Explain the correct usage of rigid insulation on the exterior of the building.

Rigid insulation seems like a good choice to add R-value to the whole wall (breaking the thermal bridging, etc) as opposed to just between the studs like most insulation. But isn’t it basically impermeable and thus not allowing the wall to breath…not allowing moisture from the inside to exit by diffusion.
GBA Detail Library
A collection of one thousand construction details organized by climate and house part
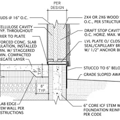
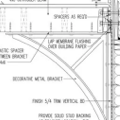
Replies
Adding exterior rigid foam board is one of several ways to add R-value and reduce thermal bridging, and it has become a favorite among builders who want a quick and easy way to meet those goals. It is also touted by building scientists as a way to decrease the condensation potential on the interior surface of the plywood or OSB sheathing by moving it toward the warmer-in-winter side of the thermal gradient.
As you suggest, there are potential problems. In a cold climate, the vapor drive and vapor-laden air movement is primarily from the inside to the outside of the thermal envelope. Given that no wall system can either be built or remain perfect for the life of the house, it is wise to allow a wall to "breathe" or allow water vapor permeance to the exterior.
Only foil-faced foam board (polyisocyanurate) is a vapor barrier. But the more commonly-used XPS (extruded polystyrene, or Styrofoam) has a vapor permeance of 1.1 per inch. This places it just a tad short of the conventional definition of a vapor retarder (perm = 1). But in a cold climate, 2" of exterior foam is typically required to prevent the sheathing from reaching the dew point, and 2" of XPS has a perm rating that places it squarely within the vapor retarder (class II) category.
It has long been considered good practice, in a cold-climate home, to have an exterior "skin" that is at least 5 times as vapor permeable as the interior "skin". Summertime vapor drive, at least when the sun is shining on a wall, is from outside to in. But a layer of exterior foam will significantly reduce the temperature-driven moisture movement toward the interior.
Long-term studies (2 years) have demonstrated that, in the event of minor exterior rain penetration, a wall system with exterior foam does not ever dry out and, because it is warmer in winter, remains above the mold danger zone (temperature and humidity), whereas a wall without exterior foam has opportunities for cyclical drying.
Other methods of increasing R-value and reducing thermal bridging include, double-frame systems, cross-hatched walls, and interior foam board. The first two can be insulated with dense-pack cellulose, the most green of all conventional insulations. There is much debate over whether any petrochemical foam can legitimately be considered a green building material.
So then.....where is this building practice used most effectively? What climate zones?
I have never used the system but have heard it recommended by a number of building scientist. John Straube, I believe, recommended it for virtually every climate zone. Then I was wondering whether it was a good idea to tape or caulk the joints. Or it would seem that you would need an additional vapor barrier like Tyvek on the outside of the foam. Then rainscreen spacing. Seems easier and safer to just stagger your wall studs to eliminate thermal bridging.
It is primarily a cold-climate strategy. Straube and Lstiburek would not recommend this strategy for all climate zones (perhaps ICC zone 4A, certainly 5 and above and possibly 3-B). If the exterior foam board is used as an air barrier or weather barrier, then joints should be sealed.
Housewrap (weather resistant barrier - WRB) like Tyvek is NOT a vapor barrier - quite the contrary, it is one of the most vapor permeable building materials available. It is relatively resistant to liquid water and air. Be careful about applying a polymeric WRB outside of exterior foam board and under a rainscreen, as this leaves it vulnerable to air pressure differentials.
Conrad,
Unlike Robert, I have few reservations recommending the installation of exterior foam on almost any building in North America.
I think Robert is wrong when he says that "Straube and Lstiburek would not recommend this strategy for all climate zones." When I interviewed Joe Lstiburek for an article on PERSIST construction (a construction method where thick foam is installed on the exterior side of wall and roof sheathing), Lstiburek told me, "It will work from Fairbanks to Miami." Read more about PERSIST here:
https://www.greenbuildingadvisor.com/blogs/dept/musings/getting-insulation-out-your-walls-and-ceilings
As with any construction method, it's important to get the details right, and to include strategies to manage bulk water intrusion. It's important that foam-sheathed walls NOT include an interior polyethylene vapor retarder. If your details are done right, a foam-sheathed wall will stay dryer than a conventional wall.
Thanks Martin. Both systems, PERSIST and the REMOTE seem like good systems, especially in cold climates....but sounds like it would be fine elsewhere as well. Seems important to stress the need for good mechanical ventilation to provide fresh air and help to deal with indoor humidity. Also seems that this method would be good for the PassiveHaus standard as well, especially in retrofit situations.
Not sure I understand the risk related to using additional insulation in the stud cavities. I heard Straube say that he would use cellulose in the cavities in almost any climate for added R value.
Conrad,
Condensation occurs on cold surfaces. If all of the insulation is exterior to the wall sheathing, as it is in a PERSIST home, the sheathing will stay warm. If it's warm, condensation won't form on it.
If you pack the studs with insulation, you've isolated the wall sheathing from the warm interior, making the sheathing cold. If any warm, humid air contacts cold wall sheathing, condensation is possible.
That's what it's always best to put all of the insulation on the exterior side of the sheathing. Most people don't build this way, however, because they want a cheaper house. So we've devised ways to build with insulation-packed wall cavities. It's possible — just a little more risky than exterior insulation.
Yes, in standard framing, I think I understand the condensation risk, especially in cold climates. Warm air infiltrating through insulation, contacting the cold exterior sheathing and condensing.
But, my question was within the PERSIST wall system, why is it risky to place more insulation in the stud cavities? The exterior sheathing is already kept warm, reducing the chance of any condensation, I think. Are you saying that additional insulation in the cavities isolates the exterior sheathing, increasing the chance of condensation? Maybe I am missing something.
