Unvented slanted roof with radiant cooling and NO polyurethane in 4C

We are in Everett WA, north of Seattle, right on the coast, zone 4C. I hope that our location will save us…
We have a low sloping steel, west facing roof. Double, 30 weight felt paper underneath to dampen rain noise. I presume 1/2″ plywood sheathing. 2×12″ rafters, 11″ true depth.
We will install WarmBoard R (13/16″ thick OSB with aluminum tracks) underneath the rafters for summer cooling and supplemental heating in winter.
The Alu WarmBoard panels will form an interior vapor barrier. We also will want to put 4″ by 2″ deep, flush mounted LED ceiling lights in. These will only enter the insulation by 3/4″ as the drywall is 1/2″ plus the WarmBoardR is 13/16″. The electrical boxes are 4″ x 2″.
The low slope makes ventilating the roof difficult. 2″ won’t cut it as a vent space on this low sloping roof. With 6″ we loose too much R value in insulation loss. We cannot bring the ceiling lower on the interior.
The steel roof is recently newly installed so do not want to remove that for exterior insulation which would also be difficult to match the other roof, which is cedar shakes.
Want to stay away from Polyurethane foam. Because of the adjacent, east facing, cedar shakes plus general dislike of the stuff. Preferring RockWool insulation.
11″ of RockWool, with interior vapor barrier plus an almost other vapor barrier on the outside, the steel roof with double felt paper. IS this outside roof assembly vapor open enough to put the WarmBoard panels in on the inside, with recessed LED lights and R44 insulation. We can acoustic caulk all we can on top of that to make sure all is as air tight as possible from the inside.
Also considering Aerogel strips on the rafters before the WarmBoard goes up to create a thermal break of R13 on the rafters by only loosing 1/4″. When we do ALL that, CAN we do this?
Thanks
Jan
GBA Detail Library
A collection of one thousand construction details organized by climate and house part
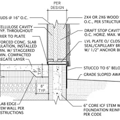
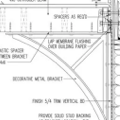
Replies
Jan,
If you want an unvented roof, you can't use an air-permeable insulation like mineral wool. Mineral wool will only work if you have a ventilation channel above the insulation.
If you want an unvented roof, you need to install spray polyurethane foam.
In any case, R-44 is a very optimistic R-value for 11 inches of mineral wool. I would guess that R-41 is more realistic.
For more information on insulated sloped roof assemblies, see How to Build an Insulated Cathedral Ceiling.
Thanks Martin,
There is absolutely no way to get around Polyurethane spray foam for this setup? What my thoughts are on this is: sure we get an air and vapor barrier all in one plus high R value, well, touch higher over mineral wool. BUT.. what about the rafters. These rafters are permeable, to a degree. Less over mineral wool, sure. But we put plastic blocks in between wood boxes. Don't we over emphasize on the good of the plastic foam but neglect to see where we put it: in between wood boxes? If the roof would become one solid SIP panel, yes, than I would see the merits of foam. But intersecting it with wood thermal and moist conductors, I fear that it greatly counters the benefits. When having to live with the wood rafters is there nothing to say for continuing the vapor permeability through the mineral wool and the roof sheathing.
BUT we must have that breathability through the steel roof's seams as well. EVEN with foam. The rafters... what about the rafters?? That is my struggle. The wood gives before the plastic will ever do. Won't the plastic HINDER any beneficial vapor movement. Remember we will warm (supplementally) the roof in winter. And cool in summer. But we live in a heating climate. WHEN that steel roof has SOME permeability won't our radiant heated ceiling be our safeguard in this case? And mineral wool, not cellulose...
Foam in wood boxes is not great. Why having to live then with the foam's other bad characteristics? R value is really that much better over mineral wool when all is said and done?
Thanks Martin, I really need good help with this!
Jan
Jan,
I agree with you that it rarely makes sense to install spray foam between rafters. The best place to put foam insulation is above your roof sheathing. If you can remove your steel roofing, and install a thick layer (or several layers) of rigid foam above the existing roof sheathing, followed by a second layer of roof sheathing or purlins, and then re-install the roofing, you will have a much better roof assembly than if you install spray foam between the rafters.
The fact is that your proposed unvented roof assembly violates the building code. If you read the article I linked to, the code requirements for insulated sloped roof assemblies are explained.
Well the roof was a fiberglass batt insulation, unvented. So not code compliant...
Or is it, when done right: "Can I build an unvented roof assembly? In recent years, most building codes have begun to allow the construction of unvented insulated sloped roof assemblies. - See more at: https://www.greenbuildingadvisor.com/blogs/dept/musings/how-build-insulated-cathedral-ceiling#sthash.qYHre7ZL.dpuf"
What I understand from reading up on GBA is that our low slope makes venting impossible/useless, unless we create a big 6" gap.
Adding insulation to the outside is impossible. The ridgeline meeting the east facing cedar shake roof will create a funky house.
So we are hitting the impossible point... (Unless you see an option here?)
Have to restudy your given link BUT is it allowed by code to have mechanical ventilation at all? As our low slope will not create sufficient stack effect for a 2" gap to work... What if I create a 1" forced air channel? (I dislike loosing any inch in insulation.) Put a fan on the bottom to force air in and through? Never pull at the top as one would pull on the interior air through cracks. Allowed and would it work? As it would be a lot of fiddling!
Again staying away from closed cell foam? Use a layer of denser ComfortBoardIS that one can custom line on one side with housewrap before placing it? And adding ComfortBatt. My R value still good?
Curious to see what trouble you see with this thinking.
Thanks Martin,
Jan
Accidental double post.. SORRY...
Jan,
There are two solutions. You just don't like them.
Solution 1 is to install closed-cell spray polyurethane foam between the rafters.
Solution 2 is to install an adequate thickness of rigid foam above the existing roof sheathing.
Your solution is still a violation of the building code. I don't recommend it.
Solution 3 is would be in the grey area of the code: Using a smart vapor retarder on the interior side of the assembly, detailed as an air barrier. This definitely works in zone 4C.
http://www.energy.wsu.edu/documents/AHT_ComparingTheMoisturePerformance%20Of%20Wood%20Framed%20Wall%20Systems.pdf
(^^This test facility is in Puyallup^^)
The moisture drives on wall # 2 (unvented stucco on an OSB sheathed wall, with R21 cavity fill and MemBrain as the interior side vapor retarder) will far exceed anything you would end up with in your roof assembly (barring a bulk-water leak, that is.) It was kind of marginal in that foggy-dew rain-belt location, but the OSB still stayed dry enough (if barely), despite the very significant exterior moisture drives in combination with the wintertime interior moisture drive. You roof won't have the exterior drying capacity of that wall, but it also won't be saturated the way a stucco wall would be.
As long as you kept the interior RH below 40% in winter you'll be fine.
With MemBrain as the interior vapor retarder & air barrier, using cellulose instead of rock wool would give you more margin, since the cellulose shares the load with the wood, keeping the peak moisture loading of the wood lower than it otherwise be.
But you can't use low-permeance stuff like Alu Warm Board for the ceiling radiant or you'll create a moisture trap. You can get there with extruded or sheet metal heat spreaders covering up to 65-70% of the total ceiling surface and still have plenty of drying capacity though
Thanks Martin,
Foam is great when you take it away it's flammability and it's toxicity... And therefor yes, I don't like it. Having it in the roof: during a fire it will drip into the house and will create serious problems for firefighters to save the house and themselves. That all goes away with mineral wool. Not a small point.
Your solution 1 remains a code violation as well I understand? Still no venting in there. Only with added insulation above the sheathing we can create a code compliant unvented roof, right?
So mechanical ventilation is out and also Solution 1.
Now we are getting stuck when not being able to take the metal roof of, but we must.
How?
Don't forget that we have our internal vapor barrier. So now when we put a solid exterior vapor barrier on the outside as well. Not a leaky metal roof but sealed vapor barrier. More R value, but also more second vapor barrier. Isn't the second vapor barrier what we do not want. It may not be code compliant, but the fact that we have our alu panel vapor barrier on the inside makes it a bit more complicated by now applying the "normal" unvented roof approach. And maybe not the right way to go?
That is where I was hoping that our climate plus the not vapor tight metal roof will give us the edge we need to built a maybe non code compliant roof, BUT one that would work still.
Just max the R value, aerogel on the rafters and invest in it that way.
Two vapor barriers will let mother nature win? And rot the roof...
Thanks again,
Jan
Jan,
Once again, I strongly urge you to read my article, How to Build an Insulated Cathedral Ceiling. The article will answer many of your questions; reading the article will prevent you from having to post questions here that are answered in the article.
In your most recent post, you wrote, "Your solution 1 remains a code violation as well." You're wrong. As my article explains, the building code provides details for both unvented and vented roof assemblies.
Reply to Dana:
What I take away from your input... No WarmBoard on the inside allowed... It is not low permeance, but vapor TIGHT, alu sheeting... But your thinking of 65-70% coverage with "spreaders", alu fins I suppose...
Cooling needs more surface area for it to work over heating. So these WarmBoardR panels come in 2'x4' size. To create drying to the interior potential: what if we instead of installing the panels tightly against eachother and acoustic sealant in between them to seal it all vapor tight, leave space in between them. The installation won't be much of a problem when we leave gaps. The PAP lines can jump over. Rafters, smart vapor retarder, Warmboard panels, drywall. OR WarmBoard panels, Smart vapor retarder, drywall...
Thanks
Jan
Reply to Martin,
The problem with the explanation in the article is that the rafters are ignored. I remember an article Joseph Lstiburek wrote on this topic and he concluded also that the rafters remained an unsolvable problem with spray foam between the rafters. When one can flash and batt, why not just batt... As moisture can travel around the foam to the rafters. Slower but still: the foam does not seal all. That is my thinking at the beginning of this post: are the big downsides of foam worth the benefits. As in: are they real benefits. Claims of total sealing are more like, it seals a bit better as the road to the rafters remains WIDE open. Pour gold in between the space: it is still an open conduction path for vapors.
It is one of those things that code may say: FINE when using closed cell. Fine, really? What do you think of Dana's thought and my added thought to that: space the WarmBoard panels to allow drying inward. Dehumidification is now paramount. Which it is anyway once one starts to cool. But is it like the steel roof: insufficient drying capacity? But maybe the best solution give the parameters. And location...
Good talking with you both!
Jan
Jan,
Polyurethane is NOT a fire hazard. You have your facts wrong. Polystyrene will melt and can drip from the ceiling but polyurethane is just the opposite. It doesn't melt and it takes 700F for it to even char. It is a CLASS A roofing material and is used in commercial buildings all over the world.
Martin laid out the options pretty well. If you don't like the options I would recommend changing your design from rafters to SIPs, polyurethane SIPs to be exact. If you don't like that, I recommend redesigning your home's roof area to something different. Just go flat roof with trusses, cellulose at the ceiling level and call it a day.
Doesn't make sense trying to put a square peg into a round opening.
Thanks Peter,
Surprise to hear that polyurethane is not "at all" a fire hazard. 700F and not charring is irrelevant info in this regard. What happens when polyurethane is exposed to flames? THAT is relevant info. And compare that to say mineral wool??
What about the off gassing. Homeowners cannot be onsite for a minimum of 24 hrs. Fiberglass is also used everywhere. Does not mean it is good material... Not at all convinced that polyurethane is the be all and end all for a roof. WHAT ABOUT THE RAFTERS. Everybody ignores this. Except Lstiburek. Who was honest about it and at least pointed this out as being a problem. That polyurethane does not help with between the rafters AT ALL.. That is my point.
Dana's documentation is interesting. And his comments. Drying to the inside. As when putting foam on the outside, say I could do this: that would also mean that my WarmBoard panels on the inside create the second, unwanted, vapor barrier. So in the end I think the best and easiest is to cut the 2' x 4' WarmBoard panels in half creating 2' x 2' panels. Spacing those on the ceiling to create any vapor openings that I can without compromising the cooling. Smart Vapor retarder over top of that. And drywall.
The other option is unfeasible. And when not that, hugely expensive. BIG question I have whether Martin's solution IS the only and best solution in this regard. I fear Dana's input was priceless.
Jan
Jan,
I can assure you that my article does not ignore the problem of thermal bridging through the rafters. I wrote, "In addition to improving the R-value of the roof assembly, a layer of rigid foam has another benefit: it interrupts thermal bridging through the rafters."
Thanks Martin,
Yes of course it does that. But what about the problem of a double vapor barrier in my setup. That changes everything. Plus the impossibility of executing your solution on this roof. What is your opinion on Dana's suggestion. And my suggestion of creating "all I can" drying to the inside. As with ANY outside install of any foam in a heating climate: one goes against the "rule" of drying to the outside.
Another question I have is: how vapor tight can I consider my steel roof to be? Or IS there some vapor openness? Any point in sealing the rafters and sheathing connections with acoustic caulk to make it air tight and can I still count on vapor diffusion happening at all?
I'll be gone for a while soon so don't think I have lost interest!!
Thanks TRULY for all of you in contributing.
Jan
Jan,
Q. "But what about the problem of a double vapor barrier in my setup?"
A. You need to choose either a vented roof assembly or an unvented roof assembly. If you choose a vented roof assembly (with a ventilation gap between the top of your insulation and the underside of your roof sheathing), the interior vapor barrier will probably work. If you choose an unvented roof assembly, the building code requires (and most experts recommend) that you install either spray polyurethane foam between your rafters or rigid foam above your roof sheathing. If you to insulate with spray foam or rigid foam, the interior vapor barrier probably won't be a problem.
