I have built a home in lower New Hampshire, about an hour north of Concord, using a hybrid insulation system.

The Insulating Contractor recommended 2″ and 4″ of closed-cell foam in the walls & ceiling respectively with the rest of the cavity filled with fiberglass batts. I defered to his “expertise” and had the system installed. After the blueboard was hung, the skimcoat of plaster applied, and allowed to dry I noticed some wet spots on the floor and lower walls that eventually dried. After checking the surface of the plaster with a moisture meter (reading was5%) and the relative humidity in the home was a very dry 35% (indoor temp. 70 outdoor temp 25) I broke a hole in the plaster to further investigate the water stains. There is standing water on the surface of the closed cell foam and the back of fiberglass (where it touches the foam) is soaked, i then spot checked other areas that did not display any signs of water and found the same situation water water everywhere. Any ideas on what caused this problem in a system that the Insulation contractor claims to have used so successfully in the past (or perhaps his other customers just haven’t looked into their wall cavities.
GBA Detail Library
A collection of one thousand construction details organized by climate and house part
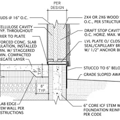
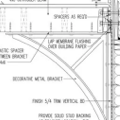
Replies
Rick,
It's possible that your insulation contractor, who promised 2 inches of spray foam, did not achieve a uniform thickness -- and that some of the foamed areas were thinner.
Here's some information on the "flash and batt" system from an article I wrote for the November 2007 issue of Energy Design Update:
Critics of foam-and-batt contend that installing thin foam is risky. For example, Henri Fennell, a spray-foam expert and the president of Foam-Tech in North Thetford, Vermont, told EDU, “It can work, as long as someone does the dewpoint analysis. But there are possibilities for getting in trouble. If you don’t use enough foam, the dewpoint can be in the fiberglass, and the first condensing surface could be on the face of the foam.”
While acknowledging the risk of thin foam, Lstiburek believes that flash-and-batt systems can work well. “The only way you can get into trouble is if the foam isn’t thick enough in a cold climate,” says Lstiburek. “To be safe, use about 1 inch in climate zone 5, or 1 1/2 inch in climate zone 6, or 2 inches in climate zone 7.”
Lstiburek points out that plywood-sheathed walls allow better drying to the exterior than OSB-sheathed walls. “It’s not a problem on plywood or gypsum sheathing, which are more vapor-open than OSB,” said Lstiburek. “OSB is the only sheathing of consequence if the spray foam is too thin in a cold climate.”
Neal Ganser, the president of Corbond, a manufacturer of closed-cell spray foam, agrees with Lstiburek that foam thickness matters. “In the upper climate zones we like to see 2 inches of Corbond with an R-11 batt, and in the severe climate zone” -- northern Canada -- “we’ll do 4 inches of Corbond and an R-19 batt.”
Some builders feel that the these foam-thickness rules of thumb are too conservative. After all, a cold-climate builder who installs 2 inches (R-14) of closed-cell spray foam won’t save much compared to a full-spray job. In fact, some contractors report success using less foam than Lstiburek recommends. Momper, who works in climate zones 4 and 5, uses just 1/2 inch of spray foam. “A half inch is all you really need. Where the stud meets the sheathing, the foam always ends up being a little thicker, so you don’t have to worry about foam popping. We’ve been doing it this way for 35 years. At some of the houses we’ve done, people are gutting or remodeling or putting additions on, and the foam is as good as the day it was installed.”
Asked to comment on Momper’s experience, Ganser advised caution. “There may be somebody in Wisconsin who hears they are doing it with half an inch of foam in Indiana, and he tries it in Wisconsin. But it’s a different world in Wisconsin.”
One cold-climate Corbond installer, Bill Abney of Helena Insulation in Helena, Montana, knows from experience that thin foam is riskier than thick foam. “Starting about 30 years ago, we were doing 1 inch of foam and then a 6-inch batt,” Abney told EDU. “Then we did a job for a homeowner, and a while later, in the spring, he called and showed us where there was about a shot-glass of water running out the bottom of the south wall and the bottom of the north wall. Once we saw that, we said we aren’t doing that anymore -- we’re learning. We started doing 2 inches of foam with an R-11 batt over it. Then about eight years ago, at the home of one of my employees, we did the wall that way -- 2 inches of foam and an R-11 batt. He was living in the house before the sheetrock was installed, in the winter. And there was a period of cold weather when it was getting down to 40 below, and he came home from work, and he pulled the fiberglass back to look at the wall, and he saw a layer of frost on the Corbond. And I know that it wasn’t a wet house -- there wasn’t a lot of moisture on the windows. But the fiberglass was cooling the surface of the foam enough for frost to form. So now we just install three inches of foam and no fiberglass.”
Martin, Thanks for the response. I checked the Spray foam with a probe in many locations and found it to be lacking in many spots, To their credit, the insulation contractor came back and reapplied more foam. I think it safe to say that I have a MINIMUM of 2" in all the walls. I am in climate zone 6. According to your response Mr. Listibureuk recomends 1 1/2". The plaster has been in place and the heat running for about 6 weeks. the walls are apparently not going to dry themselves therefore I will have to remove the blueboard, dry them, check for mold and replaster. Should there be a vapor/air barrier placed over the unfaced insulation? This raises the problem of two vapor barriers in the same assembly. ????? There is more than a trace amount of water in ALL the exterior walls. It seems to me that it is from the copious amounts of moisture given off during the plastering process. Is the hybrid system only useful for a sheetrock and tape application? What steps should be taken to avoid re-introducing the water vapor into the walls during the repair process? Thank You. Rick
I tell you what...
There sure are a lot of experiments gone bad out there.
I think I am almost ready to drink the Riversong koolaid.
Friends should not let friends play with vapor barriers.
Riversong and the Europeans might be right.
Rick,
The "Riversong Koolaid" that John refers to is my insistence on a thermal envelope that can breathe in both directions and hygroscopic insulations like cellulose.
You've gone the more conventional route and that can work as long as you control indoor relative humidity and don't use an interior vapor retarder. But you'll have to wait for warmer weather to re-plaster the walls so the house can be ventilated and dried before the next condensing season.
Rick,
Sorry about being so obscure or making light of your situation.
I have been reading too many horror stories lately.
The flash foam system is flawed in that it does not offer a thermal break over the framing. The plates and studs are the transfer link for the dewpoint temperatures in the stud cavity. The use of a cold side primary air barrier also comes into question.
Good points Doug.
I also have to wonder if the expert foam salesman knew or cared if the walls would have plaster finish.
This looks like one of those not-so-perfect storms.
Doug, we've used flash-and-batt several times with good results. A few questions for you:
Was the framing dry when the plaster base ("blueboard") was installed?
Was it regular blueboard or foil-backed?
Were unvented heaters (salamander, high-hat, etc.) run during contruction?
Have you noticed if the water is more concentrated near the studs, or is it uniformly distributed over the face of the foam?
Is there any correlation between exterior penetrations (windows, doors, electrical outlets or lights) and the water problem?
Are there any other signs of water or moisture issues in the house?