Martin,
Conrad was asking about adding exterior foam board to increase the wall R-value and create a thermal break. He was not addressing the REMOTE or PERSIST systems, which are very different beasts than the conventional exterior foam supplement.
Lstiburek was responding to your question about the PERSIST system. In his "Designs that Work" series, he does not include exterior foam in climate zones other than the ones I listed above. Your article also credited Chris Makepeace with the same assesment, but I wouldn't give much credence to an "expert" who doesn't seem to understand how a blower door test works. If your quote is correct, he seems to think that a tight house cannot be depressurized to 50 Pa, whereas a tight house is the easiest to pressure down - a loose house cannot be depressurized.
The one point on this with which I would agree is " it's important to get the details right", and it's important that the details stay right for the life of the house. It makes much more sense to build an envelope which is forgiving enough to handle the inevitable leakage or occasional condensation that will occur at some point (or many) in the life of a building. It is for that reason that Straube recommends cellulose, as it is extremely resilient and forgiving of occasional moisture, and helps buffer indoor relative humidity (as do most natural materials).
Unfortunately, the current trend in so-called "green" building is exactly the opposite. It is a logical extension of a blind faith in technology to solve the problems that earlier technology created, and is based on an assumption of perfection and infallability. Nature doesn't work that way - it creates sustainability through an innate ability to respond to known and unknown threats through flexibility and accomodation. If we were wise, we'd build our homes with the same resilience.
Conrad,
You guessed correctly: adding insulation in the stud bays cools the wall sheathing by separating the sheathing from the warm interior. There will be a temperature gradient through the insulation layers; the more insulation on the interior side of the sheathing, the colder the sheathing.
Robert,
What then is the "conventional exterior foam application".....I see lots of pictures of builders applying exterior foam in places like Texas, etc. How is it different from PERSIST/REMOTE? Do they put an impermeable membrane between the foam and the sheathing?
Also, I agree with you...tight houses are very easy to depressurize to 50 pascals. Not sure where Chris Makepeace was coming from on that one.
Robert,
Plenty of southern builders use exterior foam sheathing; in fact it is the preferred way to insulate concrete block homes in Florida.
Can anyone comment on this assembly? Cold climate (Zone 6) low budget house. It's currently framed 24" OVE and sheathed and I would like to continue assembly as follows from in to out - 5/8" drywall (airtight), dense-pack cellulose (2x6), 1/2" OSB, Tyvek, 5/8" foil-faced polyiso (foil-out), Delta dry (3/8" thick ventilation mat (vent's both sides) gapped wood siding. The rigid doesn't get me below dew-point at sheathing for all temps, but a little helps right? window flashing is back at tyvek. tyvek is taped rigid is not. the thought is that the air gap from delta dry helps make foil polyiso more effective (radiant w/ airspace) and allows siding to breathe. Interior will not have specific vapor barrier at this point. This seems to be vapor barrier on wrong side of assembly but I'm not planning on putting one in if i go w/o foam, relying on airtight drywall and dry climate to cover me. other option is 1/2" XPS but i had the thought that foil-faced polyiso would maximize air gap i am already creating? Thanks for any input.
I'd say you're asking for trouble. In IRC climate zone 6 (I assume you're out west in B-dry zone?), 2" of exterior foam is typically necessary to keep the sheathing above the dew point most of the heating season.
You're using relatively impermeable and relatively vulnerable OSB for sheathing and then covering it in an impermeable foil-faced foam board with a relatively impermeable rainscreen membrane (perm=0.385). Even with the air-tight drywall system and good indoor humidity control, you're almost certainly going to get some condensation on the sheathing, accumulating during the heating season and with insufficient drying potential during the summer due to air gap and radiant barrier.
The radiant airspace between the foam board and the vented rainscreen adds nothing to the thermal envelope, since that's vented space. If you want to use the outsulation technique, I would recommend 2" of EPS if that's available, or XPS if it's not (EPS allows more drying potential to the outside). In any case, do not use interior vapor barrier.
You can also increase the R-value of the walls and reduce thermal bridging by using a cross-hatched framing system, with 2x2s perpendicular to the studs. Those can be placed 16" oc and 1/2" drywall used (I've commonly installed 1/2" drywall on 24" oc framing with dense-pack and no bulging or screw-popping).
Conrad,
The REMOTE/PERSIST systems are just that: building systems, requiring very careful integration and detailing of the weather barriers, air barriers, and thermal barriers. They typically use bituthane self-adhering membranes over the sheathing as an air barrier, integrated with ceiling air barrier. And they use very thick exterior foam layers, often as the only thermal barrier.
In "conventional" construction, builders often simply add exterior foam board for additional R-value, for thermal break, and for weather barrier and/or air barrier. But simply adding another layer of material, without integrating it into a whole-house system, including indoor humidity control, vapor diffusion control, and drying pathways is the kind of piece-meal approach that can create more problems than it solves.
Thanks RR,
I do like the idea of simplifying and internal strapping may prove easier with my timing. I am in Idaho @ 6000' and framing now. I really like the use of cellulose as insulation, it;s fairly benign compared to foams. I'd like to hear your thoughts on the roof. I have a trussed cathedral ceiling, 20" parallel chord heels that turn horizontal (think collar tie), ridge to collar tie depth is 5'. (2/3 of single gable roof is parallel chord depth only) Would you recommend 4" urethane and remainder of cavity blown full with cellulose and unventilated (R-72 to R-120+) - or 2" baffled ventilation gap, 18" of cellulose throughout (R-54) and a small ventilated attic? I could strap or put rigid at ceiling also to boost R. I 've heard that majority of heat loss is out roof and also that my elevation and cold climate (county borders Zone 7) is best served by R-72 min at roof. Thanks again. By the way, other parts are R-20 radiant SOG and DHW via electric boiler with 2-coil tank supplemented by boiler and evac tube. Woodstove, good solar gain. 30% unlimited tax credit on solar right now, wow. Your help is appreciated.
