Tearing off my roof – reducing heat gain in my finished attic w/cathedral ceiling?

Greetings all – Thanks for maintaining such a fantastic forum. I’ve spent the past few hours reading and learning, and I’m seeking advice on my particular unique situation.
The background – I have a 1944 Cape Cod-style house located in Portland, OR, zone 4C. The attic is a finished space with a cathedral ceiling which we use as our bedroom. The rafters are 2×4 with the cavities currently insulated with what is probably R11 fiberglass and no ventilation. The interior is finished with drywall which continues all the way to the peak of the roof – there’s no “flat space” at the peak other than a ~6″ board.
The knee walls are also insulated with r11-13. There is also a small area beyond the kneewalls (under the lowest part of the roof) that has conventional insulation of fiberglass batts between joists.
It’s time to replace the roof – 2-3 layers of asphalt on cedar, all on top of the old-style 1x planks. It seems that the “right” way to do this is to tear off everything down to the rafters, which gives me the opportunity to try to add insulation and/or ventilation from the outside.
First let me state that in our relatively mild climate, reducing our winter heating bills isn’t our biggest concern – they are already pretty low with our ancient oil furnace, and should be lower after our gas conversion. What I’m most interested in is reducing the summer temps in the attic bedroom, presumably by reducing the heat transfer from the sun-heated roof.
One added complication is that the roof has essentially no overhang, which makes eave vents difficult.
The question is – what to do? Given the extremely limited depth of the rafter bays, I could get a few more R’s using spray foam or rigid foam, but I’m not sure that it would be worth the added expense. One roofer has suggested adding pre-fab channels, edge vents and a ridge vent in order to ventilate the roof ,but this just cuts the space available for insulation even more.
Another thought I had was using Energy Star shingles to reduce heat gain but again I’m not sure they would be worth the expense.
So – what would you advise in this situation? Apologies in advance for my any unclear rambling.
Thanks for your advice.
GBA Detail Library
A collection of one thousand construction details organized by climate and house part
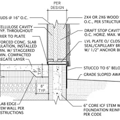
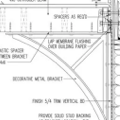
Replies
Fur out the rafters after you have them exposed, this will add space for additional insulation and ventilation. I would lean towards a quality spray foam since you will have it all open, and not likely to again for several decades. Adding overhangs would be a good idea from a ventilation perspective too. The thermal break and air barrier will make the space much more comfortable. If you have a vapor barrier in the walls you'll need to tie it into the roof as well.
Thaddeus,
Your re-roofing job is a perfect opportunity to increase the R-value of your roof to minimum code levels. Install as much rigid foam on top of the existing sheathing as you can afford -- I would suggest at least R-30 of new foam -- with or without ventilation channels above the foam.
Thaddeus,
1st off: Adding rigid foam is the easiest and most accessible method of reaching you goal of reducing summer heat gain. It's straight forward, and the foam is easy to get. It will work fine.
If you'd like to reduce your foam use (for whatever reason), read on...
Similar, or better results to a foam build-up can be had with less thickness added to the roof line, In reducing summer heat gain, what you're trying to do is reduce the temperature amplitude difference from the outside of the roof and the inside of the roof (duh!).
While lowering the indoor temperature peak on a hot day will obviously lower the indoor temps, increasing the cycle time that it takes to reach the interior peak temp means that the room can stay at comfortable temperatures longer. That is the effect of the insulating materials heat storage capacity. An example of this is that if the cycle time ( the time it takes the heat to reach the inside and the highest indoor temp of the day is reached) is 4 hours… Then if the roof gets it's hottest at 2PM, the inside temperature peak will be 4 hours later at say… 6PM. At that point the upstairs bedroom will be uncomfortable for a long time (as you know).
By choosing materials with higher storage capacity, the heat takes longer to "get in". While the increase in indoor temperature will still occur, delaying the cycle time from 4 hours to 13 hours will mean that the indoor peak is: 1, not as high & 2: happening at 13 hours later at 3AM instead of 4 PM.
As you can guess, some materials do better at keeping heat out than others. Products like Dense Packed Cellulose and Wood Fiber Insulation boards while having lower "R" values per inch have a much higher heat storage capacity than lightweight materials like Foam Boards.
