Apples, Turds & Mineral Wool

Some recent comments(2-25-11) at
Martin’s “Superinsulated House Specs” Blog
https://www.greenbuildingadvisor.com/blogs/dept/musings/superinsulated-house-specs
Martin issued a call for “Outdoor” Mineral Wool Details
I remember seeing one solution in this video( at around 3 minutes in)
Does anyone else care to comment about Mineral Wool?
How about Apples & Turds?
I assume that John Straube is calling Wall Assemblies with “Outdoor” Insulation the Apples?
GBA Detail Library
A collection of one thousand construction details organized by climate and house part
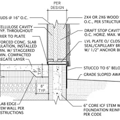
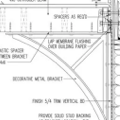
Replies
Thomas Jefferson started this interesting thread a while back:
https://www.greenbuildingadvisor.com/community/forum/green-building-techniques/18650/alternative-non-foam-outsulation-strategy-using-rock
I noticed that in Dr. Straube's comments to Martin's bolg that he refers to "double walls".
I wonder if there is a particular style of "double wall" that he had in mind?
I have seen many examples of "double stud walls" which were sheathed on both sides with OSB...
I have seen many other examples of "double stud walls" which were sheathed on the exterior with OSB...
Are these the "turds"?
Would the "ARCTIC" envelope used in SunRise house be considered a "double wall"?
Would one of Robert Riversong's truss framed homes be considered a "double wall"?
Isn't this true for any super-insulated, super-tight envelope?
John Brooks,
I think there are a lot of questions, not so many answers.
Did you see John Straube's recent report on High R-Value Enclosures?
See p. 14 for some input on mineral wool exterior insulation:
http://www.buildingscience.com/documents/reports/rr-1005-building-america-high-r-value-high-performance-residential-buildings-all-climate-zones
Regarding the Lumar video snapshot, there would obviously be some thermal bridging with this technique, as the outer insulation layer is not continuous, but it would still warm the interior layer of sheathing.
Did you also notice that Lumar used solid board sheathing on top of the mineral wool?
Martin Holladay,
This double-stud wall durability debate needs to be laid to rest. I know this is not a conventional Q&A question, but hear me out:
There must be a dozen double-stud wall houses within a short drive of your location, no?
How much would it cost for you to do a roadtrip, inspect and investigate some of these double-stud wall houses, and report your findings in a blog? The goal would be to determine which had moisture damage, which didn't, and why---essentially to figure out what to do, what not to do . . .
I'll contribute $250 to start, and I bet others visiting the GBA website would contribute some $ too. I think this is one of the burning questions that needs to be addressed. How about it? Would Taunton / GBA consider something like this? Would you?
Thanks
P.S. Sorry, John, for the potential hijack of this thread, but I think this is something that needs to be addressed for us to create more "not so foamy" solutions.
Daniel,
Thanks for your flattering suggestion, but I'm a firm believer in distinguishing between research and anecdotes.
A good field study would sample dozens of houses, would involve extensive monitoring, and would try to control for a dozen variables. A good test-hut study would require several climates, several side-by-side huts, and several years.
Anecdotes are cheap, but they don't really add much to human knowledge.
In my blog, How Risky Is Cold OSB Wall Sheathing?, I tried to list the details that lower the risk of sheathing problems with double-stud walls. I think that list is a valid summary of current knowledge.
I wouldn't hesitate to build a double stud wall sheathed with plywood, fiberboard, or diagonal board sheathing, as long as the wall included a rainscreen.
Remember, every barn in the country has cold sheathing in the winter. Cold sheathing is not really a problem, as long as the sheathing is ventilated and allowed to dry out.
Martin,
I'm not proposing that we confuse research and anecdotes.
But where is the field study? And what organization is currently testing double-stud wall variations in a controlled environment like a test-hut? Not likely . . .
What we now have are anecdotes. Like John Straube saying that double-stud walls are risky (or insinuating that any structure without exterior insulation is comparable to a horse apple). And we have your statement, "I wouldn't hesitate to build a double stud wall sheathed with plywood, fiberboard, or diagonal board sheathing, as long as the wall included a rainscreen."
Confusion reigns supreme. What I'm proposing is a gap filler.
On-site evaluations (by an experienced professional) could provide more than just anecdotes. And analyzing a 30-year old structure could potentially provide information beyond the scope of a test-hut environment. The evaluation could include:
* Cross-sectional drawing of as-built wall
* Description of mechanical systems
* Visual inspection of sheathing, rim joists, etc.
* Moisture readings of critical structural elements (even if it's just one data point on one day)
* Historical review of house repairs and homeowner complaints
* Blower door test
You could build the list as detailed as $ would allow. Perhaps something like that is beyond the scope of Taunton, Inc. But that's the kind of information needed to dispel the fog surrounding double stud walls.
C'mon, you could title the blog, "A Historical Review of Not-So-Foamy Superinsulated Houses." ;-)
There seems to be some real confusion about research, risk, and science in these comments.
There is no "safe" wall and no "unsafe" wall per se. All walls can fail if we expose them to extreme environments or build them badly. The issue is what are the odds of failure for a certain wall in a certain application. In a dry house in Boston, with good overhangs, good construction, and window/door subsill flashing, the odds of failure of either a double stud wall or exterior insulated wall is low. In a high indoor humidity home in northern Maine on the coast, the same wall designs built with ordinary skills are would have very different failure odds: the double stud wall would have a higher risk, much higher. How much higher depends on the .
Luckily, with the use of engineering and science, we have not had to build thousands of homes of two different types, wait 30 years, and then inspect them in detail. At the end of the day, this is the only correct answer of course. But building science allows us, by understanding wetting, drying, environmental exposure, interior conditions, material properties to provide approximate rankings. This understanding is, and must be, repeatedly correlated to real experience to ensure the science is not missing something.
BSC/and the building science community have repeatedly used building science to predict failures. For example, we predicted that undrained EIFS would be a disaster. If built perfectly or used in sheltered locations, it worked fine. And if you randomly chose 10 face-sealed EIFS houses in Kansas City, there would only be a few small signs of rot. On the coast of Maine, most such houses in exposed locations have already been reclad/repaired. We also warned of hard board siding, sub-sill flashing (the lack of which is still one of the best sources of work for our forensics) and poly vapor barriers in air conditioning climates (thousands of moldy buildings out there right now). We predicted problems with back drafting, high humidities in winter climates when houses were air sealed, etc etc. Before any of these warnings became accepted, we, alas, had to build thousands of buildings, wait 2 to 5 years, and then see problems unfold because people told us "but I built a house last year like that and it is just fine".
I only have anecdotes (which is where almost all of our research begins), but I also have one house of sheathing measurements (a real lived in house), I have boat loads of close examples (e.g. cold outboard OSB in SIPS walls for example are a problem -- rot photos we have without vented claddings), but I also have tons of science and modeling to support the risk of double stud walls.
As shown in the High R report, there are things we can do to reduce that risk to get it down to the level of exterior insulation: vented cladding (aka "rainscreen" although that meaning is often lost), vapor permeable and moisture tolerant exterior sheathing (fiberboard, dense glas gold, even plywood), sprayed in insulation (cellulose is obvious, some fiberglass is now just as good), and exceptional airtightness. This gets us close. How close? I cant say since it is pretty close. It wont be able to catch up to a similar wall with 50% of its R-value as rockwool or foam exterior insulation, but it does not need to.
The details of the wall design of course matter. I hear double stud walls described as R40 all the time, and then see the entire floor joists penetrate through and other such penetrations. This is easy to calculate reliably, so there is little excuse for comparing an R33 wall to an R40 wall.
Thanks for your comments, John.
A clarification of my earlier post: I wasn't implying that John Straube was drawing unjustified conclusions from anecdotes. On the contrary, John has always based his conclusions on building science verified by well-designed research studies.
My intention was to downplay the value of drawing conclusions from a few site visits by a journalist (a response to Daniel Ernst's well-meaning suggestion to send me out as GBA's forensic investigator), not to downplay the value of John Straube's observations.
John Straube,
Thank you for posting a response, and additional commentary. It's fantastic to have you on the GBA site.
