Advice for rebuilding in central Oklahoma?

Two degrees of separation from two of the many who lost homes in the recent tornadoes near Oklahoma City.
I wanted to tap the collective intelligence to work through how to build back better (or retrofit surviving homes for resilience), both in terms of ‘what’ and ‘how’ — especially, to discuss what is locally appropriate and cost-effective, specific technical resources, etc., given the unique and extreme conditions in Oklahoma (tornado, fire, hail, and recently earthquakes…!).
To start the conversation (I will also work on answering my own questions here as I find more information):
The likelihood of another direct hit is tiny. The biggest opportunity is improvements in comfort and reduced energy consumption. But ‘durability,’ I’m sure, is on people’s minds, while costs are of course an issue (any ‘beyond code’ incentives?).
Good air-sealing: no brainer to do it; anyone know how widespread it is in practice there, or anyone there who is doing it best that could share knowledge with others?
Double wall: argument for 2×4 + 2×3 being stronger than 2×6 single; but can the cost be justified? If so, what type (larsen?), how thick? Building on existing slab? Cantilever outer wythe? (code/zoning issues?)
Windows: Cost-benefit of deployable metal shutters (roll-down)? E.g., less high-tech window + shutters vs. deluxe?
Attic: Vented or not? If vented, what is considered best practice? Are there any (cost-effective) attic vents that are thermal/moisture/air pressure controlled (partial closing in high winds to not over-ventilate?) Is it correct that venting helps reduce damage by reducing pressure differentials? (at hurricane-wind levels perhaps, if not tornado).
Overhangs: good to block harsh OK sun; but wind issues and bridging; would assume lagged rafter extensions would be appropriate; would ‘breakaway’ eaves help reduce damage to the structure? (but cause more damage elsewhere…ethical issues…!)
Ventilation: ERV vs. HRV, or just exhaust-only?
Saferooms: recommended construction approach and detailing? retrofit vs. new build?
As a reference point, what I’ve seen in a lot of (fairly) recent construction is single-story, large footprint, hipped shingle roofs; not sure if 2×4 (more likely 2×6), brick clad, modest overhangs, simple double-pane metal windows, turbine attic ventilators, ~ ceiling joist height blown fiberglass insulation, bathroom fans venting (without flex pipe extensions) into vented attics (because more moderate pressure differentials than direct to outdoors?), gas furnaces and heat-pump (non-reversable) central AC’s.
any takers? 😉
d.
GBA Detail Library
A collection of one thousand construction details organized by climate and house part
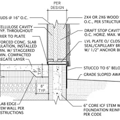
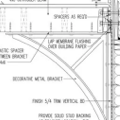
Replies
David,
Good details to address tornadoes are more expensive than conventional construction.
Items to consider:
- A full basement with a safe room. More information on safe rooms here: http://www.fema.gov/safe-rooms
- Above-grade walls made of ICFs.
David,
I'm not a builder so I can't answer your questions directly, but as you know there are very good online sources of information. One is an article called "Tornados of the South - Structural Performance of Newly Constructed Homes in North Carolina, Alabama, and Georgia". I think this analysis was of homes in the area from EF-0, EF-1, and EF-2 tornados. It is a free download from APAwood.org. You do have to register for free, but then it downloads right away after that.
In terms of safe rooms, this is a good JLC article on manufactured storm shelters http://www.jlconline.com/coastal-contractor/manufactured-storm-shelters.aspx which is also a free download.
Also a review of some of the issues of safe rooms http://www.jlconline.com/codes-and-standards/jlc-report-2.aspx
A 2004 review of tornado damage http://www.jlconline.com/Images/Practical%20Engineering_%20Resisting%20Tornado%20Damage_tcm96-1104574.pdf
One city in particular embraced "green" building practices after a tornado - Greensburg, Kansas. http://www.jlconline.com/Images/Practical%20Engineering_%20Resisting%20Tornado%20Damage_tcm96-1104574.pdf I couldn't find a lot of specifics about what they did for individual buildings, but it's inspiring that the community pulled together to do this.
That's just what I've found this morning. The real builders (and Martin) will continue to weigh-in on this topic, I'm sure.