While adding a foam "build-up" is simple and cost effective, better results may be achieved without foam.
foam sheets on top of the roof are far more economical that foam spraying the interior or trying to dense pack cellulose inside, although environmentally cellulose is the way to go and it has other advantages
go for a energy star rated metal roof that will help deflect the heat (some lighter colors will almost absorb nothing), then the foam help seals in the cool generated inside, then a peel and stick or other hardy duty roof deck covering along with air sealing any gaps prevents conditioned air leakage
if you think venting is a solution you can vent in between the added foam and new roof as well with a number of options - your basically building a new outer roof deck on top the old
consider some type of exterior vent to exhaust hot air from the area on hot days or on evenings and open up lower floor windows to bring in the cool air. or add in appropriate intake vents that route to your A/C
also consider that your 2x4 rafters are probably no where near code - if you are going to extremes with a full tear off, beefing up the roof wouldn't be a bad idea depending on your climate extremes. your builder can look at hurricane fortified codes for clues (not just for hurricanes)
i've got an old 2x4 rafter cathedral ceiling with the 1x horizontal planks (built back when 2x4 were actually 2x4) my builder isn't happy with doing anything with the space without a rebuild; 2x10's are minimum now to give you an idea.
Thanks all for the thoughtful replies.
A few questions(and please pardon my ignorance):when we're talking about adding rigid foam, are you referring to some kind of engineered panel (SIP?) that can goes on top of the rafters and then shingles on the panel?
Albert: I like where you're going with the higher thermal capacity materials. I'm not sure what you mean when you say similar results can be had with less thickness added compared to foam... doesn't foam have higher R-value? Or do you mean that similar results can be had with less R due to the higher thermal capacity? I'm also concerned about the added weight of the cellulose on the roof, although after I run the numbers it may be that I'm losing more weight in the tear-off than I'd be gaining in insulation.
Also I'm confused by Bob's comment that foam would be cheaper than cellulose - I thought it would be the other way around?
As for energy star roofing, I'm reluctant to go with metal due to cost, appearance and noise (think rain on a metal roof). I'm considering energy star asphalt shingles, but there seem to be issues with availability and cost there as well.
Also still not clear on the venting question... some things I've read have indicated that with sufficient insulation, venting isn't necessary/desirable. However I am concerned about creating new condensation points between insulation layers and the potential for rot/damage.
On the subject of beefing up the 2x4 rafters... this roof survived what was probably a 100-year storm in 1962, and snow load isn't really an issue around here, so I'm not terribly motivated to do that.
One problem I'm having is with finding an insulation contractor willing to work with more "creative" solutions than just rolling out fiberglass batts. I chose three highly-rated contractors from Angie's List... one never even answered the phone and the other two haven't called me back!
Any suggestions on finding a local contractor? Is there some kind of trade association I can consult?
Thanks again for your input.
Thaddeus,
You can install any type of rigid foam on top of your existing roof sheathing: EPS, XPS, or polyiso. There are some photos here: An Old House Gets a Superinsulation Retrofit.
Once the foam is installed, you can either install strapping (for metal roofing) or a layer of plywood or OSB (for asphalt shingles). You can also install nailbase, which is rigid foam with a facing of OSB on one side.
Thaddeus,
A couple of things on your list:
1, Foam boards will be the lightest weight insulation to add. This is said in terms of the weight capacity of your roof framing.
2, Specifically for summer heat gain only, Dense Cellulose or Wood Fibre insulation boards do better with heat gain than foam. My statement was: While the same R values may be in place, the denser cellulose wood fibre products will delay and therefore reduce summer heat gain. As such, if heat gain is the issue, less insulation can deliver good results. Perhaps that's a bad statement in retrospect. It may sound like I'm saying that you can build to less than code. Please do accept the fact that you should meet code minimums if your going to add insulation to your roof.
3, A vented metal roof will last much longer than shingles. The venting is just a gap below the metal to let condensation dry and break the thermal bridging to the sheathing.
I don't know that many builders in Portland. I do know both Green Hammer and Hammer and Hand. Contact them. They are very smart builders. If the work is not right for them, they can refer you to others.
foam is generally cheaper in overall install cost in a retrofit installation where you are already tearing off the roof. adding foam board to the top of the roof after tear off is simple. tearing out the interior to get access to shoot cellulose is not quite as easy. off course there are exceptions, like areas with competitive cellulose installers. in your case you really need larger rafters to get the cellulose depth you need.
also consider a peel and stick membrane over the initial roof deck and down the eave to air seal. air sealing is just as important as increasing r-value.
just crank the heater inside your car on a cold day and roll down the window and you'll understand why air sealing is necessary.
if you really want to solve the heat issues, you need a way to move the hot air out. regardless of how much insulation you add to the roof, the stack effect will send warm air upstairs
you also need to install a roof that reduces heat gain. dark shingles just are not going to do that. insulation doesn't stop heat transfer, it just slows it down. if you put a blacktop driveway on your roof, the heat is going to come. off course it is a balancing of costs. in a place like here, people would probably prefer to spend the money on the environmentally friendly product that reduces other concerns. you could also just install a massive amount of air conditioning too
Thanks again, one and all.