Q. "What about the impossibility of executing your solution on this roof?"
A. Nothing is impossible, but you have set some arbitrary restrictions (we cannot bring the ceiling any lower; we cannot remove the roofing; we want to install an interior panel containing radiant tubing and aluminum foil) that have boxed you into a corner. I didn't establish those arbitrary restrictions; you did. The first thing a good designer would do is to choose a roof assembly that works. You haven't done that.
Q. "What is your opinion on Dana's suggestion?"
A. To the best of my knowledge, it violates the building code two different ways: by specifying insulation that doesn't meet minimum R-value requirements, and by using an air-permeable insulation without a ventilation channel on the exterior side of the insulation. But it would probably work, at some risk of the development of damp roof sheathing, and with the downside of higher-than-usual heat flow through the assembly.
Q. "What about my suggestion of creating 'all I can' drying to the inside?"
A. Any attempt to develop your own roof assembly in violation of the code and known building science principles is risky -- but it's your house.
Q. "How vapor tight can I consider my steel roof to be?"
A. Steel roofing is a vapor barrier. Some types of steel roofing (through-fastened corrugated steel panels, for example) allow for air movement, while other types of steel roofing (standing-seam roofing) are fairly airtight.
Q. " Any point in sealing the rafters and sheathing connections with acoustic caulk to make it airtight and can I still count on vapor diffusion happening at all?"
A. Vapor diffusion is a form of vapor movement that is independent of air leakage. There is no vapor diffusion through steel roofing.
The MemBrain approach does not violate the code, it's simply outside of the code. With MemBrain you don't have a class-III vapor retarder- it's Class-II (and becomes class-III only when it needs to be, when moisture needs to get out). The IRC has plenty to say about unvented assemblies with only Class-III vapor retarders on the interior, but does not require roof deck venting when there are class II vapor retarders on the interior- it's simply silent on the subject. Where the code is silent it's technically not a violation- it's up to you and your inspectors/engineers to decide if it's robust enough.
It's true that only 11.25" of cellulose only comes to about R40-42 instead of R49. If this is new construction, it doesn't meet code on labeled R, but it might still meet code if the calculated U-factor ifor the roof assembly is U0.026 or lower, per section N1102.1.3 (R402.1.3)
http://publicecodes.cyberregs.com/icod/irc/2012/icod_irc_2012_11_sec002.htm
With a sufficiently low framing factor you can get there with R40, depending on the R-values of the other layers. (It'll be a squeaker if it makes it though.) If you cut 1.5" of rigid polyiso into 2" wide strips and mounted it to the rafter edges that would give you about 12.75" of cellulose good for R46-47, but since it thermally breaks the rafters with R9ish polyiso you'd have no problem at all doing the limbo under U0.026. You might even get there with just 1" polyiso but that depends on the actual framing fraction when running the calculation.
If you cut up your extremely low permeance warm-board panels with space between them for more drying capacity it has to be done in such a way that EACH rafter bay has an adequate drying path.
Given the very low sensible cooling loads in western WA it's not clear what's so special about taking a radiant cooling approach. With a U0.026 ceiling the ceiling temp doesn't add much to the average radiant temp. With a radiant WALL you would get very nice convective cooling flows, without the vapor barrier headache you would have with an unvented roof.
BTW: Polyurethane SIPs may not be a fire hazard, but the HFC245fa blowing agent in R50 worth of polyurethane is a crime against the planet, since it has a global warming potential of nearly 1000x that of CO2. (And that's not counting the environmental hit of the polymer itself!)
Until the polyurethane SIP manufacturers stipulate that they have switched to water or HFO1234__ variant blowing agents, high-R assemblies insulated primarily with closed cell polyurethane is about the least-green option out there (possibly outdone by high-R assemblies insulated primarily with XPS, which is currently blown with a mostly HFC134a mix, which has a GWP close to 1400x CO2.)
Dana's thinking has given us some options that I need to run by you all, but especially Dana.
Wall radiant is a very good way to heat and cool according to our radiant engineer Rob Brown from Rockport Mechanical in Maine. So, very good you brought that up Dana. However there are also big downsides to it over having the radiant install be on the ceiling.
As Rob Brown pointed out:
-Radiant wall is good for around 20 BTUs/sq ft in cooling mode.
-It's very comfortable in heating or cooling mode. People are very tolerant of temperature asymmetry in the horizontal plane (think super hot wood stove, feels good. Super hot panel over your head, not so good).
-Building in the walls require detailed consideration at the windows and doors that ceiling doesn't.
-Wall panels are susceptible to puncture risks ceilings generally aren't (hanging things, etc).
-Wall panels are susceptible to furniture blockage that ceilings generally aren't. Covering more area is a way to get around this.
-Walls are a more complicated install because of features you have to work around that you don't in ceilings.
For that reason usually the bottom 5 feet of a wall is the best location for wall radiant according to Rob.
Now for our upstairs it gets very complicated to achieve the wall surface needed with all the restrictions as Rob mentioned. Only the hallway would have wall surface area available. And that would also mean a more complex install regardless.
So back to the ceiling option.
Rob mentioned that a 25% loss of surface area on the ceiling would be acceptable to keep the cooling working properly.
What if we cut the WarmBoard in half, turning it into 1' x 4' panels. Now we have two options to install these on the ceiling with the 16" on center rafters. Attach the WarmBoard to the rafter, or hang the WarmBoard between the rafter.
Attaching the 12" wide WarmBoard to the rafter we bring the PAP tube channel to the rafter. Which is not the best way to distribute the heat. Even though the alu does the main heat distribution to the inside of the room. Also with attaching it to the rafter we block the main vapor route with the WarmBoard. Only positive of this install is that we get a 4" gap between the WarmBoard panels, between the rafters. Yes, only 4". Is that enough?
Other option, hanging the WarmBoard panel between the rafter, attached to 2" x 2" strips? That way we keep the rafters free to vent to the inside with now only 1 1/4" space on either side of the rafter. With this option we get the venting at the location where we want it most. But we go from 4" to 2 1/2" (2 x 1 1/4").
Is either option viable?
Dana's insulation suggestion of Cellulose is a bit of a surprise. Your logic for this is to "share the load" as it will buffer the moisture by slow absorption and slow release. But this being a roof, isn't the big nono for cellulose under the roof the fact that it does absorb water. So when getting a leak, first of all, you'd never know it as the sponge working of cellulose will keep you happy and dry for a long time and thus will rot your roof away without you ever knowing it.
With mineral wool water does not get absorbed so big plus is that it will start dripping through your drywall ceiling quicker, plus it dries out quicker.
Headache either way when you get a roof leak but mega disaster with cellulose.
Thanks again everybody!
Jan
As I apparently do not need to worry about any smart vapor retarder for our climate, I will desperately need one in the ceiling as Dana brought up. 1/4" plywood between the WarmBoard as good as, better than MemBrain or IntelloPlus?
Since you care about thermal bridging of the rafters, your only options to mitigate that are to apply rigid insulation boards above or below them. Since you don't want to put them above since that would entail removing and re-doing the roofing, your only option is to put them below. If you need to do that anyway, then you don't actually need to use foam; you can do the whole shebang with mineral wool; how about this:
1. Fill the rafter spaces with 7 1/4" mineral wool batts, leaving a 4" ventilation gap on top. R-value: R-26 or so, taking the thermal bridging of the rafters into consideration
2. Fasten 6" of rigid mineral wool boards to the underside of the rafters. R-value: R-25
3. Cover the mineral wool with airtight drywall to serve as an air barrier
This gives you a vented, airtight, properly-insulated cathedral ceiling with a total R-value of 51. If losing 6" of ceiling height is too much, you could reduce the size of the vent channel and add an additional 2" to the batts between the rafters and then reduce the thickness of the rigid mineral wool to 4". This would reduce the total to R-49. In the end you will probably barely notice the loss of four inches of ceiling height if this is conditioned space.
Copying Dana's answer relating to this in here to keep it where all can benefit and think along...
Dana Dorsett:
Quarter inch plywood never becomes a class-II vapor retarder (at any moisture level), though half-inch goods can when bone-dry. Quarter inch plywood never becomes as vapor-open as MemBrain, but if you're using latex paint as the interior finish the latex becomes the limiting factor on drying rates, even in a MemBrain protected structure. While the MemBrain will be over 10 perms when there is a lot of moisture in the cavity, if there is 5 perm paint between the MemBrain & conditioned space it hardly matters. It takes a higher moisture content than MemBrain before the plywood goes north of 5 perms, but it will. It's "good enough", as long as it's air-tight. But it's a heluva lot easier to make wide long sheets of MemBrain truly air tight than air sealing a bunch of 1/4" plywood edge-butted to WarmBoard (or even as a tiled-in complete layer of 1/4" plywood above the WarmBoard.) MemBrain is quite a bit cheaper per square foot than 1/4" plywood too. (About $100 for an 800 square foot roll when purchase in small quantities through retailers.)
Moisture drives affecting framing cavities in zone 4C are primarily from the exterior. As long as you have a rainscreen gap between the siding & sheathing as a capillary break & drying path you don't really need (or want) an interior side vapor barrier tighter than 5 perms- but you DO want to make it air tight on both the exterior sheathing & interior side. Caulking 1/4" plywood to the framing on the interior would work, but don't glue it without factoring it into the seismic engineering plan. The stiffer the walls, the more force will be delivered to the foundation anchors.
- See more at: https://www.greenbuildingadvisor.com/community/forum/general-questions/40070/interior-plywood-earthquake-areas-can-it-replace-vapor-retar#sthash.4JzSm4sh.dpuf
Thanks Dana. Received another thought on this just now, so when possible reply/read on at the original thread to keep it all in one place.
https://www.greenbuildingadvisor.com/community/forum/gba-pro-help/39891/unvented-slanted-roof-radiant-cooling-and-no-polyurethane-4c#comment-85016'
To Nathaniel G
Thanks for the thoughts.. Yes thermal bridging is a good thing as our radiant engineer always comments on that. We cannot go under, nor can we go up... SOooo we have to go under..... It is tough. But we have no choice but to lower the ceiling and add insulation. Martin knocks the R value of the Roxul ComfortBatts. BUT Dana has no problem calling Polyiso under the roof sheathing R9. Our radiant engineer educated me on the true R value of Polyiso... PLUS that it even looses R value when it gets cold: WHEN YOU NEED IT... It appears to be only good for hot climates to be used under the roof with an airspace.
Now back to the topic at hand... Yes, the whole shebang with mineral wool! I like that!
But what when I can only do that by filling the rafters with 2 x R23 ComfortBatt plus 1" underneath the rafters with Comfortboard IS. 46 plus 4 would make R50.
NO ventilation.... That is the point now.
When installing the WarmBoard panels not parallel with the rafters but again as was originally designed perpendicular. Makes install easier PLUS leaves all these need 2 x 2 cross members for attaching the WarmBoard out of the needed insulation space between the rafters.
Again, 1 ft WarmBoard panels with 4" gaps in between. MemBrain either uninterrupted over the entire ceiling or only over the 4" gaps. Drywall after that.
BUT one room under this slanted steel roof is a bathroom.... So the paint on that ceiling will negate the Membrain function???
From Dana I understand that ANY smart vapor retarder becomes kinda moot when it is behind drywall??
You are seriously overcomplicating this. You've gotten a couple of ideas that will work. Martin's right: you just don't like them. You can bite the bullet and go with one of these ideas, or you can roll the dice and go with something that's riskier from a building science perspective. It's your house.
Thanks Nathaniel,
but I am not overcomplicating this just for the fun of it. So foam is the way to go. So now we lock the rafters that are permeable in between two vapor barriers and call it good?
And foam is better in case of fire? Foam is easy to get a perfect install, having the mixing of chemicals in the yard and cannot be in the house for 24 hrs, offgassing no big deal? All these topics I am listing are health related. You can say that I am overcomplicating this but these things way heavily on lots of peoples' minds. And I think for a very good reason. Foam I do not see to do anything else but giving me more R value. Does not help at all with the double vapor barrier issue. Small gain for adding serious negatives. That's where I am coming from.
I am looking at Spaceloft insulation. Polyiso is also misleading to use. 2" vent does not work. 6" is what Lstiburek says is the only space that will work on this roof. You say 4"? What are your credentials if I may ask? It is very slanted... It is all not easy. Not overthinking it for fun.
If you want a 6" ventilation gap, that means 5" of mineral wool between the rafters and 7 inches of rigid mineral wool will be required below them to reach a total of R-49.
You don't need to use foam if you don't want to. If you want to use all mineral wool, you just have to live with one of the following:
1. A several-inch lowering of the drywalled ceiling height to accommodate a few inches (4-7, depending on how big you want the ventilation gap to be) of rigid mineral wool boards to thermally break the rafters
2. A lower-than-R-49 level of insulation in your ceiling
Pick your poison or acquiesce to foam. In retrofit situations, the perfect option is rarely available unless your budget is unlimited. Sometimes you have to compromise on something. Since you don't want to remove the roofing or use any foam anywhere, your options are more limited.
As for my credentials, I have none. Assume I am a deranged lunatic who is out to wreck your house. For that matter, assume that of everyone. Trust nobody but yourself, and only hire out work that you would be able to do yourself--otherwise how are you supposed to figure out if they're doing it properly?
First four INCH gaps between 2 FOOT panels isn't a sufficient percentage of the area for a decent drying path even at 10 perms.
Smart vapor retarders are still important to use under painted drywall when the exterior side is vapor impermeable, even though the paint ends up 3-5 perms, limiting the drying rate. With a smart vapor retarder the moisture accumulation rate during cold weather (when the average temp at the roof deck is below the dew point temp of the interior air, lowering the vapor permeance of the MemBrain) will be only a fraction of the rate that it can leave (when the roof deck warms up and releases it's moisture, raising the permeance of the MemBrain.) A steady 3-5-perm interior with only latex paint as the vapor retarder is fine in a 4C climate if the roof (or wall) is fully vented, but with your roof stackup something that 1-perm or less during cold weather but 3-5 perms the rest if the time gives it a lot more resilience.
