I am overwhelmed with the wall cavity options and need advice

After researching for the last few months on this website, buildingscience.com, and PHIUS.org I am just overwhelmed…buy maybe under informed. I am an owner/builder (former construction project manager…mainly responsible for foundation and electric work then) and this will be my second house. Most of the case studies and articles I have read are about homes in climate zones far more extreme than what we typically have in TN. I read about double stud walls, larson trusses, swedish framing, Riversong trusses, vapor barriers, smart vapor barriers, WRB’s, and rain screening…till I’m blue in the face.
I’m on a tight budget, using crews that are’t used to doing things right (it’s TN…labor is cheap, energy is cheap, and the climate is not extreme…except the last few weeks). I’ll be onsite quite a bit to confirm things are going to plan and likely do a lot of the sealing myself. To make it as easy as possible on my framing crew I’d like to build my wall assembly one of three ways. 1. Frame with 2×8’s, seal everything with acoustical sealant, insulate with roxul, sheathe, cover with tyvek, use furring strips and cover with hardiplank. OR 2. double stud wall, 2×4 wall, 3.5″ gap, 2×4 wall, again seal all with acoustical sealant, probably use 3 layers of fiberglass batts for insulation, sheath outer layer, cover with tyvek, use furring strips, and cover with hardiplank. OR 3. 2×4 wall 16″ OC, sealed same as above, sheathed w/tykek, on exterior side offset a 2×4 furring strip from OC framing on interior side…so there would be a 2×4 every 8 inches, one on one side of the sheathing, then one on the other. I would use R15 roxul. I know I can use furring strips on top of roxul boards, but I’m nervous about detailing around windows and doors when I (nor anybody around here) has done it before…at least no one I can find.
My preference is option 1. With the exception of advanced framing it’s a pretty typical wall, but with the extra depth, sealing, and roxul it should preform much better. I’ve read some about about insulation only on one side of the sheathing…but again all I’ve read is in much colder weather climates. I’m too confused to decide and can’t afford a consultant. It is a single story structure so I can advance frame with 2×4’s or the 2×8’s either. Any input would be appreciated.
GBA Detail Library
A collection of one thousand construction details organized by climate and house part
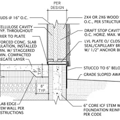
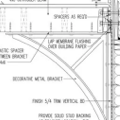
Replies
Andrew,
Option 2 (the double-stud wall) is by far the best of the three options.
A 2x8 wall doesn't make much sense, because of the thermal bridging through the studs and because of the high cost of 2x8s.
For an in-depth discussion of 2x8 walls, see Choosing the Right Wall Assembly.
I read "Choosing the Right Wall Assembly" and several other articles linked from it or succeeding articles and I think I understand a bit more both about double stud walls and single walls with foam. In regards to my double wall and reducing the "cold sheathing" risk...I already plan on using rain screen technique under my hardiplank and Tyvek under that.
Now I have two more questions. 1. Should I upgrade the north facing wall to plywood from OSB? 2. Should I upgrade the insulation from fiberglass to roxul batts?
Thank you
Andrew
Ah...thought of a third one...if I stay with fiberglass do I am planning on unfaced for the two outer layers and kraft faced for the third layer up against the sheetrock...or should that be unfaced as well?
Andrew,
Q. "Should I upgrade the north facing wall to plywood from OSB?"
A. It's your choice, of course. However, research has shown that plywood survives repeated wetting and drying cycles much better than OSB.
Q. "Should I upgrade the insulation from fiberglass to Roxul batts?"
A. Again, it's your choice. Many green builders prefer to use mineral wool, which is stiffer and somewhat denser than fiberglass batts. But either product can work well if conscientiously installed. The problem is that batts are rarely installed well. All of the typical mistakes made when installing fiberglass batts can (unfortunately) also be made when installing mineral wool. For more information, see Installing Fiberglass Right.
Andrew,
Q. "If I stay with fiberglass, I am planning on unfaced for the two outer layers and kraft-faced for the third layer up against the Sheetrock...or should that be unfaced as well?"
A. Either way will work. The important thing is to pay attention to airtightness when installing the gypsum drywall -- especially at the electrical boxes.
