problem with installing the SIPs after the T&G is in place. If I want to use a belt and suspenders approach, I attach an adhesive-backed foam sill-seal to the T&G deck where the panel joints fall. The SIP compresses the sill seal and provides another measure of air sealing without compromising the assemblies ability to dry in either direction.
If you'er looking to increase your structures durability in the New England area, your money is far better spent installing back-ventilation to your roofing than applying an air barrier between your T&G and panel.
If you want to achieve a level of air-tightness on par with the passive house standard, the tape that Albert sells is top notch. However, I would disagree with his statement about being difficult to get below 1.5@50.
It's done routinely and without any tape. If you do opt for the <1 range, you may want to look at tape although i've found most of the is used improve window seals and correcting voids left by mechanical trades.
Hi Albert,
What size panels are your comments in reference to?
I ask because we're going with a mix of 11-1/4" and 13-3/8" foam core (the different thickness are so that the roof on the shallow dormer slopes meets up properly with those on the 8/12 pitched portions) and the installer advised me that they won't be using splines on them and would not be able to foam all the way down to the bottom of the seams. I believe he did say they would tape the seams after foaming them. In addition the sub-fascia on the sides of the SIPs will be standard lumber. I don't know about if those get foamed but as you indicate the lumber will likely shrink or crack so I'm assuming they can't be sealed from the sides.
It sounds to me like you're saying the tape on the top of the SIP seams may not be necessary.
Still, at the very least their not sealing the full thickness of the SIP seam and there being no way to seal the sides of them means that moisture could potentially get into the SIPs from the sides over the top of whatever membrane ends up getting used on top of the ceiling boards. That's what Martin had pointed out and as a result I now plan to go with a more permeable membrane on the top of them and to use a roof vent.
The thing I'm trying to resolve now is what membrane to use over the ceiling boards (RoofTopGuard seems to be the leading contender) and, given that it will be comprised of multiple sheets, how best to get an air tight seal between the various sheets of it as well as between it and the top of the walls.
I just downloaded the RoofTopGuard install guide and they say not to use staples. The "other" contractor forwarded an article to me by John Nicol from the May 2006 issue of a journal called JLC in which he compares several materials. He also notes that staples aren't supposed to be used with RoofTopGuard.
I guess the real issue comes down to convincing the SIP installation contractor to not use staples to install it and to get him to use a compatible sealant (butyl rubber, urethane or EDPM based caulk or tape) to cover on any holes he makes in the course of the SIP installation. It's either than or find a contractor that is willing to do so...
thanks,
Jay
Al,
you know that SIPS/EPS moulders study is a load of balogna, right? the baseline house doesn't even meet code minimums for most jurisdictions... when you compare apples to oranges and are looking to make apple pie, the apples always look better.
Jay,
Since you decided to "stir the pot" .... I agree with Brett.
It sounds like it is too late for you to change horses.
But hopefully not for others.
If you spend enough time around GBA you will notice that Martin Holladay recommends the double stud wall with cellulose as first choice for Vermont and similar climates.
Mike,
How does a 2x6 @24"oc R-19 with osb sheeting not meet code? The folks at Franklin who did the independent study may take issue with your comments.
Why not start a new thread and I'll invite them over to defend there findings and maybe they could educate all of us on life cycle analysis.
A couple of responses:
Al Cobb: My statement about SIPS being hard to get below 1.5ACH 50 was really about the occasional SIP Builder. Not the builders who consistently build with SIPS. I agree with you comments about lumber & building movement. It can open up seams enough for air penetration. There are post construction issues that can contribute to this, hence the suggestion of adding "the belt" to "the suspenders." I am a big fan of taping the seams on SIPS, not because I'm in the tape business, but because I'm a big fan of Timber Frames (cut my first frame & joined the TFG in '98... which makes me still a "newbie"), they mostly get wrapped in SIPS, and it's really important to me that the projects stay healthy and the craft stays busy and lively. While you're probably the best SIP installer in the country... Most of the rest of us are not, and could really use "the suspender" to cover "the crack" ...pardon the pun.