Please don't take me wrong. If my comments on this topic come across as frustration, it is but my way of expressing the sentiments of one of your earlier statements: "Failure statistics are not available for window leakage in standard tract housing: expecting stats for such an odd and custom type of assembly like a double stud wall is asking for building science nirvana."
What we have is the proclamation that double-stud walls are risky---that the risk is difficult to quantify, and depends on huge number of variables, such as climate, build quality, airtightness, mitigation strategies, etc. We understand the science and hygrothermal principles of why it is risky, but we don't necessarily have clear guidance on the subject (i.e. detailed tables, climate zone recommendations).
Is the risk substantial enough that we should avoid it completely? In what climate zones? Or is it something that can be managed with a certain number of strategies? And if so, what are those exact strategies? Note that these questions are largely rhetorical. It's clear that we don't have the data and studies to draw very firm conclusions on the subject. Perhaps you have a very good feel for the correct answers, but I'd venture to say that most people in the building industry do not . . .
You pointed out that BSC clearly identified the risks associated with face sealed or undrained EIFS, and that the predictions were correct. That's exactly why people take note when you state that double stud walls are risky.
There are obviously many differences between EIFS and double stud walls, but in trying to understand the issue, there are some key points:
1) Undrained EIFS was installed on tract housing, which meant that the failures were large, well studied, and well documented. The costs and associated litigation ensured that outcome. That is not the case with double stud walls.
2) BSC created clear guidance on how to build EIFS walls correctly, and how to minimize that risk.
Double stud walls are confined to the highly custom superinsulated housing market. There is little focus on double stud walls. Because the building science industry has much bigger jobs to tackle, nobody is studying the subject. Meanwhile, custom builders are still erecting double stud wall houses. Why? Because they are trying to juggle the dazzling array of issues that confront the "green" housing market:
* Energy efficiency, or long term operational costs
* Embodied energy
* Durability
* Wetting / drying potential
* Material costs (or cost effectiveness)
* Global Warming Potential
* Material Sourcing
* Simplicity of design
* Familiarity of construction techniques
* Risks associated with new materials and technologies (unintended consequences)
It's clear that BSC favors exterior insulation, and that science supports that conclusion. Yet other variables point builders away from that direction (cost, GWP of foam insulation, religious belief in cellulose, fear of single direction drying potential), thus we have Martin's call for exterior insulation using the lower EE, lower GWP, vapor permeable mineral wool. So who is going to be the guinea pig? And how surely would the benefits and risks of this technique offset the benefits and risks associated with a double stud wall?
As I said before, there are a lot of questions, not so many answers.
Martin,
I don't think anybody took your comments as such---at least I didn't.
It's clear that you think my suggestion is naive or misguided, and perhaps it is . . .
The fact remains that we have builders erecting double stud wall houses today, shouts from leading building scientists that the technique has a durability risk, and 30-year old double stud wall housing stock that sits largely untouched, uninspected.
Thank you GBA & John Straube for the dialogue
I am hoping that John Abrams and or Marc Rosenbaum will comment
and defend their polished turds ;--)
Daniel,
thanks, I have looked at the report you referenced.
Thanks for keeping the Apples & Turd dialogue going.
I am more interested in the Apples & Turds than the Mineral Wool right now.
I share a lot of the thoughts in your recent comments.
I think we can build High Performance....
Low-Risk Enclosures without relying exclusively on Outside Insulation
I think this may open the door to...
Buildable, Affordable & Durable High Performance.
Mineral wool insulation seems to be more acceptable to most here, compared to say polyiso foam. I am confused as to why this is so. The lifetime GWP of mineral wool (0.0455) is higher than the polyiso (0.0317).
I think the problem is I was trying to be funny by saying apples and turds. Should have said apples and oranges. Both of them can be good for you but they are different.
There is no doubt that double stud walls can work, and do work. But as far as I know, the only research (measurement and calculation) we have show they are riskier than exterior insulation. Yes we should do more research to get better answers, and having Martin rip cladding of 30 houses WOULD be useful, very useful given the dearth of knowledge, but it would not be definitive either.
One of the reasons people want to use double stud walls is because they don't know how to use insulation on the exterior or they are disproportionately worried about embodied energy (which is a pretty small issue even for super insulation.)
We built a house with vinyl siding direct attached over 2" of 2.5 pound per cubic foot rockwool about ten years ago: this is as low as I would go, and would not recommend it. The house has since been sold and no one seems to know or notice (except that lots of dew forms on the vinyl siding relative to the neighboring houses, because the wall is better insulated).
If you use rockwool (we have played with Roxul) of 4-8 pcf, you can attach vinyl wood or fibercement lap siding with furring strips. The product is stiff enough for that.
Given that you backprime the siding to control inward vapor drives, this type of assembly is very safe, as in cold weather the OSB sheathing will be dried out strongly through the rockwool.
But, given that the industry is still confused about cladding attachement through rigid foam, we dont push people further to consider rockwool.... but some on this list might.
John,
If you attach vertical furring strips on top of Roxul, do you worry about wind-washing of the Roxul? Is it necessary to cover the exterior of the Roxul with housewrap before attaching furring strips because of this concern?
Here are a couple of ideas for using Roxul/rockwool products in a wall assembly. I'm assuming that the WRB is the sheathing, as well as the Air Barrier. Probably, from my naive POV, the most elementary approach is to attach i-joists/Larson Trusses (although an assembly that has pretty much only shear loads to be considered a truss.....) to the wall through the sheathing and into the wall studs. Then bays can be filled with Roxul. By the way, having used Roxul myself, its ability to be compressed and placed into a space makes it much easier to fill a bay than fiberglass. If thermal bridging paranoia is to be addressed, a layer (1 or 2 inch) of rockwool fiberboard can be placed over the i-joists. Then, as John Straube suggested, nailers can be attached over the rockwool board for the siding. If the "springy-ness" of the rockwool board is really objectionable, cut holes in the rockwool board with a hole saw and either use a plug of wood or high load XPS to attach the nailers to the i-joists.
Another approach would be to make up your own "holey" i-beam, but don't attach one flange. The other end is attached to the wall assembly; then the Roxul can be layed down in layers; the first is just layed in as any other batt insulation. The second is actually layed over everything and "ripped" into the "holey" i-beam sections. Then the top flange can be attached. I think with this approach it can be detailed such that the top flange becomes the siding nailer.
My final contribution to these approaches are to just lay the Roxul on the wall; cut holes along each wall stud in the Roxul with a hole saw (did I mention that regular Roxul batt insulation can be cut with a hole saw?) and create "plugs" with high load XPS. Bridge the plugs with the nailers for the siding.
Obviously I haven't addressed detailing around windows or corners, but I don't see why XPS can't be built up around those assemblies to provide interfaces to the Roxul field. Did I mention that Roxul's pretty cheap; $.80/sq ft at R-22 (5 1/4 inch)....
I would be interested in John's response to Martin's question regarding covering the mineral wool with some kind of a barrier (e.g., Tyvek).
The entire point of installing Roxul outboard of the sheathing is to keep the sheathing warm. If the assembly includes sheathing (even vapor-permeable sheathing) on the exterior of the Roxul, the entire purpose of the Roxul is defeated. You might as well just design a double-stud wall with vapor-permeable sheathing, and skip the Roxul, if the outermost layer of the wall assembly is going to be sheathing rather than insulation.
Which brings us back to the question, "What's wrong with EPS or polyiso?" All of us here at GBA, if we are being honest, must admit that calculating the global warming potential of rigid foam is very complicated and rests on many assumptions. It seems fair to say that EPS and polyiso are preferable to XPS, but I'm not yet convinced of the arguments against using EPS or polyiso to keep sheathing warm. Using fossil fuel to manufacture EPS or polyiso for this purpose seems to me to be a much better use of the fuel than burning it in a vehicle engine.
uh, all of these approaches assume that the Roxul are "outboard" of the sheathing.....sorry, if that wasn't clear....
We're obviously mixing a lot of ideas here, and that's okay . . .
"What's wrong with EPS or polyiso?"
To echo some ealier comments, it's not a question of right or wrong, of safe or unsafe---it's an infinite continuum of risk / reward . . . and a lot of personal prejudice thrown in to boot ;-)
Martin, I agree with your perspective on using petroleum to insulate instead of burn. The same can be said of wood: insulate with wood (cellulose) instead of burn it in your woodstove.
