Double studs vs. thick foam OVE…

I have read about every blog I could find and skimmed through most of the Q&A….tons of great info but nothing directly related to my exact situation.
Working on the design of a new house…In zone 6 with about 7400 HDD. House is about 1700 sqft on the main level, with full walkout basement (walks out to the north) and about another 1400 heated floor space in the basement.
Prairie style home with 2′ over hangs, solar design south glass (summer shading), no east or west glass, triple pane north glass. U values at .18 and air ratings at .04. Double pane on the south side, u is .27. Same air ratings.
Here is what I am debating. Going with 3 possible shell designs. The basement will be Hobbs ICF (about r-28-r30ish) on the 3 sides, walkout side will be built with the same higher r as the rest of the house. Both assemblies I want to put as much focus on an exterior air barrier as I can, then double it up with air tight drywall. (r values are clear wall obviously for ease)
All foam will be strapped with cement board siding.
Option 1: double stud wall, 10-12″ thick space, dense pack cellulose, Zip sheathing (there has been debate about drying ability of Zip. I have contacted Zip building scientists directly and they claim is has a perm rating of 2-3). Roughly $2.15 sqft material costs with more foundation taken into account to keep interior floor space similar size. r-40+
Option 2: 2×6 framing, 24″ oc. 1″ exterior polyiso, taped. over 1″ XPS, 1/2 osb/plywood sheathing, wet blown cellulose. About $2.05 sqft materials. r- 32. outie windows. Basically exterior foam code min. I have also considered to skip the poly iso and do 2 layers of 1.5″ xps, taped.
Option 3: 2×6 framing, 24″ oc, 1″ exterior polyiso, taped over 3″ solid type 2 EPS, 1/2″ osb/plywood, wet blown cellulose. About $2.15 sqft materials. r-41. Outie windows.
Any big thoughts on the best approach? My thinking is leaning towards exterior thick foams would do a better job at sealing up the house from both vapor and air vs the Zip and thicker wall. Since I will be building it (yes, I do have years of construction experience) I am thinking the 2×6 and thicker foam will be faster and easier to detail?
I did consider at one time to run the ICF to the roof, but I am left with a high dollar mid r 25 wall assembly. It does not pay off in my opinion.
Any thoughts or insights (or possible alternative suggestions) would be appreciated.
GBA Detail Library
A collection of one thousand construction details organized by climate and house part
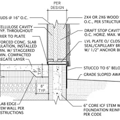
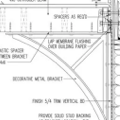
Replies
I would go with the double wall, the most cost effective option in my opinion. Foam in the wall system is expensive and hard to work with, bracing and fastening siding are tough details.
Jesse,
You'll probably have good success with any of your listed options, so if you have a personal preference, that's the way to go.
Although many builders are trying to use less foam for environmental reasons, exterior rigid foam probably aids durability significantly, because it helps keep the sheathing and framing warm and dry.
I am really leaning towards the thicker foam. Everything I have read here and Building Science studies tends to prefer thicker foams for higher performance within the r30-40 range. I also feel the air tightness will be higher with 2 layers of taped foams vs the Zip.
Any thoughts on the foam itself? I have also considered 2 layers of 1.5" XPS. Is polyiso the 'best' foam to place on the outer face of the assembly, or would XPS do well also? It would be the drainage plane, no house wraps.
thanks
Jesse,
From an environmental perspective (blowing agents and flame retardants), polyiso wins hands down.
I agree with Doug.
I think Double stud Walls would be much more "Buildable"
7400 HDD is similar to Vermont
Martin, what is your preferred wall assembly for Vermont?
Are you now leaning back to foam?
Environmentally speaking does Polyiso "win" over Cellulose?
Is Outside Polyiso more Buildable or more Affordable than a double wall?
Martin, do you have some new information?
Have you learned of any failures of Double Stud Walls w/Dense-pak Cellulose AND no poly-vapor barrier?
John,
As I've said before, it is possible to say that both the Red Sox and the Yankees are high-quality baseball teams.
Martin, ok.... just one question....
Have you learned of any failures of Double Stud Walls w/Dense-pak Cellulose?
John,
No, but I just saw a presentation at a building science conference by Mark Gauvin reporting on some findings from a test hut in Coquitlam, British Columbia. Findings are still preliminary, but there were photos showing mold growth on the interior side of OSB sheathing in walls without foam sheathing over the OSB -- under some conditions (50% interior RH). The walls with rigid foam over the OSB were clean and dry -- no signs of mold.
There are a lot of variables here, and many types of walls will work. But the evidence shows:
- Rainscreen drainage gaps are good, and
- Rigid exterior foam is good.
As Mark said, "Exterior insulation keep wood warm, keep wood dry, reduces condensation potential, reduces thermal bridging, reduces energy loss -- but most importantly, increases durability."
In a way, there's nothing really new in these conclusions. But for me, they were a reminder of all the good things that happen when we install exterior rigid foam.
Drainage planes and no osb sounds like the way to build thick cellulose walls. I have pictures of a even Advantech OSB completely rotted out and crumbling because it was installed over a wet sealed crawlspace for 3 years.
OSB is so inexpensive. But it must be kept dry as a bone for it's entire lifespan to be of any value.
