Vapour control layers, masonry and climate zones

Do feel free to comment or contribute to my assessment below. Criticisms and such as most welcome.
Vapour control layer (as opposed to the commonly employed ‘vapour barrier’ term) is a term which has found favour over here in northern Europe to describe the various membranes which seek to reduce the amount of vapour passing through to the cold side of insulation. That is, you install the VCL on the warm side of the insulation. There term VCL seems like a good term to me, because it also applies to roofs, where you don’t ventilate the cold side of the insulation, you really do need a good VCL.
Many of the roofing materials suppliers over here do supply things called ‘vapour barriers’ which are basically a thin sheet of lead metal, sandwiched between two layers of bituminous material, and which can be torched down, where you intend to have an indoor swimming pool below. A vapour barrier is a kind of product, where you need to protect reinforcement in concrete etc, from damage from vapour with indoor swimming pools in hotels etc.
We have a term also called ‘intelligent’ vapour control layers, which enable moisture in a structure to dry inwards into the interior of the building when the sun shining on the saturated outer brickwork suddenly pushes its way inwards into the building. I have read an article by Joseph Little at Construct Ireland magazine where he compared these new intelligent VCL’s against old fashioned type materials which were used. He found there were interesting things happening with the drying cycles of buildings, over a few years all the moisture from initial construction, was allowed to dry out, where the intelligent membranes had been used.
Joseph Lstiburek’s articles on this subject of course, are the ultimate reference in my view. Because he explains very simply the need for different positions of vapour control layers in southern climates such as Florida, versus Northern climate zones. He noted the fact that caravans are not manufactured specifically for the southern tropical climates, where the vapour control layer is doing a completely different job, to the one I described above in relation to Irish temperate oceanic climates.
We get un-believe-able condensation occuring within the structure here in Ireland. That is one of the main reasons why a one and a half inch ventilated cavity space behind an outer layer of four inch brickwork is still such a good technique from a water management point of view. But the trouble is, cavity wall construction has fallen out of favour somewhat lately in Ireland, because it struggles to meet with new thermal insulation requirements. Once you start to expand the size of the cavity beyond the standard four inches, suddenly all of your weathering cavity trays, steel lintels, door and window threshold details, and wall ties all start to behave differently. There are all sorts of knock on issues to deal with.
I would subscribe very much to Joseph Lstiburek’s point of view, that with masonry construction in certain climate zones, you are as well off to try and optimise roof, floor and glazing insulation first. Then do whatever you can with mechanical and electric efficiencies. Before you finally start to tackle the wall insulation, internally or externally – because of this big issue with water management and vapour control.
To develop on the ideas in Chris Briley and Phil Kaplan’s ‘Design Matters’ podcasting – the most energy efficient form of a building is probably a cube. You may elongate the cube as you move to more southern latitudes, to capture more passive solar gain on equator facing facades. I would also have a caveat to that, if you are building in masonry construction. Start with the cube, and before you make it into a rectangular shape, you should first flatten the cube down. Because in that way you can work on floor and roof insulation, which is much easier to add in masonry type of construction. Then start to pull the form in the east-west access. Of course, with timber frame you have a little bit more flexibility and still create extremely durable buildings.
P.S. I was also reading one of the discussions after a Martin Holladay blog entry about triple glazed European windows. One of the commentators from one of the north American window manufacturers made a good point. That in northern Europe we can get away with only two opening positions, for inward tilting high performance windows. While in north America, you tend to have outward opening sashes, which can open the full 90 degrees. The commentator said that in many north American climates it was essential given the higher temperatures, to allow this level of summer time ventilation to occur. I thought it was an astute point, and I felt like adding it on here.
The other debate that is happening in Europe at the moment, is whether to change to lighter tiimber construction, or remain with our higher thermal mass masonry construction – from a global warming point of view. Some studies demonstrate that with a higher thermal mass in residential construction, it might delay the length of time it takes before comfort in homes in summer time, requires us to have active cooling. Which the Co2 emission savings in building with timber are large – there are also the Co2 emissions over the lifetime of the building to consider. Based on projections of higher temperatures in coming decades, it may be the case that higher thermal mass will over the best Co2 emission reduction over the longer journey.
GBA Detail Library
A collection of one thousand construction details organized by climate and house part
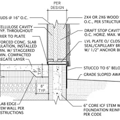
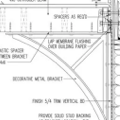
Replies
Bump....Some interesting Comments from Ireland
Brian,
lots of good comments here
my only suggestion is to break your comments/questions into smaller "bite-size" chunks
I think your long post(s) was/were overlooked
John