Garth - Perhaps drying potential, vapor permeability is driving the favoritism of mineral wool?
And, finally, regarding the compressibility of Roxul, their RockBoard™ 80 product is rated > 5 psi @ 10% deformation. In an earlier discussion, someone had mentioned that they are using sleeved fasteners in Europe when attaching furring strips; supposedly, the sleeve would engage the sheathing material before compressing the mineral wool. I can't find any such product through Google, but the concept sounds right (and is similar to commercial brick ties for cavity walls).
But I think the larger perspective here is that some people---I'm riding the fence, but probably that includes myself---look at the options, and see a solid wood wall (dense-packed double stud wall with wood sheathing) as more closely approaching the concept of "first do no harm." But if that wall isn't durable, then that conclusion is incorrect.
None of the rockwool samples I've handled would be dense enough to install strapping on top as you would with rigid foam. The highest density material (intended for roofing) would work but there's a lot more mineral and resin in that product and the price will reflect this. I think the best approach is to add some type of structural spacer that spans through the wool, even if that's just blocks of high density blue foam.
Cascadia Windows makes a "fiberglass thermal spacer" for light steel framing. This looks like a pretty serious system, for commercial applications. There also must be many ways to DIY something like this.
John Straube,
I realize you were being funny....
I also understand that you really,really prefer Outside Insulation.
I have a different (not-so-GWP) motive for considering not-so-outsulation strategies.
I am interested in Durable, Buildable & Affordable Low Energy Solutions.
I think the not-so-thick Outside Insulation strategy works for Joe Builder who wants to build an affordable better than code home.
I think it may be a different matter as we start thinking about Super Insulated Homes & extremely low energy enclosures.
If "Safe" assemblies CAN be built using Vapor Open Materials....
for example a vented attic or a double wall with vented cladding.......
Why strap not-so-buildable vapor retarder/barriers on the outside of walls and roofs?
The thicker the strap-on ....
the less "BUILDABLE" and less Affordable.
In your recent comment you noted that "the industry is still confused about cladding attachement through rigid foam"
I am not surprised that the industry is "confused".
I think it all gets pretty darn tricky.
I think some of the double wall designs would be much more "Buildable" than any of the Outsulation examples I have seen.
This Outside Insulation example does not look very "Buildable" or very safe to me.
Just imagine a house with more than one ridge or a roof with valleys.
Sorry this is unscientific, but intuitively a 2+" wool blanket seems like it should insulate pretty well even without a perfectly airtight layer to prevent wind washing. Think of a polar bear for example, whose thick fur insulates well enough even in the arctic. Now, maybe that bear would be warmer with a nylon windbreaker, but still there may be a lesson from nature here. So many "green building" materials and methods are all about plastics. Humans are the only animals that need tons of plastic to be prepared for winter.
There's been some back and forth on the topic of "walls that breathe", and some debate over semantics. My own conclusion is that I don't want walls to dry toward the interior and depend on ventilation to control indoor humidity. Rather, the shell should let moisture pass through to the outdoors. I find that gloves are not comfortable when they hold in moisture, at least not for long. Simple knit gloves (that "breathe") are more comfortable than less permeable ski gloves. Purely subjective and climate dependent, but there's one perspective.
Where is the Air Control Layer in this example?
Honey,
I might be late for dinner....
This is going to take a while.
Thomas,
You wrote, "Rather, the shell should let moisture pass through to the outdoors. I find that gloves are not comfortable when they hold in moisture, at least not for long. Simple knit gloves (that "breathe") are more comfortable than less permeable ski gloves."
We've had this discussion before, but bear with me. I hear your view a lot -- that we need to allow moisture to pass through building assemblies, because that's healthier than not allowing the moisture to flow. In fact, many old-time New England builders swear that ceilings should be deliberately designed as moisture safety valves for the home, in a way that somehow encourages the flow of moisture from the interior to the exterior.
This approach strikes me as odd. Obviously, we need ventilation so that the occupants have fresh air. But we also need to separate the interior environment from the exterior environment.
As long as the interior is 72 degrees and the exterior is below 32 degrees, it's going to be more humid indoors than out. Encouraging moisture to flow through your walls and ceilings isn't going to change this fact. Indoor conditions differ from outdoor conditions.
if you design your wall and ceiling assemblies correctly, everybody is happy without any vapor flow. During the winter, the interior is warm and humid, and the exterior is dry and cold, and the two environments are kept separate.
If any rain penetrates your siding -- and some of it will -- the siding needs a way to dry quickly. Ideally, however, there won't be much (or any) moisture flow from the interior into your wall or ceiling assemblies, because you don't want that to happen.
Martin,
My perspective is well outside the mainstream for this website or the public at large. I don't think it makes sense to expect an indoor temperature of 72° when it's freezing outdoors, except in sunny Colorado or New Mexico (and occasional cold sunny days here in the PNW). What I suggest is a good winter coat, passive solar design and then don't push the delta-T beyond what you can maintain with minimal energy input, ideally just body heat and a tea kettle.
I live in a newer code minimum building with great south exposure (~15% glass to floor area) but some poor design choices, including aluminum storefront type windows and patio doors. The heat source is electric wall units (used occasionally) and ventilation is a bath fan. There is frequently condensation on the windows and exterior doors, when the outdoor temp may be mid-30's and indoors maybe 60°. Humidity wouldn't be a problem if the interior were kept warmer, which is what I think you've suggested.
To be clear, this condensation anecdote isn't related to plastic foam per se (only the roof uses it) but I believe it suggests a value to higher permeability enclosures. Consider another example--if you ever see a car someone is sleeping inside, the windows are covered in moisture. This reflects insufficient ventilation, an impermeable enclosure, small air volume and low interior temperature. It's more likely to be a problem in a small home than a big one, and "true passive" operation (fuel the people, but not the building) can be problematic by increasing the relative humidity, when the indoor temp is well below 72°.
Thomas,
Condensation isn't a problem in a building with a decent thermal envelope. Of course you can get condensation on aluminum window frames or single glazing -- or even on double glazing in certain conditions.
The solution isn't to encourage vapor to flow into your walls and ceilings. The solution is to improve the specs of your thermal envelope with better insulation and more layers of glazing!
Martin,
I don't think condensation is the problem, it's a symptom of high humidity. Glazing in this example is 1" commercial type IG. I agree that better insulation and non-aluminum window frames would help, by allowing indoor temperatures to rise and relative humidity to drop.
Thomas,
You wrote, "I don't think condensation is the problem, it's a symptom of high humidity." You also wrote, "This condensation anecdote isn't related to plastic foam per se (only the roof uses it) but I believe it suggests a value to higher permeability enclosures."
Well, if you believe that your building is experiencing high humidity -- that's what you wrote -- then I disagree that the solution is "higher permeability enclosures." The solution is source control and mechanical ventilation.
Good lord, I wish we could put the double wall vs exterior insulation debate to rest.
Exterior insulation cons:
- EXPENSIVE- it costs more than a double wall
- Fastening issues- if you're using cladding other than horizontal siding, the fastening sucks. Yes sucks.
- WRB integration issues- can the average builder get the window/penetration flashings right?
- Hygric redistribution & hydrostatic pressure issues- moisture sandwiched between foam and OSB is no good.
- Global warming gases in the manufacturing process of foam board
AND...
What about end of life issues of foam??? Imagine what landfills would look like if ALL homes were built with 4" of EPS on the exterior of walls and roofs. Can't you just picture it? It will be beautiful! White plastic beads of foam enveloping waste fields all over the world. Ahhh 'twill be a breathtaking white winter wonderland!
I don't see a double wall-- with taped sheathing joints, acoustical sealant at the appropriate framing joints, and an Airtight Drywall Approach-- having much liability.
@ John B: you said --
"I think some of the double wall designs would be much more "Buildable" than any of the Outsulation examples I have seen."
The three builders I spoke with this past weekend hereabouts seem to agree. I offered each the alternative of exterior insulation (only 1" in 3A) or a double wall, each to 50% above code requirements. All three chose the double wall -- simpler they said, and cheaper, and especially better in getting a good job of detailing at windows/doors because local crews aren't familiar with exterior RFB.
