Rigid exterior insulation with vertical siding

I am looking for the most cost-effective and energy-efficient way of installing exterior rigid insulation where vertical siding will be installed. I want to minimize thermal bridging of the wood stud framing. I have explored blocking, stripping, extra layer or OSB or plywood sheathing. Nothing is looking quite right yet. Any ideas?
GBA Detail Library
A collection of one thousand construction details organized by climate and house part
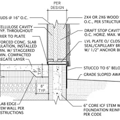
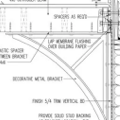
Replies
Energy-efficient and cost-effective does not a green building make. There are many other factors, including but not limited to embodied energy, environmental and human toxicity, global warming contribution, recyclability, and life-cycle costs.
Is your only purpose for using exterior rigid insulation to minimize thermal bridges? What are your concerns about the options you've explored? Where are you located and what kind of climate are you in?
Answering these questions will help us in answering yours.
Claire,
It sounds as if you're wondering how to provide something to nail your siding to.
If your vertical siding is wood, plywood, or fiber-cement, it really shouldn't be installed tight to the foam. You want an air space between the siding and the foam sheathing.
I wouldn't hesitate to install 1x3 or 2x4 horizontal strapping, 24 inches on center, on top of the foam. Screw the strapping through the foam to the studs.
I know that some people worry about drainage between the siding and the foam, but I don't. The air space allows the back of the siding to dry out, and liquid water will not really be a problem.
This is the answer I was looking for!
Thanks
To answer Robert R - There are a lot of other considerations going into this project, for energy and otherwise, which i won't go into here. The siding detail of using rigid continuous insulation is often recommended for energy loss reduction (BuildingScience,com, etc), and has the owner's keen interest, partly from past experience. It is relatively easily detailed for horizontal siding boards, but we have the challenge of the vertical wood B&B siding that is the owners' preference.
Claire,
If you are not the owner, what is your role? What is that "past experience" that makes the owner interested in "outsulation"? And what are those "other considerations" that you don't want to go into? The more information you provide us, the more appropriately we can answer your question. The choice of how or where to install a thermal break can be considered only within the larger framework (pun intended) of the building system and the design program. And you still have not disclosed what climate zone you're building in.
It sounds as if your (or the owner's) interest in exterior foam is simply to minimize thermal bridging (since you mention only energy-efficiency and not moisture management as the purpose), and there are simpler and more cost-effective ways to do that.
Additionally, if long-term durability is a concern, then I would discourage the use of vertical B&B siding, as it's not as effective a weather-seal as horizontal siding, does not work as well in a rainscreen assembly, and can be more difficult to flash and integrate with windows and the rest of the exterior cladding.
I've seen (online) some Coravent-type product placed horizontally underneath the siding every few feet. It's screwed through the foam into the studs/sheathing, and that's used to nail the vertical siding onto. You say things aren't "looking quite right yet", but I'm not too sure what aspect of it is wrong to you.
As for cost-effectiveness, you can probably get a good thermal break more cheaply by running horizontal furring inside (2x2 or some appropriate size), sheet over all that and blow it full with cellulose. I used 1.5" foam on the outside of my remodel for reducing thermal bridging, but that was because I was keeping a large portion of the old house where I didn't want to mess with the interior. To keep things consistent and get good insulation in the old part, 1.5" polyiso seemed like a good balance. Polyiso (and EPS/XPS) ain't cheap compared to cellulose.
FYI - the 1.5" polyiso was a breeze to install. The 5.5" over the vaulted ceiling, while still relatively easy to install, had the issue of long screws, which are very pricey and had to be special ordered.
Claire,
We've designed several projects that use a reverse board and batten, which is naturally rain-screened (battens on first, boards last). As well, it gives a crisp sharp profile that is very distinctive.
When applied over foam, we've done horizontal strapping as Martin described, it's been fine.
Some images for reference:
http://www.kaplanthompson.com/project.php?id=32
http://www.kaplanthompson.com/project.php?id=3
Jesse
Beautiful website, and great projects too. we've been using scrap 1/2" OSB strips for furring out vertical siding from the foam. Shoot them on with Galvanized ring shank nails through the foam rather than screws. But I really like the look of the reverse board and batten. I'd forgotten about that style, haven't done it since 1977 or 78 in Afton, Virginia during my younger days. It's definitely a self-draining sort of a situation but prone to wasp infestation as I recall. Very important to insect proof the bottom ends. We bought an eleven foot break so we can make custom Z-flashings for the bottom course on our board and batten projects. Page three of this document shows our approach http://www.chandlerdesignbuild.com/files/PoleBarnOutbuildingsDetail.pdf
Be well
Michael
Michael,
Do I understand you correctly — your vertical siding boards are attached to 1/2-inch OSB? That's it? The OSB holds the siding nails (or screws)? Do you feel that 1/2-inch OSB is an adequate substrate to hold the fasteners over the long term?