A couple of great resources are the IBHS (http://www.disastersafety.org/fortified/) and the ICLR (http://www.iclr.org/). They both have builders guides that I have been through in great detail. There is a lot of useful, free information on resilient construction from these two groups.
Reinforced concrete walls & roof with sufficient rebar (including rebar connecting the walls to the roof) can probably survive almost any tornado structurally, but you'd still have to replace all the blown windows & doors, and some or all of the siding and exterior insulation, depending on the severity of the storm.
To meet code-min on a concrete wall assembly in OK with an exterior continuous insulation only takes R5, which can beat with an inch of foil-faced polyiso, and 1.5" would bring it up to 1.5-2x code for not a huge uptick in cost. (Polyiso is preferable to XPS since the blowing agents used for XPS have more than 100x the global warming impact of those used for polyiso.)
How building with reinforced concrete compares to timber-framing costs depends on the costs of concrete and the cost of labor in that area, but for most homes in most markets it doesn't rise to a double-digit cost adder to the project as a whole.
Martin:
Underground isn't a likely option in OK due to expansive clay soils. Above ground is the path of least resistance.
David:
ICF construction would mitigate almost all tornado damage, but some are scared off by the costs. At the very least, I would think requiring hurricane straps is a good 1st step, if it isn't required already.
Lucy:
A very helpful resource for Greensburg is their Tourbook. http://www.greensburggreentown.org/tour-book
It details what certain building types did after the storm, and why.
Thanks, Mike.
The Tourbook is great. Thank you for that link.
I found a Building Science article on rebuilding energy efficient affordable homes in Greensburg Kansas. http://www.buildingscience.com/documents/reports/rr-0804-energy-efficient-plans-greensburg-ks
It describes their recommendations for rebuilding, some of which are a little surprising. They recommended rebuilding with 2 x 6 advanced framing with OSB shear panels in the corners and insulated foam sheathing elsewhere. I thought foam sheathing was not a good barrier to windblown objects in tornado-prone areas. Any comments on that?
Thanks all for the resources...great stuff; still digesting!
BSC rr 0804: a bit confused; fig. 2.1 ('recommended....') calls for 'OSB/Plywood'; while table 2.1 ('proposed') specs R-7.5 XPS, while par. 3.2.3 specs '1.5 inch foam sheathing with taped joints replaces 5/8 inch OSB and Housewrap' - I assume the drawing in 2.1 is just mis-labeled/mis-drawn. And too bad the wall/roof connection wasn't shown. Anyone know what that kind of roof truss is called? (separate/diverging chords to hit the top of wall, and form the eave/overhang)
@Lucy: I'm also surprised that there is no sheathing except at the corners; perhaps this is to stay within a certain budget; and assumes that the added 'projectile' protection of 5/8 OSB doesn't change the fact that another tornado will wreck the whole wall anyway; so if not needed for more likely events (average strong storms), isn't worth it? But they still did full basements...
Detail: Is the transition from 5/8 OSB + 1.5" foam to just 1.5" foam visible? Doesn't seem like they upped the foam to 2", or used different furring strips...?
minor point / errata: I was wrong implying that tornado damage is not covered by insurance; have heard it actually is for most under 'weather related', unlike some other disasters (e.g., flooding); editing in original to avoid propagating falsehoods.
Monolithic domes are an unconventional resource, but they do an admirable job of durability, efficiency, and safety. See their website at http://www.monolithic.com/. 2 items of contention; appeal; many don't like a dome shape. 2) financing; most banks will only make FNMA eligible loans; FNMA requires comps of similar style. The website discusses all these issues. They have video of MD's that have gone through fire, hurricane, tornadoes, etc. FEMA has grants to municipalities that build MD's for public shelter; schools, gymnasiums, government offices that can be used to shelter the public when a storm is coming. Some of the efficiency claims do not jive with the building science you find here; 3 inches of foam is R18, not R60, But they are air-tight, los of thermal mass, extremely durable and safe.