I realize this doesn't have much to do with the long term success of such a wall, but it does explain the preference in another way.
Joe
is the double wall the best solution though for a retrofit?
it seems awfully more complicated than tacking on sheets of foam. also seems there is a lack of instruction available for those wanting to do a larsen truss retrofit, as far as specific details; and there seems to be more risk in framing around windows doors.
sure a seasoned pro can throw up a double wall, and sure they may have the experience to do a retrofit right, but the mass of contractors and do-it-yourselfers don't, nor have much access to good instruction and detail. a pro in main does no good for a guy retorfitting in north dakota.
and the EPS foam can be recycled back into more styrofoam products if you have a local collection site. i've dropped a pickup truck full off at a site that directly converted it for reuse. you need wood framing for the double studs which helps equal out the material issues, especially since it is near impossible to get well managed lumber.
Rockwool Out-insulation:
Utilizing Rockwool layers as the exterior insulation is fairly common practice in Europe on super insulated lightweight type wall assemblies. One advocate and pioneer in this regards is Odd Karl Steinsvik from Norway - a very knowledgeable character who produced first class projects...one of them is the famed I-Box concept. There are several pdfs to be found with good details on his approach if goggled. The furring is attached via standoffs that ensure that the dense bats of rockwool are not compressed. Same approach as when spraying heatlock foam on the exterior instead of using the more traditional foam sheets. It works very well and has good qualities but comes with its own challenges. Rockwool carries less embodied energy then foam but more than cellulose...and I found blowing in dense pack cellulose from the exterior on our new prototype wall easier, less transmission/bridging points - plus it is cheaper (T+M). My .2 cents...TC
Apples vs Oranges
Like John Straube I can't help it but have to voice my concern about this discussion - for whatever it is worth. Martin does not really have to take on a new job to poke around in buildings. Over the last 40 years millions $$$ of research funds have been spend to figure out the core to this answer. The Canadian government funded one of the bigger of these projects which ultimately created the PERSIST wall system - because after studying the multitude of problems in fairly new homes they concluded that it costs up to 290% more to replace degraded structural framing members than to build them new. The Research Council of Canada recommended a form of outinsulation approach in the early 1960s (!). Alberta Infrastructure, CMHC, CCHRC, BSC and a many more concluded in their studies in similar ways which gave birth to PERSIST, REMOTE or Perfect Wall - which all utilize a form of outinsulation and clearly defined pressure equalization layer (after all PERSIST stands for Pressure Equalized Rain Screen Insulated Structure Technique). Millions have already been spend to conclude that it makes more sense to put on your coat, instead of trying to swallow it if you want to stay warm and dry. Or that you will be just more comfortable with your insulation pad under you vs on top when you're out camping...especially in the winter on frozen ground.
How many of you in this debate have built double walls or out insulation wall systems? How many have spent the time to go back and do proper monitoring, analyzing and research on these buildings after they were completed? How many have gone back after 1-3-5-10 years on a ADA air sealed structure to see how well this type of seal holds up to everyday life in a home? Did you place a moisture probe behind your exterior sheeting? How many have designed double wall constructed buildings - and scratched their heads about the amount of lost living space, or tried to figure out the fine details on how to truly avoid thermal bridging?
Why does John Straube really, really like outinsulation? Because he has really, really done his homework, is very smart and has analyzed many buildings and a résumé to show for it. I have built any wall assembly you can imagine over the years and looked at them afterwards under a microscope - in my cold climate there isn't anything else which works as well as utilizing some form of outinsulation. I certainly don't claim to have all the answers and we build in an extreme cold climate and fight issues most folks will never encounter...but I know by now very well what works and what doesn't.
If you really do the math (and compare apples to oranges) outinsulation is not more expensive but yields a higher efficient building with less utility expenses and maintenance. There are no fastening issues with out-insulation, we have installed any type of siding there is. Sometimes you might need to get creative and there are certainly some limitations you can run into which will require some more conventional approach. "Hygric redistribution & hydrostatic pressure issues- moisture sandwiched between foam" - pls provide data, I love to take a look at this...with thousands of sensors and data logging of many years I have not seen any indication of this even in extreme temperature swings from 50 below to 12 above within two days. No argument about foam addiction...I certainly agree and spend a lot of effort (and money) on this problem to find more sustainable ways to achieve equal performance. Embodied energy and sustainability in buildings is very important but becomes a rather complex question if you really peel away on the many layers which make up the whole picture.
Let's not muddle the waters - everything in life has its pro and cons, but we really have to keep facts from fiction and we just simply can't make apples into oranges...and there are hardly any free lunches.
Moving to a radically different wall assembly requires a learning curve and there are no shortcuts around that. The first project simply does not count, the second and third are the learning curve and after the fifth you become good at it. If you want to build high performing homes that is just what it takes, and then some - to get there. If you can frame a house you can certainly build a REMOTE wall with no problem. In the end it is a matter of taste if you like apples or oranges better - and it boils down to choices we make. Just keep in mind that oranges have more vitamin C (70mg) then apples (9mg) and there just isn't any argument about that. ;- )
PS: Martin sums it up very well: "I'm a firm believer in distinguishing between research and anecdotes". Thanks!
PPS: John B. - how do you always get me mixed up in this?
Thorsten,
Thanks for your kind words and your excellent post.
I'm glad to hear that I have the support of at least one reader if I choose to keep my day job -- at least for now.
Thorsten,
I really, really like your new Arctic Wall.
https://www.greenbuildingadvisor.com/community/forum/general-questions/19942/sunrise-home
I think the best part (besides the not-so-foamy) is the Pressure Boundary.
You have really put the "P" in PERSIST.
I continue to think that A Simple and BUILDABLE Pressure Boundary is what is needed in all climates.
I also like the fact that the ARCTIC WALL allows vapor to flow thru.
I would still like to hear Marc Rosenberg and or John Abrams defend their "oranges"
John,
Is there any reason why you aren't satisfied with John Abrams' defense of his wall assembly choice, as stated in his JLC article and quoted in my recent blog?
Here's what Abrams wrote: “After years of experimentation with a variety of approaches, we have settled on cost-effective wall and roof assemblies that meet our insulation standards ... and minimize thermal bridging — and that our carpenters and other tradespeople are comfortable with.”
Martin,
I think Thorsten did a good job of defending the overcoat crowd.
I would still like to hear more comments from the "other side".
I think for most of AMERICA the Orange(not-so-outsulation) Direction
may actually be Less RISKY
Because it has the potential to be Simple, BUILDABLE and User Friendly.
Even You recommend it and Would not Hesitate to use it in Vermont.
And Affordable to-boot !!
A SIMPLE approach might mean that we would not need an
On-Site Building Scientist
Directing where to put the "Gooey-Stuff" ;--)
By the way... John Abrams ...
I like your window detail for the same reasons that I like your wall strategy.
Simple & Buildable & Affordable
and it planes-out with the your elegant pressure boundary.
John,
I always miss about half of your obscure references, John. What is the "orange direction"? Is that a call to move in the direction of Protestant activists from Northern Ireland? Or a call to move in the direction of supporters of the Ukrainian leader Viktor Yushchenko?
Sorry Martin
I was thinking of you when I added the (not-so-outsulation) after the "orange"
I noticed that others were calling the non-outsulation strategies turds and oranges....
Thorsten Chlupp said:
"Moving to a radically different wall assembly requires a learning curve and there are no shortcuts around that. The first project simply does not count, the second and third are the learning curve and after the fifth you become good at it. If you want to build high performing homes that is just what it takes, and then some - to get there."
This is one of those simple truths that seem to get lost too often. It's worth a bumper sticker, at least. Thanks for the reinforcement.
A pair of questions to follow on it -- if you were gong to be the first in your area to implement a technique which you believe in but which is "radically different," how would you proceed the first time?
And if I (as a consumer) believe in a technique but contractors are cautious, how can I increase my chances that their first try will be an experiment I will want to live in, and pay for (instead of a nice try that 'doesn't count')?
Regards
Joe
It’s all about balance.