The cold temperature performance of polyiso in a 4C climate isn't a big hit, even in exterior sheathing applications. In fact, in your climate with say 20-25% of the total R on the exterior the average temp through the polyiso will be near the highest-performance sweet spot, where it outperforms it's labeled value. The performance of polyiso peaks at about R7/inch when the average temp through the foam is about 50-55F, and the average January temp in Everett is about 40F. Even when it's 20F outside and the conditioned interior is 70F, the performance of exterior polyiso is still pretty good- nothing like the hit it takes when it's sub-0F outdoors. And that is when polyiso is on the cold side of the assembly, which is not what we're talking about here.
When the foam is on the interior side the average temp through 1.5" of foam will never drop below 60F without a radiant ceiling, but as the outdoor temp rises, the average temp of the WarmBoard rises, and the average temp through the foam doesn't move much. R9 is about the rated value of the foam at mean temp of 75F through the foam. As that mean temp falls the performance increases, and in an interior rafter-edge application it will always perform at or slightly above it's labeled R-value. (Unless you were expecting outdoor temps of 100 below, and the WarmBoard wasn't keeping up with the heat load?) Seriously, R9 (it's tested-rated R when the warm side is 90F and the cold side of the foam is at 60F) is the low end for 1.5" of polyiso performance in this stackup during cold weather. When it's 20F outside warm side would be up against 90-100F WarmBoard, and the cool side would be up against ~50-60F rafter edge, pretty similar to the mean temperature at which it was tested for labeling. As the temps drop below 20F (below your 99% number) the performance will rise, not fall.
Yeah seen and heard too many dubious things that WE get billed for in the end. But now with the foam, the stakes get raised to a very high level. That stuff is just bad all the way around... SO, my deranged lunatic brother, where have you been all these years?
Dana was giving me hope with a limited vented roof with cellulose. Did you pick up on that? My question is now whether I can do this with mineral wool instead and come down on the ceiling the ONE measly inch. The one measly inch we cannot spare but THAT is our "give" in this. 1" continuous Comfortboard IS on the underside of the rafters. PERPENDICULAR WarmBoard panels with 4 maybe bigger gaps between them for the only vapor diffusion I can give it to dry inward. We intend to supplementally warm the ceiling in winter as well, which should aid greatly with drying out? Dehumidify and cool in summer is where the risks are during the year. I hope that delusional acid trip is paying off in the end?
Your comments are appreciated!
Should not call it limited VENTED roof. As it IS an unvented roof.. Do not want to send your mind in the wrong direction!!
.
(some cross-posting going on here... missed the last 2 posts while composing my response)
Code only requires a 1" ventilation gap, but 1.5-2" is better even for steep pitches. For flat roofs even 5" may not be enough unless there is a venturi-cap type vent stack to guarantee air changes. On the lower angled shed-dormer 2.5-3" would do, as long as there is both soffit & ridge venting (with more soffit vent area than ridge vent area, but plenty of both).
To Dana,
Good to have you back. Your contribution is HIGHLY appreciated! Sorry for the cross posting, but I think I had to pull it back to this post as that way the title would attract people to the corresponding info. The other post would make this info go into Neverland...
Yes the venting gap recommendations brought me to having no choice but create an unvented roof. Unvented now with vapor diffusion inward.
I think/hope that I can get close to R50, if not GET TO R50 with spanning 1" of ComfortBoard IS underneath the rafters. (2 x R23 ComfortBatt in the rafters)
And SKIMPING, yes, I have no choice, skimping on the vapor diffusion inward. 4" bands between the 12" WarmBoard panels. Perpendicular to the rafters. You recommended to stay parallel with the rafters but that complicates the install. The mineral wool is highly permeable so my feeling is that bringing support braces inside the rafter space would be a worse option over having the WarmBoard and spacings for diffusion perpendicular.
Struggling still with the final touch. MemBrain/IntelloPlus over the gaps, then drywall. OR is just drywall enough as I apparently am in no need for any vapor barrier anywhere else in the walls of our house in zone 4C according to Martin. Just focus on airtightness.
Hope to hear your Cellulose preference over Mineral Wool. I would not want cellulose in a roof in case of any leaks. Plus cellulose hides a leak until the rotten roof falls out of the house?
Is this solution I am depicting above my ticket away from foam?
Thanks All!
Jan
Jan, I think you're unduly worried about cellulose in a cathedral roof. The biggest danger of cellulose in a cathedral ceiling is if the slope is too steep and it all follows gravity over time. It's not water absorption. If you have an inundating roof leak the least of your problems is cellulose hiding it. Most leaks aren't inundating and the cellulose will work to spread the moisture throughout that layer. For the average water leak all you really have to worry with cellulose is that you have enough heat build up in the warmer months and a path for that moisture to escape during those warm months. Cellulose generally buys you time, whereas rock wool will just let moisture rot the ceiling drywall, or sheathing, or both.
Here, calculate it out for yourself:
With a 6" ventilation gap and 5" of mineral wool batts between the rafters:
1*4.2 (one inch of R-4.2 mineral wool board under the rafters)
+
5*4.2*0.75 (5 inches of R-4.2 mineral wool batts filling 75% of the space)
+
11*1.2*0.25 (11 inches of R-1.2 rafters filling the remaining 25% of the space)
= R-23.25
As you can see, this is nowhere near R-49. So if you're limited to a) losing a maximum of one inch of ceiling height, b) having a 6" ventilation gap under the sheathing, c) using no foam, and d) having a vented roof, you've run out of variables to tinker with and you'll wind up with an R-23.25 roof. If that's good enough for you and you don't have to meet code or get inspected, then go for it and be happy. Make sure the drywall is airtight and you'll be just fine. If you want more insulation than that or are required to have it by local law, then you'll have to bend somewhere, either by lowering your ceiling if you want to avoid foam no matter what, or putting foam somewhere. It's as simple as that I'm afraid.
As for how big of a ventilation gap you need, I honestly admit I have no idea. If Joe says 6" in a vented roof of the low pitch you have, then 6" it is I suppose.
Finally, putting spray foam under the sheathing shouldn't create a moisture trap, right? Don't you only have roofing felt above the sheathing? That's not a vapor barrier. If the sheathing gets wet for some reason and there's polyurethane spray foam beneath it, it should be able to dry through the roofing felt, or the gaps in it due to the shingle lapping, in the worse case scenario.
Thanks Eric,
Surprised to hear that you say when comparing rockwool to cellulose, with an equal leak problem... that rockwool would let the roof rot sooner over cellulose. My thinking is that rockwool will not hold, absorb the water but will show water rings on your dry wall quicker over cellulose. Rockwool will let you come to a puddle on the floor after a rainstorm whereas cellulose will not and soak it up, vent it out over the summer maybe and when the next winter comes soaks it all up again. Until the leak becomes bigger, and TOO big to do that.
I also prefer rockwool over cellulose as the install I can do myself. Just in the mechanical room with a spagheti of utilities running through the ceiling.... there cellulose is a better candidate probably.
But for it's water characteristics I take Rockwool over cellulose. Wrong thinking? Plus as you say, cellulose can sag over time. Moist blown in cellulose should not have that problem though.
Jan
FWIW, mineral wool is about R-4.2 per inch while cellulose is about R-3.7.
As for roof leaks, you should probably shoot for not having a leaky roof. Given that your roof is new, this seems like a safe assumption for the time being. Assuming you do spring a leak, I guess the question is whether you want an insulation material that will cause it to do less damage but conceal the fact, or one that will make it more obvious faster.
Just to throw a monkey wrench into the equation, if you get cellulose that has ammonium sulfates in it as a fire retardant, if it gets wet, it will become mildly corrosive to metals touching it. You can get borate-only cellulose but it's a bit more expensive.
Cellulose would wick water away from the roof deck, rock wool will not. Cellulose will completely fill the space eliminating convection around the insulation, rock wool requires a LOT of detailing to the installation to be equivalent from that point of view.
Nathaniel is correct that in the event of bulk water incursions from above (something screwy with the membrane lapping AND major leakage in the steel roof seams) you'd find it sooner with rock wool, only because it would be dripping/staining the ceiling. But barring that the assembly is more resilient if cellulose. Borate-only celluose is necessarily more expensive (I've found it cheaper or comparable to the crummy suflated stuff at box stores), but it's worth seeking out. In the event that it ever got wet, the sulfated goods would become corrosive to metals (and it stinks) whereas borate-only not so much.
It's possible to do cellulose in a vented assembly, but it's not as easy as with rock wool. Since rigid rock wool is NOT a vapor-permeable or semi-permeable air barrier, it's best to install an air barrier and snug the batts up against it, tucking in the edges & corners to ensure that there are no convection paths around the batt, then tugging it back out until it's slightly proud of the rafter edges for a compression fit to your interior-side sheet goods. MemBrain still a good idea for the interior side detailed as an air barrier, since the thermal expansion/contraction of WarmBoard makes it a dubious air-barrier over the longer term.
With a vented assembly it's fine to put foil-faced polyiso on the interior as a thermal break + additional R, taping the seams with a quality temperature rated aluminum tape (Nashua 324a is available at most box stores) and caulking/can-foaming the edges to the framing, in which case you can skip the MemBrain.
Just trying to find out whether my thinking is correct in this. When I have leak in the roof, small or large I want to know it asap. Not hiding it in cellulose. Nor pushing it to the wood and sheathing and not dripping it through the drywall that mineral wool could do?
My current thinking is that mineral wool would not absorb it and thus channeling it with gravity to the channel of least resistance. OR would that not happen in reality but the leak will stay on top of the mineral wool pushed against the sheathing as it goes down and soaked up before only major water leaks will present themselves eventually...
Cellulose showing it sooner in that thinking? CODE allows for either? Cellulose I thought was not allowed in a roof. Mineral wool I don't know...
To Dana:
Vented roof assembly will be impossible in my situation. I am forcing an unvented assembly through the eye of a needle. I do not have the depth inside to get the R50 plus a vent channel. It's a slanted roof remember. Would need 6" of channel not 2.
For all clarity.
The focus is on an UNvented roof assembly. 12" rafters, 11" real world depth.
WarmBoard R panels delivering radiant cooling plus supplemental winter heating.
The summer cooling part is the focus I'd think as the cold roof in summer is where the risk of any condensation can occur. We dehumidify to mitigate that.
Dana's suggestion of installing an air barrier around the rafters before installing mineral wool I question...
Mineral wool in all its variances, from Batts to Boards will always be permeable. Air barriers are essential to be added. However, I do not see an advantage putting air barrier material between the rafter and the mineral wool. It will not (I feel) reduce air convection, air movement between the mineral wool and the rafter but increase it. The fluffy mineral wool should, I feel, be compression fit between the rafter and make contact with the rough wood surface. A smooth air barrier will create a more open space there. Caulking the seams between the rafters and sheathing and sheathing seams will be where the air leakage must be stopped. No air barrier after that is better over an air barrier. Even when thinking of installing Polyiso for a venting channel, I think caulking all the seams is preferred over installing an air barrier.
Cellulose versus mineral wool. I understand that there is plusses and minuses to both. For cellulose, I would only consider a wet install, dense packed moist install.
When the downside of mineral wool would mainly be WHEN there'd be a leak, the mineral wool would keep the water against the sheathing for it to soak up. Steel roof means very low leak chance. So now I do not know if it is possible to maybe carefully install the first 5 1/2" batts to try and have those not press up against the sheathing? It is working in the dark on this but that would be good to avoid direct contact with the sheathing. Again it being a steel roof, leak chance is already be low.
So still focussing on mineral wool.
Would also get me, with 1" continuous Comfortboard IS underneath the rafters R50.
MemBrain between the openings of the vapor tight WarmBoard. The WarmBoard R panels with their alu plating are a Class I vapor retarder. Like poly.
So have to see whether the radian engineer allows for more than 25% reduction of the WarmBoard surface which than becomes MemBrain area. But let's assume that that is all I would be allowed to have before compromising the cooling.
MemBrain still vital to implement despite the painted drywall?
Dana, you said:
"MemBrain still a good idea for the interior side detailed as an air barrier, since the thermal expansion/contraction of WarmBoard makes it a dubious air-barrier over the longer term."
The WarmBoard panels a Class 1 vapor retarder. Only the seams will allow air and vapor movement. THAT is where the MemBrain goes. So between the WarmBoard panels, the 25% ceiling space where we will put no WarmBoard, is where the MemBrain would be installed. Or also space out the perpendicularly installed to the rafters WarmBoard panels and full cover the panels afterwards with a complete coverage of MemBrain is an option. Just to spread the vapor diffusion possibility more even over the ceiling.
I hope you can all follow my drift.
Looking forward to all comments! Thanks beforehand!
Jan
Jan,
Good luck with your insulated roof assembly. You have already gotten more than enough advice. It's time for you to make your decision.
To reiterate: there are only two code-legal ways to create an unvented roof assembly: either (a) include a layer of rigid foam of adequate thickness above the roof sheathing, or (b) include a layer of spray foam on the underside of the roof sheathing.
If you install air-permeable insulation like mineral wool against the sheathing in an unvented assembly, you risk sheathing rot.
Sorry to annoy you Martin.
But I understood from you that my steel roof is considered a Class I Vapor retarder. Consider it 6 mil poly. Correct? I can not expect any vapor diffusion to be happening to the outside.
So what does Polyurethane foam do for me apart giving me R value? It will only give me what I already have.
Plus the rafters will remain exposed pathways with polyurethane foam.
The risk of sheathing rot will only be caused from leakage? I can accept that risk with a steel roof as that is one of the best roofs to use for an unvented assembly according to GBA info.