If you're going to build a double-stud wall, just fill it fulla cellulose. That will probably wind up being way cheaper than using mineral wool, and it will protect the sheathing somewhat from moisture by wicking it away into itself; mineral wool won't do that.
Using the savings to upgrade to plywood sheathing everywhere. Cheap insurance.
The "best" place for sheathing in a double stud wall is the outer face of the inner wall! with this location it will serve as the primary air barrier and be sealed accordingly, since it will never be cold it can be OSB. I'd definitely choose mineral wool over fiberglass, as it's much more likely to be installed better, due to it's rigid, must be cut to fit, mature. With the sheathing on the outer face of the inner wall creating an insulated service cavity eliminating the need for sealed drywall, and the outer walll becomes free standing "furring" to support the siding and easily installed "outie" windows installed in plywood ( or even better Thermoply) "picture frames" to complete the air barrier. The downsides: it's unconventional, requires installing insulation from the outside, essentially forces the inner wall to be the primary load bearing structure..
Almost all of TN is in US climate zone 4A (except for the SW end which climate zone 3A). For a sanity check on bang/buck, take a look at Table 2 p.10 of this document:
http://www.buildingscience.com/documents/bareports/ba-1005-building-america-high-r-value-high-performance-residential-buildings-all-climate-zones
These are "whole wall" R values, with all of the thermal bridging factored in, not center-cavity R. At R25 and up it may become a "pays never" if you make it too complicated. Getting to R25 whole wall with a double studwall is possible, but it's making it much more complicated than it needs to be. Trying to get a perfect fit with three layers of batts with no voids or compressions in a double-studwall with "....crews that are't used to doing things right..." seems like utter folly, guaranteed to fail. It's simpler and more reliable to get there with exterior insulation, with only one set of stud cavities to inspect & correct the batt installation on.
Plan A: A 2x6 24" o.c. wall with some advanced framing features, wood or fibercement clapboards and R23 rock wool comes in at about R15 after thermal bridging. With 2" of exterior foil faced polyiso (or 3" of rigid rock wool or 3" of EPS) over the sheathing it brings that up to R27. If you used open cell foam, cellulose or R21 fiberglass instead of R23 rock wool you'd be at about R26, a loss of about R0.8.
Plan B: A 2x4 AF studwall with R15 rock wool comes in a bit higher than R10. Add 3" of exterior polyiso (or 4" of rigid rock wool or EPS) and you're at R26-R28. Changing to R13 fiberglass or cellulose or open cell foam only reduces the the whole-wall performance by about R0.5.
Plan C: The 2x8 24" o.c. AF wall with R30 rock wool cavity fill would only come in at ~R20, but if you used 1" SIS sheathing instead of plywood/OSB you'd be at R26.
Three wall stackups of similar performance, with a higher likelihood of hitting your performance goals if using batts.
For higher performance walls a double-studwall approach might make sense, but rather than three layers of batts, use rigid foam (seams taped) between the studwalls. eg. a 2x4 + 3" polyiso + 2x4 wall comes in at about R35 whole-wall, but you have to pay attention to the thermal bridging of the subfloor & floor joists, which become relevant in high-R walls. In an exterior insulation approach the exterior insulation would thermally break the band joist, foundation sill, & subfloor, which also protects the band joist & foundation sill from wintertime moisture accumulation.
Dana,
Have you priced 3" of polyiso? Or rigid mineral wool boards? Mineral wool bats are a comparative bargain that cost less than half of the board alternatives for similar r value . Any exterior sheet insulation requires exterior furring to attach the siding, adding even more cost and risk due to crew competence. It's much simpler to use an unsheathed outer wall as the furring, fill it with low cost bats and fill the space between studwalls with more low cost mineral wool bats. Putting the sheathing on the outer face of the inner wall allows it to be "detailed" as an outstanding, long lived air barrier. . For the mild climate of Tn using two 2x4 walls filled with r15 bats and a 2 1/2" inter-wall spacing filled with r10 mineral wool could save a few$ and still result in a whole wall well over r25 even with allowance for some installation mistakes.
I am building in TN. I am also concerned about the poor quality of workmanship here ("Always done it like this, no one complained yet") and I am especially concerned about mold (seems like 90% of the houses I've looked at here have moisture issues).