Thorsten,
I do appreciate the research you have conducted up north. But, just because the REMOTE/PERSIST wall works up in Alaska doesn’t mean it’s appropriate for all climates. Yes, I have heard Straube and Lstiburek (who I have the utmost respect for) talk about the “Perfect Wall” working in climates ranging from Fairbanks to Miami. I don’t doubt that it works, but is it appropriate? In my opinion, no.
I admit that there was a time when I was gung ho about the REMOTE wall assembly. I have done a lot of research about the wall assembly and have read “Remote, A Manual” by the Cold Climate Housing Research Center many times. But I began to reevaluate my enthusiasm for the REMOTE wall and exterior foam in general when I smarted up and realized that it’s not JUST about energy efficiency. This is a green building website so I think that it’s appropriate for me to say it again: ITS NOT JUST ABOUT ENERGY EFFICIENCY. Certainly energy efficiency is an important aspect of green building, but there are other things to consider (I don’t need to go over these). And yes, durability is an important aspect as well but as Dr Straube pointed out in this thread: (referring to the durability of double walls) “there are things we can do to reduce that risk to get it down to the level of exterior insulation: vented cladding (aka "rainscreen" although that meaning is often lost), vapor permeable and moisture tolerant exterior sheathing (fiberboard, dense glas gold, even plywood), sprayed in insulation (cellulose is obvious, some fiberglass is now just as good), and exceptional airtightness”
Regarding your statement: “There are no fastening issues with out-insulation, we have installed any type of siding there is.” Please tell me how to fasten lathe for stucco and stone through 6” of EPS foam? I have asked this question about 5 times on this website and no practical solution. How bout Hardiboard and batten? Cedar shingles?
Oh and by the way, the deck fastening in the REMOTE manual-simple? And the foam and flashing around the fasteners- a breeze? Hardly.
And regarding the questions you raised: I know a good arguer does not answer questions with questions but I don’t care... call me a poor arguer.
Question: How many of you in this debate have built double walls or out insulation wall systems?
Answer: How many double-wall homes have you built outside of extremely cold climates? Builders have been doing so for decades without problems.
Question: How many have spent the time to go back and do proper monitoring, analyzing and research on these buildings after they were completed?
Answer: How many double wall homes outside of extremely cold climates have you conducted moisture/temperature monitoring in? I would love to see a study conducted on moisture problems in double walls. If there is a moisture problem with double walls in climate zones 4/5/6/7, I’ll put double wall construction on the shelf.
Question: How many have gone back after 1-3-5-10 years on a ADA air sealed structure to see how well this type of seal holds up to everyday life in a home?
Answer: Have you ever read the ADA info sheets on BSC’s website? I didn’t invent the Airtight Drywall Approach. I trust the Doctors wouldn’t include an info sheet on ADA if it was silly and didn’t work.
Question: Did you place a moisture probe behind your exterior sheeting?
Answer: Have you placed moisture probes in double wall homes outside of extremely cold climates?
How many have designed double wall constructed buildings - and scratched their heads about the amount of lost living space?
Answer: Did you know it’s 6 inches?
Question: Or tried to figure out the fine details on how to truly avoid thermal bridging?
Answer: Have you seen the other double wall discussions on GBA?
Again I wish we could put this debate to bed.
Do we really have to debate the foam in GREEN homes issue? Can’t we all agree that building with copious amounts of foam isn’t green building? Don’t we need to BALANCE energy efficiency, embodied energy, green house gas output in manufacturing, and material end of life issues?
I’m so tired of this. I’m so tired of SIPs, ICFs, and thick-foamed walls being included in green building discussions.
Please bring back Robert Riversong, I can’t fight this fight anymore.
Brett,
Debate is good. It's how we all learn. Of course, totalitarian societies discourage debate. Healthy universities encourage it.
So why do you say, "Again I wish we could put this debate to bed ... I’m so tired of this"? I'm sorry you're tired. Take a vacation, Brett.
We're all learning from this discussion. I say, let the debates continue.
Martin,
Come on, of course a healthy debate is a good thing. But we shouldn't be debating the obvious.
Brett,
You wrote, "we shouldn't be debating the obvious."
Evidently it's obvious to you that certain materials are off-limits to green builders, which is why you wrote, "I’m so tired of SIPs, ICFs, and thick-foamed walls being included in green building discussions."
But attempts to shut down debate on the issue are ill-advised. I think we all need to hear both sides of this issue.
Someone really smart once said to me that the dumbest thing to do with petroleum is to burn it.
Just because foam is made from oil does not mean it is not 'green'
Is a prius not green because it is not made from hay bales?
Are Pv panels green? Ever seen what hydrofluoric acid does? Or Silane gas? Cant PV without em.
We live in a technological world, a world where people can think of really really cool ways to conserve, and really really cool ways to waste.
Which side are you on?
Everything else is just noise
Brett,
Just to address one question you raise, here's how to do cedar shingles with out-insulation: First have two frames, either Riversong style or with panel sheathing on the outer face of the inner frame. Thorsten Chlupp described the latter as out-insulation. Cover the outer frame with Typar, then 1x4 horizontal boards at 8" on center vertically. Shingle over that, and dense pack the cavity.
I'd be leery of how the siding directly contacts the WRB, with cellulose against that, in the Riversong wall. But that's a model of minimum resources used in construction. Adding horizontal 1x4s creates some space between the cellulose and the shingles. This wall is also vapor open toward the exterior. It would be easier to make exceptionally airtight if there were sheathing over the inner frame (as mentioned) and then services only to the interior of that. Thorsten suggested you wouldn't need to insulate the inner frame for less than Arctic climates, but it depends on how thick you want to make the outer cavity.
As described, this has no cold sheathing (unless you count the widely spaced 1x4s), potentially very low air leakage (with taped plywood sheathing) and minimal risk of homeowners undermining the air barrier. If all the insulation is at the exterior, the structural frame stays at room temperature. Should be a very low risk solution.
Keith,
I'm sorry, but if this "really smart" individual you talk about is suggesting that instead of burning oil we make plastics from it, this individual is NOT smart. We don't HAVE to use oil. Heres an novel concept... keep oil where it belongs- in the sea floor 5,000 ft below the ocean's surface.
And yes, I would not call a Prius green. Cars aren't green. Driving is not green. Is a Prius a fuel-effcient vehicle? Yes, but it aint green.
"We live in a technological world, a world where people can think of really really cool ways to conserve, and really really cool ways to waste. Which side are you on?"
What kind of a question is that? As if I'm "wasting" by advocating a double wall assembly over a wall with a boat load of foam.
I have great respect for Betsy Pettit, John Straube, Joe Lstiburek, BSC and Building America.
I have never designed or built a "superinsulated home" or even a "double-code-R-value" home.
I am merely an Architect who believes we need to make a radical shift in the way we build all of our homes.
The shift needs to be Affordable & Buildable.
I don't think we should abandon or not consider outside-insulation.
I believe there should be more attention paid to the strategies that do not depend on Extreme Outsulation.
I say this because I think the Extreme Outsulation examples seem to be
Extremely Not-So-Buildable.....and Not-So-Practical
Unless you live in the Arctic ;--)
John, I disagree that we need to make radical changes in the way we build, for the simple reason consumers and builders don’t want radical changes. It isn’t happening except for .0001% of the people building houses. I’ve been hearing dire predictions for decades about energy costs, we get the occasional spike but nothing is happening that makes the average person want to build to the extreme described here. And consumers, not Building Sciences drives the market.
I am a very pragmatic person, I believe some easy, affordable common sense changes make much more sense. Crawl, walk, run. Make it too difficult or complex, 99% of builders and consumers will resist.
That’s my Saturday morning mini-rant.
Allan
https://picasaweb.google.com/edwards.allan1
Allan,
I did say radical shift not radical change.
To be buildable it needs to build on the skills we already have.
Brett,
I disagree on oil, I see no problem with using the resources at our disposal to solve a problem. You can pretend you can live in a world without oil, but you cannot, and will not in our and our children's lifetime. It is a resource like steel and copper, even wood. Renewable is 'better' but when you are not wasting something by burning it away, it is not as important.
Look around you at the housing stock, most buildings will stay intact for a minimum of 50 years. Most foam products will stay exactly where they are put practically forever.