Martin,
I think Michael has the answer to your entry 8 question on the 3rd (scroll down) page of the link he gave.
Rick,
Okay, I get it. He's talking about a pole barn with horizontal planks spanning the posts, followed by rigid foam, followed by strips of 1/2-inch OSB installed in the same locations as the horizontal planks behind the foam. While this detail may make sense for a pole barn, it doesn't really make sense for a house with conventional wall framing.
Since Claire has apparently chosen not to offer additional information on this project or answer the questions I (and others) have posed, I'll take the liberty to answer some of them from her website:
http://remsbergarchitecture.com/
If you are not the owner, what is your role? Where are you located and what kind of climate are you in?
"I specialize in residential and small commercial architecture projects in the Northwest and Intermountain West."
And what are those "other considerations" that you don't want to go into?
"In my work, green building means:
•Appropriate and sufficient building size
•Durability - both in materials and timeless design
•Appropriate materials - local, recyclable, renewable, low impact
•Retaining open space, natural terrain and vegetation
•Human health and comfort
•Renewable and non-polluting energy sources
•Conservation of energy and water resources
•Passive solar heating and passive cooling
•Improvement of existing structures
•Design to support a sustainable lifestyle
•Respect for community and future generations"
That's a good list, though I might also add respectful, open, transparent, and responsive communication between all parties, including those building professionals who are sought out for advice.
Is your only purpose for using exterior rigid insulation to minimize thermal bridges? What are your concerns about the options you've explored? What is that "past experience" that makes the owner interested in "outsulation"?
These questions remain unanswered. Perhaps Claire will yet respond so that more appropriate and complete advice can be offered.
Martin
Sorry for not checking back. Yes, the boards are nailed through the OSB and foam to the full 1" planking which makes up the interior of the structure so they are only using the 1/2" OSB as a spacer, not as support for the siding. The battens are nailed only to the siding.
The galvanized Z-flashing termite barrier does make one heck of a thermal break though, it goes all the way through the wall and folds up as a sort of baseboard detail on the interior.
Michael,
I assume you meant "thermal bridge" rather than "thermal break" in regard to the flashing detail.
And it still sounds as if you have a good deal less than the recommended 1¼" ring-shank nail penetration into solid wood, if you're nailing into exposed interior 1" planking.
I appreciate all the thoughtful input. Sorry to not respond sooner to earnest questions, but I have been busy out-of-office. Controlling thermal bridging and increasing R-value are chief goals here. The contractor, based on his limited past experience of working with continuous rigid exterior insulation is concerned about longevity of the siding, particularly that it will not move over time if not secured properly, having experienced that siding directly over foam does not hold well. The owner had outsulation on a previous home, with horizontal siding and thinks it was generally successful, though there were siding problems (movement, nail popping). I appreciate all the comments about rain screen design - very helpful. This is a mostly-arid, high altitude rocky mountain climate. Most of our precipitation is as snow, and lots of it. This site also has a lot of wind and sun exposure. Climate Zone 16 as per IECC 2003. My role is architect.
Sorry, Robert, I am not trying to be elusive here. I just don't think is makes sense to delve into every last design consideration for this project, as it would be unnecessary distraction from this question on wall detailing. I will say, however, that passive solar and site orientation were considered. It is a conventional 2x6 stick-frame wall with blown-in cellulose insulation between the studs. The siding chosen by the owner will be vertical fir board and batten. There is an OSB sheathing on the outside of the studs and air barrier behind the siding. I hope this helps.
On moisture management, my concern is that the outsulation does not prohibit the wall from breathing properly. The choice of insulation type is also a topic which I welcome comments on. As this is mostly a heating climate, I do not want to create a vapor barrier in the outer portion of the wall.
Robert - Since I operate in the real world, with real clients, which have real budget concerns, it is impossible to get away from cost issues, which will always be a part of the green building conversation, like it or not. May I understand you to say that energy efficiency is a very important an critical part of green building design, though, of course not the only one, as it is a careful balance with many other considerations? If so, a would agree.
This is my first visit to this forum and webpage. I am on a trial membership. I am grateful for all the positive, generous, helpful and respectful responses, especially the ones that do not make assumptions as to unexpressed intent.
