Need to correct moisture/mold problem on cathedral roof

Have a room over garage center with closets on both sides between the closet kneewalls and the eaves. Insulation over the room section is 6 inches of foam slabs sealed by “Great Stuff” spray-in foam. Above this ceiling foam and under the roof plywood, there are 1 inch x 20.5 inch unobstructed foam encased ducts between the rafters for venting to the roof peak vent. The side sections outside the knee walls are insulated with rolled fiberglass fiber with durovent ducts above the insulation. There are substantial soffit vents at the bases of the durovent ducts. After a new roof was installed, the fiberglass started to absorb substantial moisture and mold appeared on the plywood as shown in the picture. This only happened on the north side of the garage, none on the south side. Since the plywood must now be removed, I am thinking of increasing the duct heights by raising the roof to give 2 ” ducts rather than the 1″. Also I would add a mid-roof SmartVent to increase airflow. In addition I would increase the peak vent height from a Coravent 300 to CoraVent 600 to double the outlet area. Does this look like a reasonable fix?
GBA Detail Library
A collection of one thousand construction details organized by climate and house part
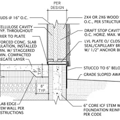
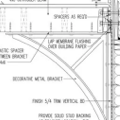
Replies
George,
Your terminology is confusing. It sounds as if:
1. You used the cut-and-cobble approach to insulate your sloped roof assemblies. (For more on cut-and-cobble, see Cut-and-Cobble Insulation.)
2. You have some kneewalls, and you have insulated the kneewalls so that the triangular attics behind the kneewalls are outside of the home's conditioned envelope.
3. You have an attic above the flat ceiling in the center your bonus room, and you were in this attic when you took the photo you shared.
4. Your problem is that you have moisture accumulation and mold on the roof sheathing on the north side of the building.
Assuming that I have understood the situation correctly, we need to determine the source of the moisture. In most cases like yours, the source of the moisture is interior air that escapes through leaks your floors, walls, or ceiling. When this hot interior air contacts the cold roof sheathing, you get condensation. On the south side of your roof, the sun dries out the roof sheathing. On the north side of the roof, the sheathing never dries out.
There are many opportunities for air leaks in this type of building. Did you remember to include blocking under the bottom plates of your kneewalls? This blocking (which must be air sealed at the perimeter of each piece of blocking) is required to prevent air leaks. Similar blocking is necessary between the rafters above the kneewall top plates.
The solution is to track down the defects in your air barrier and seal your leaks. For more information, see this article: “Two Ways to Insulate Attic Kneewalls.”
moist air is the problem to be stopped.
The sheathing is fine, keep it, the mold can be cleaned up.
The mold needs moisture to be active, stop the moisture, clean up the mold and treat the plywood.
1. I used the cut and cobble method to insulate the ceiling of the room, consisting of 3 layers of 2 INCH Owens corning FOAMULAR. The edges were sealed with by "Great Stuff" spray-in foam. Above this ceiling foam and under the roof plywood, there are 1 inch x 20.5 inch unobstructed foam encased ducts between the rafters for venting to the roof peak vent.
2 The vertical knee walls were insulated with rolled fiberglass batts with the vapor barrier on the inside facing the wallboard. The triangular prism-shaped sections were outside the room-insulated envelope. The one door into this space that is a 4 inches. The layout is shown in the attached drawing. The prior picture sent (also attached) was taken from inside the triangular prism side area looking upward toward the knee wall and end of the triple layer foam ceiling, showing a 1” ceiling vent duct.
3. There is no attic space above the bonus room ceiling
4. The knee walls are framed by 2x6s sitting on the plywood floor of the bonus room and insulated with 6” fiberglass with the vapor barrier inward.
5. the air vent is continuous from the soffit vents to the baffles over the side areas to the vent over the FOAMULAR above the bonus room and to the ridge vent.
6. A fix I have considered is to double the vent area by raising the roof 1” and adding a mid-roof vent to feed in more vent air .
0. response with attachments added
1. I used the cut and cobble method to insulate the ceiling of the room, consisting of 3 layers of 2 INCH Owens corning FOAMULAR. The edges were sealed with by "Great Stuff" spray-in foam. Above this ceiling foam and under the roof plywood, there are 1 inch x 20.5 inch unobstructed foam encased ducts between the rafters for venting to the roof peak vent.
