Still not 100% clear

I have been studying high-r walls as well as air barriers and vapor retarders in an effort to design/specify a high-r wall that will perform well in CT (Zone 5). I have now spent many hours reading blogs and case studies etc. regarding these subject matters. I have some solid ideas and have learned a lot about high-r wall construction. Currently, I plan to specify 2×6 studs at 24”o.c. with fiberglass or cellulous insulation in the cavity. The horizontal cement board siding will be fastened through vertical furring then through the rigid insulation, and into the stud beyond creating a drainage plane or rain screen. The interior will be finished with an air tight gypsum approach (caulk etc.). However, due to some conflicting information and/or vague descriptions/details I still have a number of unanswered questions/concerns as follows:
1. Based on my readings, I have a concern about the shrinkage of rigid insulation and the longevity of the adhesive on tapes therefore, I am considerng useing Tyvek or some other wrap in addition to the exterior rigid insulation however, it is not clear to me where the Tyvek should be placed. Should it be on the inside or the outside of the rigid insulation? Again, Zone 5.
2. I am aware of a liquid applied product used under synth. Stucco(EIFS) that is supposedly a drainage plain, an air barrier, and vapor retarder all in one. I believe it comes in two different levels of permeability. I am curious to know why this product is not a more popular method in other non- synth stucco assemblies that use exterior rigid insulation such as the assembly I discribed above and why more people don’t consider using this under siding as it “seams” (pun intended) superior to wraps with tape.
3. I have read pros and cons regarding EPS, XPS, and PIC. Faced and un-faced. Unfortunately, I still don’t know what the best choice of rigid is for this application. Is there an ideal product/perm value for the rigid insulation in this application? Should it be faced or un-faced? (Thus far, I assume un-faced as there is a code requirement for an interior vapor “barrier” and I don’t want to create a double barrier however, some of the recent projects highlighted at building science.com are using two (2) layers of foil-faced rigid insulation (habitat in MA I think)???
4. I also understand the benifit of keeping the dew point outside of the structure but, how much r-value must be outside of the structure in order to achieve this in zone 5? I have read conflicting information on this matter.
5. The whole discussion of vapor barriers is somewhat frustrating as it seems that some of the leading experts at least partially disagree with each other. I understand the concept of drying to the inside and the outside. I understand the negative effects of a double vapor barrier. I am also aware of the code requirements for an interior vapor “barrier” in zone 5. IF… the exterior rigid insulation provides enough r-value to get the dew point out of the structure, should I go with NO interior vapor barrier (against code), a Class II (kraft paper), or a Class III (latex paint) on the interior?
I apologize if some of these questions have been answered previously however; I have been unable to find direct answers to these questions/concerns. Any direct answers that can be given would be greatly appreciated. Thank you.
GBA Detail Library
A collection of one thousand construction details organized by climate and house part
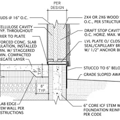
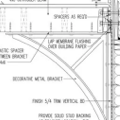
Replies
Cory,
Q. "It is not clear to me where the Tyvek should be placed. Should it be on the inside or the outside of the rigid insulation?"
A. Either location can work. But remember, if the Tyvek is your WRB, it has to be integrated with the window flashing and door flashing. I think that's easier if the Tyvek is on top of the foam than if it is underneath. But you can do it either way, as long as you think through your flashing details.
Q. "I am curious to know why this product [a liquid-applied WRB] is not a more popular method in other non-synthetic stucco assemblies that use exterior rigid insulation?"
A. Probably because the manufacturers of liquid-applied WRBs mostly market the products to commercial customers. Read more about liquid-applied WRBs here:
Housewrap in a Can: Liquid-Applied WRBs.
Q. "I still don’t know what the best choice of rigid is for this application."
A. Use any foam you want. Because of environmental concerns, more and more builders are gravitating away from XPS in favor of EPS or polyiso. Remember, the thicker your foam, the less permeance matters -- because for all intents and purposes, all foams become impermeable if they are thick enough. And remember, thick foam is always safer than thin foam -- because it reduces the
chance of wintertime condensation.
Q. "I also understand the benefit of keeping the dew point outside of the structure but, how much R-value must be outside of the structure in order to achieve this in zone 5?"
A. According to Table N1102.5.1 in the 2007 Supplement to the International Residential Code (IRC), rigid foam over a 2x6 wall in Climate Zone 5 needs a minimum R-value of R-7.5. For more information on Table N1102.5.1, see:
http://www.buildingscience.com/documents/information-sheets/irc-faqs/IRC-FAQ-insulating-sheathing-vapor-retarder-requirements/
Q. "IF... the exterior rigid insulation provides enough R-value to get the dew point out of the structure, should I go with NO interior vapor barrier (against code), a Class II (kraft paper), or a Class III (latex paint) on the interior?"