Claire, one of the reasons it's helpful if you provide more detail than you think is necessary is because with insulation, particularly with foam, there is a very real danger of problems if you do not consider the entire wall assembly, or even better, the entire house as a system. In your cold climate, with 5.5" of dense packed cellulose, you already have about R-21 in your walls. Assuming a relative humidity of 30%, with inside air at 68° and outside air at 20°, and closed cell foam "outsulation," you could experience condensation on the inner surface of the foam if the foam is less than an inch thick. Your variables may be different, but you have to be careful with exterior foam in a cold climate. Done right, it's great. Done wrong, even the best rain screen detail won't do anything to save you from moisture problems. If you're even considering foam I hope you don't have a poly vapor barrier on the inside of the wall assembly.
If you do decide to go with exterior foam, you could use the Coravent product mentioned above (http://www.cor-a-vent.com/siding-vent-sv-3.cfm) which has the benefit of allowing air to flow behind the siding, but in your arid climate I would have no qualms about simply using 1x3 softwood nailed through the foam into the studs. If your studs are 24" o.c. or if your foam will be thicker than 2" I would suggest installing one layer of foam over the entire wall, installing 2x2 nailers, and infilling between the nailers with additional foam.
Claire,
Michael and Robert make some very good points. I'd like to highlight the one Michael just made that is pretty important if you are adding a thermal barrier of XPS or EPS rigid insulation to the exterior side of the walls.
Michael said...
"If you're even considering foam I hope you don't have a poly vapor barrier on the inside of the wall assembly."
This is important, because condensation will still happen, no matter how well the interior side poly has been installed, moist interior air will find a way in. Once it condenses in the cavity it will be a lot harder for it to "dry" out if you have poly on the interior side, BSC has a number of articles on this, and the "strategies and details" part of GBA I'm sure has plenty of useful drawings for you.
If you have the appropriate amount of rigid foam on the exterior side of the wall, for your climate, then latex painted drywall should provide enough vapour resistance to minimize the amount of condensation that accumulates in the cellulose in the stud cavity, and still allow it to dry back when the "drive" is back to the interior. There is a little more detail to it, which you'll need to read the BSC articles for but that is the gist of it.
Andrew
P.S. I always welcome any corrections. : )
Claire,
The only assumption I made from your initial query was that you were a home-owner or owner-builder, since you didn't identify your role and you seemed confused about the conventional options. Given that (not unreasonable) assumption, my first response (since this is a green building forum) was to encourage you to think outside the box of cost-effective and energy efficient.
Clearly, you have experience in green design, but perhaps insufficient expertise to realize that a question about exterior insulation and rainscreen is both climate-dependent and interdependent (as Michael points out) with the rest of the building envelope and the mechanical systems in the house.
Thank you for sharing more on some of these collateral issues. I'm glad to hear that you're concerned about moisture management, as that becomes more problematic with low-perm exterior cladding systems.
Knowing your HDDs would be helpful, but it sounds as if you're in a climate which would require at least 2" of exterior XPS to avoid interior sheathing condensation, particulary if you eliminate the interior vapor barrer as should be done when reducing exterior vapor permeability.You can use 1 perm latex vapor-retarder primer to meet code, if necessary, but without an interior vapor barrier layer, the interior air barrier detailing becomes crucial.
When you say "air barrier behind the siding", I assume you mean polymeric housewrap or weather-resistant barrier (WRB), though it's not clear whether it will be located between sheathing and insulation or over the insulation. An olefin housewrap is not necessarily an air barrier, though some of them (the non-perforated ones) will meet Air Barrier Association of America (ABAA) standards as an air barrier material. But a 2D air barrier assembly and a 3D air barrier system requires careful integration between elements and a continuous, non-deflecting and durable barrier around all 6 sides of the thermal envelope, either inside or out. Since the primary purpose of the air barrier system is to limit air-borne moisture from entering the thermal envelope, in a heating climate it makes more sense for the air barrier to be inside. Absent a poly vapor barrier, this can be accomplished with the Air-Tight Drywall Approach.
I agree with Michael that, in your arid climate, a rainscreen is not necessary, provided the siding is back-sealed and there is proper integration between WRB and flashings. But your builder is correct that siding problems were not uncommon when applied directly over rigid foam board. So some spacing, with provisions for good nailing (1½" into framing for smooth nails or 1¼" into framing for ring shank). Be aware that excessive nailing through exterior foam reduces its insulating capacity, particularly at the studs that it's supposed to be thermally breaking.
The Coravent products (SV3 and SV5) are designed to be siding vents and not siding spacers. They recommend either wood strapping (with the SV5) or their own polypropylene nailing strips (Sturdi-Strip) for use with the thinner SV3. You'll note that the Sturdi-Strip is 3/8" thick while the SV3 vent is 7/16", so some crushing is expected. This may or may not create problems in anchoring the siding if the vent strips are used out-of-spec as spacer strips.