As when it would be from condensation, the steel roof is not a Class I vapor retarder.
With MemBrain and dehumidifying you think the sheathing can get moisture from the inside?
I hope to hear more from Dana AND from you for that matter regarding my confusion you created.
But when the inspector will allow it I will stay away from foam. My mind is made up in that regard.
Jan,
You are correct that most types of roofing, including steel roofing, do not allow any drying to the exterior. If you want drying to the exterior, you need either (a) to include a ventilation channel adjacent to your roof sheathing, or (b) to choose a vapor-permeable roofing material like concrete tiles, slate, or cedar shingles.
You asked what foam insulation gives you apart from R-value. Here's what it gives you: a barrier to air flow. That (along with the fact that most foams are not very vapor-permeable) helps protect your roof sheathing from moisture accumulation and rot.
But don't I have that barrier to airflow with my steel roof?
When the steel roof is a Class I vapor retarder it IS an air barrier?
Any vapor retarder is an air barrier. Not any air barrier is a vapor retarder.
Caulking the seams on the underside of the sheathing is an extra safeguard. Foam would "only" be that extra safeguard. The rafters remain the vapor diffusion holes in the entire setup. THAT is why I do not rate the foam that highly, taking all those facts in consideration.
Thanks for continued help Martin,
Jan
Jan,
Most types of steel roofing are vapor barriers but not air barriers.
There are several examples of vapor retarders that are not good air barriers. One example is vapor-retarder paint.
You can also have an air barrier that is not a good vapor retarder; an example is Tyvek.
During the winter, the source of the moisture that can damage your roof sheathing is the interior of the house, not the exterior. Spraying closed-cell foam against the underside of your roof sheathing would provide an air barrier that protects the cold sheathing, preventing moisture accumulation. Mineral wool can't do that.
Mmm. Interesting.
The Tyvek logic is easy to follow. Surprised to read that steel roofs are poor air barriers BUT good vapor retarders. Water molecules are bigger than air molecules. But the SEAMS would than be the molecular filters on a steel roof? That makes me frown...
MemBrain or IntelloPlus will become more open on elevated relative humidity detection, so when I have to guard for humidity coming from the inside of the house: a smart vapor retarder behind the drywall won't help, correct? It should not allow any moisture in. OUT yes, but in no. So I can treat the roof like the walls in our climate: no smart vapor retarder needed. For the roof: a smart vapor retarder would be the WRONG thing to do? Or pointless at least...
When polyurethane would keep moisture off the sheathing: why not just paint the underside and rafters?
Thanks again.
Jan
Jan,
It seems that you doubt my reasoning and distrust my advice. Look, it's your house, and it sounds like you have developed a firm understanding of what you want. That's fine, because you should build it the way you want to.
Good luck.
Where is the distrust? I am just trying to comprehend your explanation. I am posing questions and in the end now get no answers. But being accused of distrusting you and having made up my mind. The questions prove that I have not made up my mind at all.
Isn't this forum supposed to get questions answered?
This is getting very weird now.
You cannot or will not answer my questions? Either way it is a dubious situation now.
Sorry Martin but I can see no other view on this.
Jan,
Experience has shown that drywall or other similar air barriers on the interior side of an unvented assembly are not enough to prevent interior air from reaching cold roof sheathing when the rafter bays are filled with air-permeable insulation.
For one thing, the air between the fibers is moist, interior air -- not magic dry air. For another, it's hard to totally eliminate hidden air channels.
Painting the underside of the roof sheathing will not prevent the sheathing from absorbing moisture. If you doubt this, make a shower stall out of plywood, and paint the plywood, and tell me what the shower stall looks like in two or three years.
Jan, Martin has given you lots of good advice and has been very patient with you even though there are lots of other people that also require his advice and help. Listen to him. It's not Martin that has brought an attitude with him. It's you, but unfortunately you are unable to see that. If you don't think he or others are giving adequate help then move along to another internet forum that may be more helpful to your needs.
"it's hard to totally eliminate hidden air channels"
That I would change to impossible. That is how mother nature always beats us. Your plywood shower example can be sprayed on with polyurethane as long as it is a continuous polyurethane layer and will suffer no wood decay is your suggestion. But that is a purely theoretical shower. As it is IMPOSSIBLE to totally eliminate hidden air channels. OR build a shower you cannot get in and out of...
Brings me back to the wooden rafters in a polyurethane insulated unvented roof.
The warm moist air that WILL get in in the winter must have a path out over the summer. The shower is in that regard not a fair comparison as the moisture loads and frequencies of bringing those to the hidden pathways give it not enough time to get out between showers. See it as a swimming pool... Different approach applies there..
So assume we spray polyurethane under the sheathing. The sheathing will not get condensation forming on it. The mineral wool-polyurethane surface will. I understand the "warming" effect of the polyurethane under the sheathing. Thus reducing the condensation risk. But in both situations, no polyurethane under the sheathing or with polyurethane under the sheathing: moisture must always be able to get out over the summer. As it will always get in over the winter.
So no multi layer of paint can ever compete with Polyurethane in this scenario? Polyurethane gets also sprayed onto the rafters in your scenario? When so: would make sense, but would make installing mineral wool more difficult/impossible avoiding over and under compressing.
Polyurethane coat would have to completely follow the sheathing, rafter sides and bottoms. Thus sealing it all plus giving the thermal breaks at the rafters.
BUT it's a moon landscape once it is cured. Can one spray it to get a smooth level surface to work with?
That is where paint can do that at least.
Acoustic seal first. Paint over top. The only thing missing in this is the reduction of the sheathing temperature by the polyurethane.
But when getting to R50 in the assembly in our climate big question is now would that be suffice?
The forming of moisture onto the sheathing in winter is solely to blame to the permeability of the insulation? R 50 will not help at all as the mineral wool is permeable and whether your make it R100: you will always get moisture diffusion to wander to the sheathing?
That 1" of polyurethane between the rafters will totally prevent all moisture and reduce the condensation forming between the polyurethane and mineral wool?
Rafters will stay safe? As there the R value is not there at all.
I can follow the sheathing protection but again what about the R1 in the rafters...
The full foaming of the whole shebang with one continuous layer or 1" of Polyurethane makes sense. But makes the rest of any install impossible, insulation, drywall?
1" under the sheathing, and that's it? With R1 rafters would poking through all over the place? And that would be the panacea?
Moisture will get in, make sure it can get out is I think the basic rule. Polyurethane only oh so marginally helps. How wet do the rafters still get?
To Eric,
Sorry Eric to consume all Martin's time on this, and others. But the questions I have, I feel are all fair. Maybe you can explain how the R1 rafters have to be treated in this unvented roof? Lstiburek struggled with this.
And now so do I.
It sounds like you have convinced yourself of the need for roof sheathing ventilation.
There are two ways you can do this: above the roof sheathing, or below it.
If you ventilate above the sheathing, you have to remove and re-install your steel roofing and deal with the headache of detailing it properly with the other roofing materials you have.
If you ventilate below the sheathing, you have to leave a large ventilation gap that reduces the amount of insulation you can stuff between the rafters.
Pick your poison.
I recognize and sympathize with your mindset. You are trying to get a result that is perfect according to theory, within the constraints of the non-perfect situation that reality has handed you with. I sometimes struggle with this kind of thing too. The science and the experts tell us X or Y, but we are pushed by the vicissitudes of reality to accept Z instead when we not only want X but understand why it is preferable. Or we have made a personal decision not to accept Y even though science and the experts tell us it will work that way, reducing our options. Etc.
When we are confronted with this kind of situation, we have two options: we can make a compromise, coming as close to what we want as is practical within our budget, means, and preferences, and accept that the result might nonetheless be deficient in some ways... or we can continue to try to shoot for perfection, and accept that it will cost us dearly in time and money to achieve it, if it is even achievable at all.
It sounds to me like you need to decide between the following options:
1. Accept foam into your life and apply a few inches of ccSPF under the sheathing, then fill the rest of the space with mineral wool.
2. Accept a roof that is not as well-insulated as you would might prefer, and make a 6" ventilation gap under the sheathing, leaving you with only 5" of mineral wool batts between the rafters.
3. Accept that your ceiling will need to come down a bit, and put 6" of mineral wool boards under the rafters, with 5" of mineral wool batts above it and a 6" ventilation gap above that.
4. Accept the cost and complication of adding ventilation underneath your metal roof, and then stuff the rafter bays with mineral wool.
5. Accept the risk of roof sheathing rot if you stuff the rafter bays full of fluffy insulation with no ventilation channels either above or below it.
You can go around in circles forever but fundamentally, these are your options.
Let me give you an example from my own continuing home improvement saga. I read all the time that cellulose is the best material to use for attic insulation. Cellulose, cellulose, cellulose. It's the bee's knees. It'll walk your dog and make you breakfast. So I go to hire out my attic insulation job and nobody wants to blow cellulose. They only do fiberglass. Owens Corning this, Owens Corning that. And all the cellulose that I can find locally available--in case I acquiesce to doing the job myself--is the crappy stuff that has Ammonium Sulfide in it, which is corrosive to metal when wet. I don't want that junk. So now I'm stuck. I can't find the best material available and I can't find anyone to install it.
What did I do? I hired a crew to air seal and blow fiberglass for a very reasonable price. I made buddy-buddy with them during the job and as a result they gave me an extra 3" free of charge. Finally, one of them had his eyes on a TV in my garage that I wasn't using, so I told him he could have it if he used a couple more bags that they had in their truck. Boom, another 3" or so.
So for the price of 10" of fiberglass, I got 16". Now, is 16" of fiberglass as good as 16" of cellulose? Probably not. But it's still pretty darn good, and it's on top of abut 5" worth of fiberglass batts and existing cellulose. So I have about 21 inches of insulation in my attic now. Is it the best kind of insulation out there that comes highly recommended by the foremost building science professionals? No. Is it going to be good enough? I'm sure it will be.
Don't let perfect be the enemy of the good. Perfect is for the rich. And if that describes you, when what are you doing bumming around here? Just pay them the money to reinstall the roofing panels with ventilation channels! :)
We could have a good yarn Nathaniel, for sure. Enjoyed reading your addition to this "quest for the best".
Yes we have some spare cash to do this. BUT cannot rip off the roof as it cascades onto the other roof... 5 yrs ago new steel roof plus new 1" pressure treated cedar shakes on the east facing roof. Not a good waste of our money to rip that up now hey!
I am a thinker, call it overthinker. YOU may have accused me of that in this thread? YOU!!!!
But no, sleeping on things make me think things through. We have limited space. We want radiant cooling. We have a ground source heatpump installed. It's going to be quite the nice setup.
Bloody foam is going to spoil that now for us? YES when it makes sense. BUT it just does not add up. I see so much BS code rules that we go 4 times over or just comply with when we must. THIS may end up the same when the inspector says we cannot install mineral wool the way we want to. You and your cellulose hunt: with mineral wool I need no TV brokering to get it done right or better. I can do it myself. It's our house. I love to do as much as I can myself.
Now can YOU explain the point of polyurethane next to a R1 rafter "BECAUSE YOU NEED AIR SEALING"... and condensation reduction. As it won't eliminate it...
The shower example from Martin is also ingenuous. Not a fair comparison. It just does not convince me..
You had the room to add insulation for free. I don't. The wiser minds like Lstiburek I have mentioned multiple times, throw their hands in the air. I am so glad I read that line from him. So it IS not set in stone. It is a moving target.
Cannot go 6" below the rafters. 1" was already a problem but we have to.
For the cedar roof I think we have only 2 x 4 rafters there... Ever heard of Spaceloft? KACHINGGG! But at least we have ample outward venting there...
Life goes on.
Thanks Nathaniel!
Jan
You are worried about durability and insist on no foam. Honestly it sounds like the best approach is to go with an all-mineral-wool vented roof. This approach seems like a no-brainer to me. Leave a 6" gap under the sheathing, fill the 5" under that with mineral wool batts, and put 1" mineral wool board below that--more if you can stand to lose another inch or two. Cover it in drywall and bob's your uncle. This roof has some advantages:
- It's robust; you have a big ventilation cavity
- It's cheap!
- The insulation is all totally fireproof, moldproof, and insect-proof
- You can easily do it entirely yourself
It has only one disadvantage:
- The total R-value is only about R-23 if you absolutely cannot use anything thicker than a 1" mineral wool board under the rafters
Maybe that's okay. If it's not, maybe you can look into Dana's suggestion to improve airflow in the cavity with a venturi thingy. Frankly I have no idea what that means but if it lets you safely reduce the cavity to, say, only 2", then you can add 4" more mineral wool batts and total R-value of the assembly would be 36. That's not superinsulated passivehaus level, but frankly it's probably better than what most of your neighbors have in their roofs. It should be easy to accept the slightly increased utility bills vs a theoretically perfect R-50 roof in exchange for the peace of mind of a foam-free highly durable roof and drastically reduced installation costs.
That spaceloft stuff looks scammy. My initial impression is that it's too good to be true or else everyone would be using it, but I'll happily defer to a real actual expert and not a deranged lunatic such as myself. :)
I'd rather have foam and R value over your suggestion. MY problem is and it is mine only apparently.... that I, me and myself don't see the NO CONDENSATION forming with polyurethane between the rafters on an unvented assembly.
It will, MUST, form on the rafters. Which is no problem as long as it can get out. When it will form on the sheathing without polyurethane, it will continue to develop on the rafters with polyurethane. The r value is less. What else can you expect. Moisture will condensate first on the coldest surface. Polyurethane only helps half the problem. Less attention on polyurethane. More attention on the vapor diffusion.