Jay, I'm not sure of your question. There are two Al's here: Al Cobb and Albert Rooks. I think that Al Cobb is ok with no tape on the top of the SIP below the WRB. I'm suggesting the addition of a tape (new to all of us) that is air-tight, water proof but vapor permeable. We both are suggesting that the warm side gets air-sealed extremely well. Be it by just "the belt", or the addition of "suspenders" to the "belt". Choose your method: Tape, membrane, sill sealer w/ adhesive, whatever method will fit. The primary need is air-sealing at the joint. If it is local, in the joint area, than permeability isn't an issue. If a membrane spans the entire underside, then a low perm is better than a high perm, all of which is better than no perm.
Again, what the vapor permeable tape on the cold side has to offer, is the ability for vapor to "dry through" an air & liquid water tight joint should vapor build up in the joint. If vapor does accumulate in the joint for whatever reason, however many years later, the result will be the raised joint seams that Chris Keohn described above, or perhaps OSB degradation. My thought is that it's cheap insurance. :)
I'll leave the ethics of foam out of this post. Regardless of material preference, I think it's very important to the Green Building Industry that all super-insulated envelops succeed without failures. Their success will encourage more super-insulated envelops, and more work.
Energy isn't getting any cheaper or cleaner, there is a whole country to convince that conservation is practical, possible and reliable.
Al C.,
you might be right, i was looking at a different SIPs LCA study that referenced an EPSMA document where the US baseline was 2x4 w/ R-13, while Canada's baseline was 2x6 w/ R-19. it still doesn't state what the SIPs panel is in the summary of the franklin assoc. LCA study i've seen, which is really weird.
i'm interested in discussing further (as i've never seen the value of SIPs) so i'll start a new thread
On second look, Tremco Trio might not be the best, Trio seems to be for windows and doors (waterproof impregnated). Timber Max or Super might be better. We'll have to check with a rep to see what they say.
Timber Max: http://www.tremco-illbruck.co.uk/products/00861_index.html
Compriband Super: http://www.tremco-illbruck.co.uk/products/00858_index.html
since Jesse mentioned tapes RoofTopGuard says to use butyl, urethane or EDPM based caulk sealants or tape. Does anyone know which brands in particular might fit this requirement?
thanks,
Jay
Has anyone used Tremco's expanding foam tapes in these situations (SIP panels over timbers, no access to pull release tape from underside, etc).
Tremco Compribond Trio for example: http://www.tremco-illbruck.co.uk/products/03999_index.html
These tapes slowly expand, used commonly for window installation. Peel off one side, stick to the top side furring, you would have 30 minutes or so to drop down your SIP panels before full expansion. They have US distribution through http://www.tremcosealants.com/ but these tapes don't seem to be listed on their US website, even though their reps have them available.
jesse,
there were some prefab builders using the trio for module joint air sealing, but it's vapor diffuse, isn't it? good stuff (outside the vinyl).
Mike,
The white side of the Tremco Trio is the vapor retarder. Your retarded side (and that's not a slam) is intended as the interior side. From there it's diffusive open to the exterior (but air & liquid water proof).
It'll be in stock in http://www.smallplanetworkshopstore.com in a few weeks, but can be special ordered now.
that's right, which would be perpendicular to the "direction" or grain of the tape. i'll just keep the tremco to passivhaus windows and panelized wall joints
Here are details from Premier SIP for interior tape sealing their panels (which they describe as a required practice in cold climates):
http://www.premiersips.com/details/013%20(11-9-10).pdf
http://www.premiersips.com/product-resources/details/
http://www.premiersips.com/Tech%20Bulletins/TECH%20BULL%2028c%20vapor%20retarders%20with%20pbs%20residential%20Panels.pdf
Key to make it possible over a timber frame is very wide tape sheets (12" at wall / roof intersections, 18" @ ridge beams) to allow the tape to be stapled to the furring sticky side up like Chris K recommended , then set panels, and still have access to the tape sheets after the panels are dropped down and fixed in place. Having really wide tape seems to make this a plausible practice, it has never seemed practical with typical tape widths.