Since a vented rainscreen is unnecessary in your arid clime, I would corroborate Michael's suggestion for a double-layer exterior foam with inlaid solid wood nailers. If doors and windows will be brought out to the exterior of the outsulation layers (on solid wood nailers), then I would also suggest applying the WRB on the exterior of the foam layers for easier integration with flashings. At that plane, using self-adhering butyl flexible flashing membranes is also less problematic, since it won't be applied directly to the OSB, where it can cause moisture-retention and rot problems.
P.S. With outsulation strategies, using dense-pack cellulose between the wall framing is a good idea since it has far better moisture absorption and release properties than almost any other insulation (except straw or end-grain wood). But, again, the caveat is: no interior vapor barrier (1 perm OK).
I have built four houses and consulted on retrofitting an old barn and 100 year old cabin using Exterior Thermal Moisture Management System (ETMMS). This system is adapted by the U of Minnesota from the Canadian PERSIST system (Pressure Equalized Rain Screen Insulated Structure Technique). The difference between the two is we eliminated the rain screen. Optimal effectiveness requires drainage plane/vapor barrier/air barrier all in one product on the building structure (outside sheathing) and on the foundation. We use only WR Grace Permabarrier peel and stick. This is critical for long term control of the elements. But is does make the structure extremely air tight, so you must deliver appropriate ventilation. Then rigid foam can be applied and strapped with furring strips. No need for wrap under siding or interior vapor retarder. If you want some photos you can email me at [email protected].
Also, this technique was address by one of the leading building scientists Joe Lstiburek in an article called "The Perfect Wall". http://www.buildingscience.com/documents/insights/bsi-001-the-perfect-wall. This system will work on any structure in any climate with very little change. It is a bit silly to use the conventional methods. Good Luck!
Tom,
Do you have any links to your ETMMS, since nothing comes up on Google?
Your retort: "It is a bit silly to use the conventional methods" is a mild example of the usual disdain that the scientific/engineering community shows toward traditional or natural building approaches (or anything else from the first 2.5 million years of human evolutionary history). Perhaps unintentionally, you concluded with "Good Luck!" - which is exactly what's required with such a system.
Joe Lstiburek may consider this exterior barrier system to be "The Perfect Wall", but the wise have often said that the perfect is the enemy of the good. A hermetically-sealed house works perfectly as long as every element of it gets integrated perfectly and remains perfect during the life of the building. At least, perfectly as far as the building itself is concerned. But a building is supposed to be designed as a habitat for people.
The most advanced "building science" in the world today, the German Bau Biologie movement which integrates biological requirements for the sustenance of life with shelter technologies, understands that human beings cannot live in a plastic bag but require a breathing membrane, as does every living thing - a semi-permeable membrane which only conditionally separates the organism from the rest of the web-of-life. Isolation = death.
I suspect that it won't be too far off when we realize the foolish mistake we've made by designing and building increasingly isolating habitats. It is our technological separation from the natural world which is the root of every crisis we now face and which threatens us, and many other species, with extinction.
I read with interest the article by Joseph Lstiburek called "The Perfect Wall".
What I don't quite understand is where the air barrier needs to be. Mr. Lstibruek mentions that the air barrier should be between the outer exterior rigid insulation and the insulated wood stud wall.
He states "Repeat after me - no vapor barrier on the inside of the assembly. We want the assembly to dry inwards from the control layers and outwards from the control layers", the control layer being the place where the air barrier is placed, which is between the outer exterior rigid insulation and the insulated wood stud wall.
So, here's my question: in the winter the humidity outside the home, at least in the Nothern part of the U.S. where I live, is lower than the humidity inside the home. So it seems that we want to dry outwards from the inner wall to the outside of the house (humidity like heat moves from high levels to low levels).
If so, it seems to me that the air barrier should be on the inside of the inner wall. When the temperature drops outside the house (lets say 68 degrees inside the home and 20 degrees outside), the dew point is somewhere inside the wall. But if the elevated humidity from inside the home is locked inside the home, and the exterior humidity is low, no condensation should occur inside the walls and if there was any condensation, the drying would move towards the low humidity dry winter air outside the building envelope.
I know this is not what is done, but it just doesn't feel right. What am I missing?
Ken,
In the good "old days" (30 years ago) the common wisdom for cold climate was to establish a permeability gradient in the wall, ranging from very low at the interior surface (using a polyethylene VB) to very high at the exterior - for the reasons you cite. Under this theory of construction you would keep the water vapor trapped in the interior of the building and never let it reach the cold wood exterior where it could do its dirty work (and carry away energy). And if any leaks should occur in your tight envelope seal, the vapor molecules could easily escape to the exterior because of the increasingly higher permeability of the outer wall materials.