Heat moves equally in all directions. Only warm fluids (liquid or gas) move upward. So there is no more heat loss through the roof than through any other part of the thermal envelope unless you have a leaky house with consequent air temperature stratification. There can be more summer heat gain through the roof, however, because of the more direct angle of incidence.
For that reason, and to avoid ice dams and allow evaporative drying and drainage of possible roof leaks, I recommend vented roof systems. Given the depth of roof trusses, it would be reasonable to install continuous, sturdy vent baffles, continuous soffit and ridge vents (the only venting system that works, which requires wind-baffled ridge vents such as Lomanco OR4 or Air Vent Shingle Vent II), and dense-pack cellulose. You can also sheath the trusses with 3/8" CDX, cover that with housewrap, install 2x2 sleepers on top of each truss and then sheathing and roofing to create a weathertight, self-draining vent cavity and allow a full 20" of insulation.
18" of cellulose should give you an R-68 roof (R-3.8/in), but that would be excessive without bringing the walls up to at least R-40 which would require a double-wall framing system, either staggered studs or Skekatchewan or modified Larsen Truss (which is my system: http://www.builditsolar.com/Projects/SolarHomes/LarsenTruss/LarsenTruss.htm)
You can use the flash & fill system, but I prefer cellulose to any foam product and I keep my exterior skin at least 5x as vapor permeable as the interior, which means avoiding OSB and plywood (fiberboard or sawn lumber is good).
Here's a related question from a new reader. I've got a client who needs to re-side and would like to upgrade the insulation. 6B climate zone, 7961 HDD, 1166 CDD, 12 ' precip/yr. Typical mid 80's construction, 1/2" GWB, VB (currently being verified, but probable) 2x6 R-19 fiberglass, cdx, paper (felt?) and siding. The client was assuming EFIS which suits the house style.
Question: Would a cement based finish such as TESS (www.tessfinishes.com) with a perm rating of 72 over 2-3" of XPS (perm 1.1/inch) (they also specifiy Tyvec stucco wrap) over the existing sheathing safely allow moisture to migrate outward?
thanks, Jim Baerg
Can anyone advise on proper insulation of exterior walls and roofs in Gulf Coast wet and always humid climate. Moisture tends to drive inward. Do ERV's work well in this type of climate?
Thanks,
HJC
Henry,
It isn't possible in a paragraph or two to explain "proper insulation of exterior walls and roofs" in your climate. Can you narrow the focus of your question?
Either an ERV or an HRV will work well in your climate, providing excellent mechanical ventilation while minimizing energy use. However, don't expect either device to significantly lower indoor humidity levels. In your climate, you'll need an air conditioning system or dehumidifier if you expect to lower indoor humidity.
Robert,
Thanks. It seems that you are saying the only 'safe' application of exterior foam on the framing means to follow the REMOTE/PERSIST methods....that is, carefully installing a weather barrier on top of the sheathing, before applying the necessary outsulation.
Applying foam insulation on the sheathing, without the weather barrier, may certainly work in certain climates....but it can be risky due to the needs of allowing the inside humidity to escape and allowing moisture to dry to the exterior by diffusion.....but it does seem that you would need something over the foam because that in now the drain screen behind the exterior cladding, especially on the vertical joints where it is difficult to seal with a z-bar type flashing...unless the existing tapes work well for sealing joints over a long period of time....just the life of the siding!
Jim,
2"-3" of XPS (perm 0.55-0.37)is an effective vapor retarder (vapor semi-impermeable) and will not allow the wall assembly to dry to the outside effectively. It's kind of silly to place a 72 perm coating (is it really that high?) over a relatively impermeable backing. Use EPS instead.
P.S. I assume you meant 12" of annual precipitation, if you're in a "B" or dry climate zone.
Conrad,
No, I'm not an advocate of the REMOTE/PERSIST systems, though they do include a more systematic approach to integrating the three necessary barriers: thermal, air, and moisture. What those systems use over the sheathing is not simply a "weather barrier", which typically means housewrap, but an air/vapor barrier. The foam board is used as the weather barrier as well as thermal barrier. And I'm not an advocate of relying on any kind of tape to last the life of the house. In fact, in water pressure tests on housewrap, the common failure points are the taped diagonal slits on the above-window flaps.
All envelopes that rely on foam or any form of plastic tend to expect that all systems will be installed perfectly and remain perfect over the life of the house. This assumption is necessary, since most of these buildings have little capacity for diffusive drying and little or no moisture storage (buffering) capacity.
What I do advocate are building envelopes that are tolerant of occasional moisture, allowing safe storage (buffering) and diffusive drying in both directions. This requires natural building materials, which are preferable for many reasons in green construction, such as wood, cellulose insulation, straw bale, cob, earthen plasters and natural paints. Such materials are not only highly moisture tolerant (breathable) but offer additional indoor air quality improvements such as negative ions.
Conrad,
For more information on determining adequate foam sheathing thickness in different climates, you might want to read "Robust Walls" by Ted Cushman.
Thanks Martin and Robert for your input.
Seems that Lstiburek recommends a housewrap under the foam, on top of structural sheathing (if it is required)....to act as a secondary drainage plain... if and when water goes past the foam, thru the joints I assume. Not sure how you would provide the secondary drainage plane, if you are able to attach the foam directly to framing without the use of plywood or OSB sheathing. Maybe you then put the housewrap on the outside of the foam.
Of course, I always recommend a drainage plane space behind the cladding....by attaching vertical furring strips for siding attachment. Perhaps then, that furring would be attached over the taped vertical seams on the foam and you could use a simple Z-bar flashing on the horizontal joints. That would be pretty tight, I think.
