Why are my wood floors cupping?

My new hickory solid wood floors are beginning to cup as soon it got hot and humid outside. I live in Southeast, LA and the house has a 3′ crawl space under it. I tried to research the proper insulation to use and I went with a sprayed open cell foam under the subfloor. I have tar paper between the floor and subfloor and I did have the floors adjusted to the home air conditions prior to installing it. I also verified that I had proper expansion room around the floor edges.
I’ve been told that air is condensing under my floor and that I should have put in either closed cell foam, or enclosed my crawl space. At this point both would be difficult and expensive to do, but if it controls the cupping I’ll consider it. Could my AC be pulling out too much humidity and therefore “drying” the upper surface of the floor? Maybe my attic vent is pulling out too much air and forcing up the outside humid air through my floor. No idea… At this point I’m lost. Any ideas?
GBA Detail Library
A collection of one thousand construction details organized by climate and house part
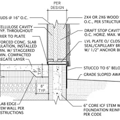
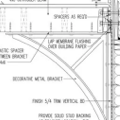
Replies
Kevin,
It sounds like you have a ventilated crawl space. That means that your crawlspace is full of warm, humid air. Your house is air conditioned, so it is relatively cool and dry. You chose to install a vapor-permeable insulation, and the direction of the vapor drive is from your warm, humid crawl space towards your cool, dry floor.
So the underside of your flooring is always damp, and the upper side of your flooring is always dry. It's no surprise that it is cupping.
The best solution would be a sealed, conditioned crawl space. Seal up your vents, insulate your crawlspace walls with rigid foam, install a poly ground cover, and install a forced-air register in your crawlspace to condition the area.
Failing that, you could install a continuous horizontal layer of foil-faced polyisocyanurate insulation along the underside of your floor joists. Seal the seams very carefully with housewrap tape. Then you'll have a vapor barrier where it belongs.
The immediate remedy to slow the cupping will be to run a dehumidifier or two draining through hoses to the exterior and a fan to circulate the air under your floor and close up the crawlspace vents. IE later today or first thing in the morning. If you have electric attic vents cut the power to them, they don't actually work anyway.
Finally hire an insulation company to spread 6mil poly on the floor of the crawl and start looking into the best method to enclose the perimeter walls and make it a true sealed crawl, probably two layers of foil faced poly-iso on the crawlspace walls but there are a lot of variables there. first get the basics done as outlined above.
If you follow Michael's advice, I'd like to clarify one point: put the dehumidifiers in the crawl space, not in the house. And don't forget to seal your crawl space vents!
My house doesn't have "vent". It actually has 30" x 70" openings between the individual brick piers. This makes sealing open the crawl space much more difficult, but I may have no choice. I like the vapor barrier idea under the floor joists, but I'm not sure how easy that will be either, due to my water piping being under the house. I'll take a look when I get home. Any ideas on how best to close off my large openings that will be largely exposed to sun and rain? Any recommendations on dehumidifier types (cheap indoor residental or expensive exterior commerical grade)? I hear that some of these dehumidifiers can cost over a $1000.
Thanks, so much for the advice!!!!!
Kevin,
If your house is built on brick piers, and your crawl space is entirely open, your only choice is to install the foil-faced poly (or a similar product) under the floor joists. The poly should probably be protected by a layer of OSB or plywood.
Could I just use non-perforated radiant barrier cloth to attach to the joists? It might add to my R value, and it should prevent the vapor from coming through. It might be easier to install and cheaper than foil faced foam board. Now that I thinking about it, what about just stapling 6 mil plastic to the underneath? If neither of my ideas are valid, how thick should your recommended foil faced board be? Again thanks so much for the feedback. This helps me out greatly.
Kevin,
The problem with a radiant barrier or 6-mil polethylene is that they become wrong-side vapor barriers in winter, when it's likely that moisture will condense on the upper side of the barriers, trapping water in your floor.
The polyiso has an R-value, so it will never be cold enough in winter to allow wintertime condensation.
I would use at least 1-inch polyiso. Be sure to get the foil-faced stuff, and tape the seams with high-quality tape.
Kevin
I build in Houston so I assume we are in about the same climate, very hot and humid. I use a lot of hickory flooring as you mentioned. All of my homes are on concrete slab foundations, we use 2x4 or 1x4 screeds set in hot tar, then finish floor over the screeds. There are a couple of areas here where we do pier and beam foundations for affect like you have described. The best technique I’ve seen is to use Ice & Water Shield on the plywood subloor as a moisture barrier, not builder’s paper (felt).
Also, you said you acclimated the wood first, how long did you run your AC before installing, did you stick stack your hardwoods in the house, and did you take a moisture content reading on the flooring? Was it kiln dried? Also, I’ve seen plywood subfloor that gets rained on a lot and has a high moisture content. Wood floors are very persnickety in this climate.