Okay, then here's another option for you. Replacing the 5" mineral wool batts with 3" batts snugged up against 2" foil-faced polyiso caulked to the rafters raises the total R-value of the assembly to R-26 with a 6" ventilation gap and R-39 with a 2" ventilation gap. You don't like foam but the polyiso would be protected from fire by the mineral wool and drywall (an excellent set of fire barriers!). Just another option. I'm not even including the extra R-2 or so from the foil facer being a radiant barrier facing open airspace because it would be facing upwards, and therefore will accumulate dust over time and no longer be a radiant barrier.
Conceivably you could replace all the mineral wool batts between the rafters with polyiso, which gives you R-30 with a 6" ventilation gap and R-48 with a 2" ventilation gap. The polyiso would still be protected from fire by one inch of mineral wool and drywall. You could even make it 5/8" fire-rated drywall if that's something that worries you.
Oh God! I unleashed the Foam Monster! Poly Iso does not have good long term R values hey. But you may have calculated those in. Off gassing is also a bad thing PLUS how does it get recycled? Not.
But what about the condensation issue. What does your mind say about that. WHEN we foam it all BUT, like everybody, ignore the R1 rafters... That means ALWAYS we must have a moisture path OUT. Foam, mineral wool or Dorito chips in the ceiling...
There seems to be some mental confusion about air barriers vs. vapor barriers. Time for some Building Science 101 review:
An air barrier blocks the movement of air that would move when there is a difference in air pressure. This is pretty easy to understand, since we can directly sense moving air.
A vapor barrier blocks the movement of water vapor via diffusion through solid materials driven by vapor pressure, which is a function of the absolute moisture content of the air on either side of the vapor barrier. This is NOT something we can sense directly, but we can measure it. Wet-bulb temperature is one direct method of measuring it, dew point temperature is also a function of absolute moisture content, but is more complicated to measure.
The vapor pressure difference that moves moisture through a semi-permeable air-tight ceiling is created by the temperature difference of the roof deck and the dew point of the interior air. Healthy comfortable air is between 30-50% relative humidity (relative to the temperature, that is.) At 70F the dew point of 50% RH air is about 51F. When those are the indoor conditions, whenever the roof deck is below 51F moisture in the entrained air in the fiber insulation migrates into the OSB as adsorb (not condensation on the surface). The lower the temperature of the roof deck, the lower the dew point of the air inside the cavity. That creates a difference in vapor pressure (not air pressure) between the room air and the roof cavity air, which causes room air moisture to migrate into the cavity. The rate at which the moisture enters the cavity is moderated by the vapor retardency of the ceiling materials. During warmer weather the roof deck releases it's moisture into the cavity, causing a cavity dew-point higher than your conditioned space air, moving the moisture out.
As long as the rates of moisture migration are sufficiently moderated, nothing bad happens. But if it's too vapor open to the interior or there is air-transported moisture, the roof deck can become saturated to high moisture levels over a winter, and it's a problem, creating a risk of mold or rot conditions in the roof deck.
Whether a vapor barrier is air-tight or not doesn't affect it's vapor retardency. The vapor tightness of an air barrier has no effect on it's air-tightness. They are two separate properties of an assembly or material layer within an assembly.
Steel roofing has seams that are not gas-tight, or even liquid-tight, but steel is a powerful vapor barrier- moisture will not move through the steel roofing via vapor diffusion, but it can via air leakage or direct wetting (wind-driven air or rain).
Air leakage at the ceiling can move quite a bit more moisture into the roof assembly than vapor diffusion through painted gypsum board, and that's why the CEILING needs to be absolutely air tight when the roof deck isn't vented. Vented roof assemblies continuously purge any moisture that finds it's way in via the ceiling leaks or vapor diffusion by displacing & diluting the air inside the cavity with outdoor air, (which in western WA is almost always pretty dry, from an absolute moisture point of view, with out door dew points rarely exceeding 60F.) If the assembly isn't vented to the outdoor, and there are vapor-impermeable layers between the roof deck and the great outdoors (which there are, in almost all roof assemblies), then the only path out has to be through the ceiling. As long as the ceiling is air tight and sufficiently vapor permeable (but not TOO vapor permeable), moisture can't build up to excessive levels or become trapped. If the ceiling is NOT air tight, too much moisture can get in via air-transported moisture, and drying sufficiently quickly via the same air-transport mechanism is far from guaranteed. Air transported moisture is second only to bulk water incursions for causing damage in building assemblies.
The amount of moisture moving in or out via vapor diffusion at any given difference in vapor pressure is a function of the ceiling's vapor permeance and it's total surface area. If you are installing vapor-impermeable WarmBoard over 75% of the area that other 25% needs to be more vapor permeable to move the same amount of moisture in or out of the roof deck than if the ceiling were all the same permeance. If the 100% coverage were all about 1 perm or a bit less, the risk of moisture build up is very low- and the drying rate is pretty reasonable. With 24" wide strips of warm-board separated by 6" of ~1-perm material (such as half-inch OSB), the drying rate is only 20% of what it would be in the continuous 1-perm ceiling case. That means that the moisture that would normally escape via vapor diffusion in 1 month of warmer weather now takes 5 months, which is a potential problem. But if you use latex painted gypsum board for those 6" stripes it would be about the same drying rate as if the whole ceiling were 1-perm.
But it's damned near impossible to reliably & permanently air-seal a ceiling by taping & caulking all the seams of the WarmBoard panels to each other and to strips of gypsum board. That's why you would want to use large flexible sheet-goods that are sufficiently vapor open as the interior side air barrier between your WarmBoard and insulation layers- there are far fewer seams to detail, and they won't open up by repeated thermal expansion & contraction the way a radiant heating/cooling panel system would.
Using variable-permeance material like MemBrain as the wide flexible-sheet air barrier does it even one better, since then the drying rate would be 3-5x faster than the moisture accumulation rate. During cold weather when the air is drier the roof deck is cold (creating a vapor-pressure difference across the ceiling), but the drier air makes the MemBrain more vapor tight. During warm weather when the dew point of the cavity air rises due to the roof deck releasing moisture, the higher humidity makes the MemBrain highly vapor-open, and the drying rate is only limited by the vapor retardency of the interior paint. Those properties make it better than most other materials as an air-barrier.
Closed cell polyurethane protects the roof deck in a couple of ways. At 1" thickness it's vapor permeance is about 1 perm, which limits the rate of moisture migration to the roof deck via diffusion, and even if liquid moisture condenses on the surface of the polyurethane, it will not wick liquids toward the susceptible wood. But at 1" thickness the interior surface of the polyurethane will dwell at temps low enough over the winter to draw significant moisture in from the conditioned space, depending on the vapor retardency issues previously discussed. But rather than being drawn into the material as adsorb, if the insulation is rock wool it remains as liquid. If enough liquid condensate forms inside the cavity gravity will move it to areas where it concentrates into a potential mold problem. Martin's solution (enshrined in code prescriptives) is to put sufficient foam-R in there to keep the interior surface of the foam sufficiently above the dew point of the room air that very little liquid moisture forms. But that much closed cell foam is also extremely vapor retardent, which means that the roof deck has no meaningful drying path. As long as the roofing materials above never leak (not even a tiny bit), and the foam is installed when the moisture content of the roof deck is already low everything will be fine.
But for large enough amounts of liquid condensate to form even on 1" polyurethane to cause a problem takes a fairly significant air leak & convection to the interior, not just vapor diffusion. And if you use cellulose as the insulation, the cellulose will harmlessly take on significant moisture as adsorb inside it's hollow fiber structure- there would be NO liquid forming, unless there is a VERY significant air leak to the interior. That's why a continuous & reliable interior side air barrier is critical to the long term moisture performance of the assembly, unless you use a heluva lot o' closed cell foam. With cellulose cavity fill and a smart vapor retarder as the interior air barrier you would be able to skip the spray foam altogether in your climate- let the roof deck & cellulose share the moisture load. But if you use rock wool there's an argument for at least a flash-inch of closed cell polyurethane.
Thank you Dana, not read your long posting yet but thank you beforehand! Will do so tonight.
Jan
To put some concrete numbers out there using Dana's examples, filling the rafter cavities with cellulose and putting a smart vapor retarder and one inch of mineral wool below the rafters yields a whole-roof performance of R-34 [ ((3.2*11)*0.75)+(1.2*11*0.25)+4.2 ]
Spraying one inch of polyurethane foam against the sheathing and filling the rest of the rafter bays with mineral wool and then putting a smart vapor retarder and one inch of mineral wool below the rafters yields a whole-roof performance of R-44 [ (((4.2*10)+(7*1))*0.75)+(1.2*11*0.25)+4.2 ]
Neither of these options gets you an R-50 roof. If that's what you want, you have no options left other than to put more foam between the rafters (i.e. replace lower-R products with higher-R products) or lower your ceiling by applying a thicker layer of mineral wool boards (i.e. increase the thickness of the insulation). IMHO this is a good idea anyway to provide a better thermal break for the rafters. You'll never notice another inch of lost headroom.
I'm going to do that most unforgivable thing... commit that most grievous breach of internet forum etiquette... and post on this topic without reading all 63 prior posts in detail.
Jan, if I understand this thread, you are talking about adding Warmboard to the *ceiling* of a part of your house, the part with the low-slope shed dormer, and you're doing this so as to have both heating and cooling available via that Warmboard. Your concern is about the impermeability of the resulting roof assembly. I'm sure the posters on this thread have done a great job of crunching the various numbers that might apply.
My question is, WHY heat and cool the ceiling. I'm in the San Juans, maybe 30 miles from you. I have inspected hundreds of houses up here for energy issues, and have only seen maybe two buildings with heated ceilings, and none with cooled ceilings. We have a huge variety of housing stock here, including plenty where cost is no object. No one I have met or heard of is doing what you're doing. Is it worth the cost and expense? Almost no one here even has air conditioning, and those that do use it a few days per year at most.
Why not install a more conventional system? What am I missing?
We warm through the floors and cool through the ceiling. I can give you more details later if you wish. It's designed by one of the best radiant engineers in the country. Rob Brown or Rockport Mechanical in Maine. Highly recommended!
We only supplementally heat through the ceiling as we have the WarmBoard in there anyway. It's available at least.
Ground source heat pump. Not the cheapest setup but of course but silent heat and cool delivery. Lunos E2 for ventilation.
Dana,
Thanks for this very good explanation. It was a study post!
You mentioned:
"Whether a vapor barrier is air-tight or not doesn't affect it's vapor retardency. The vapor tightness of an air barrier has no effect on it's air-tightness. They are two separate properties of an assembly or material layer within an assembly."
The first line is confusing. Openings in a vapor barrier allow moist laden air through. Huge effect on vapor retardency as it lets buckets of water in. Vapor, concentrated. The second line I can follow.
"But it's damned near impossible to reliably & permanently air-seal a ceiling by taping & caulking all the seams of the WarmBoard panels to each other and to strips of gypsum board."
That is not how we plan to install the WarmBoard and drywall. Warmboard goes in, and drywall sheets go overtop of the WarmBoard, entirely covering the WarmBoard, Creating a full surface drywall ceiling. Between the drywall we can install strips of MemBrain.
But you also mention not to be TOO vapor open. But is it not, in our case, a necessity to be as vapor open and airtight as possible. As long we control humidity levels.
"But rather than being drawn into the material as adsorb, if the insulation is rock wool it remains as liquid"
Cellulose lets water adsorb, spread, wick into and onto it's surfaces. Mineral wool leaves the droplet sizes bigger and won't hold it as much in place so gravity can take over. But both adsorb? Both have vapor going to water/liquid.
But don't both scenarios have to rely again on differing vapor pressures, as explained, to release the water. Vapor and water are two different things I understand. Water is thousand fold vapor. But also in the Cellulose, the moisture is ultimately in there, when it builds up, not held in there as vapor but water.
AS LONG as we have drying to the inside as a path out: what is better: moisture, water pulled into the cellulose and wicked in. Over bigger droplets (I assume that that is how it would go in rock wool) that can collect and start an avalanche downward to the drywall/WarmBoard surface. Which is closer to the way out over cellulose that can pull it all the way TO the sheathing... But again prevention through humidity control is what should prevent the bulk of moist vapor going into the roof in the first place.
Vapor travel will happen in both. Vapor is condensed as water in cellulose and in rock wool the same. Bigger cavities in rock wool, less wicking over cellulose. But isn't that better?
Isn't the insulation secondary to: R value, airtightness, vapor openness and humidity control.
Isn't it the case that in all damage reports regarding mineral wool or cellulose causing rot, some of the primary conditions were not in place? Code may stand in our way as the active part, the humidity control can not be guaranteed for an inspector. So some talking may be involved??
Thanks a lot for all your time Dana. You came up with the third solution using a smart vapor retarder and I hope we can come to a good solution for this tough roof.
Jan
"Openings in a vapor barrier allow moist laden air through. Huge effect on vapor retardency as it lets buckets of water in."
That's EXACTLY where you are confused. Only air pressure differences allow air-transported moisture through air leaks. That isn't the same as vapor diffusion. Vapor diffusion through an air leak path without actual air movement is very slow, since the cross sectional area of those paths can be extremely small. With steel roofing laid tight to the roof deck moisture that gets behind the steel through the cracks & seams can be drawn via capillary action into the tight space, but the cross sectional area of that thin path is miniscule, and vapor doesn't leave via vapor diffusion very quickly along that path, nor can it diffuse through the steel, which has extremely low vapor permeance. The vapor permeance of steel is several orders of magnitude lower than 6 mil polyethylene- the amount of moisture that move through 6 mil poly in a week would take a several million years to get through 26 gauge steel. From any practical perspective it's completely impermeable.