Anyway, all these systems need to be considered carefully within each climatic region. with great attention to details around all penetrations.........
If using the housewrap as the air barrier material for the wall system, then it must be protected from positive and negative pressure differentials and installed in such a way as to avoid deflection. For that reason, I believe, Lstiburek recommends placing it between sheathing and exterior foam board.
If there is no structural sheathing, the housewrap can be applied under the foam board if dense-pack insulation is installed in the cavities to keep the air barrier from flexing. Otherwise, it's best to apply the housewrap/air barrier outside the foam board, but only if it's sandwiched by the cladding (i.e. no rainscreen) unless the foam is used as the air barrier material.
I would not "always recommend a drainage plane space" under cladding. That's required only in high rain exposure areas. In most climate zones, back-priming the siding is sufficient for long-term durability, assuming the thermal envelope can breathe in both directions. A rainscreen complicates door and window installation and falshing integration and can leave the housewrap vulnerable to pressure deflection.
While self-adhering flashing tape and rainscreens are useful technologies, they've both become overused as panaceas for moisture problems. The KISS principle still applies.
I am finding these postings very interesting...if not a little over my head.
I am currently framing a new house for myself. OVE principles with 7/16 osb followed by tyvek , 1" stryofoam board, and then cedar siding. Am i hearing you right that condensation may be a problem?
I live in southern oregon. A semi dry climate with hot dry summers and wet winters. Should I skip the foam? I love the idea of the thermal break but spending my life savings on a future mold-pit scares the h*ll out of me! Thanks for any insite.
What's the rest of the thermal envelope? Drywall, poly vapor barrier, cavity insulation, wall thickness, rainscreen? What kind of HVAC system? Whole house ventilation? Full basement, crawl space, slab on grade? Ventilated roof/attic?
I need the whole picture to offer any useful advice.
Robert,
its drywall, fiberglass batts, 2x6, 7/16"osb, 1" styrofoam, tyvek, cedar siding. Mitsubishi minisplit ductless heat/ac. ventilation is bathfans (1 on 1st floor and 1 on 2nd )on 24 hr timers, and slot vent windows in bedrooms and one in the living room.
crawlspace. vented roof (combo of stick framed 12" i joists and trusses).
Currently in framing stage with osb installed. What do you think of the system as a whole? any changes youd recommend? Thanks, jason
J.P. Eaton,
You should be fine. A couple of points:
1. Don't include an interior polyethylene vapor retarder.
2. It sounds like you are using R-5 XPS for exterior foam. That's fine for your climate. Readers in colder climates should use thicker foam. If you can afford it, thicker foam is always better in this location than thinner foam.
3. Be sure to include rainscreen strapping between the foam and the cedar siding. Cedar siding should never be installed directly against foam.
You didn't list interior vapor barrier - that's good, since you're reducing the outward drying potential with the perm 1.1 foam board.
Assuming the crawlspace is dry, I'll go along with Martin's assessment - with the caveat that careful attention must be paid to exterior detailing and flashing integration (which becomes more problematic with a rainscreen) to prevent water leakage. Tests have demonstrated that water intrusion into foam-sheathed walls often remains long enough, in the warmer wall environment, to cause mold problems.
If you must use fiberglass, I would at least suggest using unfaced batts to avoid any interior vapor retarder. You would be much better off, however, with dense-pack cellulose in the stud cavities. Not only is it a completely non-toxic, low embodied energy, fire resistant and largely recycled product, but it also manages potential water intrusion far better than glass fibers by pulling it away from wood framing and sheathing and allowing slow release. Use cellulose treated only with borates (not ammonium sulfate), and your walls will also be mold-resistant.
Cedar siding should also not be placed directly over polymeric housewraps, since the surfactants in the wood can make the polyolefins more permeable to liquid water. However traditional 15# felt underlayment works fine and often works better than plastic housewraps.
I'm doing a remodel on a 1928 bungalow. At present, most walls remain the original 2 by 4 with 3/4 fir t&g or shiplap inside and out. I'm trying to retain this construction to avoid going down the major seismic retrofit route with the building department. It's odd construction with non-uniform stud spacing.
The plan at present (from the inside) is 1/2 inch or 5/8 inch drywall detailed as ADA (with vapor barrier paint only if the bldg dept makes me), 3/4 fir shiplap interior cladding, densepack cellulose in the wall cavity, 3/4 fir t&g fir exterior cladding, 15 lb felt, 1 inch XPS, 1/2 PT ply furring/air space, fiber cement lap siding. ( Most manufacturers seem to suggest not back priming fiber cement) For what it's worth, the fir cladding is nothing like air tight.
I'm trying to make the felt serve as an innermost WRB with details to route water out to the exterior of the foam sheathing. I've constructed a model of the extant wall to work out the details of the design. The foam (1 inch Foamular t&g) will be taped (vertical) and Z-flashed (horizontal) and treated as a second WRB with window//door details flashed at that layer. I'm essentially trying to adapt the Lstiburek Wall Section 1 design from his Guide to Insulating Sheathing.
The house is located in Portland, OR. It is about 550 sq ft with a basement (it is relatively dry and I'm using large overhangs and somewhat improved drainage at the top of the vintage concrete) and will incorporate a Panasonic ERV, an LG Art Cool mini-split heat pump with direct vent, natural gas wall heat for backup. It will have soffit/ridge ventilated comp roof with about 18 inches of cellulose. I'm pretty sure I understand the issue with the ratio of inter cavity insulation to exterior foam and that it means paying careful attention to the interior air barrier and humidity levels. My thinking is that the storage capacity of the cellulose and felt might also assist in prevent the exterior fir cladding or inner foam surface from becoming the first condensing surface.
I realize that retaining the present dual clad construction presents additional challenges but the option gets close to completely rebuilding the structure. Even now, some of the wall sections will have to be rebuilt as shear panels with plywood sheathing on the exterior to meet seismic requirements.