Under the new theory (if I have it right) we pay more homage to air flow as the principal demon in the moisture battle and we outwit the condensation gremlin by clever placement of impermeable insulation.
If we install impermeable (closed cell) foam insulation on the exterior surface of the building and seal it tightly against air flow, we accomplish two things simultaneously. The stud cavity (and exterior wood sheathing where present) is insulated from the low outside temperatures by our foam to the extent that the entire cavity stays above the dew point. If you draw a graph of winter temperature through the wall, the dew point temperature will occur inside our foam layer (if it is thick enough) where no vapor can reach. We therefore effectively prevent condensation from occurring!
And secondly, by paying a lot of attention to our air barrier, gaskets, and sealing of the foam, we prevent air leaks that can carry large quantities of moisture through our building envelope. We more or less neglect the process of "diffusion" of moisture through our interior materials because that method of moisture transfer is now deemed to be much less important than formerly thought. The interior vapor barrier has been cast on the theoretical dung heap for fear of reverse vapor drive in the summer when you have the AC going full blast..
Ken,
You're quite right that, in a cold climate and with a heated interior space, the dominant moisture drive is toward the outside. But you're a bit confused about the dynamics.
In most parts of the US, winter relative humidity (which is what we mean by "humidity") is a bit higher than summer RH, and considerably higher than winter indoor RH. But it is not RH that drives vapor diffusion - it's vapor pressure (the partial pressure of the water vapor content of air). Vapor pressure is a function of temperature and RH, with temperature playing the greater role. So, even with 100% RH winter air, at 0°F the vapor pressure is 1/7 as much as indoor vapor pressure at 68° and 40% RH.
It is because of this vapor pressure differential that vapor barriers were introduced (particularly because most houses were insulated with highly permeable and non-hygroscopic fiberglass).
However, liquid diffusion IS drive by both RH and temperature, so even in the winter there can be inward liquid diffusion coinciding with outward vapor diffusion. But, because it's energy-driven, most liquid diffusion occurs in the summer with solar radiance pushing the water like a solar wind. And, if there is an interior vapor barrier in an air-conditioned space, there is a near certainty of condensation on the backside of the barrier. It is for this reason that codes in the US have eliminated the requirement for a vapor barrier and now mandate at most a class II vapor retarder (about 1 perm) and, in some cases, allow a class III retarder (1-10 perm).
I agree with you, however, that an exterior vapor barrier in a cold climated "just doesn't feel right" because it defies common sense and conventional wisdom (which often has a sound basis in experience).
Carl,
That "common wisdom" that you refer to from the good ole days of 30 years ago, when I began my building career, is still worth noting.
Yes, we now know that most water vapor transport within a building envelope is from convection not vapor diffusion, and we correctly emphasize integral air barriers over vapor barriers. But, in these discussions, most fail to recognize that the primary cause of moisture-related building failure is from bulk leakage.
Joe's "perfect wall" approach requires both initial and perpetual perfection. While it might seem to "solve" the problems of vapor diffusion and air transport, it has the unintended consequence of sufficiently slowing drying (actually eliminating the dominant outward-drying potential) and maintaining the structural envelope at sufficiently high temperatures (the warm sheathing approach) to initiate and support the growth of mold and decay organisms should there ever be a leak, either from the exterior or from interior mechanicals. The Canadian MEWS studies have demonstrated this: a wall wetted by rain leaking through an 8" uncaulked penetration (not atypical of many constructions) would not dry in the entire two years of the study.
Also, there is a misconception about the conditions necessary for mold growth and decay. Dew point condensation is not required. Mold will grow quite nicely in warm temperatures when the RH reaches a sustained 80% (well below the dew point) and decay will occur at sustained humidity of 90%.
The "warm sheathing approach", designed to eliminate dew point conditions for all but the worst of the winter season, may still allow high humidity levels within the structural envelope - particularly if bath fans are not used or there is an undetected moisture source (such as a small but regular pipe leak (and water pipes, of course, will be placed in the conditioned space of the structural envelope once the insulation is moved entirely to the outside).
Science and technology has yet to become "smart" enough to outwit the gremlins of Mother Nature. When we (re)learn that She is still far more powerful than we, we will return to some of those "common wisdom" approaches to working WITH the forces of nature rather than thinking we can outwit them with our cleverness (what the Greeks understood as fatal hubris).