I have decided to use 2x4 framing with plywood sheathing, liquid-applied membrane, stud bays filled with dense-packed cellulose, and EIFS over 4" of foam on the exterior. Nearly R-29. I see a lot of EIFS around town, especially on commercial buildings, so I am not asking for unknown work processes. The extra inches in exterior foam will increase costs by only the material cost. I am also providing almost 4' of overhang with deep eaves for the protective factor against rain and sun (hip roof, so eaves all the way 'round), and the structure is a simple rectangle with only one extension.
I am adding extra hold-downs and hurricane ties to increase the wind resistance by almost 50% for very little extra $.
From my projections, I will be getting a lot of bang for my bucks, and using common practices that will not test the skills or patience of local trades. The air sealing I will attend to personally.
Dana, In my double stud wall I'd have three layers of R15 batt...either fiberglass or roxul. I dare say that I would have in excess of an R25. One of the options I had initially was sheathing sandwiched between two walls with R15 Roxul on each side. The double stud wall eliminates thermal bridging, the sheathing between two walls minimizes it. Either way between the insulation, sheathing, tyvek, and sealing I'm over R25. Holladay says the double stud is the way to go...so...I'm probably going to go double stud.
David, I'm in the Lenoir City area it would be good to get together and compare notes. There's lots of stuff to work out besides walls. Vapor control and insulation in crawlspace, roof/ceilings, etc. I don't find a lot of articles that address our climate specifically. If you would like to compare notes I can be found on facebook or linkedin.
Ignoring the thermal bridge at the subfloor and band joists, figure about R9.5 each after thermal bridging for the 2x4 framed walls (including the siding, sheathing and wallboard), R15 for the continuous layer in-between, which is about R32-sh performance.
It's actually a bit less due to the thermal bridging at the subfloors & band joists unless you do something there too.
This presumes PERFECT installation of the batts on all three layers, with no compressions, voids, gaps, etc. which is
A: hard to inspect...
....and...
B:... hard to do, especially for "...crews that are't used to doing things right."
It can be done, but you're more likely to get a satisfactory result if you use blown insulation instead.
Compare notes on the different approaches (including whole-wall-R, clear wal-R, and rim joist R values in Table 3) in the analysis found in this document:
http://www.buildingscience.com/documents/bareports/ba-0903-building-america-special-research-project-high-r-walls
Case 2b is analgous to my "Plan -A" exterior foam proposal, but with slightly higher exterior R but lower cavity-R.
Case 10 is as close as it gets to the pair of 2x4 walls w/ 3x R15 batts, but it uses 2" of closed cell foam on the inteiror side of the sheathing to protect the sheathing from interior moisture drives. The center-cavity R is comparable to your wall. Figure 49 shows the thermal bridging issue at the subfloor & band joist, which is part of why the whole-wall R is only ~R32, despite a center-cavity R of about R40.
The rim-joist R in case 10 is only R16-ish, compared to R29 for case 2b, the foam-over- the achilles heel of the approach. If going double-studwall, think carefully about what you are going to do at the rim joist and foundation sill to improve the whole-wall performance.
Jerry: Yes I've priced 3" polyiso, not so much 3" rigid rock wool. In my neighborhood I can get used-once reclaimed 3" roofing polyiso from multiple vendors for about the same cost per square foot as R15 rock wool batts. Assembly labor wise a 3" foam-over is pretty simple, but there may still be learning curve issues with the labor pool as-described.
I too am building in Tennessee (Franklin). I'm going with 2x4 wall with R-15 insulation and 1.5" insulated Zipp panel. That should be about a 21 calced r value. Not sure what whole wall would be. There's plenty of experience with Zipp in our area and of course, 2x4 walls. I'd suspect there is zero experience with double walls.
I know most here would say that's not going far enough, but chasing that next R gets expensive quickly in my parts.
Dana Dorset...what is an AF wall?
AF...Advanced Framed...sorry, not thunking clearly.
Safe from moisture problems using double stud walls... I agree with Jerry, using OSB in the middle of the wall makes sense and would be easy to construct for any crew.