A related question has to do with the detail at the top of the rainscreen. I would have a trim detail at the top of the wall to conceal the upper rainscreen vent but I also have the soffit vents just above that. I note that some Canadian references state that venting the wall into the roof is a bad idea so I'm wondering how to isolate the upper rainscreen vent from the soffit vents (or if the mixing of outside air with the rainscreen 'exhaust' would mitigate any issue with that air finding its way into the soffit vent. (I recently noticed an APA publication illustrating a rainscreen not vented at the top - another possibility . . . )
This may or may not sound completely crazy but no one I know is familiar with any of the particular issues involved so I'm hoping some of you can provide some feedback. My apologies for the lengthy initial post, but it seems like more detail is better on this forum.
You might want to post this in a new thread instead of at the end of someone else's lengthy one (or ask the moderator to move it).
You seem to understand the issues involved and have come up with a functional wall system that should work well in your climate while keeping the integrity of the bungalow. An inch of exterior foam should be sufficient for your "warm sheathing" approach, combined with the ADA, a vapor-open interior and hygroscopic cellulose insulation in the cavity.
It appears that the fiber-cement siding manufacturers' recommendations against back-priming are to allow the drying of process moisture from manufacture as much as to allow drying from environmental moisture. I would backprime any cellulosic siding that is not applied to a rainscreen, but leaving it unprimed with a drainage space is fine. I would recommend flashing with felt gaskets or aluminum step flashing at butt joints.
In your marine climate, it may be better to not top vent the rainscreen (which makes it a drainscreen), both to prevent extra moisture from entering your soffit vents and to prevent ground moisture from venting up behind the unsealed back of the siding.
I've heard a lot of recommendations for OSB, Tyvek, and insulated sheathing on exterior walls. My question is... Where is the drainage plane? I hope you are not relying on the Tyvek as your drainage plane, because drainage aint going to occur at that layer. Sandwiching Tyvek between OSB and rigid insulation will not allow for water to drain. Perhaps the insulated sheathing is the drainage plane... but then what is the point of the Tyvek?
Shouldn't you be using a Stucco Wrap or Drain Wrap?
very interesting reading.. we are framing 2 houses in vancouver bc wet coastal climate, and trying to decide on insulation methods as well.. have had some discussion on using a Roxul mineral fibre semi rigid board instead of SM due to the Roxul's permeability qualities.. Roxul is interested in getting some residential market for what is traditionally a commercial product.. may be a little more difficult to use as the density is quite a bit less and we would need to use 2 inch to get a R value of 8 or 8. We like the fact that it may be better at drying and perhaps it is a "greener " product but are still puzzling through it and looking for other thoughts. We are also thinking air tight drywall , have an Arxx basement, radiant heat with an eneready hrv and still finalizing a solar thermal system for domestic hot water and radiant heat assist.
Exterior remodel project for a 1960's 2-story colonial in central New England. Scope includes replacing windows and doors, siding and exterior trim, and applying a layer of exterior wall insulation and roof replacement. Wall construction is plaster/drywall, 2 x 4 frame 16" OC with fiberglass batt R11, 3/4" plank sheathing. We want to add 1" Foil-faced iso-board R7 over the sheathing, tape all seams, and install pre-finished cement board siding. All door and window openings will be flashed with bitithane.
Do we install house wrap atop the sheathing or atop the new insulation board? Is vertical strapping over the insulation board recommended, or not? Would R5 'Dow' board be preferred for the exterior insulation?
Richard,
To answer your questions:
1 "Do we install house wrap atop the sheathing or atop the new insulation board?" Either way. It's even possible to omit the housewrap and use the foil-faced polyiso as your water-resistant barrier (WRB). But regardless of which of these three option you choose, your WRB has to be carefully integrated with your window and door flashings.
2. "Is vertical strapping over the insulation board recommended, or not?" Yes, it's recommended.
3. "Would R5 'Dow' board be preferred for the exterior insulation?" No. In fact, if you are going to all that trouble, I'd advise you to use thicker polyisocyanurate, or multiple layers. Several recent deep-energy-retrofit projects in New England have used two layers of 2" polyiso over the wall sheathing, followed by vertical strapping and new siding.
Martin,
I have noticed that you have not adopted Joe's new Vocabulary.
Check out this Vocabulary Insight
http://www.buildingscience.com/documents/insights/bsi-024-vocabulary/?topic=/doctypes/building-science-insights
John,
You're right. It's always best to communicate with words that are technically accurate — but also in current use by the community with which one is communicating. Joe's proposed vocabulary shift has not yet been widely adopted.
I know .... I have barely seen it being promoted.
I heard about it through his Newsletter
I really like It .
I think it helps me to visualize
Richard,
In central New England I would not recommend foil-faced exterior insulation board, even if you used 2". That creates a wrong-side vapor barrier during the heating season and an excellent condensation plane at the inner foil face. If you used unfaced fiberglass between the studs and no interior vapor barrier, then the wall assembly could breathe to the inside for eventual drying during summer months, but in a cold climate a wall should be able to breathe to some degree outward.
Extruded polystyrene insulation board (styrofoam) at least allows some vapor permeance, whereas foil-faced insulation has zero permeance, but you should use a minimum of 2" of exterior foam to reduce the likelihood of condensation.
Richard,
You should understand that Robert Riversong is expressing a minority opinion in the building science community. If he was correct that the use of polyisocyanurate insulation on exterior sheathing would cause problems because it creates a "wrong side vapor barrier," then every single commercial flat roof in the country would be in failure mode.
As long as the foam is thick enough, it does not increase the chance of moisture problems in the wall — it greatly reduces that chance by warming the wall and making condensation impossible. The only important caveat: don't use an interior poly vapor barrier or vinyl wallpaper.