A. Latex paint (Class III) is perfectly acceptable in this application -- if your local code is up-to-date with the 2007 version of the IRC. Again, see the link provided to the question above.
Thank you Mr. Holliday. I vaule your time. I understand your answers however I have one follow up qustion if you don't mind. Mr. Riversong introduced me to the concept of a "vapor open" wall. What is your opinion regarding vapor assemblies?
I mean to say what are your thoughts regarding open vapor assemblies? Thank you.
Vapor open assemblies = good. If you're putting foam on the outside, don't put vapor barrier on the inside.
-Rob
Cory,
I assume you're a homeowner trying to figure out the best way to build. Unless you're building this home all by yourself, you'd be better off not trying to become "100% clear" about issues that few designers, builders and building scientists agree upon, and simply find yourself a designer or builder whose approach and knowledge you're comfortable with and trust them to make or guide you through these decisions. It is they who will guarantee the product, and it is only a highly experienced and knowledgeable professional who has the expertise to create something as complex and integrated as a modern home.
Cory,
There is no simple answer to your question, "What are your thoughts regarding vapor-open assemblies?"
In the past, building codes encouraged the overuse of interior polyethylene vapor barriers. When building scientists realized that interior polyethylene can do more harm than good in some climates, interior poly got a bad name.
Nevertheless, there are situations when interior vapor retarders still make a lot of sense (for example, in very cold climates or rooms containing swimming pools). There are other situations where exterior vapor retarders make a lot of sense (for example, to limit inward solar vapor drive behind reservoir claddings).
So it's impossible to come up with a simple rule on this question. Nothing beats studying the building science issues underlying your question. As Robert said, it's complicated.
Here's some more information:
Vapor Retarders and Vapor Barriers
Forget Vapor Diffusion — Stop the Air Leaks!
When Sunshine Drives Moisture Into Walls
Riversong,
You are somewhat correct in your assumption. I am a homeowner however; I am also an architectural designer and a student of green building. I have a BS in architectural/engineering, I worked for an architectural firm for almost 6 yrs. I now work as a consultant for housing authorities regarding modernization of public housing. I have long been interested in green building techniques and details however; my former employer (architect) did not share my enthusiasm. As far as I know, he is still specifying 2x6 at 16"oc with R-19 fiberglass and OSB sheathing. I have a decent amount of knowledge regarding the subject matter however, I am by no means an expert. Currently, I am attempting to gain more knowledge on the subject so that in the future I can also gain experience when I have the opportunity to design and build a "complex and integrated modern home". I disagree with you "leave it to the experts" approach as I myself would like to someday be considered an expert. I am doing a lot of reading/studying on my own however the questions that I posted above were questions that I wished to hear expert opinions on. I understand that there may not be a right or wrong answer in some cases. That being said, I thank you for your thought as you are far more experienced than I. DO you have a website of your own? Where can I see one of your typical wall sections? Thank you.
Holladay,
I agree it is complicated, there's no doubt about that. Thank you for the additional reading. Btw, I have been reading about the liquid applied WRBs and the PassivHaus that you suggested. Very good information, I am grateful for your suggestions. Thank you.
Cory,
If you're in the architectural design field, then you certainly should improve your knowledge base around these issues. The best place to start is with the fundamentals of hygro-thermal engineering. I had been teaching a course by that name, but am not currently. Without a sound knowledge of the physical principles behind moisture and heat flux, you will have no basis for judging the validity of any "expert" opinion.
I have no website, but some of my building sections are viewable at: http://www.flickr.com/photos/riversong-housewright/sets/72157624253116215/
And my approach and the last house I built is described and depicted at:
http://www.builditsolar.com/Projects/SolarHomes/LarsenTruss/LarsenTruss.htm
Riversong,
Agreed. I thank you for your assistance.
Corry,
I must say I am surprised that after all your research you would consider using a fiberglass batt insulation. It is 2010, not 1950. If you really want to take the next step and build high performance homes, I'd recommend eliminating kraft facings and batt insulation from the equation, exterior foam board or not. When long term performance losses and durability issues are taken into consideration, fiberglass batts don't look like such a bargain. Once you go cellulose you don't go back;)
Amen Skylar!
Not to mention embodied energy.......
Skylar,
Agreed. I am no longer considering fiberglass. I assume that you recommend latex paint rather than kraft paper?
Cory,
My vote would be for standard latex paint. What matters to me is air-tightness. I have seen cellulose and low density spray foams perform flawlessly in 9,000 HDD climates without traditional vapor retarders. The key is a quality installation. Stay away from polyethylene vapor barriers and focus on air-tightness. This will save some headaches.
I assume you mean "conventional vapor barriers". In a 9,000 DD climate with only open-cell foam and cellulose (such as flash & fill), you'd better have a code-minimum 1 perm vapor retarder, such as latex VR primer.
There is no reason not to use vapor retarder primer, which is often less expensive than conventional primers.