I am no expert, but I recall that some wind forces are similar to earthquake forces (which are more of a concern on Vancouver Island than tornadoes). So if concrete is too expensive and folks go for a wood frame house with a concrete safe room there are some things that can be done to reinforce the entire home. Our house has the Simpson tie down metal straps on the rafters and between the storeys. There are 3" metal plate washers on the anchor bolts fastening the house to the slab as well as some heavy duty metal brackets connecting studs to some anchor bolts. The house was built with pre-made stud panels sheathed with plywood. This ply wood overlaps adjacent panels and the second floor in a jig saw fashion. The design limited expanses of windows to allow enough shear strength in each wall. The architect insisted that the nails be flush with the plywood and not inset which compromises the wall strength. Our walls happen to be thick with 2x10 plates and staggered studs as well as 2" exterior roxul so that would help with strength and resistance to penetration. There are also interior sheer walls sheathed in plywood also with the special anchor bolt system. The roof is sheathed in 5/8" plywood and has metal roofing. I will write up some seismic post on our blog at some point with photos http://www.agreenhearth.com
Another way to frame my question:
What would a 'pretty good house' for Oklahoma look like? (focused on energy, with some improvements to high wind, wildfire, and other hazard resistance; assuming a 'tornado proof' house is out of the question / not cost effective)...some thoughts:
Hollow-core brick veneer is common; I see GBA's detail 2-02024 shows brick over 1-1/2" foam with penetrations for masonry ties - I guess with air barrier on the inside and some sealing around the tie, they aren't a major leak or thermal break. Target R11-22; 1-1/2 foil-faced polyiso (6.6) plus standard 2x4 & cellulose = ~19, 2x6 = ~25 (and better for 24OC framing given big roof and wind loads).
Slab insulation would need to stick out beyond the brick face (covered with flashing, sealed against termites) in liu of a galv. ledger. Any detail ref. for this area? The Greensburg BSC rec assumes wood siding (could use cement/fiber board) which doesn't need support under, and a basement (insulated from inside); so...quite different detail.
Any rec for slab edge insulation thickness/depth? What I see from EnergyStar only lists floor, and basement/crawlspace recs, with target R-values of 13-25 and 11-19 respectively (meaning insulate the floor, _or_ basement/crawlspace).
Other issues:
Attic venting: the wildfires Oklahoma has seen are an argument for unvented, 'conditioned' attics (sure, you can screen your eave vents and use something better than whirlygigs, but still...); by putting nailable insulation above the rafters (or less preferred, below), and/or 1/2 ply below the rafters and insulating the bays (furr out for thermal break), the roof should be stiffer and stronger than a standard uninsulated, exposed rafter/deck attic. Target R-38 (EnergyStar); could do that with 3.5" polyiso over 2x6+cellulose, or 2.5 polyiso over 2x8+cellulose...?
blown cellulose won't increase the strength of the assembly like SPF (probably minimal, anyway), but assuming nailable insulation above and the option of 1/4 ply below (vs. fabric/netting) hardly seems an issue...and if the roof does blow off, cellulose will be less damaging to the environment wherever it lands...
David: On the roof-R, it's both cheaper and better to go with 1" (R6-ish) of iso and 2x12 rafters with a full cellulose fill, since it'll be a higher R value (about R48 center cavity), less foam, but also measurably more thermal mass from the cellulose, enough to make a difference on the cooling loads.
Hurricane ties between the rafters and wall framing keeps the roof from from flying off in one piece. Construction adhesive between the rafters & roof sheathing and tighter fastener spacing keeps the sheathing from popping off a sheet at a time. If the wind strips the deck bare off roofing & foam that's a much cheaper repair than the whole roof (or whole house.)
Lucy:
As I understand it, foam sheathing is not a good barrier to windblown objects unless it is backed with something of significance, like Kevlar or concrete. I've personally witnessed 2x4s fly right through brick veneer/batt insulation/frame construction during wind-cannon testing, and the speed of the stud was only simulating an EF-1 tornado (110 MPH wind speed/60 MPH stud speed). Foam insulation in that instance wouldn't have fared too much better, in my opinion.
However, I did see foam insulation perform well during a DoD blast test. Backed by concrete, an ICF box (meant to simulate a small closet) was subjected to 50 lbs military grade TNT from 6 ft away. There were areas of compression and minor burn marks on the foam, but that was the limit of the damage.