Recent examples of the technique can be found here:
https://www.greenbuildingadvisor.com/video-leed-platinum-habitat-humanity-house-westford-mass
https://www.greenbuildingadvisor.com/homes/old-house-gets-superinsulation-retrofit
See also Bruce Coldham's article, "Energy Smart Walls," in the December 2009 issue of Fine Homebuilding: "A DOUBLE LAYER OF RIGID-FOAM PANELS BLANKETS THE EXTERIOR. Conceptually, the most simple of the six systems, this technique is particularly well-suited to retrofits or for enhancing conventionally framed new construction. In an approach developed by architect Betsy
Pettit of Building Science Corporation, a double layer of 2-in. polyisocyanurate insulation is applied directly to the studs and is held in place with vertical 1x4s screwed to the framing."
True that Robert Riversong's opinion concerning vapor tightness is a minority opinion in North America.
Not so true in Europe.
Almost every modern European assembly that I have observed (by internet) seems to be vapor permeable.
Here is just one example:
http://www.natural-building.co.uk/PDF/Pavatex/090216_Technical_Manual_PASSIVHAUS.pdf
I have looked at MANY and can provide many more links
The Europeans seem to have more respect for water than "we" do.
If it were just Riversong... I might dismiss him as one of those Vermont Hippies ;-)
I am not sure that Robert is "correct" ...but what if he is....
Intersting how Europeans seem to have no problem using a wall system that provides a warm side (vapour permeable) rigid board for racking resistance and air control.
I really like the apparent simplicity and continuity of such systems.
I feel like I'm butting my head against a brick wall trying to find similar approaches to building here in NA.
John, I would love to see more examples please.
Lucas,
here is a video showing modular construction ..airtight and vapor open...
mineral wool outsulation
https://www.youtube.com/watch?v=wBQHBr7zn0M&feature=related
here is webpage... airtight ...vapor open wall
notice...no peel & stick....ventilated cladding...metal sills
http://live.pege.org/2006-building-salzburg/passive-house-wall.htm
Here is an Outsulation Retroftit
http://www.passivhaustagung.de/Passive_House_E/modernisation.htm
appears(not sure) to be vapor open graphite enhanced EPS
Notice the Mineral fiber above windows
When I was searching for Passivhaus info...I did not see any examples that used foil or vapor barriers.
John,
Walls with outsulation are also vapor open — they just dry to the interior, whereas the European walls you are describing dry to the exterior.
Both are vapor open. Just different.
I think I have gathered through these posts what is "ideal". Just want to double check. Framing in Central VT- 2x6 blown in cellulose. House ontop of ICF foundation. I am still not sure if it is better to place the 2" xps (all seams taped) inside or outside of the 1/2" plywood. Then vertical strapping (drainage plane) and then spruce clapboards.
Adam,
There is no "ideal" building system. Each approach has benefits and liabilities. The important thing is to understand the hygro-thermal dynamics so as to build on the strengths and not exacerbate the weaknesses.
If you're in Central VT and free this weekend, there's still room in my Hygro-Thermal Engineering class at Yestermorrow in Warren.http://www.yestermorrow.org/courses/detail/hygro-thermal-engineering-managing-moisture-in-the-home?StartDate=2010-02-15&SortColumn=StartDate&SortDir=ASC
With the wall system you've described, you'd want the plywood sheathing on the frame for shear resistance and to keep in on the warm side of the outsulation. If you're using the XPS also as a weather barrier (with no housewrap), then you might want to use two layers of 1" board with offset and taped seams. If you're using housewrap, that's somewhat less important, but the housewrap will be somewhat vulnerable to pressure differentials since it won't be tightly sandwiched between solid surfaces. And bulging polymeric housewrap is susceptible to condensation on the backside.
Drainscreen or not, make sure you backprime your clapboards and seal the endgrain before installing. And, if you haven't already poured your foundation and it's a full basement with conditioned space, you might consider the ThermoMass system with the foam sandwiched in the middle of the concrete where it's not vulnerable to UV, insect or physical damage and doesn't require additional coating. With ICFs, you lose most of the thermal mass benefit of the concrete. With the inverse - concrete/foam/concrete - you get almost as much dynamic mass benefit as with exterior-only insulation.
Robert, I think there was a space missing before your link try this
http://www.yestermorrow.org/courses/detail/hygro-thermal-engineering-managing-moisture-in-the-home?StartDate=2010-02-15&SortColumn=StartDate&SortDir=ASC
Thanks John. I saw that after I posted and there is STILL no edit function. I guess the webmeisters here expect all us "greenies" to be perfect ;-)
Thank you Robert, I am going to try to make it there this weekend. I was wondering if I can speak with you off this forum, as the steep tuition might inhibit me from joining this weekend. Thanks
Adam,
Most of my students at Yestermorrow feel the tuition is more than fair for what is offered, but I understand that not everyone can afford such things (I live on a subsistence income myself).
You can contact me at HouseWright at Ponds-Edge dot net.
Is there any valid concern about moisture being trapped between layers of exterior foam?
Even if the foam layers are unable to dry, would it be a problem?
CJ,
As with most questions about the complexity of hygro-thermal dynamics in a modern house, the answer has to be "it depends".
Among other variables, it depends on how deep into the multiple foam layers. The trapped water is most likely to be near the exterior where it was driven by rain and wind. In that case, it could freeze in very cold weather and cause frost damage to the rigid foam board or create a cavity behind it. Such damage, as is not uncommonly the case, could then make the layers more vulnerable to further water intrusion and start a self-stoking (or "vicious") cycle.
What about using one layer of 1-7/8" rigid with Insulated Vinyl siding attached directly to it?