Here's another possibility for the membrane on your roof deck and below your steel:
http://www.cosella-dorken.com/bvf-ca-en/products/roof/underlayments_pitched/products/maxx_titan.php
It is a reflective, water-proof but breathable (high 28 perm) membrane. The reflective quality may reduce heat gains in the summer. It would work most ideally with a "cold roof" approach where the steel is on strapping, raised above the roof deck, allowing for a ventilation space. In sunny weather, heat reflected from the membrane would ventilate away and reduce any chance of conductive heating of the SIPs from the hot steel cladding. More importantly, in cold weather, any vapour sneaking through the SIPs' joints would have a chance to ventilate away.
It's always worth repeating that another benefit of having this raised steel roofing, with the ventilation space below, reduces any chance of the SIPs conducting heat to the steel under a snow-load, which could contribute to ice-damming, which is definitely a concern in the North-East.
Hi Mike,
we did change gears and go with the vented roof. Here's how we are implementing things (even as I type):
- T&G ceiling boards got installed directly over the rafters
- RoofTopGuard got installed on top of that and all the seams and nail holes taped. this serves as a vapor barrier to keep moisture migrating out of the house and up into the ~14in thick roof SIPs. It also serves as an air sealing membrane to help us try to achieve our 1.0ACH goal
- the ~14in overall thickness R-53 SIPs go on next and have the gaps between panels foamed. Since the ceiling boards were put on over the rafters the gap foaming can only be done from above and therefore almost certainly won't go to the bottom of the gaps. That's why the RoofTopGuard getting taped was important, so that there is no way for moisture to move up from the house that could condense in those gaps
- the SIPs get covered in GAF DeckArmor with WIP300 HT Ice & Water Shield used at the last 18in of eaves and for 18in above and below wall to roof transitions. The DeckArmor is highly permeable from the underside so if any moisture did get under it (through the fasteners for the battens that hold up the standing seam metal roof for example) it can move back up and out. Since that's already been purchased and by now laid down it's too late to consider any other products but the one you mentioned does look like it would have worked equally well.
- since the roof SIPs are so thick we're using diagonal battens for the metal roof to nail down onto. I still have to review with the roofer and my contractor as to whether we'll be using some type of sheathing on top of the battens and below the metal
That's it. This design should do a good job of keeping moisture from moving out of the building and up to the SIPs from below while also allowing any moisture that could ever possibly get in from above to evaporate back out. And at R-53 it should do so while really keeping the heat in our home..
thanks
Sounds cool.
Can you explain the battens on the diagonal?
Also, did you come across anything like the Ice & Water Shield but that might be vapor permeable or consider anything else for those edges and transitions?
Thanks and good luck!
the standing seam metal roof fasteners run in a line straight up from the eave to the ridge. my contractor tells me that because it's really tough to place running vertically up from the eave to the ridge so exactly that the metal roof can get fastened to that what they usually do is put vertical ones down and then put horizontal ones on top of them. this allows for air movement and drainage under the metal roof but creates nailing surfaces that are sure to be under the the roof seams.
the drawback to our doing this is that the overall thickness of the SIPs on the dormer roof is over 14 inches. So we were hoping to not have another 1.5 to 2 in air gap over that. Placing a single layer of diagonal battens makes it so that the battens always cross the roof seams but allows moisture to drain down and air to flow up without adding the extra thickness of a 2nd batten.
The short answer is that no I didn't come across anything like the Ice & Water Shield that is vapor permeable. I considered products from Grace, CertainTeed and Carlisle. My roofer had a strong preference for the Carlisle WIP300HT (high temp for use under standing seam metal roofs) so we went with that.
I'll defer to others on this forum but I didn't think it was necessary for the Ice & Water Shield to be permeable. It only gets used for 18in up from the eaves and 18 inches out from the wall and up along it. So while it's not permeable I would think that if any moisture got under it that it would be able to migrate around the edges to evaporate out.
Somewhere on this forum I found a link to a good article by John Nicol in a publication called JLC (don't know what it stands for) about synthetic roofing underlayments and lists 8 different ones.