Stopping log home heat loss

Built the dream log home and now face the heating nightmare in Climate Zone 7. A masonry heater reduces the heating load of my in-floor heating system by half but without it my heating bills avg $500/mo. Here is my wild idea to reduce heat loss:
1/2″ or 1″ rigid foam against interior of perimeter log walls
Log siding nailed against rigid foam
I am thinking the rigid foam provides a thermal break and the log siding maintains the log look. The insulation and log siding will not be cheap but my heating season goes from late Oct thru Mar/early Apr and at least 3 of those months with many sub-zero days. I can afford to lose the 2″ to 2-1/2″ of space per room and the labor would be mine.
Is this crazy or would the payback in energy costs justify the project?
Thanks…
GBA Detail Library
A collection of one thousand construction details organized by climate and house part
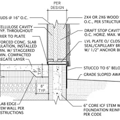
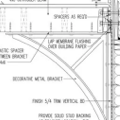
Replies
Dear ADK,
I'm sorry to hear that your dream home was built with leaky logs. That's unfortunate.
The easiest thing to do is to sell your home and buy a home with tight walls. It's very hard to fix log homes.
Most of my friends with log homes have ended up installing interior drywall. I think that makes more sense than installing fake "log siding" over rigid foam, but the choice is yours.
There are several problems to consider if you want to install rigid foam on the interior of log walls. The first issue is settling; log walls move, making it hard to retrofit interior insulation. The second issue is making sure that the rigid foam is continuous between floors (where the floor joists or roof rafters intersect the walls).
If you decide to go ahead and install interior rigid foam, pay close attention to air sealing. Multiple layers of rigid foam will be better than a single layer; make sure that the second layer of rigid foam has staggered seams, and seal the seams of every layer of foam with high-quality tape.
Your proposed foam thickness -- 1/2-inch or 1 inch -- isn't much. You would be better off if you could find a way to install 4 inches of rigid foam, either on the exterior or the interior.
Good luck.
ADK.
My son has a 1990 built log home just down the road (he's owned less than 2 years), so I am becoming familiar with the challenges of heating a log home here in zone 6. The fuel is cheap as it is wood cut from property by us, but that doesn't change the fact that it takes alot to heat (and alot of work). In this case the log design is 1st floor only, -there is much roof surface, which can be improved upon, insulation-wise, when reroofing is needed (soon), and I have gotten good advice from this forum in that regard. The gable ends are conventional framing with 6" of fiberglass, but also much window area in the "great room".
We have considered doing much what you are thinking with some walls, although with sheetrock as Martin suggests, and with 1.5 inches of rigid foam. More foam would be better but the space taken from the smallish bedrooms we are starting with would be a factor. Our thinking is this will add R and help very much with air leakage thru seams.
As far as selling your dream home, that seems extreme advice. Do what you can to make it as efficient as possible, then consider it one of life's tradeoffs. As an energy use issue, the new owners would still have to use more energy than a tighter designed house.
Perhaps others have advice about improving log home efficiency, which I would like to hear, but I would agree with Martin that this is not easily done. I was surprised to read (on this forum) about someone doing this with a complete add on outer wall, adding insulation and then vinyl siding over what is already great siding (log), in my opinion one of the best aspects of a log home, but I guess there is a reason that is preferred to interior insulating.
Seal the exterior of the logs with 1" of closed cell spray polyurethane and build out an 8-16" deep (whatever fits under your roof overhangs) Larsen Truss and blow it full of cellulose, using conventional or log siding (with a rainscreen gap for the cellulose to dry into) on the exterior.
That puts all of the structural wood inside the thermal and moisture boundary of the structure keeping it much better bounded in both temperature & moisture content over the seasons, reducing the amount of dimensional changes that wreak havoc with air-sealing efforts on log houses.
It also doesn't eat up living space, or force you to live in a construction zone while it's going on.
A Larsen truss works over a flat surface, but in this case you'd probably be better with a row of studs exterior to the logs. Insulating the exterior makes it possible to cover everything from the foundation to the roof, and to add considerable thickness for some real R-value.
Shimming the trusses to the logs to achieve a vertical and exterior isn't too tough, but they do need to be tied in with timber-screws to support the weight of the cellulose. Unless there's a good way to support an exterior studwall on the foundation without major thermal bridging trusses are going to be an easier way to hit an appropriately high-R.