Anonymous,
The answer to your question depends on your climate. Most so-called insulated vinyl siding has an R-value of R-2 or R-3. A layer of 1 7/8-in.-thick rigid foam has an R-value ranging from R-7 (for EPS) to R-12 (for polyiso). The total of these two products would have an R-value between R-7 and R-15.
If you are in Climate Zone 6, your foam sheathing must have a minimum R-value of R-7.5 for a 2x4 wall, of R-11.25 for a 2x6 wall.
If you are in Climate Zone 7 or 8, your foam sheathing must have a minimum R-value of R-10 for a 2x4 wall, or R-15 for a 2x6 wall.
I have a low-slope roof that due to variety of reasons (insulation one of them) we are increasing the pitch (from 2/12 to 6/12). We are leaving existing roof decking (at 2/12), attaching 2 layers of polyiso (staggered, taped) and will have a vented roof (cavity is insualted between the old and the new roofs). Any recommendation / feedback on this plan would be highly appreciated. This is in Midwest. Thanks in advance.
Alex,
It's hard to judge whether your plan makes any sense unless you tell us:
1. Whether there is any existing insulation under the existing roof sheathing.
2. What the total planned thickness of the new polyiso will be.
3. What your climate zone is. (Are you in Missouri? Minnesota?)
Alex,
Assuming you'll have intake vents at the low end of the roof slope (soffit?), make sure that the polyiso can drain out those vents, since it will serve as a secondary drainage plane in the event of a leak in the new roof (all roofs eventually leak).
Thank you, both, for your input. To provide more details, there is no existing insulation under existing roof sheathing. I will have 3" to 5" of ISO (5 in most places, 3 closer to the wall plates, as there is no room for more). And this is Chicago. I understand that it will most likely not meet the codes (R-value-wise) but I am trying my best within limitations of 45 year old house.
Alex,
Chicago is in Climate Zone 5; most codes require a minimum of R-38 in zone 5. Depending on the R-value you ascribe to your polyiso, you will need 5 1/2 or 6 inches of polyiso, minimum, to meet code.
Although you explain that you are "trying your best," I'm not sure what that means. I doubt that there are any physical limitations that prevent you from beefing up your roof insulation from 3 inches to 6 inches (although there may be).
Perhaps you can't afford the minimum code level of insulation. All I can advise is that you should do your best to scrape up the money -- perhaps you can get a bank loan? -- because this is a rare chance to get it right.
You'll be suffering the effects of thin insulation for decades if you get this wrong.
Martin, the limitation is not as much financial as the design one (limited space between old roof decking and new one at wall plane to include 6" of insulation AND allow 2" for venting). Also, to be taken into account that my siding (that is not part of this project) - is very poorly (if at all) insulated. So, to have R40 at the roof yet R2 (drywall and cedar siding) does not make much sense either.
Alex,
Bringing a building assembly up to current energy code standards ALWAYS makes sense. Phase 2 can be to bring the sidewalls up to snuff. But if you bring the roof only half way there, then it will be "sensible" to do phase 2 half-fast as well and you will end up with a relatively poorly-performing building as the price of heating fuels escalates.
I just bought a 1960's ranch with 2x4 walls, some kind of shiny metal looking paper material, then sheetrock and plaster walls. I want to add foam board insulation to the outside then vinyl siding. I need 2 questions answered - 1. will this metal material be an unwanted vapor barrier and cause problems when I add foam board insulation ( I was thinking of adding Thermax instead of styrofoam 2" thick)? 2. I will be replacing the windows - since I am adding 2" of foam board do I get windows sized for 2 x 6 construction or 2 x 4 construction?
Thanks!
Susan,
First question: where are you?
If the " shiny metal looking paper material" behind the drywall is builder's foil (kraft paper-backed foil), then you definitely don't want an exterior vapor barrier which will create a vapor trap in the wall assembly.
In any case, exterior XPS will at least breathe to some degree (EPS is more vapor open), while foil-faced Thermax will not breathe at all.
You can either install windows with jambs sized for 2x6 construction (assuming your total wall assembly measures 6-9/16" thick) or the 2x4 jambs with site-applied jamb extensions.
I am in Massachusetts. Did they make builder's foil in 1960? I am now considering taking the old sheetrock/plaster off and adding fiberglass insulation to the walls. (R15) since there is absolutely none there right now.
Builder's foil has been around a long time. If you remove the interior vapor barrier, then you have more options for exterior insulation. In climate zone 5, with R-15 in the walls, you could get by with 1" of polyiso on the outside to meet code standards and reduce sheathing condensation potential.
Make sure you air seal all penetrations, corners, and ceilings on the inside and use exhaust fans to control indoor relative humidity.
Should the R-15 fiberglass insulation be unfaced (no vapor barrier) if I plan on putting polyiso on the outside?
The kraft paper facing has a perm of about 1 and won't significantly limit inward drying. But unfaced fiberglass is wider (friction fit) and much easier to fit tightly into each space. Most paper-faced batts are very poorly installed, significantly reducing their effective R-value.
If I have to use fiberglass (the worst insulation on the market), I always use unfaced. A better, though more expensive alternative, is recycled blue jean batts. They contain, like cellulose, borates for fire resistance which also kills all common household insects and inhibits rodents (which always invade fiberglass). They are much more dense than fiberglass batts, thus reducing sound transmission far better, and they are hygrosopic (able to absorb and release moisture) which helps buffer humidity and protect the framing from moisture damage.
Please assist. My question concerns a 1962 ranch with central air conditioning, a full basement, 2x4 walls, kraft-faced fiberglass batts in the walls, 18" cellulose in the walk-up attic.
Installing triple-pane windows. Information wanted on the best way to layer 1" Foamular, Tyvek and Hardie-Plank. Is it worth adding 1" Foamular before siding?
Bob,
The answer depends on your climate. Where are you located?
The colder the climate, the thicker your exterior foam needs to be to avoid problems with condensation in your wall cavities.