JLC doesn't always put their information online, but they are always at the cutting edge. A recent issue explains in detail the latest Building Science method that skips the sheathing altogether.
http://greenbuildingindenver.blogspot.com/2010/05/walls-for-new-construction-state-of-art.html
And check out the way Chad Ludeman plans to do it:
At the 100kHouse blog: most-affordable-effective-super-insulated-wall-assembly
On my sons home we used 5/8 ruff tex plywood to cover the rigid insulation. With the 5/8" ruff tex you will add strucural stability to the home and will not need diagonals in the walls to cut down on your r value. One thing I have learned over the 30 years of building is that insect's like ridig foam. We make a trough to let the insulation lay in to keep them out.
Kevin,
I agree about JLC
the 2 recent David Joyce articles are good
The BSC project that he writes about is featured in 3 videos here at GBA
http://link.brightcove.com/services/player/bcpid24348669001?bclid=28919737001&bctid=62514798001
I think it is pretty standard for Joe & Betsy to use more foam and minimize sheathing
Anonymous,
I don't think your method will eliminate the need for code approved bracing.
Kevin,
Just to be clear
The BSC method does not eliminate structural sheathing "altogether".
They use structural sheathing sparingly and it is fastened directly to the framing according to code.
I wouldn't describe Betsy Petit's approach to be "cutting edge", but rather "cutting corners". And, like most of the systems that come out of BSC, is far too reliant on petrochemical foams.
Betsy's concerns about SIPS are well-founded, as are her issues with double-stud walls. But I gave up on double-studs (because of a variety of issues) more than 20 years ago (after having built half a dozen in various permutations) and created what was an authentically radical envelope: the modified Larsen Truss (or the Riversong Truss), which uses native lumber and cellulose insulation and is easy and resource efficient to build. And - oh yeah - it requires no sheathing of any kind.
Robert and Carl,
Thanks for your responses. I'll need to noodle this around a bit.
Regarding this comment by Carl "If we install impermeable (closed cell) foam insulation on the exterior surface of the building and seal it tightly against air flow ...", if we have a impermeable covering the entire outside of the building, how can there be any flow of moisture from the inside ot the building to the outside? It seems to me that The Perfect Wall would need a permeable vapor barrier on the outside wall. And Mr. Lstiburek says that the Exterior rigid insulation can be "extruded or expanded polystyrene or isocyanurate or rock wool or fiberglass". I am not completely familiar with iso foam but I would assume the only permeable materials are rock wook and fiberglass.
By the way, I am not a mechanical engineer or a professional builder. But I did build a house a few years ago in a difficult environment, and this house seems to be holding up well. I'd like to take a peak inside one of the walls to see if there is any moisture or mold trapped in the wall.
Ken,
You're quite right that, with an impermeable outside layer, there can be no moisture flow from inside the house to the outside, which is the primary vapor drive direction in a cold climate.
The "perfect wall" approach (or should I say "belief" since it's more like a religion) is based on the idea that cladding can dry from the vapor-impermeable thermal/air/vapor barrier layer outward (particularly with a rainscreen), and the structural envelope can dry to the inside (if it should ever get wet at all because it's now so darn warm), and hence there is not only no need for a continuous vapor path from inside to out but it's best to arrest it completely since it's outmigration of moisture in the winter (and inmigration in the sumer) that condenses and causes all those horrible problems.
"JUST SAY NO!" is the motto of this approach. No moisture movement, no air movement, no wetting of the structural materials ever, and no worries about mold and decay. Whooppee! We beat Mother Nature and stopped the mass and energy flows that are essential to living things. But, no worries, occupants of modern homes don't much resemble living things. They are hard-wired to TVs and I-pods and I-phones and I-pads and Blackberries (except in the UAW, Saudi Arabia and India) and Google and have RFID chips embedded in their bodies, and are full of plastic prostheses and have designer babies whose traits are chosen from a menu, and never leave conditioned space...
Bobby.... weekly cleansing time...
John,
You're right, Ms. Pettit has sheathing in the corners, sorry. I was extrapolating that method to one using only let-in steel t-bracing, like Riversong.
Once again, discourse drops into the gutter because this site allows cowardly anonymous posting (and the absurdity is that we all know who the gutterballer is).
It's time to put a stop to this abomination or it's going to drag the "green" building movement down with it (but perhaps that's the motive of Anony Mouse).
I was anonymous on 27 buy mistake. I am also a green certified builder and have been building green for about 10 years before green was a word. We have been using foam board sense the 70's because of the enegy crunch. On foam board without structural plywood, bracing is required, weather using metal or plywood corners or enleting 1x4 bracing. But with 5/8" structure ruff tex the bracing is not required.
Using 1/2" R-max with blown in batt you will get a r value of 18.6 which is equal to a 2x6 wall with 1/2" plywood at a R-value of 18.4.