There will be a lot of detailing to attend to to get the window flashing done right with any exterior insulation approach, but it's really the only way to turn the current 3-legged dog thermal performance into a thoroughbred performance building envelope.
Log homes look nice & rustic in pictures, but it's a tough way to go in a zone 7 climate.
Sorry for the late response to everyone. Thanks to Martin for fixing a problem with logging into the site. Thanks to all for the responses.
Selling and rebuilding are currently not an option. Dana's and TJ's recommendations are sound but are beyond my budget. They would also create many design problems in relation to my overhangs, dormers, windows, doors, deck, etc. I would love to add 2"-4" of rigid foam bu Howard nails it when he identifies loss of interior space as a limiting factor for depth of insulation.
Of note -- I do not think air leakage is my problem. I had an energy audit and the results showed only two problem areas which were addressed. I have misplaced the report but the blower door results were well within tolerances. My non-scientific observations lead me to believe the primary cause of my heat loss is conduction through the 8" milled kit logs (T&G type design w/flat tops & bottoms). The logs are cold to the touch, particularly in spaces more closed off from larger spaces, and I think the heat is passing through like a hot knife through butter -- current outside temp of 12 deg and logs range from 52 to 54 deg on interior.
The other problem is cost vs appearance. My wife loves the log look and will not consider covering them with sheetrock. 1" of R-5 rigid foam is definitely not much but it is a workable compromise. IF I ever build again I will likely use Bruce Brownell's methods for low energy use and log siding inside and out for the look.
Martin warns of log settling but I am hoping any movement is minimal after 7 yrs.
What I did do in my unfinished 2x8 framed walkout basement walls was to put 2" of rigid foam against the sheathing, 1/2" rigid foam on stud sides, R-19 in the remaining space, and strips of 1" rigid foam on the inside edge of my studs. Anal and labor intensive but I have now done what should have been done better and quicker with rigid foam over the outside of the sheathing before the siding was installed. I have also covered the poured concrete walls with rigid foam. I do not think the heat comes on in the basement zone more than once a day to keep it at 60 deg.
Thanks again for all the responses...
ADK... if you had an energy audit, dig it out, this is the best place to post it for analysis. If you lost it, ask the auditor to email you a copy, post it here. You will find out real quick where your construction and performance improvement opportunities are.
I frankly find it hard to believe that a milled log structure can be adequately air sealed without a second wall. Your audit should tell the real story to the experts on this site.
For sure your personal assessment is at least partly right. Wood has an R value hovering around R1/inch. That makes R7-R9 for your 8"ish logs. That value isn't even legal by code.
I have not seen a milled log house unfinished on the inside for decades. Yes, lots of seasonal cottages and camps, but never a primary residence. Where are you that you can get a Certificate of Occupancy with this structure? Also, logs check with age, open up crevices, joints separate and air flows due to shrinkage and weather effect; etc. I guess there are no carpenter bees in your area? They make quick work of log houses in Zone 6, mid-country.
Why suggest Larsen Trusses when there is already an adequate frame? He needs a second wall, internal or external. Plumb it and bridge it structurally to the logs. It can be 2 X 3's. Most milled log houses have finishing walls where in air sealing, insulation, etc can be added. That is the norm for log houses in the heating climates.
Outside and inside, I would chink the logs and all joints with polyether caulk.
http://www.chemlink.com/index.php/component/content/article?id=112
Extremely easy to work with (way easier to work with than PVC caulks; and not a rip off like the latex caulks from the big box and paint supply stores). No VOC's, cleans up with soap and water, lasts indefinitely, can over-paint, it won't dry out and has an amazing elasticity to move with log's, wood frame's and timber's seasonal and humidity changes. It comes in multiple colors.
While clearly the biggest heat loss is the conduction through the logs & chinking, air leakage tests done on a log house are rarely repeatable 24 months hence- it'll be new/different problem areas every time. Normal seasonal changes in moisture content of the logs changes their dimensions over time, and it's a constantly evolving set of conditions that never goes away. A flexible membrane type air barrier between the logs and whatever insulation method you choose will, help, but it's difficult to achieve a reliable and persistent air seal. I have no experience with the polyether chinking caulk approach, but I'd be curious if there were any data over 2-3 decade time frame or longer.