One thing to remember for all of us here at GBA, is that any of us will build with high regard to doing the work right, so I would think any of us will install batts very well. There should be no need to caution any one away from the use of batts. I have done every phase of building a home, and I can tell you installing batts perfectly is about the easiest thing to do in construction.
Try to avoid foam. At this time I see using used foam as smart and or using new foam under slabs as smart and possibly using foam for the rim joist though there are other ways to take care of the rim joist.
Cellulose for attic floors
batts in well sealed stud walls should work very well.
Air seal the home, the wall sill plates before lifting in place, the rim joist as constructing. Basically seal up every joining of materials between inside and outside, between inside and basement, between inside and attic.
Deal with doing top notch metal duct work for bath venting, kitchen venting, dryer venting. Afraid of dryer vent fires then use gas style double wall B flue to duct the dryer as it is designed to have a fire exhaust in it. Seal up with roof gaskets items that pierce your sealed up home.
Panasonic bath fans are great. If needed add some passive vents for air to enter the home. I prefer using something called a window. I like windows, though to save energy and money use more fixed windows, they all don't need to open. Overhangs are good things on homes, wide overhangs. If you live in a rain forest use rainscreening, strapping under the siding. For my area the north side needs special attention for mold and moisture. the south and west sides need porches to deal with too much sun exposure. Build a home long length east to west. Put small window bathrooms on the north side and views on the East and South sides. Master bedrooms are nice on the north east side so the morning sun streams in to wake you and greet you in the master bath too. heated tile set to come on before waking is so nice in the bathroom and even the kitchen. Electric heated tile in those areas can work well with two mini splits, one up one down, one will heat and one will cool. Both will work for the extreme days. A small woodstove for power outages and ambiance and a glass of wine after skiing or snow shoeing. Plant fruit trees for the blossoms and the fruit and the shade possibly, cut down the trees that are too close the home.
Don't build a home out of a Quantset hut, shipping container or whatever. Shipping containers do make great shipping containers and also great storage areas for hang gliders. Go hang gliding, surfing, skiing, scuba, sky diving and go dig a well for a village in Africa.
Take a day off to do nothing but enjoy the day and being.
I just did some estimates on different types of wall assemblies breaking them down to cost per sf and dollars per R value. It was very interesting that a typical 2x4 wall with R13 fiberglass batts (though it is the cheapest to construct) actually had the highest $ per R value. Costs were figured for a 10x10 section of wall and then broken down to cost per sf. This is for material only. I'd add cost for walls wrapped with roxul boards, but I am having trouble finding prices.
forgot the attachment
Andrew,
We just recently finished a house in Upstate SC where we were heavily involved in the construction. I am a big fan of Roxul as an insulation material in the south (where, as you noted, the crews are not used to doing things right) because of its density, fire resistance and insect resistance.
We first built a shop with 2 x 6 walls and insulated with mineral wool (not Roxul though). The installers did not do a great job. In fact, David Meiland called it "a typical low quality install". We had to make them come back and reinstall some it because it was so compressed, but the building works amazingly well. My brother leaves the heating and air off most of the time and it holds the temperature really well despite that. So what I'm saying is that even with a poor installation, I think it works better than fiberglass largely because of the density of the insulation.
See this post - https://www.greenbuildingadvisor.com/community/forum/energy-efficiency-and-durability/22755/installation-mineral-wool-insulation-shop
You can meet with your subs BEFORE you start the building to emphasize that your priority is building a energy efficient home, not just a building to code. I don't think the crews (that I've experienced) get it though. I've worked with my carpenter for several years on several projects and he will still say to me, "But a building has to breathe" ARGH!! And that is after many hours of discussions. He is extremely proud of my brother's house and is beginning to get the fundamentals of air sealing and insulation because he sees how beautifully the house works.
The other thing you have to do is be on site as much as you can. You have to talk to these guys. If you have a big crew working for you they will finish things so fast, you don't have time to intervene if they do something wrong. How fast does a framing crew frame a typical house? A few days, a week at most? We had 2 guys basically building my brother's house over several weeks and if they did something like framed some corner so that there was a void in the wall that was very difficult to insulate, I made sure they filled it with insulation before it was inaccessible.