I guess I'm still not totally clear on the foam board installation - how does the plywood get secured on top of the foam? Really long screws? Is that considered... secure?
Bob- you don't mention installing cellulose from the outside as an option. If I'm tearing off the roof (including the old 1x decking/sheathing), why wouldn't/couldn't I install the cellulose from the outside? I understand that to dense-pack it needs some kind of containment, right? Couldn't I use a similar method (netting?) as if it were going into an open wall?
At this point I'm starting to lean towards this idea: add 2x6s on top of the existing rafters (to give 10" more-or-less bays) and fill with dense-pack cellulose. This would also allow me to extend the new rafters beyond the exterior walls and give me eaves that I currently lack, which in turn would facilitate a 1" vent channel from eve to ridge vent, on top of the cellulose. The 2x6's would presumably transfer load to the walls, taking the strain off of the 2x4s.
On the subject of code (and I realize you guys aren't lawyers, code inspectors, etc): would one typically be required to upgrade to code insulation levels when opening the roof? Do similar rules apply as for electrical/plumbing/etc? In other words will a 10" cavity and dense-pack not allow me to meet code(R38)?
One point of concern: if I do the plan outlined above, won't the weight of the cellulose primarily rest on my drywall? Any thoughts on if that's a significant issue?
And this may be a little out there, but I was thinking about the thermal bridge created by the 2x4 and 2x6 "stacked", and I thought - what if the 2x6's were offset from the 2x4s to create a break?
I'm not very clear on where a vapor/air barrier should go in this situation... against the drywall?
Last but not least, I finally got an insulation contractor to call me... meeting with him on Wednesday.
Thaddeus,
I don't have the expertise of the others who have responded, but I'll throw my ideas out as food for thought.
You mentioned concerns about the weight of cellulose on the drywall. A few months ago, there was a GBA discussion about that. If my memory is correct, the solution was to attach the netting to the bottom of the rafters and strap the rafters before installing the cellulose. The drywall will span the bulges.
You indicated you would like to add 2x6s to give strength and increase the insulating depth. You also asked about thermal bridging. If you cut rigid foam, such as Styrofoam SM, into 1.5 inch wide strips and nailed them to the top of the 2x4s, then added the 2x6, you would have a thermal break and more depth. Use twinned plywood gussets every three or four feet to tie the 2x4 to the 2x6 and add strength. This would be like a roof Larsen Truss.
If you needed more depth, add another strip of foam on top of each 2x6. This would separate the 2x6 from your plywood roof deck. The layers of foam could be 1 or 1.5 inches thick. - Jim
"I guess I'm still not totally clear on the foam board installation - how does the plywood get secured on top of the foam? Really long screws? Is that considered... secure?"
yes, check with the folks behind the counter at your local ABC supply roofing distributor, they can set you up with the stuff you need and training videos etc. they sell the foam boards as well as the nail base foam that has OSB already attached and they have all the screws etc that you will need.
James Morgan had a great detail on a similar post recently where he recommended stepping the new foam out beyond the existing (crooked and warped) fascia to create a tiered look to the roof edge. This also gets you a nice straight line for your metal roof edging, gutters and starts your roofing off with something easier to work with than most old roof edges.
Hi again all - I spoke with a couple insulation contractors and heard their opinions.
One contractor wasn't very impressive - seemed disorganized, had never done a netted install for cellulose, seemed unsure on the best way to install cellulose in a vaulted ceiling. Ended up deciding on blowing into the cavity after the sheathing was on, using the ridge vent channel for access... but this was after *I* asked if that was an option.
2nd contractor definitely had his stuff together much better, but wasn't a fan of cellulose for this application. Per his numbers, the cellulose only had an R value of 3.8, while the HD fiberglass was 4.something.
He suggested FG batts with 3" of rigid foam board on top. The board would provide a good vent channel as well as helping to solve the wind washing issue of the FG.
One question for ya'll... how to best insulate the wing attics? Do I insulate the new rafter bays from ridge to soffit, or drop down the kneewall to the attic floor? I assume that it's usually preferred to not include the attic space in the conditioned envelope, but in this case it seems like I'd be adding unnecessary complexity and probably labor cost to insulate the kneewall. Also an additional factor is that I have a storage area in the wing attic, so insulating the door and floor of the storage would be awkward at best, not to mention accommodating less r-value than the continuous rafter insulation.
Another question - is a 1" vent channel sufficient in this application? I assume the relatively steep slope of my roof (not quite 45 degrees, but close) will help air circulation.
Any comments or thoughts are appreciated as always.