R-value of plywood is .40 R-19 compressed to 51/2" is only r-18
Randy,
It is the location of the structural sheathing that I question.
My understanding is that structural sheathing must be in direct contact with the framing.
Here is the response from Peter Yost when I asked a similar question about GBA details.
(BTW I think this may be THE first question asked at GBA)
https://www.greenbuildingadvisor.com/community/forum/general-questions/11778/details-and-building-code
Randy,
With ½" Rmax and BIB in a 2x6 wall, you'll get no more than R-18.2 with conventional 16" oc framing and no more than R-13.1 in a 2x4 wall.
No sheathing is structural if applied over foam board. It has to be in direct contact with framing.
And I think "green" has been a word at least since we switched from B&W TV.
The Word Green was first used by Al Gore shortly after he invented the Internet.
I think the word "green" (as in envy) was first used by Al Gore when he had his election stolen by the Supremes.
1/2" r-max with the bibs system in a 2x6 wall will achieve a r-value of 25.6, we use the bib system in 2x4 walls and get a R-15. We are using the federal energy rated standards for affordable housing where we are limited to 11% glass in the whole house. We have found that the most air loss in the homes we are building are were we us batts.
I will not use the blown in system on ceilings in attic spaces. We have gone back and found that the blown in insulation has been blown off the ceiling from the air coming through the soffit vents and gable vents.
We have also eliminated the gable vents for ridge vents, to control this from happening. The house just completed was built under the federal standards with 2x4 walls and got a Hers certified star rating of 66 34 %better then code.
Winter design temp for our area 10 degree
Wind loads 100 mph
Even assuming the best possible installation, with BIBS at R-4.2/inch and R-max at R6.5/inch, with the typical 25% framing ratio, and including all wall layers and air films, you'll get no more than R-21.9 clear wall value for a 2x6 wall.
How are you determining those numbers?
This discussion is starting to deteriorate. This reader would appreciate it if contributors could stay on the topic of building science. Thank you.
Clair, 9/6/10
Previous answer from Armstrong was good. Go to the Cor-A-Vent.com web site and look for this detail,
http://www.cor-a-vent.com/siding-vent-sv-3.cfm. I know a contractor who used this detail for a board & batten installation with great success.
This daily respondent would appreciate it if you would use your real name. If you aren't willing to stand by your words, then you deserve to be ignored or eliminated from this forum.
I have been studying high-r walls as well as air barriers and vapor retarders in an effort to design/specify a high-r wall that will perform well in CT (Zone 5). I have now spent many hours reading blogs and case studies etc. regarding these subject matters. I have some solid ideas and have learned a lot about high-r wall construction. Currently, I plan to specify 2x6 studs at 24”o.c. with fiberglass or cellulous insulation in the cavity. The horizontal cement board siding will be fastened through vertical strapping, through the rigid, and into the stud beyond creating a drainage plane or rain screen. The interior will be finished with an air tight gypsum approach. However, due to conflicting information and/or vague descriptions I still have a number of unanswered questions/concerns as follows:
1. Based on my readings, I have a concern regarding the shrinkage of rigid insulation and the longevity of the adhesive on tapes therefore I plan to use Tyvek or some other house wrap in addition to the exterior rigid insulation however, it is not clear to me where the Tyvek should be placed. Should it be on the inside or the outside of the rigid insulation?
2. I am aware of a product used under EIFS that is supposedly drainage plain, an air barrier, and vapor retarder all in one. I believe it comes in two different levels of permeability. I am curious to know why this product is not a more popular method in other non-stucco systems and why more people don’t consider using this under siding as it “seam” (pun intended) superior to wraps with tape.
3. I have read pros and cons regarding EPS, XPS, and PIC. Faced and un-faced. Unfortunately, I still don’t know what the best choice of rigid is for this application. What is the ideal perm value for the rigid insulation in this application? Should it be faced or un-faced? (Thus far I assume un-faced as there is a code requirement for an interior vapor barrier and I don’t want to create a double barrier however, some of the projects highlighted at building science are using two (2) layers of foil-faced rigid insulation???
4. I understand the idea of keeping the dew point outside of the structure. How much r-value must be outside of the structure in order to achieve this in zone 5? I have read conflicting information on this matter.
5. The whole discussion of vapor barriers is somewhat frustrating as it seems that the some of the experts at least partially disagree with each other. I understand the concept of drying to the inside and the outside. I understand the negative effects of a double vapor barrier. I am also aware of the code requirements for an interior vapor “barrier” in zone 5. If the exterior rigid insulation provides enough r-value to get the dew point out of the structure, should I go with NO interior vapor barrier (against code), a Class II (kraft paper), or a Class III (latex paint) on the interior?