Add-on Larsen Trusses aren't structural, but don't need to be supported under the exterior chord the way a studwall would. An interior side double-studwall eats up a lot of interior space when going for a higher-R, and working on the interior while occupied means living in the construction zone. But if you only have a few inches to work with without running afoul of roof overhang complexities, an exterior side foam-over with rigid foam is probably the best bet, hanging your new siding on the furring that holds down the foam. A housewrap detailed as an air barrier (to the extent possible between the foam & logs is probably possible without re-mounting the windows, and would be fairly immune to the seasonal dimensional changes in the logs.
I agree I need to find my audit but Dana's point may make the results moot as the audit was conducted in 2009.
All the comments have me rethinking my original proposal. I now think I could do an exterior fix using 2" rigid foam & 1-1/2" T&G log siding. I have 2 ft overhangs and the windows/doors will still benefit as they are not being moved out. I will lose some of the passive solar heating on the south wall but I believe the improved heat retention of the logs offsets that loss (and I still get the gain thru the windows).
The devil is truly in the details. Dana raises the excellent point of how I seal everything. I also have to deal with butt and pass corners, exterior outlet wiring, and redoing the window/door casing.
Unless I am reading everybody's answers wrong, it appears there are different ways to go about this. Can I attach the foam board directly to the logs or do I need to attach 1x3 furring strips vertically before the foam board and siding (with the air barrier as the first layer in either installation)? And corner detailing becomes trickier the deeper I make the assembly.
Re log homes in Zone 7 - I visited log homes from Virginia to my area and not one of them added anything to the interior side of the logs. And my local building inspector never raised any concerns about log-only walls. Nor was this an issue during multiple seminars at log home expos or with my specific log package provider. I learned not to rely on my inspector as he only came to my house 3 times and had me pick up my CO from his office after deciding not to conduct a final inspection. No carpenter bees yet but maybe that means the NBS-30 insecticide mixed into my stain is working. Checking is minimal and any large checks are filled with Sikaflex.
Thanks all...
You can tack the foam directly on the logs (with housewrap under it detailed as an air-barrier, as noted), then clamp it in place with furring through-screwed to the logs with pancake-head timber screws 24" o.c. onto which you can nail the new siding. The timber screws need to penetrate at least 1.5" into the logs to have sufficient retention, and it needs to be a pancake head to limit the forces on the furring causing it to split. FastenMaster HeadLok (available at the box-store chains) or similar are fine, but even then, use 1x4 furring, not 1x3, since 1x3s are far more likely to split.
Seal up the seams & edge of the foam to the extent possible, to limit performance-robbing convection currents from getting between the smooth foam layer and the uneven log surface. You can use can-foam on the edges and even under the seams, but adding fiber-reinforced duct-mastic over the exterior of the seams will likely hold up better if the foam shrinks over time. In your climate zone 2" EPS is likely to perform as well or better as 2" polyiso during the mid-winter extremes, and would give the logs a reasonable drying path toward the exterior into the rainscreen cavity formed by the furring. With 2" of EPS you'd be cutting the conducted heat loss by half or more.
Caulk the housewrap to something smooth at every edge with acoustic sealant, which may require tacking on bit's of lath here & there with a bead of "windows & doors" type flexible can foam between the lath & logs to get that smoother caulk-sealing surface. Where there are seams between sheets of housewrap you may have to tack some lath to the logs to achieve a reliable long term seal on the seam.
I had been thinking of exactly Dana's suggestion once reading that ADK was willing to consider external insulation. We're not there yet but may get there. My son's place also has generous overhangs so could accomodate the added depth. There would be lots of challenging details with any retrofit of this type, but I don't think the rigid foam idea is worse than others. It is certainly easy to put up as it is light, easy to cut, etc.
Are furring strips, presumably 3/4", enough for the fastenig of siding? No doubt fine for securing the foam, but I had thought probably 2x4's would be needed here. My son's house has white pine logs that are milled to look like clapboard on the outside, so is not a flat surface, but is really quite attractive. What would one use as exterior siding to look like something close?
We were kind of blind about log home (in)efficiency, and didn't research enough, but I think sellers, owners and builders of them assume it's a proactive lifestyle choice that we were clear about.
Howard,
The following article should answer all your questions about furring strips -- how to fasten the strips to your wall, and whether or not the furring strips will be able to hold up your siding: Fastening Furring Strips to a Foam-Sheathed Wall.
I'm not sure whether log walls are (as you put it) a "lifestyle choice," a thermal disaster, or both.
