Exterior wall configuration

Hi All,
I am starting to build a home in Minnesota and have been reading all over the internet and on this site about energy efficiency and exterior wall construction/mold issues and have read many of the excellent/expert articles on the subject. I want a solid wall that is going to be mold free in 50 years and somewhat energy efficient at the same time. I would like to implement the following wall configuration if any of you could please comment on it, it would be greatly appreciated:
From interior to exterior:
1. Drywall
2. Polyethylene barrier
3. JM Spider sprayed in fiberglass insulation in 2 x 6 stud walls
4. 1/2 inch plywood
5. Benjamin Opdyke Hydrogap WRB
6. Fiber cement and stone veneer
Is this a good wall? Does this make sense? Do you think I will get a lot of condensation on the inside or outside of the exterior sheathing in the winter in climate zone 5 that wont dry out in the summer?
I am worried about exterior foam for drying to the exterior. I am worried about interior spray foam and the potential VOC hazards with it, don’t want any issues with any offgassing as we have sensitive allergies in the home. Is JM Spyder any better than Fiberglass Batts?
Thank you all very much. I know there are a lot of questions but very much appreciated.
Jeff
GBA Detail Library
A collection of one thousand construction details organized by climate and house part
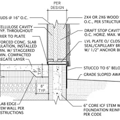
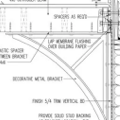
Replies
Sorry that was climate zone 6 i meant not 5.
If you want mold free, I'm not sure you want drywall, polyethylene, and wood. In addition, your proposed wall is not particularly high-performance. There is no thermal break to prevent the studs from compromising the performance of whatever insulation you put between them. And the polyethylene may do more harm than good, especially if you put stone veneer right over your WRB without an air gap. Forget spray foam between studs. It's a huge waste of money and can be an allergy risk if you have any allergy-sensitive people.
If it were me, I would start with a structural masonry core for the wall, like concrete-filled CMUs. Then apply a thin coat of veneer plaster or drywall mud over the interior for the finish surface, and cover the exterior with continuous insulation , followed by a drainage gap, and then freestanding brick or stone cladding. It's simpler, far more durable, much easier to air-seal, and much better for your health and indoor air quality than a sandwich made up of a zillion different layers of wood and plastic that's full of holes and cavities. More expensive, of course, but "solid", "mold-free", "energy-efficient", and "good for allergy-sufferers" are not usually synonyms of "cheap"!
Thank you Nate. That is great advice but I am unable to build with structural masonry stone at this time.
If I have to build a wall with 2 x 6 studs how best to construct it I guess would be my question, from interior to exterior that will be as mold free as possible and also add some energy efficiency. I have read all the posts on this subject and they are all over the place. Maybe I am asking a redundant question but hopefully this can help again all going forward.
Thank you again very much for your answer.
Jeff,
There are lots of problems with this wall.
1. In Climate Zone 6, the 2012 International Residential Code requires walls to have a minimum R-value of 20+5 or 13+10. (The first number refers to insulation between the studs, and the second number to a continuous layer of insulation on the exterior side of the wall sheathing.) Your proposed wall lacks a continuous layer of exterior insulation, and so it doesn't meet minimum code requirements.
2. The interior polyethylene is more likely to cause moisture problems than solve them, because it prevents your wall from drying to the interior during the summer. If you don't want mold, then don't install interior poly (especially if there is any chance that the house will ever have air conditioning).
3. Stone veneer over wood framing and plywood or OSB wall sheathing is probably the most problematic cladding ever invented. This type of cladding has more moisture-entry problems than any other. Lots of other siding types are more likely to be free of moisture problems -- including vinyl siding and fiber-cement siding installed over a ventilated rainscreen gap.
It doesn't meet IRC 2012 or later code min (though it meets current code min in MN.), and lacks moisture resilience without ANY ability to dry toward the interior through the 6-mil poly.
IRC 2012 calls out R20 + R5 continuous insulation for any part of MN (zones 6 & 7)
http://publicecodes.cyberregs.com/icod/irc/2012/icod_irc_2012_11_sec002.htm
By MN code in southern MN (zone 6) R20 cuts it, but in northern MN it needs R21.
http://codes.iccsafe.org/app/book/content/2015_Minnesota/Residential/Chapter%204%20%5BRE%5D.html
Spider will get you there, but it's not a very high performance wall at about R15 whole-wall (after factoring in the thermal bridging.)
To get the performance up to what would be at the higher IRC code-min in zones you could add rigid rock wool sheathing in the masonry cavity, which would also keep the sheathing warmer & drier:
http://www.roxul.com/files/RX-NA_EN/pdf/Technical%20Bulletins_Guides/13A08%20ROXUL%20COMFORTBOARD%20IS%20Application%20Guide%20-%2004-11-2014.pdf
http://www.roxul.com/files/RX-NA_EN/pdf/Brochures%20and%20Sell%20Sheets/Building%20Envelope/ComfortBoard%20CIS%20Eng.pdf
At 1.25" you'd hit the R5 continuous insulation spelled out in the IRC, but it's fine to go thicker.
