Spray Foam / Condensation Concerns

I am currently renovating my home in northern Wisconsin (Zone 7A). The house was constructed approximately 50 years ago using conventional 2×4 framing, batt insulation, fiber board (Celotex type sheeting), and hardboard siding.
Due to health issues, the previous owner left the home in poor repair for about 2 years, resulting in some interior water damage and roof issues. I replaced the roof last fall and will be tackling the entire exterior later this spring.
I will be removing all of the existing siding, fiber board sheathing, and batt insulation. My plan was to keep the interior vapor barrier and add approximately 3″ of closed cell polyurethane spray foam insulation (applied from the outside).
Several of the local contractors have also recommended the addition of 3/4″ – 1″ of rigid foam to the exterior studs before sheathing with 1/2″ OSB and 8″ cedar lap siding. While I like the idea of eliminating thermal bridging through the studs, my concern is that there will be an air gap between the two layers of foam insulation (both of which have limited permeability).
In this scenario, wouldn’t I be creating an ideal situation for condensation to form between the two layers? We obviously live in a very cold climate and winter temperatures regularly reach -20 to -30 F.
I know that foam insulation is a heavily debated topic and I was hoping for some insight from some insulating professionals to this particular configuration. The usual phrase …. “we do this all the time up here” …. really doesn’t help me sleep at night!
Many thanks!
GBA Detail Library
A collection of one thousand construction details organized by climate and house part
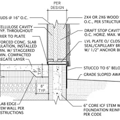
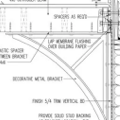
Replies
Gregg,
You don't have to worry about the air gap. Closed-cell spray polyurethane foam is both an air barrier and a vapor barrier, so there won't be any way for interior moisture to reach the gap between the two types of insulation.
imho ... sandwiching an organic surface between 2 vapor barriers is risky ... IF there is absolutely no way for moisture to get in, then it should be ok ... is that truly a reality? Martin, what would you think about a drainage plane between the spray foam & the sheathing? If the spray foam is for insulation and the rigid foam is for thermal bridging, wouldn't that add a fail-safe?
Gregg,
I just re-read your original question, and I now realize there are several questions that need to be clarified.
You proposed installing rigid foam under the OSB sheathing. If you do it that way, the OSB will not be able to provide wall bracing, so you would probably want to install metal strapping for bracing before you install the foam.
If you can manage that, then the only wood components that are subject to the dread "foam sandwich" problem are the 2x4 studs and plates. And the best way to provide at least the possibility that the studs could dry out would be to remove as much of the poly vapor barrier as possible with a utility knife before installing the spray foam. That way the 2x4s could (kinda sorta) dry out a little to the interior -- through their corners.
Thanks to you both. Paul .... that's exactly my concern. The insulator said that he will spray roughly 3" into the existing stud cavity (which is actually 3 3/4" deep due to the original framing materials). Even though both surfaces are both air and vapor barriers, there's no way to guarantee that some moisture will not penetrate the exterior rigid foam. If moisture does enter this cavity, there's essentially a 3/4" dead space for condensation to develop (with little opportunity to dry out).
I should also clarify that the vapor barrier left in place on the interior side of the wall would be the old Kraft paper from the fiberglass batt insulation and not poly (I'm not sure if that makes a huge difference). Since we can roughly attain an R-value of 20, would I be better off limiting the insulation to the spray foam ONLY and then applying my OSB directly to the studs for bracing. We'd obviously lose the ability to eliminate thermal bridging, but one of my initial "motivations" to remove the fiber board was to add some rigidty and strength to the exterior walls.
Also .... if I remove the Kraft paper, won't the foam bond directly to the face of the drywall? In this case, any future modifications or changes would be extremely difficult. The insulator suggested leaving the paper to keep that from happening. Would that also create a problem?
Gregg,
The kraft paper facing can be left in place, since it will still allow the studs to dry to the interior. Kraft facing is better than poly in this application.