I agree with Martin... selling is the only financially sensible solution if the problem is the financial burden of heating a log home. Martin, did you borrow from me? I used to say sell quite often at this site in days of yore, not so much of late as no one wants to here it.
OK... so solutions... I like exterior spray foam more than rigid. Trying to stop air leaks with a layer that wants to air leak is lots of good money not going to work as expected tossed after good money buying a wood home that does not heat well.
Really should have bought a home that first and foremost used the amount of energy you want to use.
Lots of ways to solve the energy use. The best way is to move to mild climate. Or go PGH. Parts of Hawaii and many other areas... use close to no heat or AC. I built a home in Curacao that has neither. And no ERVs and no HRVs... power to a place I stayed at in Mérida MX was two single strands of #10 wire(no heat no AC). In Vieques I stayed at a place that had just openings no glass... maybe bars... roosters for alarm clocks...
ADK final answer if going ahead anyway; rigid over round logs... air is going to get past... if not today... tomorrow. I would go with Northeast Sprayfoam, call Doug... tell em aj sent ya. Pay back... my guess... two decades.
I'm really not a fan of spray foam but this would be a pretty sweet system: use vertical 2x2 furring strips, spaced at 24" horizontally, attached with screws at 24" vertically. Drill pilot holes for screws in the furring strip in advance. Cut short pieces of PVC pipe (like this)as spacers. Slip the pipe segments over the screws as you install them, so the furring floats over the logs. Then you can spray a mostly continuous layer of closed cell foam, and still have a nice flat surface for installing the siding. Ideally you'd make the foam at least 1.5" deep under the furring, and then leave at least 1/4" or 3/8" clear space under the siding for a capillary break. As AJ says a layer of spray foam would stop the air leaks.
I always look for ways to use rockwool for out-insulation, so that would be my preference. Serious air sealing would require a full membrane like Blueskin or one of the fancy European membranes. This type of wall is pretty much state of the art even for Passivhaus level insulation--solid timber exposed to the interior (e.g. cross-laminated timber), an adhesive membrane at the exterior, then rockwool, furring with long screws, and siding.
First, a little blowback -- selling is not a financial, or any other type of, option. Reasons for not wanting to "hear" that incl: I built just 7 yrs ago on acreage no longer available where I have chosen to live, I would lose a considerable amount of money if I were to sell now, daughter starting college, established close friendships with neighbors and in the local community, little to nothing available in the type of home we want to live in, and I was happy to leave Hawaii after 3 yrs despite the climate. Bottom line - after 20+ yrs of living around half the world as Marines, my wife and I are where we want to be. The house was built with an attempt at being energy efficient. AJ & Martin claim log homes are notoriously drafty but the surely biased attachment refutes that with data. And my heating-only system provider of geothermal & radiant floor heat - another "expert" with professional credentials - turned out to be a bust with their design of Insultarp under my basement slab (among other things). Finally, most of what I have learned about energy efficiency was only just starting to come out at the time of my build; and AJ can probably attest to how much of that knowledge is incorporated by home builders in the northeast Adirondacks.
TJ - I get exactly what you are describing and it makes sense. Except for the 1.5" of foam. A friend recently visited with a coworker who is a thermal engineer. The coworker agrees with installing the insulation on the exterior. We also discussed thermodynamics and the fact that calculations show there is a sharp decrease in the value of having more than R-8 in a properly constructed envelope (see also this link on the website for AJ's recommended Northeast Spray Foam, Inc. -- http://northeastsprayfoam.com/sprayfoam/rvalue/ -- cost data is out of date)
IF air leakage is not the problem, why would I need more than 1" of spray foam on the exterior? My logs are 7-1/2" thick giving me an approx R-7 value. 1" of spray foam provides approx R-6 and solves any air leakage and goes well past the 90% effectiveness of R-8. This touches on some of what Bruce Brownell argues in his method of encapsulating homes with 4" of rigid foam (R-20) and nothing more.
Which all goes to the question of how does one becomes sufficiently educated by the right experts when traveling the non-conventional path to owning a home (i.e., building a one-off vice within a development)? I have learned a tremendous amount re energy efficiency from this site, Fine Homebuilding, and the Journal of Light Construction. Unfortunately, much of it has been after the fact. Live and learn but now it is time to fix, not run from, my situation. Thanks all...