You never put " ...strips of MemBrain..." between anything, since it would make air-sealing a nightmare. Put the MemBrain between the cavity insulation and everything that lives below it, and detail it as an air barrier, making it the primary air barrier for the interior side of the assembly. That means you can be less obsessive about air-sealing the finish ceiling drywall, which WILL have air leaks over time, due to the thermal contraction/expansion imparted by the WarmBoard, the house flexing in the wind, minor earthquake events, etc. Being flexible & elastic, the air tightness of the MemBrain won't change significantly over time through any of that. Be sure to install something as thick as the WarmBoard at the 6" gap between panels at the rafter edges though, so you don't make air leaks in the MemBrain with the drywall fasteners. With the fasteners pressing the WarmBoard and gap-fill material tight to the rafter edge there isn't significant air leakage at the annular ring around the fastener penetration. But if there is a 1/2' or 3/4" gap between the drywall and rafter edge in those areas it won't be clamped air-tight, and it'll leak air.
Mineral wool fibers are not sufficiently porous to take on significant amounts of moisture as adsorb the way wood and cellulose do. With rock wool it is always liquid condensate on the surface of the fibers rather than held internally in the material as adsorb. It takes a HELL of a lot of water to saturate cellulose to the point where it's liquid at the surface. The adsorb-moisture enters and leaves the cellulose fiber as water vapor as the seasonal conditions change, not as liquid water. Only when you have a real roof leak would there be liquid water in the cellulose. In the event that the air seal at the ceiling fails you could have visible quantities of liquid water in the rock wool case, but it would have to be an extremely large air leak above some extra damp location such as the bathroom shower or something to end up with moisture saturated cellulose in a zone 4C climate. (In a zone 6 climate it doesn't take nearly as huge a leak to get there though.)
Roof rot and mold problems to not require high moisture saturation levels in the wood even 16-20% can be an issue if it's for extended periods, which is why a 1" shot of foam is good protection in the rock wool case. But with cellulose the peak levels of moisture in the roof are inherently lower, since the cellulose shares the moisture burden with the wood, and disperses it evenly within the cellulose layer.
The moisture collects initially at the coldest surface of the cavity, which is the roof deck- there's no moisture for the cellulose to wick up toward the roof deck, it only wicks it away from the roof deck, except in the even of a leak in your radiant tubing. That's another reason to put the MemBrain between the WarmBoard layer and fiber/rafter layer, since it's waterproof to liquid moisture.
Dana, thanks a million man for your patience and time!
The definition of adsorption:
"Adsorption is the process in which atoms, ions or molecules from a substance (it could be gas, liquid or dissolved solid) adhere to a surface of the adsorbent. Adsorption is a surface-based process where a film of adsorbate is created on the surface while absorption involves the entire volume of the absorbing substance."
So aren't mineral wool and cellulose in their physical properties identical, atomically. EXCEPT for the fact that when putting it like this: two rooms, one with 15 towels. Second room with 10 towels. Room one is the cellulose, can hold more water.
So the good of that is that it can pull water away from the coldest surface: the sheathing that Rockwool can do less or VERY less or hardly. Maybe it's 15 towels and 1 towel?
Can I put 5 1/2" cellulose against the sheathing, followed by 5 1/2" of rock wool.
Still one inch of Comfort board across the rafters, MemBrain or IntelloPlus (what is your verdict on IntelloPlus compared to MemBrain?) than the WarmBoard 13/16" thick, fill the 6" spaces with OSB?
Now between the cellulose and the rock wool, what is best for a separation so that I can put the cellulose in as I go up on the ceiling. A second smart vapor retarder sounds like the best choice.
OR, getting bold now. Can I install 2 X 5 1/2" rock wool in the rafters when I use a second smart vapor retarder??? Sealing the middle one on the rafters or wrapping it as uninterrupted around the rafters and sealing only at the widths of the roll. On the rafters I would have two vapor retarders on top of eachother...
THANK YOU !!
Jan
It sounds like you have decided that it's going to be okay to skimp on R-value. Your half-cellulose-half-mineral-wool plan:
(((5.5*3.2)+(5.5*4.2))*0.75)+(1.2*11*0.25)+4.2 = R-38.
Nothing wrong with R-38; could be worse. Just be aware that that's what you've decided to compromise on. Again, the only way to have an R-50 roof if you aren't willing to put more than an inch of mineral wool board below the rafters would be to replace some of the cellulose or mineral wool between the rafters with polyurethane spray foam. If you can come down just another two inches and have three inches of mineral wool below the rafters instead of one, then the total rises to R-46; one more inch beyond that gets you to R-50. Thermally breaking those rafters better is a good idea...
Nathaniel,
Struggling with the double smart vapor barrier, if that makes sense. I fear we do not want to loose the wicking effect on the sheathing from the cellulose. But if 2 x 5 1/2 rock wool is allowed than with the 1" underneath I am back where I was with the R value.
Jan
2" of cellulose and 9.5" of mineral wool gets you R-40.5: (((2*3.2)+(9*4.2))*0.75)+(1.2*11*0.25)+4.2
The math isn't very hard; you can figure out for yourself what R-value you'd like to achieve given your limitations and desires.
Dana will have to weigh in about the double smart vapor retarder but it just on random gut instinct it doesn't sound like a great idea to me. Why wouldn't one be enough?
One other comment: spill some water on cellulose and do the same thing on mineral wool and watch what happens. It may be eye-opening. The cellulose sucks it up, while it beads up on the surface of the mineral wool or drains through. Totally different behavior; mineral wool is made up of non-porous rock strands treated with some kind of oily substance; it doesn't absorb water at all. Cellulose, as a natural material, has totally different behaviors when it encounters water.
R value is secondary in our roof but do NEED to optimize it at the same time as that will also contribute to the moisture control.
I think just an air barrier to physically hold up my cellulose is all that would be needed. Insulweb, when it is cheaper but I doubt it is. I think the smart vapor retarder only works on the warm side of the assembly and will do little to nothing in the cavity. I may be wrong. As cellulose and rock wool deal with water differently.
And when the cellulose-rock wool combo would work...
Can it be 7 1/2", R30 rock wool 3 3/4 cellulose? It's a question that may get a "maybe" for an answer as it will get very specific..
Jan
Wanting to span Comfortboard underneath the rafters before the smart vapor retarder and WarmBoard goes in I will end up with mineral wool making contact with the WarmBoard wood and strips of OSB, be it covered with the smart vapor retarder.
Also when it would be a full cellulose cavity, still the thermal break of the Comfortboard should be in there: mineral wool touching the wood at least at the bottom of the cavity But the roof sheathing is where the problems of condensation occur. The cellulose there will prevent any moisture coming down in driplets and ending up on the WarmBoard wood and rafters.
So my guess is that half or even more than half of mineral wool would be tolerable as the roof sheathing is where the condensation risk is.
7 1/2" R30 appears hard to work with. At least in a horizontal application.
5 1/2 R23 PLUS a 3 1/2 R15 layer makes 9" of R38 mineral wool leaving 2" of cellulose.
Two layers of 3 1/2 R15 makes 7" of R30 mineral wool leaving 4" of cellulose.
5 1/2 R23 leaves 5 1/2" of cellulose.
2" not enough? 4" perfect? 5 1/2" overkill? As we start eating on the R value. First option best for that... but is 2" of cellulose all I would need in our climate?
Jan
Nathaniel- where is the double smart vapor retarder? I'm talking ONE layer of vapor retarder tacked to the bottom rafter edges, with the WarmBoard and gypsum below that.
-steel roof
-#30 felt
-roof deck
-Cellulose & rafters
-blowing mesh
-MemBrain
-WarmBoard & rafter edge filler (between WarmBoard panels)
-gypsum board
-paint
Jan: Blow the cellulose in mesh from below. Roll the pillowed out mesh flat to the rafter edges, then install the MemBrain. Vapor retarders by themselves are not sufficiently structural to hold the cellulose. People will dense-pack behind Intello, but it has to be supported by the gypsum after the fact. If you use damp-sprayed cellulose (recommended), the adhesives in the cellulose make it self-supporting.
If the rafters are 11.25" deep (standard 2x12s), with cellulose alone you'll have a center-cavity R of about R41-42 for just the cellulose. To that you add about R1 for the WarmBoard + roof deck, and another R0.5 for the roof deck, which brings it to R43-44. If the rafters are 24" o.c. and there is very little other framing that results in a framing fraction less than 10% which would have a whole-assembly R of about R36, or a U-factor of U0.028. Code-max is U0.026- you're not quite there, but close.
If you rip some 2-2.5" wide 1" thick rigid polyisocyanurate strips glued to the underside of the rafters, (then the blowing mesh/vapor retarder/ WarmBoard/ gypsum) making it 12.25" cellulose, the center-cavity R goes up to R45, the framing fraction is now R18 instead of R12, bringing the whole-assembly R to about R42, or U0.024, and you have met code on a U-factor basis. See Table N1102.1.3:
http://publicecodes.cyberregs.com/icod/irc/2012/icod_irc_2012_11_sec002.htm
That should be considerably easier & cheaper than using full-width 2" rigid rock wool.
If your rafter spacing is 16" and has other framing sufficient to take the framing fraction up as high as 15% it just squeaks by at a bare-maximum U0.26 with just 1" polyiso on the rafter edges, and you might want to consider bumping that up to 1.5" iso board & 12.75" of cellulose if you think the building inspector is going to be a hardass about it, in which case the cellulose would be R47ish. With R47 cavity fill and R9 rafter edge strips you can just do the arm-waving (no math or engineering needed) thermal break raising it to the full required performance (which it would do with margin.)
Speaking for Nathaniel, as I actually launched the idea of a double vapor barrier... But shot it down too...
It was the idea for getting the cellulose in, in this close to horizontal application and separating it from the possible mineral wool. Would have enough buffer with just 2" cellulose? As it, as you say, can hold a helluvalot of water :-)!
Thought was whether a second vapor retarder would have any function. OR just use a strong fabric like a Tyvec air barrier instead. OR is there a tear stronger air barrier I can use?
I hear you with the moist blown in cellulose as you recommend that over "just cellulose". Problem is with that, that I should have mentioned before, is that we go in phases. Room by room. So it's all small parts of the roof for which an installer must show up every time. Hassle plus costly. PLUS cellulose is a bit of a mess, and Polyurethane is a bit of a chemical waste dump in the yard plus multiple off gassing days that way...
I cannot:
put 2" of cellulose against the sheathing, hand pack it in, held up by Tyvek. (as it can hold a hell of a lot of water!)
Rest mineral wool.
1.5" ComfortBoardIS under the rafters.
We have 16" rafters by the way...
Cost is not the issue as much. We'd put full rafter fill polyurethane in when it was like mineral wool benign and fireproof...
Avoiding also polyiso.
Only the cellulose will be a precision struggling to get in. Strong attach the Tyvec with 1" x 1/4" wood strips screwed onto the rafters. Tight like a guitar string and fill and attach as I go up the ceiling to the pitch.
Once THAT is in, it's a cake walk with the mineral wool. MAY need some temporary support before the ComfortBoard goes underneath.
It's the easiest, gives me zero foam and gives me good R value. With 16" rafters...
2 " cellulose enough under the sheathing? Rafters all but 2" in mineral wool ok?
Thanks for keeping an eye on this post!!
Jan
You can dry blow it in mesh and it'll be fine too, but as a DIY it's several daily rental fees if you're doing it piecemeal.
But if it's all wide open, a damp spray installer can be in and out in a day, and you can staple up the MemBrain as soon as they leave. It's not nearly as messy as you might think. Fluffing then packing cellulose by hand, THATS a mess.
If you're committed to doing it with batts, cotton batts have comparable hygric charactersistics to cellulose (but they're much more expensive.)
The amount of polyiso in a 1" thick edge job is pretty tiny in the scheme of things. If you use rigid rock wool it's more compressible, making for a less flat surface, and greater likelihood of air leaks at the fastener penetrations of the vapor retarder. If you're looking for something rigid but as inert as possible, 2" (R7) Foamglas (tm) would be a reasonable subsitute for the thermal break, but since it is also extremely low permenace, it would have to be rafter-edge only, not full sheets: http://www.foamglas.us/__/frontend/handler/document.php?id=905
Dana,
Just stumbled on to Spider insulation via your cotton batt thought.
https://www.greenbuildingadvisor.com/blogs/dept/energy-solutions/getting-know-spider-insulation
This line needs clarification: "Fiberglass is an inorganic fiber, so if it gets wet it may dry out better than cellulose"
Spider is less dense than cellulose, so would it still wick moisture off the sheathing like cellulose. OR is it more comparable in that regard to mineral wool.
The R value is there with Spider. Fire proof, non toxic. Spray in is good to go around wires and irreglular cavities. It is highly regarded in the linked article and an improvement over cellulose. Is it something that could work for our ceiling?? Big downside again would be the multiple installs and not being able to do it myself... But when the wicking action is acceptable: it is a very good consideration!
Avoiding leakage in the Membrain with the flexible Comfortboard IS. Good point.
Membrain should go on just before the WarmBoard so sandwiched between the Comfortboard IS and the Warmboard.
Why not run two beads of acoustic caulk onto the Membrain at the width ends of the bottom of the rafter's locations. (I hope you can follow that sentence!) The rafters are now hidden from view by the Comfortboard and so lining out where the WarmBoard screws will have to go and the drywall later on and run ample acoustic caulk to seal off the penetrating screws area where the Wood panels will press evenly onto the Comfortboard.
Polyiso or FoamGlass strips won't help with sealing as they would be behind the MemBrain.. Sealing of the MemBrain and Warmboard is what is needed most. Yes the ComfortBoard will have more give over polyiso or Foamglass. But would in both cases still an acoustic flexible bead be advised and would actucally do all the sealing of the WarmBoard OSB strips?
Spider,
ComfortBoard (could that be glued onto the rafters temporarily AND the MemBrain onto the ComfortBoard to avoid screw interruption paths for the proper WarmBoard screws?)