I don't know if linking to YouTube is allowed on here, but if you search "blast testing icf" you'll see videos that confirm both of my stories above.
Patrick:
I don't usually highlight specific manufacturers, but Simpson Strong Ties are legit products and I plan to use them on my personal construction project.
@Dana: Yes, better to use less foam and deep rafters in new-build; I was unconsciously in repair/retrofit/typical rafter depth mode...Thinner foam perhaps has the advantage of shorter screws and so maybe better attachment to rafters? Hadn't thought about the mass benefits; I know there's some debate about the 'effective R-value' approach; but for a roof in the sun, in a state with large diurnal swings [record high and record low on the same day!] could be beneficial...though would want to check loads with the added weight.
So I'm imagining: 3-tab shingle > WRB > Decking+polyiso (w/o foil b/c no air gap) > cellulose >(netting) > then, either 1/4 ply (cheap, light, adds stiffness?), or do we need gyp because of fire issues? At which point you might as well add windows and stairs and pay more in taxes... ;) Or go back to the air sealed attic + loose fill cellulose + venting...
@Mike: I noticed hollow bricks in lots of the rubble; can veneer be reinforced with small diameter rebar with centering spacers attached before insertion, the grouting? Tight gap; and would need to weld or thread to anchors at the foundation and tie into the top plate / roof (e.g., IBHS / FORTIFIED's 'continuous load path' graphic); costly, but you get a strong post-tensioned outer shell... ;) At which point the veneer is no longer a veneer...
For fire resistance the fiber cement board siding over rigid rock wool panels would help. Could use rigid rock wool on roof too with strapping and metal roofing over.
Tornado resistance for $600 http://www.finehomebuilding.com/item/29114/homes-can-survive-tornadoes
http://www.finehomebuilding.com/item/17009/energy-efficient-framing-practices-for-hurricane-and-tornado-country/page/all
http://forums.finehomebuilding.com/breaktime/general-discussion/can-build-withstand-tornado?page=3
David:
Your last sentence made me smile. You did a great job of describing a "super veneer".
Mike: 'super veneer' has a nice ring to it...! It's probably overkill and not a good 'payback' / benefit to cost ration, but I've seen too many piles of unreinforced masonry rubble over the years, and folks who would have benefitted from some vertical rebar and grout through the hollow core (and / or horizontal reinforcing between courses!)...
JIMHO the 'super veneer' is a total waste of time and resources. The post-tensioned scenario you describe would be a total pain in the backside to build - imagine the reply you'd get from asking the mason to slide each brick down over eight feet or more of rebar - and then I very much doubt that the compressive strength of the brick or the tensile strength of the bar and fittings would be anywhere close to providing the bending resistance required of what is in effect an extremely shallow vertical beam subject to unpredictably severe side loading. And even if the veneer did not immediately collapse, the chances of it surviving a direct hit from a major twister without substantial cracking requiring subsequent demolition would probably be zero to none.
Again JIMHO, the best use of resources in a post-tornado rebuild is to focus on the best chances of survival of the inhabitants: safe rooms, not bunker buildings. Think of the sacrificial crumple zones engineered into a modern automobile, with the occupants protected in a hardened interior shell, rather than requiring everyone to travel in a Sherman tank.
James: thanks for your H.O.! I agree, the first thing to do is focus on safe rooms and storm shelters.
But once that's covered, for the sake of argument, let's probe the next step: Consider that this website is dedicated to 'green building'. What is the environmental impact of premature building death and substantial / total landfilling of its materials? What level of investment would yeild what level of savings? And what about more immaterial things - personal affects, displacement to temporary accomodations, work, life, school interruptions?
The same 'weakest link' principles of energy conservation apply: no point in a R60 wall, or R10 windows, when you've got a leaky attic hatch. Here, no point in a reinforced brick wall if you don't have hurricane shutters and a strong garage door, full WRB under the roofing, etc. Also perhaps metal strapping from roof to walls and to foundation... but a stronger outer wall could partially offset the need for this strapping by providing load path continuity directly from roof to foundation.