Rather than plywood, which is a 0.5-1 perm vapor retarder on the "wrong" side of the assembly, you could use structural 3/4" asphalted fiberboard, which is 5 perms when bone dry, 15+ perms when the humidity levels are high, which allows the assembly to dry into the masonry cavity. Fiberboard is less susceptible to moisture than plywood and lets moisture out, which makes the whole assembly more moisture-resilient. It's also about R2, which means you can back off to 1" on the rigid rock wool and still hit IRC code min performance.
Then you can use a "smart" vapor retarder such as Certainteed MemBrain or Intello Plus on the interior side under the gypsum, which is a class-II vapor retarder when dry (under 1 perm), but becomes vapor open allowing the assembly to dry when the relative humidity inside the fiber layer becomes high enough. Alternatively, half-inch plywood or OSB also behave as smart vapor retarders, and if you put it on the interior under the gypsum it becomes the structural sheathing, allowing you to use thinner less-structural fiberboard sheathing facing the masonry cavity. Most fiberboard is sufficiently structural to use as exterior sheathing on it's own, but it's not as strong as CDX or OSB.
http://www.fiberboard.org/index.php?option=com_content&view=article&id=54&Itemid=60
With fiberboard sheathing and a smart vapor retarder on the interior side, the assembly can dry in either direction, and it won't load up with moisture in the winter. With 1-perm CDX and 6 mil poly (about 0.05 perms) the winter moisture drives are controlled, but it has very limited drying capacity, and has more moisture-susceptible sheathing in the colder-wetter side of the assembly.
Spider has about the same performance as PERFECTLY installed R21 fiberglass batts, slightly lower performance than perfectly installed R23 rock wool. But perfection is hard to get with batts- there is always some voids & compressions, whereas with Spider there are none.
Whatever you do for insulation, the cheapest wall performance you can buy is to meticulously air seal the house. With studwalls this means caulking the framing to the sheathing inside every stud bay, caulking under the bottom plate, and between doubled up studs/headers/top plates. With a powered caulking gun and the appropriate purpose-made caulks (ProPink, EcoSeal etc.) it goes pretty quickly. Sealing all electrical & plumbing penetrations of the framing with can-foam is also part of the protocol. Not only does air leakage drive energy use (a well insulated wind tunnel is expensive to heat at any R-value), air leakage is a much bigger mover of moisture into studwall assmblies than vapor diffusion through latex painted walls (or 1/2" plywood/OSB.)
Why do you need to use 2x6s? Have you already bought the material or something? There are many, many ways to build good walls. If for some odd reason you have to use 2x6s, you need to make sure your walls' drainage is as good as possible. That means half inch or deeper air channels behind the cladding, it means selecting a cladding that's not a moisture reservoir (e.g. stucco, brick, or stone) unless it's a freestanding wall physically separated from the rest of the wall such that bulk moisture can easily drain down through the bottom. As martin said, it's hard to choose a worse wall from a moisture management perspective than adhered stone veneer over sheet goods (at least you're thinking of plywood instead of OSB!). The Hydrogap WRB you've chosen would be virtually worthless; the air gap it creates is only 1 millimeter, and the little rubber nubbins are compressible. The mortar touching it would create zillions of points of contact with the sheathing behind it, allowing water to wick right into the plywood. It's no substitute for a real half-inch-or-greater air gap.
You should read these:
https://www.greenbuildingadvisor.com/blogs/dept/musings/all-about-wall-rot
https://www.greenbuildingadvisor.com/blogs/dept/musings/all-about-rainscreens
FWIW: If you went with 3/4" fiberboard sheathing and are in zone 6, not zone 7, with a rainscreen gap behind the siding you wouldn't need the interior smart vapor retarder, or the 6-mil poly. Latex painted wallboard would be sufficient:
http://publicecodes.cyberregs.com/icod/irc/2012/icod_irc_2012_7_sec002_par025.htm
Thank you for the responses.
I do have to use 2x6 because my builder does that for all his homes.
So in taking it all in does this sound better:
1. Drywall
2. Membrain from CertainTeed
3. Spyder in 2 x 6 (or do you recommend something else in 2 x 6 stud bays
4. 1/2 inch or 5/8 inch plywood (i have to use this for exterior sheathing vs OSB, I assume plywood is better)
5. Tyvek (or is there a better WRB)
6. Furring strips (does 1/4 inch work?)
7. Fiber cement is along most of the walls with stone veneer along the bottom mainly. I would like to use foundational stone but this appears to cost so much more.
Thank you all again.
And of course the air sealing with calk that was mentioned inside the stud bays.
How about getting a new builder? It sounds like he doesn't know how to build the kind of house you want.
Jeff: do you really want to spend hundreds of thousands of dollars on a lousy house just to avoid upsetting your builder?