As to rigid foam, the day is basically here that through tech. progress we will have rigid foam that is not harmful to the planet any more than the basic harm that several billion too many of us exist. I am all for using rigid foam and rainscreens and also for thick cellulose filled walls if and only if properly detailed for moisture and no OSB.
John
cost of the 2 really depends on the total r desired. From my extensive pricing (this has been going on for over 1 year now...) for r-35 and below, I have found that (pure materials cost) 2x6 24" oc with 2 layers of foam to be the same as double stud 10" wall in $. However the more r desired, then that starts to shift towards the double stud option. r-40 and up probably can not be beat, cost wise, for a double stud. However the big mystery in my pricing is labor. I do not know how labor costs affect it. Obviously double stud is more, however when you add in the double layers of foaming, taped, then the strapping and detailing around the windows (plywood RO, etc) labor could start to be a wash. The advantage thicker foams have is in your building footprint. if you want your rooms the right size, the foundation needs to grow add dollars to the double stud number where the foam adds to the exterior and can overhang the foundation if need be. Really thick walls also play against you some on taxing. Since they measure the exterior of your shell, you are being taxed for unusable square footage. 200 LF of exterior 12" wall adds 200 sqft to your building footprint of taxable, unusable area. Obviously one would hope and assume the energy savings number would far surpass the extra tax number. but something to think about. You can hit R35 or even 40 with a thinner, tighter wall then with double studs.
1" polyiso is going for around $17 a sheet around here. 1" of XPS is going for around $12. 1.5" is going around 16. This is why I was curious to having an r15 and 3" of XPS vs an r 13 and having 2" of poly at a higher price. My area calls for 11.25" for "safe" sheathing condensation levels for a 2x6 stud.
Jesse,
In your cost calcs for the thicker foam, have you considered the additional for siding attachment? If you are putting strapping over foam, you'll need SIPS type screws for attaching the strapping. If you were strapping the double wall for a rainscreen, you could use conventional fasteners. Also consider you are sheathing the house three times: plywood, foam layer, foam layer.
price includes 1x3 strapping and 6" headlok screws (suckers arent cheap!). I still need to check spacing however...I priced 5 per 9' stud. There is around $400 in screws. If i stick to 2" of foam, I am thinking I can change to a 4.5" deck screw or something spaced a littler closer. Even sticking with headlok screws, a 4.5" saves about $150 vs the 6". I was also thinking about eliminating most mechanical attachment of foam, rather realy on caulk and the strapping to secure it. Frame, sheathing/caulk, and strap all laying down prior to tipping.
The sheathing is more of a "added sense of security" vs necessity. It will be sided in cement siding however. However I have debated eliminating it except for shear required locations. I just personally think it makes 24" spaced studs a little stiffer in the assembly. Thoughts on this? (I have never framed a full house with out osb)
OSB as an exterior sheathing in a cold climate is a horrible choice, when building a double wall use fiberboard sheathing with housewrap and a rainscreen. The wall should dry to the cold side, OSB will not allow this.
so would you recommend that black fiberboard product instead or is there something else?
I assume fiberboards meet the same structural requirements for shear and bracing? I have never worked with the stuff nor seen it used in our area.
Having built both double walls and exterior foam, I'd say the overall cost savings are with double wall, easily. The interior walls are easy to build and go up quickly. Exterior foam is slow to install, expensive, and makes all the exterior details much harder and slower.
The cellulose itself is a relatively small part of the cost of the insulation install. Obviously it's harder to install an open system than a single wall with closed bays, but a good installer should know how to do it - make sure it's not their first time with a double wall!
And the wall thickness shouldn't vary that much between the two - a matter of inches if you're talking comparable R-values.
Dan
so you framed your double walls separately and tilted the inner wall later? I have been researching the various methods of framing them. I would like to frame both walls, sheath, and use 3/4" plywood on the top and bottom to tie the 2 together. however this gives me a single top plate. This appears to be a code violation mixing 16" oc 2x4 framing with trusses 24" oc. The other thought is to use double plates, but the first plate are 2x4s and then a 2x12 as the top plate. Then use plywood strips towards the bottom of the wall to tie the 2 together.
Jesse,
Dan Kolbert has a very good article at JLC magazine and available Online w/ membership
http://www.jlconline.com/cgi-bin/jlconline.storefront/EN/UserTemplate/2
There are many good articles about superinsulated enclosures
just to name a few more builder/authors......John Abrams, David Joyce, Thorsten Chlupp.
I see no reason to "tie" the double walls together with plywood or a wide top plate. If the walls rest on a plywood subfloor just nail each wall to the chalk line. Same way on the top, the rafters will hold the wall spacing and walls parallel to the rafters will require an occasional 2 x 4 spacer on top of the double plate. The double wall is designed to minimize thermal bridging, no wide plates. Only around the windows do I use a wrap of 1/2" plywood the width of the wall, spacers would work as well. Some folks flare the inner wall around windows to allow for more daylighting, be creative!
Thanks, John. Jesse, yes, we build them separately. I think it makes more sense, is easier and faster. Never understood the desire to build them together. To me one of the nice things about double wall is all the walls are nice and light, easy to raise and move around. Guess it depends how good a framer you are.
Dan
thanks. Very true. I love tilting interior walls vs the typical 2x6 sheathed exterior wall. I think I will try it this way assuming I go the double stud route.