To clarify my idea:
Constructability: Shouldn't need to slide bricks down over 8' of rebar, like the straw bale folks were trying 20 years ago; I can just leave out one brick at the bottom for each vertical run (where the foundation anchor is located) and send it down after, either welding (3rd world) or threaded coupling it to the anchor, then packing the hole with mortar and a half-brick.. My question was, will the grout for each course as it's laid up block the holes so much that you can't send rebar through, or pack it with grout after? The cost of keeping the 'chase' clear may become prohibitive; thinner but higher tensile-strength wire could help but
Re-use: Grouting the rebar makes the wall an expensive bumper that will likely be so damaged it will need to be replaced anyway, while making it harder to dis-assemble / re-use materials. Option: partially or completely de-bonded rebar, or sheathed wire that can pulled out afterwards for 'dis-assembly' and recycling/reuse. However, improved ductility may not provide an advantage in this case as it does for poured concrete.
Shallow Beam: Absolutely an issue, with the rebar at the neutral axis (the least efficient point!). But remember, I still have the 'inner wythe' of a wood framed wall on the inside (essentially a double wall); if well tied together, the two systems can act as top and bottom chord of a truss (albeit creating some thermal bridging). Reinforcing the veneer could also obviate the need for masonry ties and keeping sheathing/studs close to the brick, allowing for a thicker (and better insulated) wall.
Ok, enough dreaming about 'the perfect wall (for tornado country)'. Houses may be rebuilt without even basic improvements that are already proven (e.g., recs from the APA documents), so I'm focusing on sharing that type of information. But given the seeming preference for brick facades over potentially better alternative materials, it is interesting to brainstorm on improvements to the (contemporary) vernacular - as it's unlikely we'll go back to sod houses with sod roofs...!
I was being facetious about the "super veneer". I wouldn't recommend it as a storm-proofing measure.
IMO, just build out of a reinforced concrete wall system and be done with it. Whatever veneer(s) you choose are basically for show at that point.
I'd love to see more reinforced concrete, and will recommend it; but am also looking for solutions within the seeming preference (and sometimes, HOA requirement) for brick, which for residential is typically done over studs, assuming because of 'affordability' (first-cost).
Regardless of the structural system, the question is still also about energy and getting the section right; and I see lots of different and sometime contradictory information regarding light frame construction, R-values (code min. vs. energy star vs....)
I'm going to propose:
Wall: ~R25+, dry to inside
Unreinforced brick veneer + 1" air gap + 1-1/2" taped foil-faced polyiso + taped plywood sheathing + 2x6 stud / cellulose + drywall (optionally air-tight)
Roof: ~R38+, dry to inside (unvented / conditioned attic)
3-tab shingle + continuous peel&stick + plywood sheathing + 2x10 rafter and 2x2 horizontal furring + netting (+ drywall required for fire protection?)
Rationale:
-Foil only of benefit if facing air gap, so only in wall.
-No foam in roof so plywood sheathing can be in direct contact with studs and rafters (seems stronger?)
-Ply can form continuous air barrier; can break the roof sheathing at eave and bring peel&stick down over foil for continuous WRB (with additional piece continous to eave edge)
-Continuous peel&stick roof for rain protection in case of shingle damage
-Horizontal furring in roof provides thermal break in absence of foam on top, and strengthens roof (less stiff along slope, but stiffer across, and distributes point loads).
-Ply better than OSB (strength, environment)?
Options:
Roof: netting between 2x10 and 2x2; isolates bays for better control of cellulose (dense pack?); then use rockwool (sheets?) between furring.
Roof/Walls: could put ply on top with non-foil foam under for both; but distancing the ply from the structure seems weaker; and the ply in the wall would then need a WRB. Best for strength if nailable insulation (foam bonded to ply/osb), though better for air sealing if separate ply + foam (staggered joints).
Roof/Walls: can always increase wood dimensions for more R and more strength, if you have budget...
Eaves: Thermally broken; a kind of bracket...
Will work on an image.
Will also work on better understanding slab edge insulation best practice for OK, with brick veneer, termite protection, and insulation as continuous as possible...any advice appreciated.
Sources and Contradictions:
GBA's detail 2-02024 shows brick veneer attached with ties through foam to studs, no sheathing; but this doesn't seem very strong to me (might be a short veneer wall in front of a raised crawl space, no significant wind loads; shows shingles above).