Jeff,
I think that the reason that a couple of GBA readers are urging you to reconsider your fixation on 2x6 walls is that one good option for cold-climate builders is a double stud wall consisting of two parallel exterior walls framed with 2x4s. This gives your insulation contractor plenty of room for lots of insulation.
If you insist on framing with 2x6s, the performance of your walls can be improved by including a continuous layer of exterior insulation (usually rigid foam).
Jeff, I've also found myself in a similar position getting overwhelmed by the multitude of advice and recommendations for efficient framing and insulating options. We're planning to build in the upcoming Spring in N. Oakland county Michigan climate zone 5. I've been researching since we bought our property in Jan 2014 and am still going back and forth in making a decision. Problem is, once I think I've figured out something I like, there is an article or comment that steers me away. I've also circled back to a few building methods I initially dismissed. Its easy to get discouraged, especially from some of the comments in this thread thinking your builder and his methods are inferior. But, what you have to realize is that all of these energy efficient options eventually come to a point of diminishing returns. We just have to decide what is the most important factor that will result in the greatest return on investment and will bring the most comfort to you. From what I've gained from GBA, its the air sealing that is the number one priority, followed by insulating and reducing thermal bridging.
Here's my two cents:
1. I've come across these Hammer and Hand guys (http://hammerandhand.com/) that build energy efficient homes out in Seattle. They have videos on youtube as well. What I liked most was their use of a fluid applied WRB. They like to use Prosoco products like Cat 5 to both waterproof and airseal from the outside - looks a little simpler than to worry about a staple up or peel and stick WRB and helps avoid all the caulking of joints from the interior.
https://www.youtube.com/watch?v=jyI39ykbsSM&index=7&list=PLgsMdVoGy9slnDUdOzcIXllG-SwwbKtrg
https://www.youtube.com/watch?v=vV3DbVDg83E
2. Also, check out this REMOTE building method. Martin talked about it in an earlier post as well. It involves making the exterior sheathing your air barrier with all your insulation on the outside. I'm leaning towards this idea using roxul rigid mineral wool insulation.
http://cchrc.org/docs/best_practices/REMOTE_Manual.pdf
@Martin,
"I think that the reason that a couple of GBA readers are urging you to reconsider your fixation on 2x6 walls is that one good option for cold-climate builders is a double stud wall consisting of two parallel exterior walls framed with 2x4s. This gives your insulation contractor plenty of room for lots of insulation."
Good point. One fact that attaches to this advice is not to even think about this type of construction if you do not have insulation contractors locally that are accustomed to this type of construction. If you do not then don't think about this type of construction. In many ways the contractors that are available locally will end up determining the type of construction. That's just the way it is. This also applies to ICF. If there is not the expertise locally to do a particular kind of construction then you can't do it unless one takes on the project as a DIYer. So be forewarned.
The 2x6 MemBrain / Spider / plywood / rainscreened wall is about as good as it gets for a MN code-min, but it's still just code min, and BELOW IRC 2012 code min. The fact that it's below the IRC code min is a bit at odds with the stated goal of:
"I want a solid wall that is going to be mold free in 50 years and somewhat energy efficient at the same time."
With plywood sheathing drying into the rainscreen and MemBrain on the interior the mold free goals are met, but the "...somewhat energy efficient..." part isn't quite there. The stackup described is an ~R15 wall after factoring in the thermal bridging, adding in the R-values of the sheathing, wallboard and air films.
An IRC code-min wall for US climate zones 6 / 7 is an ~R20 wall with 25% lower heat loss. Taking it to the IRC code min could be construed as "...somewhat energy efficient...", but not sticking with MN code min is clearly substantially less energy efficient. The ~R15 wall is what would be IRC code min in US climate zone 3 (most of GA, AL, MS), and pretty lossy/skimpy for your zone 6/7 climate.
Taking it higher than IRC minimums is still financially rational on a lifecycle basis in most cases. An inch of rigid rock wool on the exterior of the sheathing would improve both the mold-resistance and the energy performance of that wall, and would also be pretty close to the IRC code-min. At 2" with the exterior rock wool you'd be in the "...somewhat energy efficient..." by almost anybody's definition, though far from super-insulated, and well behind even what would it would take to be "Net Zero Ready" in your climate.
Plywood is indeed better than OSB in the respect that it becomes more vapor permeable more rapidly with rising humidity, but it's nowhere near as good as fiberboard from a drying capacity point of view. Reluctance to use a less-rigid sheathing such as fiberboard is understandable, but incorporating cut in bracing or plywood shear panels on the corners can provide the necessary rigidity to meet any structural spec if that's the primary concern. Fiberboard is far more moisture resilient than plywood or OSB, (you don't even have to store it inside!) and has more than 2x the R-value of plywood at any given thickness. It's more commonly used in the humid swampy parts of the southeastern US than the upper midwest (in part due to it's moisture resilience), but it's mature product with a good track record under masonry claddings. Changing to fiberboard sheathing would be enhancing both the mold free and energy efficiency goals.