So what I am saying is that more important than choosing a design or a specific material is the quality of the installation - preventing as many thermal bridges as possible (an old style carpenter wants these spaces around windows and doors filled with wood), insuring complete air sealing, and seriously good installation of whatever insulation you choose.
Still I am a fan of mineral wool as exterior insulation to reduce thermal bridging. My guys installed that beautifully. We did foam around the windows so we could tape better. See this post on my blog.
http://greenvillegreen.blogspot.com/2013/10/cozy-mineral-wool-sweater-on-house.html
I hope that helps a little bit.
And your a biker too!! That's great. I will be on site most of the time and actually do have a good crew that is on board...at least the owner of the business is...we'll see about the crew once we start.
Have you ever thought about one of these for your "caulker's elbow?" http://www.zoro.com/i/G7418537/?utm_source=google_shopping&utm_medium=cpc&utm_campaign=Google_Shopping_Feed&gclid=Cj0KEQiA4OqnBRDAj9aazvPji9ABEiQANq28oO7uOwRFYaceQlbT_UWfsI67rmJzVWaa_fIFq2zHedUaAiYO8P8HAQ
Mostly I used to be a biker. I will be again when I transition out of my job in the ER in the next 2 years (it's too hard when you get older).
With your crew, the person you have to get on board is the head carpenter. When we did our first blower door test, he was as nervous as I was. The owner wants to please you, but that person isn't around all the time. You've got to get buy-in from the head guy (assuming it's a guy), that's there everyday. That person is your eyes and ears on site.
Yes, the cordless caulk guns are very appealing. When I start the next big projects (2 full gut kitchen renovations - my house and a rental house) I really do need to get one of those.
Andrew - I like the idea of the double stud- Roxul 3 layer-sheathing in the middle as air barrier approach. Cellulose is "Greener" but I'm not sure it's as "resilient" as Roxul. Like if the wall ever does get wet in a fierce hurricane or tornado, or if someone remodels down the road. Consider "hanging the second floor joists off the inside of taller studs on the outer wall to reduce thermal bridging.( Rim joist would be inside the two walls). Air barrier is now well protected, and doesn't undergo wide temperature swings which would render the taped joints more longstanding I would think. Foam would also work well between, both as insulation and your air barrier, but I'd prefer Roxul and plywood to foam, even though the foam here is probably cheaper( assuming the in the middle plywood is your second layer of sheathing). Good luck with your project.
I'm with Nathaniel G on this one... every other option discussed here is MUCH more complicated, and I understand completely how you feel overwhelmed.
" If you're going to build a double-stud wall, just fill it fulla cellulose. That will probably wind up being way cheaper than using mineral wool, and it will protect the sheathing somewhat from moisture by wicking it away into itself; mineral wool won't do that. Using the savings to upgrade to plywood sheathing everywhere. Cheap insurance."
Study the Shirley wall and roof: search Shirley here on GBA
Some folks believe that it may have risky condensation potential. I don't. I believe that an excellent air and weather barrier properly installed eliminates the condensation issues seen in the past.
As a bonus, the construction of the roof /ceiling assembly is exactly the same as the wall, just thicker.
If going the double-studwall approach I'd be inclined to do it in cellulose too, but I wouldn't put an impermeable WRB on it when there are so many other good options for air sealing that don't block drying toward the exterior. While that much cellulose would likely have sufficient buffering to protect the sheathing from interior side moisture drives, if you used rock wool it would raise the overall risk (unless you used a smart vapor retarder on the interior side.)
Air leakage from the exterior is never the cause of wintertime moisture accumulation in sheathing- if anything it helps dry that sheathing (albeit at an energy use cost. If you're going to have an ultra-low permeance layer in a high-R wall in a zone 4A climate putting it in the middle or toward the interior, not on the exterior.
Air leakage into the cavity from the INTERIOR is a known cause of wintertime moisture accumulation in sheathing, but air-sealing the exteririor doesn't much affect how much conditioned space air gets into the wall cavity.