Well, driving is not green, neither is building new houses, we have enough damn houses so knock it off.
Wasting by building double wall? Well, maybe i could try and make that point, but it is hard to imagine someone missing my point by more than you did.
Everyone here is on the same 'side' as far as i can tell.
If you had stated 'IMO double wall with cellulose is the greener all around alternative' or somesuch, I think you would get little friction.
When one goes off on the 'foam is evil' tangent people will start suggesting you re-point your tin foil hat.
Oil companies loooove it when environmentalists fight wind power and PV and insulation. Makes them happy happy happy.
Especially concerning retrofits, talking people out of foam plays right into their[oil companies] wallets.
John
I'm all ears. I'm on the frontlines building houses every day, tell me what to do that is affordable, has real impact, is easy or at least semi-easy to implement. Not theory, but pragmatic advice. And works in Sun Belt states and climate, where 90% of new homes are being built. Not Vermont or Alaska.
Allan
I don't know how I (or anyone) could disagree with John's recent position:
"The shift needs to be Affordable & Buildable.
I don't think we should abandon or not consider outside-insulation."
If so, maybe it would help if the discussion took two steps -- A) itemize ways outsulation is NOT(presently) buildable or affordable or (if you insist) "green." Perhaps this varies by CZ?
B) suggest solutions for the "problems." if such exist. And list the solutions in a thread, perhaps with details (like Lucas and John have done several times).
I've heard of only two problems, actually. (Though I willingly admit that my knowledge gap is a black hole.)
The first is that foam ain't "green." This thread began as an attempt, in part to deal with that objection with a discussion of mineral wool. It doesnt' sound like many experienced folk are happy with wool as an answer though. What else can be used?
The second comes from local builders who indicate that exterior insulation is way too pricey to install because crews don't know how to detail it (especially at windows and doors) properly. But there are step-by-step diagrams (for RFB) available from BSC as well as here at GBA and in several of Martin's blogs (iirc). Are those satisfactory -- can I give a stack of detail sheets to a contractor and say: "bid the job using this detailing, please." Or are the available details defective in some way?
Are there other problems? If so, what? Please don't tell me -- a consumer -- that this is one of those debates that sounds practical and useful but is actually just a subjective matter of individual values and habit.
Regards,
Joe
Allan,
I think half of a good and buildable starting strategy is in this article
http://www.jlconline.com/cgi-bin/jlconline.storefront/4d725ada105d6d3e27170a32100a063c/Product/View/1101hig
Have you read the article?
I would not call it Affordable or Buildable because of the Roof Assembly.
I would suggest substituting
an Airtight Attic Floor and a Ventilated Attic.
Here's another illustration of why Compact Roof Assemblies are
Not-So-Buildable
and Not-So-Safe.
Joe,
Jesse Thompson posted this link on another thread.
http://passivehouse.us/passiveHouse/2010_Passive_House_Conference_Presentations,_November_5_files/2010%20Conference-Rue%20Evans-Blake%20Bilyeu.pdf
(warning large file)
The project illustrates an Apples & Oranges Approach
translation....Outsulation combined with double wall
the amount of outsulation is not too crazy and it is not a vapor barrier.
John,
Yes, I remember reading the JLC article and thinking to myself, "this is great, I just wish the homes had a flat attic floor framed with high-heel trusses and a bunch of cellulose."
Cathedral ceilings belong in cathedrals not homes.
Allan,
Your comments demonstrate a serious lack of long-term perspective. Human civilization didn't start with your grandparents, and your own lifetime has not included a particularly large fraction of history. In fact it has included a bizarre and exceptional period in history when humans exploited resources at a rate unprecedented in the millions of years of history prior, and which will be short lived (as your grandchildren and even your children will understand).
Yes, the dire predictions of the 70's about energy running out or population exploding have not yet been proven by the end of the American Way of Life. You could choose to believe this proves that oil is infinite, pollution will never accumulate enough to matter, people can keep doubling in number every 50 years, and all that matters is for builders to serve popular demand.
However, my generation has begun to see the truth: for a very short period of history (a few generations) affluent westerners have taken for granted that they could consume whatever they could "afford" and disregard all issues of waste or depletion. This turns out to be unsustainable, and it won't be sustained much longer before it's impossible to continue. Some of us have become early adopters, taking steps to need less and trying to pay attention to the consequences of our actions. That's what this conversation is about.
I can respect both sides to this argument, as it relates to new construction. So what would you have me do to my house in a retrofit application. Surely tearing it down and starting over isn't the "green" thing to do. What about the many millions of homes in low income areas that have lead in the paint? As has been said before, building a new home period isn't "green", kind of like driving a hybrid isn't "green".
Aaron,
concerning not-so-foamy retrofits
perhaps a mineral wool overcoat similar to the illustration from the Lumar Video in my original post?
Bret, I am afraid you did not quite get my point or my concern I have with a traditional double wall approach. The goal of all the research I referred to was to address the cause of the endless amount of homes which started to develop serious problems…condensation, moisture buildup, rot and mold. This has nothing to do with energy, or with “GREEN” but with the fundamental truth that we build homes which are very unhealthy – and which develop often times problems hidden away in the wall assemblies – unknown to the occupants. Effecting their daily life’s and health in often times still not quite quantifiable means. Bad indoor air quality unfortunately is nothing which we can see and often times it affects us over long periods of time.
The pressure equalization layer is the key to ensure that a assembly works, that it does not develop moisture and maintains its structural integrity. That is its primary and most important function – and at the same token it ensures also your energy efficiency. But first and foremost it is about health and longevity of the structure. Our health is priceless.
That is why Passiv Haus places such importance on your airtightness – your pressure equalization layer – which so many here in the States find so excessive. If you really understand the importance and implications of the building physics at work than this really doesn’t seem such a drastic measure. Building Scientist in the 1960s already concluded this simple fact…but still 40 years later we are being ignorant on how we go about this problem and its solutions. I have looked at plenty newly build homes with severe moisture and mold issues and unfortunately probably 90% of the new homes build today are built on flawed principles…which is for me very frustrating to see. Does my extreme climate relate to more moderate climates – and does it hold true there as well? Absolutely – with the exaptation of a time shift. I am very lucky to be blessed with extreme temperature differences and problems show up very quickly. In more moderate temperatures the same physics are at work but simply take more time to manifest themselves. I am not saying that double walls don’t work if done properly. But they place your core layer at a very risky position…and that position comes with its limitations. That is just a simple fact. And I personally just believe that good is simply not good enough in our day and age. Out-insulation does also not have to equal layers of foam…there have been many variations and we continuously working on better and simpler solutions. My plea is to not be ignorant to your most important layer – the pressure boundary. Design it well, continuous and seal it very tight – and last but not least – keep it protected from the environment in and outside. IMO it should also be kept diffusion open in BOTH directions…
Any new building build today is a grand opportunity – or a liability in the near future. We simply should not build anything else anymore (including retrofits) that is not at least 80% more efficient and ensures a healthy and very durable structure with a life span of a minimum of 80 years. We are faced with a challenging future and everything else just simply makes no sense if we look at the true economics and values. Of course that will not happen on a grander scheme until the reality of sky high energy costs will make anything else impossible. Until then we as individuals can make choices as we see fit. Energy is the grandest problem we will be faced with in the not so far of future and all of us hold one or another piece of the puzzle in our own hands…and we all can make a difference if we set our minds to it.
Please build responsible. TC
Thorsten, as you know... I am an Architect and not a Building Scientist.
I try to "visualize" thermal & vapor flow....but I can not completely wrap my head around it.
I CAN visualize 3 dimensional Geometry and "layers" rather well.
I think the Geometry of the Plywood "pressure equalization layer" in your recent SunRise Home is damned elegant.
I also think the Geometry of the pressure plane in the John Abrams/Marc Rosenbaum example is elegant.
I can not say the same about most of the GBA,BSC and Building America examples and details.
I can guess that you will say we need both... a damned good pressure plane and a tuned thermal overcoat to protect it.
I am pretty sure you subscribe to JLC and have access to the John Abrams article.
http://www.jlconline.com/cgi-bin/jlconline.storefront/4d737f4e02c4437527170a32100a0645/Product/View/1101hig
Can you explain why/how/where you think the Rosenbaum/Abrams strategy might "fail" ?
