Real world quotes on HFO blown foam, anyone?

A guy in my office is (finally!) getting around to insulating the basement of his 1920s cinder block (real cinder blocks, not CMU) foundation bungalow. After getting some quotes using different approaches, he’s opted to do it with 3″ of HFO blown closed cell foam (~R20-ish) .
There is about 950 square feet of wall to be foamed, x 3″ = 2850 board feet of foam. The line item for the foam portion is about $4K, which would make it $4000 / 2850 =
$1.40 per board foot for R7, or about 20 cents per R-foot.
That’s about a 15% cost/R premium compared to a single 2″ lift of HFC blown 2lb foam, but is in fact cheaper than R20 of HFC blown foam since it can be installed in a single lift instead of two.
It’s also coming in cheaper than single lift R12 HFC blown foam + 2×4/R13 studwall to hit a similar performance point due to the lower cost of the studwall:
After the foam is installed they’re putting in a 1-5/8″ deep steel studwall completely to the interior side of the foam onto which the wallboard will hang, an inch of EPS under the steel bottom channel plate to avoid summertime condensation on the steel that could otherwise happen if in direct contact with the cool slab. The cost of the skinny steel studs is comparable to 2x4s, but the labor cost is quite a bit less, since the studs can be cut a bit short all at once, letting the depth of the top & bottom channels take up the variation in height over the length of a wall, whereas a wood studded wall would have to be cut separately and shimmed a bit. Steel studs are also be quite a bit straighter, for a flatter overall wall. I’m liking that approach!
The whole project, (including new windows etc) is coming in under $10K- definitely not cheap. He’s been using it as a rehearsal/jamming space with his jazz musician buddies, and since the rest of the house is being heated with mini-splits it’s been getting pretty cool down there during the winter (too cool for jazz? 🙂 ). I expect the overall air tightness of the house will be much improved too, but there are no plans for running before & after blower door tests. There is currently no plan for actively heating the space either, but that may change after it becomes semi-finished conditioned space.
GBA Detail Library
A collection of one thousand construction details organized by climate and house part
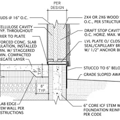
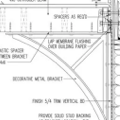
Replies
Dana,
Thanks for the cost information -- always good to share.
Good info, Dana. For situations where foam is the only good option, I've been spec'ing HFO-blown for a couple of years now, but as a designer I'm not often privy to the actual quotes or what product gets installed. I did hear directly from one insulator that he is now only using HFO-blown, and that he is keeping his pricing the same as for conventional foam; the material costs more, but installation is easier. In fact he thought he would make more money on some jobs with HFO-blown foam.
That seemed to be the feedback from this installer- the ease of installation and not having to wait between lifts is a cost saver, particularly on bigger jobs than this, at deeper thicknesses.
From the same installer quote for just 2" of HFO blown foam instead of 3" barely moved the needle, less than a 20% on the quoted price at a 33% reduction in material. He claimed it was about the set up and break down cost being the same. With only 2" it would have required batts in the studwall to make code-min.