An unvented cellulose roof in zone 4A without a class-II (or tighter) vapor barrier on the interior would be a code violation, and even dense-packed cellulose would carry a long term risk. An interior side smart vapor retarder (or a vented attic) would be the right solution there. All-cellulose unvented roofs can be fine with just latex as the interior vapor retarder works in climate zone 3 (or lower), and that's about where a low permeance WRB like Grace Ice & Water would be OK too.
http://www.buildingscience.com/documents/bareports/ba-1001-moisture-safe-unvented-wood-roof-systems
I've read several places the suggestion to put the sheathing on the exterior of the interior wall, but what keeps the insulation in place or from getting damp if you do that (with dense back cellulose..I'm not doing foam boards)? I've been planning on using this wall...2. double stud wall, 2x4 wall, 3.5" gap, 2x4 wall, again seal all with acoustical sealant, probably use 3 layers of fiberglass batts for insulation, sheath outer layer, cover with tyvek, then vinyl siding. However, after reading a couple more articles on the "perfect wall" I have a second option. Option 2: (from interior) 2x4 wall, intello smart membrane on outside of wall, netting for cellulose, 9.5" I joist as a larson truss, sheathing, tyvek, siding (fill larson trusses with cellulose and leave 2x4 walls open for chases. (possibly back fill open areas with more insulation (fiberglass). Thoughts? I have a feeling the double stud wall would be the least expensive.
Andrew,
Sounds like a variation on the Klingenberg wall. More information here: The Klingenberg Wall.
Q. "I've read several places the suggestion to put the sheathing on the exterior of the interior wall, but what keeps the insulation in place or from getting damp if you do that?"
A. I don't understand your worry. What is the origin of the moisture that you think will cause this dampness?
I just read the Klingenberg article. I think what is left out of the discussion when sheathing is in the middle (or on interior as in the Klingenberg wall) is suggested is that there is still sheathing on the outside, but it's more permeable fiberboard sheathing. With no sheathing a blowing rain or humidity could get right behind siding (vinyl, hardiplank, or otherwise). If cellulose is used and all there was was the netting to keep in place I would think bad things would happen (netting could break down over time releasing cellulose.) I could see if one were using roxul that deals well with moisture maybe you could install it and then the edges of your larson trusses or 2x4 become your nailing surface (ala Riversong)...however I think Riversong uses shiplap siding doesn't he...right over cellulose.
I think my original "Option 2 double stud wall" will be fine in my climate. I'll use plywood sheathing on the northside and tyvek for a cost effective WRB. Building science research over a three year span actually found, " when the walls were disassembled at the conclusion of the experiment, the sheathing and framing showed remarkably little evidence of wetting damage or mold growth. No visible mold growth was found, nor evidence of staining or water rundown. The damage was limited to some grain raise of the interior surface of the OSB at the cellulose wall, and corrosion of fasteners." http://www.buildingscience.com/documents/bareports/ba-1501-monitor-double-stud-moisture-conditions-northeast/view
I'm in a much more moderate climate so I think I'll get a substantial R-Value, low cost to build, easy instructions for my subs, low energy bills, and once we get it built and out of this drafty 70's bi-level rental a happier wife.
Andrew,
Every wall needs a water-resistive barrier (WRB) behind the siding -- even a Klingenberg wall. The WRB keeps the insulation dry.
For more information on WRBs, see All About Water-Resistive Barriers.
Ah yes, I mentioned Tyvek in several options, but kind of forgot about it when thinking of the larson truss option. My budget is likely a vinyl siding budget. I think I'm just more comfortable with wood (or something solid) behind vinyl siding. Riversong doesn't use sheathing, but shiplapped siding effectively is sheathing and siding. I don't think I've ever seen a wall detail with cellulose right next to tyvek and then siding other than his variation. I've seen all sorts of board insulation right before siding, but as you mention every wall needs a WRB and that is typically below the board insulation.
Have you ever seen a cellulose, tyvek, siding combo without either board insulation or sheating before the siding?
Thanks for all the input by the way.
Robert Riversong builds high-R cellulose walls without structural sheathing, using deep roof overhangs of at least 1' per story (to minimize direct wetting from the exterior) and horizonal shiplap siding. So far, so good, but we don't have decades of experience on those houses yet.
Without a capillary break (like a rainscreen gap) between the shiplap and the cellulose seems pretty risky to me though. YMMV.