MemBrain,
caulk beads,
WarmBoard and OSB strips,
Drywall.
Jan
I definitely just wasted a half hour..... Time to reread the unibomber's manifesto...
Let's start a betting pool. I say there will be no conclusion... $20 down for me... Takers at $20?
Spider is a great product, but like rock wool it has effectively ZERO moisture buffering capacity. Unlike cellulose, you wouldn't be able to DIY it with a rental blower. Rock wool dries faster than cellulose too, but so what?
Cellulose or cotton shares the moisture burden with the roof deck, fiberglass & rock wool do not. It's the same amount of seasonal moisture going in/out of the cavity, but with mineral wool or fiberglass effectively ALL the moisture ends up in the roof deck. The higher the moisture content of the roof deck, the greater chance of mold/rot issues setting in.
The polyiso or foamglass strips are behind the MemBrain, but due to their higher rigidity and lower compression, will hold the MemBrain tighter than rigid rock wool. The rigid-insultiono & gypsum will clamp the MemBrain in a nearly gas-tight fit, a tightens that is impossible to achieve with rigid rock wool, which is also, air-permeable, unlike foamglas & polyiso. Between the thermal flexing tearing/widening the annular ring hole around the fastener over time and the air permeability of rigid rock wool it can't be counted on to remain air tight for decades.
Do the cavity fill with rock wool if you like (MemBrain does work) but don't use rigid rock wool as the thermal break.
Doubled up R23s carefully fitted would just fill the 11.25" of cavity. You could then run tack up the MemBrain and install 2x2s perpenidcular to the rafters "Mooney wall" style, then install split 3" Safe'n'Sound batts or split R15s between the 2x2s to hit/beat the R49 center-cavity. That would also provide at least some amount of thermal break. Use ring-shank nails or better yet, screws penetrating the rafter by at least an 1" to reduce the chance of fasteners pulling under the thermal cycling of the radiant.
AJ: I'll see that $20 and raise ya five! But we may have to wait a decade or more to find out! :-)
Hi Dana,
Indeed "so what" if Spider dries quicker than mineral wool. When it has the same hydrophobic properties as mineral wool.
But you say at the end they I CAN fill the cavity with 2 x R23 mineral wool?
Sure I can, but it is not, let's say, intelligent. I understand the moisture management with cellulose or cotton batts. Cotton batts are no sure thing either btw: https://www2.buildinggreen.com/blogs/problems-installing-cotton-insulation.
FoamGlass appears friable, especially when I would be space limited and would have to use them at 1" depth... There is no 3" to be had below the rafters. I must stick to 1, 1,5" max when ComfortBoard IS would be used.
But could not follow your 2 x 2's perpendicular idea and SafeNSound or R15 3" Comfortbatt suggestion last night. But now I think you suggest the 2x R23 mineral wool in between the rafters plus Comfortbatt below because "I am set on" mineral wool or something?
I only focus on mineral wool because it gives higher R value.
The very best, most expensive would be: (when wanting to stay clear from closed cell foam)
Install thermal breaks at the rafters first. Give up on the foam rule right there and use PolyIso. But polyiso's R value is not R9. But more like R6, in the end isn't it? Nothing else available with similar rigidity with similar R value. THAT is why I was thinking of 1.5" Comfortboard and acoustic caulk for the WarmBoard Membrain contact which is R6.
Wet blown in cellulose followed by Spider in the now 12" Cavity(with polyiso strips), or 11" cavity when we still go with Comfortboard under the rafters.
Is that an option? Where to stop with cellulose, how much is minimally needed for the wicking working on the sheathing. I think that cellulose, hand stuffed or wet blown will be superior in it's sheathing contact over cotton batts.
When a few inches like say TWO would be suffice for the cellulose to do it's work and have enough volume at the same time to be a buffer for the moisture: I could consider hand stuff the mess in there behind Tyvec.
MORE cellulose means less R value. So how much cellulose.
Blown in Spider I fear beats mineral wool batts in performance.
Focussed on splitting all in TWO trips for the installers.
OR you say the use of Cotton Batts remains 100% equal in it's wicking working plus would add to R value.
As for the Las Vegas trip.
I am ALL IN now as I am challenging THE HOUSE!
Jan
This is going around and around in circles for no reason. Here is what I would do if I was in your shoes and had all of your constraints.
Between the rafters:
- 3" of cellulose against the roof deck held up with netting
- 8" of mineral wool batting under the cellulose
Under the rafters:
- MemBrain, sealed and detailed as an air barrier
- 1" of the most rigid mineral wool boards possible
- 0.25" plywood screwed into the underside of the rafters, to serve as a fastening surface for the warmBoards and hold up the mineral wool boards
- WarmBoards fastened to the plywood, with scrap mineral wool stuffed in any open areas between the boards
- 1/2" drywall fastened to whatever's available, avoiding penetrating the tubes in the WarmBoards
This gets you about R-43, assuming a 15% framing fraction (my estimate of 25% was too high)
(((3*3.2)+(8*4.2))*0.85)+(1.2*11*0.15)+4.2 = 42.9
Is this perfect? Maybe not. Will this work and be safe and inexpensive and fully DIY-able and yield enough insulation for your purposes? Yes.
Nathaniel: WarmBoard and radiant lines cannot go into 1/4" plywood... They need more support. But regarding the hardest mineral wool sheathings possible: they'll never seal the smart vapor retarder properly.
Dana,
What if...
Insulation between rafters. Membrain onto rafter. 1/4" strips of wood with acoustic caulk squeezing the membrain between the strips and rafter. THAT would seal the Membrain perfect without having to worry AT ALL, EVER.
Than Comfortboard IS, CAN I keep that out of the vapor barrier controlled space behind the WarmBoard and OSB?
It would be neccessary as we WILL commit another sin: ceiling lights. Cooper LED lights that need 2 1/8" deep junction boxes. Can attach to WarmBoard and 3/4" OSB just fine. Only wire penetration again needs sealing through MemBrain. Not many lights, but crucial. They would stay out of MemBrain zone that way.
WarmBoard.
Drywall.
Smart vapor retarder up to roof sheathing on soffit end and wall ends as well I would think? That would mean preinstall before insulation goes in on those area. Taping onto the ceiling smart vapor retarder, or leave in protected roll hanging on the side as much as possible during insulation install to avoid taping to the max.
Choice of smart vapor retarder. When drywall with latex paint would reduce the openness to 5 perm or less regardless, IntelloPlus is pointless. EXCEPT for the better closing at low RH. Is that not a better criteria for picking the smart vapor retarder in general. It's sealing ability? It is practically always behind drywall so any smart vapor retarder would do: pick the cheapest. But the SEALING rate is maybe worth the extra money?
Thanks again all!
Jan
The issue of the hygric buffering cellulose vs. mineral or glass fiber when used with MemBrain is a matter of which provides the greatest moisture resilience.
So what if polyiso's R-value @ 1" is only R6, not R9? The code-compliant U-factor I calculated for you was based on R6, not R9.
If you use 1/4" plywood strips as the nearly-gas-tight clamp for the MemBrain above the ComfortBoard it should work, if that's the way you want to do it. There would be potential convection paths around the comfort board at those strips though, unless you cut a 1/4" deep dado in the ComfortBoard to accommodate the plywood strips. From a total performance point of view that's kind of "in the noise" though, not worth spending too much time worrying about, but thinner stock would be even better.
Given that your 5-perm paint open to the interior side are only ~20% of the total area, the rest being impermeable WarmBoard, it's somewhat better to go with the more vapor open MemBrain rather than Intello Plus, but either would work.
You mentioned:
"The issue of the hygric buffering cellulose vs. mineral or glass fiber when used with MemBrain is a matter of which provides the greatest moisture resilience."
But I could use mineral wool in combination with 1" Polyurethane layer sprayed onto the roof sheathing, right? The condensing happens on the cold roof sheathing. So I was hoping in attempting to stay away from foam BUT still max out the needed R value: to have "a" layer, (need help with the depth estimate there) of cellulose (cotton batts may not wick as good, PLUS burn, I just noticed!!).
So the condensing sponge of cellulose at the sheathing of some inches.
Than followed by Sider blown in fiberglass, to max out the R value.
Good to hear that ComfortBoard below the MemBrain is ok. That makes the MemBrain install less complicated. But the 1/4" wood or thinner rigid plastic? strips WITH acoustic sealant between the strip and the MemBrain will ONLY create a vapor path now around the screw holes of the WarmBoard and drywall. Which may get a smear of Acoustic seelant on them as they go in.. The ComfortBoard would get compressed between the strip and WarmBoard, OSB panels. Not onto the Membrain, well not as much.
Regarding the choice of smart vapor retarders.
You mentioned:
"While the MemBrain will be over 10 perms when there is a lot of moisture in the cavity, if there is 5 perm paint between the MemBrain & conditioned space it hardly matters."
So that is where I was going with the IntelloPlus or MemBrain or DB+? These smart vapor retarders all perform passed the limiting drywall. So ANY would do. Even though I have limited paths due to the WarmBoard: my limit remains: the surface area and permeability of the DRYWALL. Not the smart vapor retarder?
MemBrain's openness is >10 perms.
IntelloPlus is 13.2
MemBrain goes more open than IntelloPlus, you say? >10 means up to air barrier rating, totally open??
And DB+ is not stated more than:"• Works very well as vapor retarder for mineral wool, fiberglass, BIBS, cotton and sheepswool insulation.
• Reinforced layer allows it to be used as Cellulose blow-in mesh – follow application guidelines for best results – use counter battens to support DB+ to hold in the insulation.
Biggest question: can I still use part Spider blown in, with cellulose right under the sheathing. How much cellulose at LEAST? Only 11" of rafter space to fill, with Comforboard R6 underneath. And WarmBoard and drywall...
Thanks Dana, impressed with your patience and best help possible for this extreme roof!
Jan
Jan
It doesnt seem like the weather is that extreme. December has an average high of 45 and average low of 34. I would think that if an air tight ceiling was installed and maintained that moisture should not be a big concern.
Personally I think a putting up a radiant ceiling is the wrong idea. You are putting a heat source against the ceiling raising the delta T at the thermal boundary. In the summer you are putting the cooling against the thermal boundary and I would be concerned with the cold attracting moisture.
Some of your comments about spray foam and the framing leave me confused. Wood has an R value of about 1 per inch. A 2 x 11 has and R value of about 11. If the side of the framing is spray foamed it would only leave the bottom edge uninsulated. That edge would be above the dew point and would not cause wood rot so it is a non issue. Yes there would be thermal bridging but that is something you will have to live with unless you remove the roof and add foam above. I understand that is not going to happen.
What about adding a minisplit heat pump to provide heating and cooling. I would think that would be somewhat similar in cost to extending and install the radiant heat to the ceiling.
What do you do for dehumidifying the air in the summer. A radiant ceiling would not dehumidify.
What is the status of the lighting. Any holes in the ceiling are going to be a problem.
Also what is the code R value for cathedral ceiling versus a non cathedral ceiling. Is it R 38 in you location.
Because of the low slope I think the best bet is to put in 2 inches of closed cell and finish with rock wool.
Thanks Robert for thinking along.
Average low is the important number. And that can lead to condensation on the sheathing. Your personal idea of radiant ceiling being wrong is not totally wrong. Preferred is floor heating. Which is what we will have on the second floor. Part staple up with ThinFin alu plates and WarmBoard for the bathrooms. Best for cooling is having it higher up: the ceiling. With a GSHP setup our cooling costs are low and will only lay in the installation cost of the panels, tubing and manifold. Not a low number still! We are cool sleepers so really value this radiant cooling ceiling. Plus living in the city it is also a big bonus to be able to keep the windows closed in summer for noise. Blowing air through minisplit systems we experienced in hotel rooms and really see that as a forced air system, which it is: uncomfortable and noisy even though it were newer units we have slept under. So we warm through the floors and cool through the ceilings.
BUT we will heat and cool through the ceiling only on the main floor. Floor height issues there make a WarmBoard install very difficult. Ceiling installs have big advantages though, WHEN YOUR SURFACE IS FLAT. You cannot warm a room via a slanted ceiling. Cooling is fine. Ceilings do not have carpets or wood paneling on average. Drywall has low insulating value so radiation works very good. When your floor is not tile or stone: ceiling installs will make your floor just as warm via radiation. Electric ceiling installs get the complaints of warm head and cold feet. Because people turn them on and off. Insulation and constant on are two factors that are required for a proper working/experience of a ceiling as well as floor radiant system. But ceiling is a very good second best after floor radiant: for heating only when you have a horizontal ceiling.
We can use the upstairs ceiling for supplemental heating though. But not more than that.
Lighting will stay out of the MemBrain layer. 2 1/8" deep junction boxes for flat LED ceiling lights. Drywall, WarmBoard and ComfortBoard will give us that needed depth.
Spraying foam onto rafters will make mineral wool batts impossible to install unless we'd custom cut those.
Hoping to hear Dana's last thoughts on the cellulose depth as we can use Spider install also on our double stud 8" kitchen walls and other installs in the house. Only cellulose for below the sheathing, rest in the house Spider fiberglass. All in two times two separate products: wet blown cellulose, JM Spider blown in fiberglass.
Dehumidification load would be low according to our radiant engineer and we could use a centrally located, high under the roof in the hallway, SantFe Rx unit to service the entire house. Except for the basement...
I hope I covered all your questions.
But no closed cell foam, that remains high on the list. I agree with this article on foams:
http://foursevenfive.com/is-foam-evil-a-new-paradigm-of-foam-less-is-more/
Jan
Jan
When your floor is not tile or stone: ceiling installs will make your floor just as warm via radiation.