2 The vertical knee walls were insulated with rolled fiberglass batts with the vapor barrier on the inside facing the wallboard. The triangular prism-shaped sections were outside the room-insulated envelope. The one door into this space that is a 4 inches. The layout is shown in the attached drawing. The prior picture sent (also attached) was taken from inside the triangular prism side area looking upward toward the knee wall and end of the triple layer foam ceiling, showing a 1” ceiling vent duct.
3. There is no attic space above the bonus room ceiling
4. The knee walls are framed by 2x6s sitting on the plywood floor of the bonus room and insulated with 6” fiberglass with the vapor barrier inward.
5. the air vent is continuous from the soffit vents to the baffles over the side areas to the vent over the FOAMULAR above the bonus room and to the ridge vent.
6. A fix I have considered is to double the vent area by raising the roof 1” and adding a mid-roof vent to feed in more vent air .
In addition to the increased roof vent from 1" to 2", I would use a larger capacity ridge vent like the Cor-A-Vent 600
I'm confused by the diagram. It seems to show something quite different from the description.
I'm also confused by "The one door into this space that is a 4 inches"
Martin's kneewall article has an excellent figure titled "keep the attic outside" . Key details you might be missing include the blocking under the kneewall and the air barrier on the attic side of the kneewall insulation. There might also be air leaks in the ceiling below the attic space.
I added an end view of the over-garage spaces. The door is in the kneewall of the center closet to provide access to the side closet. The mold is on the upper areas of the roof deck plywood, on the underside o the plywood . The overhead of the center closet was well sealed with"Great Stuff" foam when it was installed.
George,
The sketch is helpful, but it still doesn't show whether you have proper air barriers. Air could still be leaking through these insulated walls and floors.
Is the garage heated?
Garage is unheated, but remains above freezing due to heat transfer from the attached house. So the garage is probably not a big source of moist air.
The only vapor barrier between the center closet and side closets is the Kraft paper facing on the fiberglass batt insulation, which is not nearly airtight. There is some masonite facing on the outside of the kneewall to protect the batt insulation. Perhaps it would help to sheath the entire outboard side of the kneewall with a plastic sheet. Since the mold is mostly adjacent to and above the kneewall, that could be an indication that moisture escaping through the kneewall could be the water source
Thank you for all your insight into our moisture issues
Having thought it over further, it seems like moist air through the kneewall could be the badboy here. Since there is a roof ridge vent and since the inside air with hot air heating is usually higher pressure than the outside air, the ridge vent (at even lower pressure because it’s higher) could actually be sucking the moist air through the kneewall and up into the 1" roof vent space. All of the mold is on the higher portion of the plywood roof decking, i.e., toward the center of the over-garage room space and even under the duct atop the sealed Foamular ceiling.
Given that this assessment is valid, a solution would be to replace the fiberglass batt insulation in the knee walls with 6” of pumped-in closed cell foam insulation to seal the kneewalls. The higher R value would also improve the heat loss from the center closet into the sides.
I thought of wrapping the outside of the kneewall with plastic (since the inside is inaccessible), but this would probably lead to condensation of water on the cold plastic wrapper and create another big water problem
George,
If you want to insulate your kneewalls with fiberglass, it is certainly true that you would need an air barrier on both sides of the wall.
It is also true that polyethylene would be a terrible choice for your air barrier on the exterior side of the kneewalls. Almost any other material would be better -- housewrap, OSB, or rigid foam with taped seams. The polyethylene would get damp in the winter.
Your sketch shows that you made a half-hearted attempt to insulate the sloped roof assembly all the way down to the soffit. That is the correct approach -- much better than your idea of insulating the kneewalls.
Whatever you do, do it right. If you want to insulate the sloped roof assembly down to the soffit, make sure that the roof is insulated to minimum code requirements. (We still don't know your climate zone or location, unless I missed it.) That means R-38 or R-49 insulation, depending on your location.
If you want to insulate your kneewall, do it right. Spray foam insulation is one option that solves the air leakage problem through the wall. But this approach isn't complete unless you are willing to install blocking between the joists under the kneewall bottom plate, and blocking between the rafters above the kneewall top plate, as explaining in my article, “Two Ways to Insulate Attic Kneewalls.”