The BSC's rr 0804 (Greensburg) house rec only has OSB sheathing at corners, but I assume that's because of the wood siding.
The illustrated axonometric cutaway 'Tight house illustration from FHB.jpb' (from air-sealing article) puts XPS foam outside the sheathing for the wall, but under the rafters in the roof...but then which side does the roof dry to? Doesn't show detail of the roof, but I assume it's just using building paper, not peel&stick, so maybe ok. The detail also shows 10" (wall) to 14" (roof) open-cell spray foam...counts as air barrier, but not vapor barrier, right? Here the air barrier is primarily the roof sheathing and wall sheathing, with taped foam as a backup for the walls, and spray foam as backup for roof and walls.
Spray foam might add a little strength, water protection (open less on both counts than closed? but don't like the propellants and fire risks of closed); but strongest if bonding to all sides, which I believe isn't possible in the field, due to expansion, and the need for drying.
David:
Ahhh HOAs, how I despise their short-sightedness.
Brick can be used on reinforced concrete walls. For ICF, just start with a brick ledge form and go up from there. If using a removable form wall above grade (pretty rare), you can actually use a form liner (with color) to create a brick aesthetic... without the hassles of installing brick.
But enough about that.
In your most recent post, I didn't see anything about hurricane straps for the roof. You would use those, wouldn't you?
Working in a firm that designs schools mainly, we have done quite a few safe rooms and are getting calls more and more now for safe rooms to be added. I have used precast, reinforced block, and ICF in construction of them. I was a part of the first one about 4 years ago, which was actually a large auditorium. The concrete used was very substantial (all precast). However using ICF seems to be the best out of the options we have used. Construction was easier since block needs to have every core reinforced and grouted full. Precast works and is fast, but its not always the look we are after. ICF allows us to use any exterior material and gets well above commercial code for mass walls in zone 6.
Doing the research and being apart of the projects made me choose ICF for my home under construction I am building myself. It is not constructed anywhere near FEMA 361 standards, but we live in a windy area and are in tornado alley. An F5 hit just a few miles away from the home several years ago, and I have personally been in 4 tornadoes, so it made sense to go ICF. The roof construction is a 2x10 plate anchored every 3' with 5/8" cast in anchor bolts. A combination of trusses, 2x12s, and TJI make the roof structure. I used all simpson hurricane ties to anchor everything to the top plate. Everyone knows I too went down the road of exploring all different wall types, and it was between double stud and ICF in the end. I decided on the ICF due to the strength, longer lasting air tightness, sound qualities, and decent r value. (system I chose works out to be a average r value of 28)
I did a house where the master bedroom closet was constructed out of ICF with a precast 8" concrete cap. There was 2 doors on it, one was a hollow metal steel door with dead bolt locking similar to ones we spec on FEMA 361 rated buildings. This was swung into the room and held back to the wall, out of the way. The second door was a standard wood door. They keep their safe and other items in here as well, and its plenty big for the family to go into if needed. Might be another option to look into if you do not want to do a full house out of it. This is far more of a true safe room design vs a home like mine, due to the windows and doors.
ICF: thanks Jesse and Mike for all the info; still very interested in ICF as an option...
Costs: PCA says 3-6% more (whole-house, new construction), which is better than I assumed; but they might be biased...does that jibe with what others have found?
Ceiling: Jesse, what is the ceiling / attic floor for your house?
What about pouring a concrete topping slab on a wood deck as a cap, joists set below the top of ICF wall? This would avoid the trouble of removable formwork for a true structural slab, or the cost (and wasted material) of polystyrene left-in-place forms as in some safe room plans, and be conceptually similar to a wood frame on concrete podium approach (with insulation moved to the roof, this becomes usable space; but does need windows, and stairs...).
Mike: Ties and fasteners: I intentionally left all fasteners out of the wall assembly section description to keep it simple. Absolutely, hurricane ties, straps, foundation bolts with plate washers, ring-shank full head nails, etc...learning from the APA and FORTIFIED materials among others, plus what I know from para-seismic details in CA.