Should read as "when you cannot have a radiant tile or stone floor"... As radiant in those types of floors is of course perfect. ONLY when you have good insulation otherwise also stone radiant floors can be uncomfortably warm... And wood floors have limits in how much heat you can put through them before you damage your floor... So in all: do not dish the ceiling radiant for heating...! It needs to have all parameters in place...
Jan
Jan
Jan you are dealing with a retrofit and I understand about ccsf. What you need is to make the improvements durable. If you create wood rot and mold it will be a lot worse. Overall I am sure the home is not very energy efficient. Your heat pump is probably not as efficient as you think it is.
Personally I am not a fan of radiant in most cases. If your home was truly energy efficient heat loads would be so low that radiant would not be the right choice for a number of reasons.
For the lighting. Well you are complicating the issue by cutting in to the ceiling. Couldnt you do wall sconces or something else.
What do you do for humidity control in the summer
We have all that in check Robert. We have one of the best radiant engineers in the country working on this.
The roof is the only concern as that is a Rubic's cube. We are fine with all the rest. Lights stay out of the MemBrain area. ALL possibilities been contemplated and gone through many times, believe me. Walls ALMOST all get double studded, TRUE 8". 9 in some places.
Dana:
the cellulose thickness thought would be my last struggle.
I am even more happy with cellulose (EXCEPT for the lower R value), over Polyurethane.
Moisture between the sheathing and polyurethane can get trapped there too.
With a vapor tight metal roof: NOTHING should stand in the way of any moisture to go out.
Let out with what can come in, is the idea.
Is my R value good with ? inches of Cellulose? Those are the only two questions left.
Jan
The vapor permeance of Intello Plus doesn't rise above 2 perms until the RH of the proximate air is about 70%. The 13.2 perms is an absolute maximum, which is it's vapor permeance in the presence of 100% relative humidity fully saturated air.
With MemBrain becomes greater than 2 perms at about 40% RH, and is almost 10 perms at 70%RH:
http://www.naturalspacesdomes.com/dome_store/dome_insulation_systems/images/Membrain3.jpg
In English ">10" reads "greater than ten", with no defined limit. Unlike Intello it has no specified maximum permeance though it must have SOME vapor permeance in nearly-saturated air. But whatever that limit is, it's in the "who cares?" range.
http://www.naturalspacesdomes.com/dome_store/dome_insulation_systems/Membrain.htm
So, yes, MemBrain is more vapor open than Intello Plus, at any moisture level.
It doesn't really matter what the maximum vapor permeance is, since the ~3-5 perm ceiling paint becomes the limiting factor for vapor permeance whenever the smart vapor retarder is over 5-6 perms. What is important is how the vapor permeance varies at air humidities between 30-50% RH (the healthy-for-humans range) and what it is when the RH goes significantly higher than that.
With MemBrain it doesn't take super-humid air to become more vapor-open than latex paint, with Intello it does. Either are sufficiently vapor open for the ceiling to dry at a reasonable rate if the drying area is 100% of the ceiling area. But in your case with 24" stripes of impermeable radiant separated by 6" stripes of more vapor open area, your drying path has been reduced by 80%, which is what makes MemBrain preferable for this assembly. When 20% of the area is at 5 perms, it moves as much water as 100% of the area does at 1 perm. So if it takes 70% RH for the Intello to cross the 2 perm boundary, with only 1/5 of the drying area to work with that's not a very high drying rate, the same as 0.4 perms across 100% of the area. At 13.2 perms in 100% RH air, the drying rate is like having 2.6 perms across 100% of the area. Unlike MemBrain, Intello permeance would still be the limiting factor for the drying rate. This is important since 70% RH is the threshold of very rapid mold growth, and even at substantially higher humidities than 70% the assembly would still have the drying-rate equivalent substantially less than 1-perm.
A thin layer of cellulose below the roof deck with Spider below doesn't really seem worth the extra trouble & expense. If you're going to do it with Spider / MemBrain / ComfortBoard, forget the cellulose. As long as you ventilate sufficiently to keep the interior RH under 50% in winter you'll be fine. That WSU test wall setup in Puyallup with the fiberglass insulated unventilated stucco clad wall (Wall 2 ) put the MemBrain through a bigger moisture load test than anything you would be delivering.
http://www.energy.wsu.edu/documents/AHT_ComparingTheMoisturePerformance%20Of%20Wood%20Framed%20Wall%20Systems.pdf
The interior RH in that test was kept and 55%, and wall #2 with the MemBrain outperformed wall #7 considerably (same stackup, but with only latex paint, no MemBrain.) While that wall can dry toward the exterior and your roof cannot, but unless you have serious roof leaks the roof deck will never see the extreme moisture drives from the exterior that unvented stucco delivers in foggy-dew Puyallup (or Everett).
As I stated in earlier posts, if the cavity fill were all cellulose you could probably skip the MemBrain. With Spider you would absolutely need the MemBrain, but that's why you have it. Compare the 4C Seattle row, first two columns in Table 3 of this document, all of which only have latex paint as the interior vapor retarder:
http://www.buildingscience.com/documents/bareports/ba-1001-moisture-safe-unvented-wood-roof-systems
You'll note that 1.8lb Spider alone is a moisture disaster for the roof deck independent of roofing color & type, whereas with a dark shingled roof the cellulose insulated roof only hits the warning levels of humidity, and then only if the conditioned space air tracks the high-humidity profile. But with the smart vapor retarder in addition to latex ceiling paint Spider will do just fine. (See the Boundary Conditions discussion beginning on p.7. In fact, read the whole thing- it's fairly short. Most of it is graphics.)
Robert ,
I think yourself and some others may find these pieces an interesting read and quite informative . Don't wanna take this away from the ceiling / roof discussion but I continue to see many questions answered by folks that should not still be hidden .
http://doas-radiant.psu.edu/
http://www.radiantcooling.org/energy.aspx
http://www.radiantcooling.org/radiant-system-forced-air-system.aspx
As far as Jan's designer / engineer is concerned . Rob is certainly one of the best I know and I know all the best . The system for cooling will run around 3*F above dewpoint at all times and latent will be addressed in whichever way Rob determines is best for the specific area where Jan's home is located .
Sorry Dana for not responding sooner. Got busy here.
Impressed with your detailed knowledge and patience. VERY relieved to receive your OK on this roof plus a full WHY.
You are saving us a lot of money with this information. No need to bring in a cellulose installer TWICE, (as we would have to split things up), is a huge money saver. With only Spider we can combine it with other installs in the house which will make things again way easier plus cost effective. Double whammy!
I kid you not when I want to pay you for your time.
It is worth every penny. Is there any way we can arrange this??
And Richard, thank you for confirming the status of our radiant engineer, Rob Brown from Rockport Mechanical, Rockport Maine. He is an equal to Dana in his field. PATIENCE in conveying his expertise to an simple home owner: schmuck me...
Thank you all, Dana Dorsett in particular!
Jan
First and third link "don't work". Well they do but I have to delete a "-" symbol in the .pdf extension after downloading. Cannot find that same document: "WASHINGTON STATE
ENERGY CODE 2009 EDITION" quickly at my first Googling attempt. So maybe re-copy that in for others. Downloading and renaming it, giving it a .pdf extension fixes it though!
Yes, your "considerably arm weaving" remark in a posting in front of the inspector is understood. I'll bring it up with the contractor here and see where we go from there.
WarmBoard supply and return lines will go through the MemBrain. Regardless of your savior solution, we'll be "thinking of you" during the execution, no doubt!!
It is not going to be easy, but it is our only way out.
Thanks again!
Jan
Expect push back from code officials on this, and you may need a variance, since WA State code doesn't exactly allow smart vapor retarders as one of the exceptions for unvented roof assemblies (even though it works pretty well.) Full sheet membrane type variable permeance vapor retarders are still rare enough to not have made it into code, and specifying the parameters sufficiently in code-speak would be difficult, to be sure.
See:
https://fortress.wa.gov/ga/apps/SBCC/File.ashx?cid=1588
http://www.energy.wsu.edu/documents/AHT_Unvented%20attics%5B1%5D.pdf
The full text of WSEC Section 502.1.6.3 starts on page 21 (p 41 in PDF pagination.)
https://fortress.wa.gov/ga/apps/sbcc/File.ashx?cid=1096 (< not that it matters, but you are in WSEC climate zone 1.)
The key to your argument with the code officials is that unlike kraft facers on batts an 8' wide membrane type vapor retarder can be installed in a very air tight, manner, and that it's variable permeance is far greater than that of kraft facers, which is the only commonly used variable-permeance class-II vapor retarder. It's up to YOU to ensure that it actually is air tight, caulking all of the edges to the framing and taping all of the seams, and only allowing seams between sheets where the taped seam is fully supported by framing. If you take those measure and don't rip any holes in it you'll be good for the duration. If you happen to nick it while installing the ComfortBoard or radiant, tape it carefully and hope for the best. It should tolerate a few small air leaks, but not big ones.
Explaining the WSU wall test data from the Puyallup test site may help your argument too, since both the interior & exterior moisture drives under that unvented stucco wall and the higher than wintertime-usual 55% RH interior is higher than you are likely to experience. On p.8 they state:
" Both Wall 1 and Wall 2 had interior vapor control in the winter capable of preventing significant
levels of moisture accumulation in the building cavity. Under the test conditions, the vapor
transport characteristics of the smart vapor retarder allowed a little more moisture through.
This resulted in slightly higher RH and slightly more moisture accumulation in the sheathing in
the winter, day 285 through 50.
In the spring, Wall 2 dried more quickly than Wall 1. The polyethylene vapor retarder included
in Wall 1 prevents the wall cavity from drying to the interior. When the vapor drive is from the
exterior to the interior, as occurs on a warm day, the polyethylene sheathing in Wall 1 prevents
the moisture from escaping. Mid day, moisture frequently accumulates on the polyethylene
sheathing. The MemBrain™ used on Wall 2 allows the moisture to move through the material
when it nears a condensing condition."
The stackup for Wall #2 was:
Unvented stucco | 2-layers of #30 felt | 1/2" OSB | R21 fiberglass | MemBrain | wallboard | latex paint
(The stackups for all assemblies tested are in the matrix on page 12.)
The moisture sensor data for Wall 2 is graphed on p.16, which you should probably study before explaining it to a code enforcer. Moisture content sensor MC3 is mid-cavity on the sheathing and it looks like it peaks at around 17% for a few days around Valentine's day (which is fine.) The only wood moisture sensor with a peak of any significance was the MC1, located near the exterior edge of the framing's top plate, which peaked around 18-20% starting the last week of February, falling slowly through the month of March. That is likely due to wetting from the exterior a problem you won't have given your impermeable roof layers. (What, you mean it sometimes RAINS in western WA during late winter? :-) )
The RH3 sensor (the high red arc) is the relative humidity of the air inside the cavity next to the sheathing and though it goes over 90% during the cold weather, it never hit's saturation. The RH4 (dark blue) sensor is inside the cavity next to the MemBrain. Even though the air on the other side of the MemBrain was maintained at 55% for the test, you'll note that when it's cold outside the RH next to the MemBrain drops into the 45% & lower range (where it's more vapor tight) through the winter. This is because the moisture inside the cavity is being adsorbed into the OSB. But the vapor tightness of the MemBrain at 35-45% RH is sufficient to keep the moisture content sensor for the OSB (MC3) never reaches problematic levels, and dries quickly in the spring. When the OSB is releasing moisture into the cavity RH4 sensor goes above, then below 55% with the weather, and when it's above 55% RH it's fairly vapor open, letting the moisture out into the interior space (the space that is still maintained at 55% for the experiment.) If you keep the interior of your house at 45% RH or lower, the moisture accumulation is slower, and the moisture release is faster, since if the cavity moisture hits 55-60% the MemBrain becomes VERY vapor open, and there is a high vapor pressure difference between from the 55-60%RH cavity air toward the 40-45% RH conditioned space.
Also, compare of the graphs on p.19 of Wall 5, that had kraft faced R13s instead of MemBrain. The sheathing moisture content was above 15% for more than three months, and though it eventually got down to 10%, it wasn't until May, whereas the MemBrain wall had 10% RH sheathing by the beginning of April. This is the difference between using a less responsive (and air-leakier) smart vapor retarder and something like MemBrain. It's understandable why code doesn't allow kraft faced batts in unvented roof assemblies, but also why it arguably should allow smart vapor retarders that have better-controlled characteristics.
What the codes are really trying to prevent is the graphs for Wall 7 on p.21, where the exterior sheathing dwells at moisture content above 25% for most of the winter, and even the framing timbers are moist enough to get moldy or rot.
So, study the argument- you may need it. Hopefully it'll fly without them making you hire an engineer to vet the stackup. But out here in the real world, if you make it air tight with a wide-sheet smart vapor retarder, you won't have a problem, even with zero-moisture-buffering fiberglass insulation.
I won't take your cash, but you can send me a Tesla Model S- or let me ride in yours! ( I'll buy all the gas! :-) )
(edited to delete some control characters that kept it from displaying....)
Just seeing perm ratings for OSB, as that would be the strips of wood to use to fill the 6" spaces between the WarmBoard: http://www.performancepanels.com/permeability .91 for 7/16"
Perm goes up on OSB as it gets wet but we do not want it to get WET. The OSB sitting behind the drywall (5 perms) and than the MemBrain. For the MemBrain to work best would it not be best to leave the OSB totally out and leave an opening there for the connecting PAP lines to cross over to the next WarmBoard panel? 6" space is not that much on the ceiling to have as unsupported drywall.
Or when that is a bit much to have unsupported, that would make the cutting of the WarmBoard in half make sense again, spreading the 6" gaps into double 3" gaps. But leave the OSB out?
Jan
BuildingScience notes that OSB has an average of 2 perms.
Plywood 10 perms...
But nothing remains best?
Wow! And I get accused of over analyzing things?!!!