I wouldn't hesitate to install OSB (or, better yet, plywood) over the studs, and then rigid foam and vertical strapping to create a rainscreen, if that's what you want to do. Water entry into the stud cavities is unlikely if you have a rainscreen and good flashing, and the wall assembly can still dry to the interior through the studs if there is ever a small amount of moisture in your wall cavity.
I agree with Martin's last suggestion. I would consider pulling the batts and going w/ dense packed cellulose or open cell foam, then structural sheathing, then rigid foam (I keep hearing things about don't go less than 1.5" in zones 5 or higher, but can never find the source of this recommendation). Might as well take the opportunity to upgrade from the fiberglass.
I like the idea of giving a little more drying potential to the interior, but I guess in your climate that probably isn't as much of a concern as farther south.
Additionally, depending on the structural requirements you probably only need structural sheathing in the corners and maybe a couple of other wall panels. So you could run a combination of let's say 2" of foam and then 1/2" sheathing and 1 1/2" foam where shear panels are required.
Chris,
You wrote, "I keep hearing things about don't go less than 1.5" in zones 5 or higher, but can never find the source of this recommendation."
Here's one source: Calculating the Minimum Thickness of Rigid Foam Sheathing
So if I understand everyone's comments correctly (and the article that Chris referenced), I could proceed as planned: remove the existing fiberglass, leave the Kraft paper, add spray foam insulation (leaving a 3/4" air space), add 1/2" structural sheathing (my preference, not necessarily code required), then 1 1/2" of XPS insulation with strapping, and finally my siding. I'm not familar with the strapping procedure - would that entail wood strips? If so, how thick?
Gregg,
Q. "If so, how thick?"
A. Usually 3/8" to 3/4". Search for "vertical furring" on the GBA Web site and you'll get lots of information.
Thanks again, Martin. I think I had it wrong in my last post .... if I need an R-10 on the outside of the structural sheathing, I'd need 2" XPS instead of 1 1/2". That is really going to push my wall thickness out ... more things to consider.
Gregg,
You don't have air-permeable insulation between your studs, so the minimum thickness guidelines for foam sheathing don't apply to you (unless you decide to switch to cellulose between the studs).
As suggested, I've been researching the various vertical furring methods on the GBA website and other threads. As is true with most non-traditional assemblies, the devil is in the details - and in particular - window installation and flashing. I've looked at a number of installation details, including the outset and inset methods that detailed in the REMOTE Wall System model. Obviously, these details apply to a much thicker depth of exterior insulation. If I'm only going with 1" XPS foam, could I "frame" each window opening with a flat 2x4? Then I could install my 1" foam over the structural sheeting and add 1/2" plywood strips for strapping. If this approach is adequate, I assume that I would need to flash over the flat 2x4 framing member and back onto the structural sheathing.
I misread the original question and thought the spray foam was going on the exterior sheathing ... a perfect wall. I am always leary of the foam sandwich, though.
Thanks for the reference Martin. Someone had told me it was in the IECC Energy Code, but I never found it and assumed there must be a different reference guide somewhere.
Gregg,
I would suggest going to buildingscience.com. Look for "designs that work" and also the case studies. They have a lot of good info on various wall types and detailing considerations.
Greg- you got it exactly right when you said the devil is in the details - my concern would be the wiring- particularly the outlets and switch boxes in the wall. Remember that condensation is a function of the differentials- temperature, humidity, atmospheric pressure AND HEAT RESISTANCE of the assembly- the least insulated materials or areas ( ie windows and electrical boxes, in this case) tend to provide an avenue for condensation - and the moisture can come from everywhere- even what soaked into the studs while you were doing this project- or the humidity from the inside accumulating in the outlet itself ( or switch) and into the foam ( only about 1/2" left between the box and the airspace). My biggest recommendation would be to fill the stud space with flexible closed cell, ignore the bridging and move all the wiring and all through wall piping etc to the inside- raised baseboard etc. the standard shim space around wood windows would cause an issue. Think small and aim at a perfect foam insulation with no penetrations.