First off. I am in Maryland, outside D.C, in the mid-Atlantic zone.
The over-garage space consists of 3 separate areas. The core center section is a clothes closet kept at house temperature. The triangular spaces on the north side (over the garage) and the south side(over the house) are just for dead storage. These aren’t heated except for the heat that is conducted in from the adjoining center closet and from the unheated, (but warmer than outside) garage below the north space and house areas below the south space. The floors of the triangular spaces are insulated, with the north (over the garage) having 4-6 “ fiberglass and the south (over the house) having 8 “ fiberglass. The overhead surfaces of these side spaces are insulated with 3.5 inches of fiberglass between the 2x4 rafters. The intent of the overhead insulation is to keep these triangular spaces somewhat warmer than the outside and thus reduce heat conducted out of the center clothes closet section . This has worked well thermally, as the clothes closet doesn’t even have to be heated in the winter, with enough heat coming in through the door.
The floor of the center closet space is insulated with 8 inches of fiberglass. Both the 7 inch thick kneewalls have fiberglass insulation used to minimize the heat transfer out of the center closet space into the side spaces. It appears that moisture is probably getting into the side spaces through this insulation and the ½ inch inner wallboard. In cold weather this warm moisture would rise upward by convection plus the slightly lower ambient pressure at the ridge vent. It would then be condensed on the underside of the roof plywood. Note that the mold is only at the upper portions of the roof plywood, with none down toward the eaves.
To eliminate this moisture source, I proposed the replacement of the kneewall fiberglass with 7-8 inches of spray-in polyurethane foam between the studs (at 24” centers) and possibly also over the studs. As you pointed out, spray-in polyurethane should also be added below the kneewall between the floor joists to seal off this potential moisture passageway. The space above the kneewall between the 2x8 rafters (and above the center clothes closet) is already filed by the 3 x 2” (6” OA) pink polyurethane foam sheets, with all gaps sealed with “Great Stuff” polyurethane foam. This foam can be seen at the bottom of the original picture that I sent (note that the picture is taken looking upward from the eaves toward the roof ridge) . (It also shows the 1” x 20.5” vent duct going to the roof ridge over the center closet.)
13. I am in Maryland, outside D.C, which looks like Zone 4.
The room where the problem exists is over the garage space and consists of 3 separate areas. The core center section is a clothes closet kept at house temperature. The center section is insulated overhead, under the roof, with 6” of polyurethane slabs sealed with foam polyurethane between 2x8 rafters The center section kneewalls have 7” of fiberglass insulation, outside of the ½” drywall. The center section floor is insulated with 8 inches of fiberglass.
The triangular spaces on the north side (over the garage) and the south side(over the house) aren’t heated. The north space, over the garage, is insulated on the floor with 4-6 “ fiberglass. It is insulated at the roof with 3.5” fiberglass between the 2x4 rafters, with a vent duct between the insulation and the roof plywood. The south space, over the house interior, is insulated on the floor with 8“ fiberglass. It is insulated at the roof with 3.5” fiberglass between the 2x4 rafters, with a vent duct between the insulation and the roof plywood.
It appears that moisture is probably getting into the side spaces through the kneewall insulation. In cold weather this warm moisture would rise upward by convection plus suction from the slightly lower ambient pressure at the ridge vent. It is then condensed on the underside of the roof plywood. The mold in the picture is only at the upper portions of the roof plywood, with none down toward the eaves. There is only mold on the north side section, none on the south.
To eliminate this moisture source, I can replace kneewall fiberglass with 7-8 inches of spray-in polyurethane foam between the studs (at 24” centers) and possibly over the studs. Spray-in polyurethane would also be added below the kneewall between the floor joists to seal off this moisture passageway. The space above the kneewall between the 2x8 rafters (and above the center clothes closet) is already filed by the 6” polyurethane foam sheets, with gaps sealed with polyurethane foam. This can be seen at the bottom of the picture which was taken looking upward from the eaves toward the roof ridge. (It also shows the 1” x 20.5” vent duct going to the roof ridge over the center closet.)