I apologize if some of these questions have been answered previously however; I have been unable to find direct answers to these questions/concerns. Any information that the readers can supply would be greatly appreciated. Thank you.
Coy,
It looks like your long post with many questions has been posted twice. I answered your questions here:
https://www.greenbuildingadvisor.com/community/forum/green-building-techniques/18196/still-not-100-clear#comment-13321
Robert Riversong: I am afraid that your pitbull like attitude towards other readers kept me from using my name, which in this case was irrelevant to the point I was making. Perhaps a more welcoming attitude would make people feel more comfortable using their names.
Re-formatted:
Thanks for the compliment.
The American Pit Bull Terrier (which was the preferred pet of both President Roosevelt and Helen Keller) has as unearned a reputation for aggression as those, like myself, who state truths with blunt honesty.
According to extensive professional testing performed by the American Temperament Testing Society (ATTS), the Pit Bull is higher ranked than these common pet breeds: Afghan Hound, Beagle, Border Collie, Collie, Dalmatian, German Shepherd, Golden Retriever, Great Dane, Labrador Retriever, Miniature Poodle, Samoyed, Shetland Sheepdog - and ranks higher than the average of all breeds.
The Pit Bull, like me, is "never aggressive towards people without real need, should not be an instigator, yet is unlikely to shy away from a challenge."
But don't have the audacity to blame me for your unwillingness to put your name to your statements or I AM liable to bare my teeth.
Mr. Riversong:
It may be too late to turn this into a more constructive discussion, but I will try. The kind of attitude I was referring to is your lecturing of Claire in post 11 after she failed to respond to your question within one day.
"That's a good list, though I might also add respectful, open, transparent, and responsive communication between all parties, including those building professionals who are sought out for advice."
Builders are busy people. Not everybody is able or willing to visit these forums on a daily basis and to in efffect call a reader disrespectful for not responding within a day is unreasonable and will make people reconsider whether to contribute to a forum at all. I felt sorry for Claire for your lashing out at her like that and in my mind it undermines your credibility.
Respectfully, Anony Mouse
Yes, Anony Mouse, it's too late to make this constructive when you accuse me of something for which there is no evidence and do so from a position of anonymity, unwiling to stand by your misplaced words.
Reread that post you refer to. There was not a word of disrespect in it, but merely a request for the original poster to answer the questions asked of her and provide sufficient information to receive constructive responses from the rest of us.
Mr. Riversong:
It is clear from post 14 that I am not the only one who interpreted your post 11 as critical. To write that someone is lacking 'respectful, open, transparent, and responsive communication' after not responding to your post within one day does not contribute to an open discussion. Intended or not, that comment was in my opinion a turning point in this forum. Since this is not a scientific argument, there is no scientific proof of the evidence you ask for. This is simply the opinion of one reader. I am sharing it with you because I care about the quality of the discussions at greenbuildingadvisor.com.
The critical tone of this forum was re-enforced by your post 36. You may disagree with anonymous posts, but the forum allows for it and you should take up that issue with the editors instead of taking it out on other contributors. Words like 'cowardly' and 'gutterballer' do not belong in online forums and do not contribute to a positive atmosphere. No, the ends do not justify the means.
When the discussion started to deteriorate, I decided to post a friendly request to stay on topic since I had been enjoying the building science part of the discussion (post 44). Because of the general negativity displayed up till then I did not want to post my name and become the next victim of this negativity. My post was merely a 'point of order', and I believe it was a valid one. Although you seem to have interpreted it as a personal attack on you, it was not intended as a criticism of anyone in particular. It was a friendly request to stay on topic. You could have decided to take the message on its merit, instead of attacking the messenger, which only confirmed that my decision to post anonymously was the right one.
All writers want to be read and in most cases to be respected by their readership. Some readers interpret some of your posts as critical, negative, and heavy handed and believe that this attitude undermines the credibility of the writer. The choice is yours.
This is my last post in this forum. You can have the last word, but I won't be reading it. You are an angry man, Robert. Take good care of yourself.
Anony Mouse
Anony Mouse,
You can read this or not. But you are completely wrong about me and so have clearly projected your own bias and your own emotional state onto my words. I harbor no anger whatsoever, and have always responded with calm objectivity, and intellectual honesty.
But I am justifiably critical of inappropriate responses (such as yours), failure to answer requests for the information necessary to respond constructively to questions, and for the refusal of any adult to stand by their words by putting their name to them.
This is not a forum for enforced "political correctness", but for free and open dialogue, which must include critical responses. Those who cannot tolerate their words being challenged should not venture into such a discussion forum.