John
I have a problem with the Abrams roof. What happens when re roofing is required? There are now thousands of nail holes in the air barrier. I suppose a layer of Ice & Water would do the trick, but will the owner even know that this must be dealt with?
Thomas Jefferson:
I will stand by my statement:
" I’ve been hearing dire predictions for decades about energy costs, we get the occasional spike but nothing is happening that makes the average person want to build to the extreme described here."
I'm only describing things as there are, not as they should be. And as I have spent my entire adult life building houses, I have to deal with home buyers' priorities and where they want to spend their money. Sure, I can try to educate them to some of the methods discussed here, and I try to incorporate good building techniques, but at the end of the day I build the kind of house they want.
Allan
Garth, I agree about the Abrams Roof
Just Another good reason to go with Ventilated Attic.
The desire to "occupy" the roof has turned the fork in a bad direction.
There is also the question of the not-so-vapor open ZIP sheathing in a Cold Climate.
Since the Mixed Climates are the forgottens
What about "HomeBuyer Joe" who lives in a Mixed Climate?
What is wrong with the "Abrams Wall" in a Mixed Climate
Like Georgia or North Texas?
Martin Holladay endorses...actually recommends a Double Wall for Vermont.
Seems like it would "work" in a mixed climate if it "works" in Vermont.
John Abrams is not the only one building the Marc Rosenbaum style wall.
Dan Kolbert, Jesse Thompson, Christopher Briley
Do you have any comments?
I would never do double wall construction in my climate, I use 2x6 and Icynene open cell and I like installing some some reasonably thick foam board on the exterior. When Joe Lstiburek spoke to our local HBA that was actually his recommendation too. I also don't like the detail around windows and doors of double walls. And it also cuts down on your livable interior sq footage.
Allan
Allan,
You are not at the HBA forum
this is the GBA
What's your point John, I was relating some of Joe Lstiburek's recommendations about building in a hot humid climate.
Allan,
I think that Joe's Advice is probably good for the HBA.
You and the HBA are not-so-interested in extreme Low Energy.
John
There's not much in life that I'm interested in that is extreme. I think Joe gave good advice for this climate, where I might point out 27,000 new homes were built last year (Houston), in a down year. Point being that the Building Science community should focus more on climates where most new homes are being built and focus on non-extreme methods that, if used, will have much more beneficial impact than the extreme.
But carry on anyway.
Allan
Allan,
Joe has also said something to the effect of.......
for the sake of our Children
we should double the "current" R-value
or maybe it was....
whatever you "think you need" for R-value...double it
For the love of god Allen.
The idea is to identify methods to achieve "extreme" performance without having to resort to "extreme" methodology.
"0.6ACH_50 made simple" for example.
Simplicity is the key to high-performance at less cost.
Material choices impact on simplicity.
Fastening thick foam panel "outsulation" is not simple.
Spray foam is not simple.
Besides Allen, if "extreme" performance could be built into the envelope for little more than "non-extreme" performance, your customers wouldn't even know the difference.
Although I have my doubts that homes as complex as the ones you build could ever be good candidates for "0.6ACH50 made simple".
Lucas, you said:
"Although I have my doubts that homes as complex as the ones you build could ever be good candidates for "0.6ACH50 made simple".
That's another observation I have of extreme Low Energy homes, they are so small and so simply designed it is much easier to make them very efficient. It is much more challenging with larger and more cut up 3 story homes. But I'm trying, I really am.
Allan
Allan,
You are closer than many builders to having a Simple Pressure Boundary.
You already use the ZIP wall system.
All you need is a gasket at the bottom of your wall (ala Rosenbaum) and you would no longer have to depend on Expensive spray foam to complete your wall air barrier.
You probably already use I-joists for many of your ceiling Joists?
(custom builders in Dallas often use I-joists for ceiling joists.)
Why not get rid of the HIGH dollar, outgassing, (less than code R-value) sprayfoam at your roof deck?
Spend the money saved on
....An attic deck pressure boundary(plywood&tape)
....MORE than code minimum R-value above
....the cost of a few Air Handler closets.
John - I think you hit upon a key point when you said that the mixed climates were forgotten.
Much of this discussion is viewed through cold climate goggles. And the majority of the research is there too, thus we have: Alberta Infrastructure, CMHC, CCHRC, and BSC (although BSC covers a lot more ground and climates). Even Passivhaus wears those same goggles---and GBA too. I don't say this to downplay the value of these organizations and companies, since a lot of the information DOES carryover to our climates. It's just the way things are . . .
And way down south, the Florida Solar Energy Center has a lot of great research on cooling dominated climates & building techniques.
But in the mixed climates---we're sitting in the doldrums.
How does a "traditional" double stud wall (exterior sheathing layer) perform in Climate Zones 3A & 4A, where summertime solar vapor drives are a big deal? Almost all of the discussion here centers around cold weather sorption, and winter time moisture accumulation, NOT vapor drives in the other direction . . .
Reading through this thread there seems to be some confusion as to what constitutes "outsulation".
Is there a definition for "outsulation?
What exactly is the insulation "outside" of?
If I had to guess - or make my own definition - I would say that "outsulation" is insulation located "outside" the primary air barrier.
Maybe the question shouldn't be "Where is your insulation?" but "Where is your primary air barrier?"
If the "outsulation" approach can be applied "from Miami to Maine", then maybe the biggest problem is in determining the most suitable material and permeability rating for the primary air barrier for the given climate zone...
Lucas,
I'd say the "out" in outsulation (or out-insulation) refers to the structural frame. It suggests insulation wrapped around the structure, an "overcoat". Locating air barriers is a separate issue.
Speaking of which, I'm not clear on the phrase "pressure equalization boundary", because I read this as the same thing as an air barrier. How is pressure being equalized?
Thomas,
you may want to check this out
http://www.homeenergy.org/archive/hem.dis.anl.gov/eehem/99/991108.html#fig1
Thomas, not-so-long ago I would have agreed with you.
Now, I'm not-so-sure.
I wonder if "the structure" isn't best thought of as seperate from thermal and air control layers.
The problem as I see it is that defining "the structure" can become very ambiguous.
For example, in the ARCTIC wall, Larsen and Riversong truss walls...
Are the outer components of these walls "structure" or simply a means of fastening additional insulation?
A little bit of both, but what is the more meaningful purpose?
As far as "pressure equalization boundary" goes, I believe it refers to an ideal that an air barrier isolates air pressure variation on the "inside" from air pressure variation on the "outside"...
Though I'm not sure what is being "equalized" either...
Well at least I am doing a good job getting everyone confused.
Definition of Out-Insulation:
1. The pressure boundary or airtightness layer is placed on the outside of your structural sheeting between the framing and the exterior insulation layer. In the early days this layer was completely sealed with a 60 mil peel and stick rubber membrane, later your typical 6 mil poly vapor barrier was used or taped Tyvek. Taped and sealed CDX plywood works excellent and creates a diffusion open boundary which allows drying potential in both directions.
2. The exterior framing is now part of your conditioned space and is utilized as your utility chase - electrical, mechanical, and plumbing...which opens many more options on how you can run your utilities. It is your structural building core. It can be insulated if additional R-value is needed and the 1/3 to 2/3 insulation ratios in-between you pressure boundary is maintained...I actually think 40/60 is still a safe ratio.
3. The insulation is wrapped around the exterior of the structure and keeps everything warm and is protected with a weather barrier.
4. Vertical strapping attaches to the main structure with long fasteners or in form of a Larsen type truss design depending on the design and insulation used. This creates a rain screen and drainage plane - which promotes the equalization of the pressure outwards, which in turn ensures the wall assembly can dry to the outside. IMO this is very important if cellulose or mineral wool is used. If foam sheeting or spray foam is used as the exterior insulation this of course is a moot point...REMOTE walls can only dry to the inside in reality.
5. Siding of choice is attached to the strapping, which is plenty strong to support the weight...with engineer approval.
6. Roof assembly is separated with the same pressure boundary and built with a vented cold attic roof truss (with exterior access). The same basic physical principles of air flow and temperature differentials ensure pressure equalization and drying potential to the outside.