Question: is my concern about foam between roof sheathing and rafters weakening the assembly justified, or unfounded? gut says there are trade-offs, not sure on balance. I also worry a bit about the roof sheathing being trapped between two vapor impermeable layers (peel&stick and foam); but it's perhaps no worse than a roof flash-and-batt approach.
HOA's / zoning: Not all bad, if they forbid gable ends and require storm shelters! ;) But my instincts say that SF, low-density zoning is one barrier to affordable, durable construction. You could do a lot of concrete walls and roofs with the money and materials you save going from 1/2 or 1/4 acre lots with huge driveways to 8+ du/ac duplex/multifamily, party wall, multi-story...but that's a whole 'nother issue...
The ceiling is simply trusses with 5/8" gyp and an r60 of blown insulation. I did do an attic seal with spray foam in the attic prior to blowing in the insulation. In the area with 2x12 rafters and 14" TJI, I used spray foam to get my about an r50. you can see images of the build at my blog:
http://lizerhomestead.blogspot.com/2013/04/spray-foam-and-attic-seal.html
The cost figures PCA touts are the same I touted when I worked there (and ran their website).
I would add this context: 3-6% of the price tag of the home. But that is a national average. Some fall below that, while some will far exceed that. And it's going to be influenced by some of the following factors:
Installer. More experienced, less labor time and fewer (if any) snafus. I knew of installers 10 years ago who could build with ICFs for the same price as 2x6. Also, the solidity of their business model. What I mean is, it's not always the product's fault. If they can't control their overall costs very well...
Size of home (and complexity of design)
ICF manufacturer (i.e., price of the block)
Price of concrete in your area
Another plea for fewer acronyms! "PCA touts" had me confused. I think it's a reference to the Portland Cement Association.
Recently Dana Dorsett has sent me to the online dictionaries with SFAIK and lots of other alphabet-soup nonsense that I haven't yet had time to look up. English, please!
Sorry; the 'PCA' was my fault! Don't blame Mike...[but the 'touts' was his...] Yes, Portland Cement Association; lots of info on Insulated Concrete Forms (ICF). Will find better ways to save characters!
Thanks for confirmation on costs / cost factors - one need is those currently (or at least until recently) living in mobile home parks. Simple forms, party (adiabiatic) walls, repitition, (and 2-story?) might help, too
Surprised to see ICF for fully interior walls where insulation isn't needed (safe rooms); assume due to cost savings on one-off projects. WIth repitition, re-usable formwork might become cost-competitive? Looking for polyiso ICFs now...
Re: polyiso ICF: I have never seen or heard of them, but that does not mean they aren't out there. I would have to think the cost to build forms with them would be insanely high due to the cost of iso vs EPS.
Yes, PCA is Portland Cement Association.
"Touts" is a verb.
David:
Where are you seeing ICF for interior walls? Other than safe rooms and party walls in multifamily, I don't believe I've ever seen a project utilize them for interior walls. It doesn't make any sense (to me).
@Mike C., interior ICF: yes, seen in plans for safe rooms, and would be interior if for party walls using the same system as exterior walls for simplicity. Not for any other interior walls. For party walls, ICF would have some sound transmission and interior acoustics advantages, but decouples the mass and wastes the foam. But cheaper / easier than getting stud walls to reach fire ratings? Ideally: ICF for exterior walls, cast-in place (reuse forms) or CMU for safe rooms (coupled mass), and wood otherwise (incl. party walls)? But using multiple systems might take away the savings.
@Jesse: interested in polyiso forms to avoid certain blowing agents. More expensive, but more R per inch; maybe stiffer too, so can use less? Have seen non-foam ICFs (e.g., Faswall); could imagine a hybrid (foil-faced polyiso out, non-foam inside)? Or asymmetric forms to shift the mass inward?
-
Brainstorm on safe rooms: pour-in-place into existing stud bays? If only drywall in/out, would need to reinforce anyway (to prevent saturation/blowout); less destructive than demo and reconstruction; but cost maybe higher than just layering plywood and steel plate. FEMA also shows dry-laid masonry infill in stud walls; seems only a minimal improvement and requires partial demo; and minimal savings over at least mortaring blocks in place, if not reinforcing (rebar in, or mesh out both sides)...