NOTE: The key difference of an outinsulation strategy is not only that insulation is placed on the outside of the core structure but also that your critical pressure boundary (or airtightness layer) is CONTINUOUS and PROTECTED from both directions. This layer will stay untouched and functional for the lifespan of the structure. From my experience drywall/gypsum/6 mil is just not a very durable material choice to handle a critical building function.
Summary: Insulation where it belongs - on the cold side, thermal bridge free construction, protected placement of your main defense of moisture, and easy to use utility chase now and in the future.
John B. - if you can visualize the flow of moisture and what drives it you can figure out for yourself were the key difference really comes in. Again, I am not saying that double walls are evil and cannot work. I have built plenty, but surely won't do so anymore...and I for sure would not put an unvented hot roof on a building.
Allan, I completely understand what you are saying...you cater to a special breed of clients and your business model is difficult to fit into a more sustainable building approach. Therefor I really comment you for being open to consider other building methods. We absolutely need builders like yourself to drive this idea forward and better our industry. I certainly disagree that more complex buildings like your typical custom homes can't be drastically improved in regards to efficiency...and maybe indoor air quality - no idea what you're doing here so far. Your climate zone is very different but also a lot less hostile then mine...which might be the reason why like you state 90% of new homes are built in your belt. Any new home build in such a climate should be operating at a carbon neutral level. Have you done a top done analysis on where your main consumptions are in your homes? Hot water as an example - how do you make it and distribute it through the fairly large mansions you build? Are the lines insulated? Are you utilizing an on-demand recirculation system? Right here you could increase maybe efficiency by up to 90% depending on what you do right now. Solar thermal systems? Are you installing any energy monitoring for your clients to help them understand were consumption comes from?
In my experience most clients are really not stupid - but simply ignorant when it comes to health or energy upgrades. Nobody ever complained to me if I spend $1200 of their hard earned money to save them $600 every year for the next 20 years...Trouble is you can't sell them on something if you haven't thought about it yourself.
There are so many pieces to building truly efficient - and healthy homes...and it really takes commitment to chip away piece by piece. Consulting with an energy expert and investing in some energy modeling might be an invaluable investment you make to help you improve this part of your business.
Something to think about - keep up the good work. TC
If "outsulation" works from "Miami to Maine"...
A warm in winter air barrier is good for all climates?
The air barrier and it's tape stay warm, dry and protected?
Why does the location of the "structure" matter in relation to the insulation?
The air barrier might be part of the "structure", but it is more importantly the air barrier.
Why not just worry about where the air barrier is in relation to the insulation?
Lucas,
About your image with the horizontal 2x3 furring: I think this would make sense if the cladding needed a horizontal support, e.g. vertical board and batten. For horizontal siding it would make more sense to have spacers at the intersections (where the 2x3s would cross vertical furring).
Also there's nothing too ambiguous about "structure". When I suggested this is what defines "out", the structure is the loadbearing frame rather than furring that supports the cladding. That is, the primary structure. In the Riversong truss both frames are structural, because the outer frame supports the roof.
This is not an example of out-insulation.
The advantage of having the structure inside a thermal wrap is (or should be) durability, when the primary framing is essentially indoors and protected rather than outdoors.
Thomas, the 2x3 furring is at the inside of the wall for a service cavity and interior cladding. but I agree that vertical blocking at 8' centres would probably be a good idea.
This is not true. The exterior framing in the Riversong truss only bears the weight of the cladding, insulation and possibly windows. The roof bears on the inner structure. I believe Robert's houses use vertical 2x3s (I think he even told me once he's used 2x2s) to create the outer balloon frame.
For my own purposes I have gone to using vertical 2x4s so as to accomodate Roxul batt insulation (I don't have the means to do dense pack cellulose).
Not-so-foamy "outsulation" using Larsen truss.
Air control layer in red.
Thickness of "outsulation" and permeability of air barrier to be determined for specific climate.
Insulation to the "outside" of the air control layer and "structure".
Less-ambiguous definition of "structure".
Front and back perspectives:
Not-so-foamy "outsulation" using Riversong truss.
Air control layer in red.
Thickness of "outsulation" and permeability of air barrier to be determined for specific climate.
Insulation to the "outside" of the air control layer.
Insulation amid "structure".
More-ambiguous definition of "structure".
Front and back perspectives:
Lucas,
Nice Work!
Your "post 89 " version IS VERY similar to an ATTIC scenario.
where the insulation and the structure can "share space"
It will be interesting to hear what Thorsten has to say.
Version 88 is "like" an attic as well
It is "like" the attic in the SunRise Home
the Trusses sit "on top" of the Sheathing
as far as keeping layers consistent....
seems like 88 is more continuous
I suppose what I'm wondering is...
If the air barrier is the structural sheathing as in the two drawings above...
Is it really that important where the load bearing studs are?
A vented roof has much uninsulated structure, yet they are often regarded as "safer".
Isn't it more important to make sure that the air barrier is in the right location?
If the air barrier is well protected and warm... and consequently performs well for the life of the structure, that should help protect the rest of the structure - regardless of where it is located in the envelope profile.
Thomas,
Sorry, I'm still trying to sort my own thoughts out...
I agree there is nothing ambiguous about what is structure.
I think what I was suggesting is what should be considered "out" gets ambiguous.
Could either of these wall profiles be considered "double stud" walls - "turds"?
They both rely on two rows of studs, being that the outermost are more substantial than typical furring...
If Thorsten's profile can be considered an "outsulation" approach despite using an outer row of studs, why not the Riversong profile?
John, thanks.
I agree that #88 is more continuous - it avoids the rim joist "bump out" between levels.
I think there are other advantages to the #88 style as well.
However, I think the Riversong truss is very elegant with ADA and no service cavity...
Maybe just not appropriate in it's most elegant form in all climates.
And maybe just not quite as "tight" as a taped plywood system.
1. could anyone provide an estimate on the overall R loss of a foamy wall versus a not so foamy one due to the increased thermal bridging (each walls total build R value being the same)? that is if it is significant. the battens ina foamy wall connect via the metal screws, but there is a bit more structure connecting back to the sheating in the other walls.
2. in the riversong truss, what is commonly used for the inner exterior wall gusset - the part that connects the old wall sheating to the plywood arm - ie what type of bracket either bought, brand names, etc or crafted is used?
3. is there any concern about the weight of all that cellulose? in a retrofit, a deal of it rests on whatever bottom plate you fashion. there never is a detail on the type of connection made to that bottom plate hanging out over the ground. the pics in 88 don't even show one
Bob,
1. My opinion is that the thermal bridging in either of the wall sections illustrated in 88 or 89 is small enough to be insignificant. I calculated (roughly) once that the cross-sectional area of "thermal bridges" in a Riversong truss wall (ie: through the gussets) is something on the order of 0.5% of a standard 2x wall 24" OC with no attention to thermal bridging.
2. Gussets for a Riversong truss would be site-built. In my case using 3/4 inch plywood. Robert uses 1x dimensional lumber. Plywood gussets might offer some extra strength but it is much easier to cut the gussets from 1xs.
3. The drawing in post 88 is not meant to be comprehensive and omits many crucial structural details. Both truss walls (88 and 89) use load bearing inner walls (the roof and floor framing bear on the inner frame). The exterior trusses bear on the foundation but are only carrying the weight of cladding, insulation and possibly windows. If you would like more detail on my adaptation of a Riversong truss, you can find it here:
https://www.greenbuildingadvisor.com/community/forum/plans-review/19568/detail-directory
Photos of one of Robert's houses can be viewed here:
http://www.builditsolar.com/Projects/SolarHomes/LarsenTruss/LarsenTruss.htm
thx for the reply lucas
for point 3. looking at the example image below, you can see the bottom plate - highlighted with a red box - would hang out from the foundation and bear quite a bit of weight with a large volume of dense pack cellulose above it. this image shows no support either like the prior ones above
without prior experience, it is hard to determine how 'strong' to build....
I did find a good example to help decipher the gusset construction...
interesting in that this diagram seems to indicate running a batten along the sheating for attachment, although i'm sure you could just use pieces long enough to attach the plywood rather than a full lenght piece