Is putting 2 layers of 3" foil-backed ISO (staggered, seams taped) into vented attic (size limitations) creates a problem (midwest) ?
Should I condiser puncturing little holes in ISO (to eliminate / open a little vapor barrier ?
Thanks in advance.
Alex L.,
1. What is ISO? Is it a brand of foil-faced polyisocyanurate insulation?
2. You say you are putting this insulation "into a vented attic," but you don't say where. On the floor? Between the rafters with venting between the insulation and the roof sheathing? Between the rafters and tight to the sheathing? Under the rafters? Somewhere else entirely?
3. Why choose a foil-faced product if you intend to poke holes in the foil facing?
Sorry for not being clear. To your questions:
1. It is just a regular foil-faced polyiso (Thermax).
2. It is going on the floor of the attic with sufficient venting above it.
3. I got a reallly good deal on "insulation factory seconds" Foil-faced polyiso, and they did not carry fiber-faced one.
Thanks again for your help.
Alex, where are you putting the foam?
best place would be under your exterior... siding... shingles etc. Next best place would be under your drywall... if you protect it with very good barrier under your slab.
There are many details involved... read read read... here... building science... and more.
Lindell Cedar homes details foam that thick between 2x6s to allow for a vent channel... plywood etc then shingles, They spec the tar felt surfaced iso.
Alex L.,
1. No, it won't cause a problem.
2. No, don't poke holes in the foil.
3. You might want to increase the R-value by blowing cellulose on top, depending where you live -- especially if you put the polyisocyanurate between the joists. There will be lots of thermal bridging through the joists.
It is not an "usual" attic. It is a decking of existing low-slope (2/12) roof (mostly over cathedral ceilings). We are framing a new roof (6/12) over existing (new rafters attached on top of exitsing rafters). Polyiso will go on top of the old roof decking (plywood). There are 2 ft overhangs. Thermal bridging should be limited (only where new rafters sit on top of old rafters and at posts supporting new ridge.
I am renovating a historic barn in coastal New England, currently uninsulated, in which the interior surfaces of the wood sheathing must remain exposed. In other words: NO insulation between studs (and no interior finish). I therefore need to use only exterior rigid insulation on the roof and walls, with wood shakes as cladding. I had planned to do the following (from inside out): existing wood sheathing - Tyvek - 2-3" rigid insulation (preferably lapped) - 1x3 furring strips - building paper - cedar shakes (or shingles). My questions:
1) Do I need an additional airspace behind the rigid insulation?
2) Do I need an additional membrane?
3) Should we be looking at something other than XPS? Would a foil faced panel change anything?
4) Any cost effective way to get this up above roughly R-16?
4) Am I on the right track?
Many thanks from all you erudite contributors to this very interesting thread.
Simon,
Q. "Do I need an additional airspace behind the rigid insulation?"
A. No.
Q. "Do I need an additional membrane?"
A. No.
Q. "Should we be looking at something other than XPS?"
A. Probably. Many builders prefer EPS or polyiso because of their lower global warming potential.
Q. "Would a foil faced panel change anything?"
A. Yes -- lower global warming potential compared to XPS.
Q. "Any cost effective way to get this up above roughly R-16?"
A. Check with your local building codes. Your R-values need to be far higher to meet code minimum standards, so your foam is likely to be much thicker than you are currently planning, especially for your roof.
Q. "Am I on the right track?"
A. Yes, except for your very low R-values.
Simon,
It's typically the exterior facade of historic buildings which needs to be preserved. But if you can do anything you want to the exterior, I would suggest adding Larsen trusses to create an exterior insulation cavity filled with dense-pack cellulose. You'll need 6" of thickness to get the required R-20, then skip or solid wood sheathing, WRB (felt is best with cedar shingles), and cladding. You may have to extend the roof eaves, but if you're also going to insulate on the exterior of the roof you can install Larsen Trusses to create both the insulation cavity and the extended eaves (10" minimum depth for R-38).
Martin and Robert, many thanks for your prompt replies. It is indeed an oddity that it is the interior which must be preserved, but as the exterior will end up shingled as before, and the interior is on the national register, we felt this was the way to go. We have some latitude on our final R-values (the town is eager to see the building preserved, and flexible to make it happen), but the numbers you suggest (20 and 38) are certainly better targets, and I will use them. The Larsen truss system is very cool, though I'm a little concerned at adding so much thickness to roof and walls (eaves will need be extended either way). I will draw up versions based on both suggestions, and see where we end up. Thank you again.
Hi, I just signed up today looking for info on this very subject, I'm in the framing stages (2x6 24 O.C.) of of an addition to my coastal Maine house. I was planning to dense pack the walls with cellulose, sheath the walls with 1/2" OSB and use 1" of rigid foam on the exterior and a typar vapor barrier over the foam, but now I'm not too sure about my plans.
Do I actually need 2" of foam to prevent condensation from forming on the inside of the sheathing of the stud cavity or will the cellulose help to prevent that? If I need 2" of foam, how do I incorporate shear resistance into such a thick foam layer. I was planning to just use vinyl siding, can I just nail it on the sheathing through the foam? Would I be safer just to put the foam and vapor barrier on the inside? I had hoped to just read up on the subject, and make an informed decision on my own, but now I'm pretty confused. I'm just looking for a simple solution so I can move forward and be confident I am doing it right the first time. Thanks -Chris
Chris Steiner,
Q. "Do I actually need 2 inches of foam to prevent condensation from forming on the inside of the sheathing of the stud cavity or will the cellulose help to prevent that?"
A. In your climate zone, foam sheathing on a house with 2x6 walls needs to have a minimum R-value of R-11.25 (at least 2 1/2 inches of XPS or 2 inches of polyiso). For more information on this issue, see Calculating the Minimum Thickness of Rigid Foam Sheathing.
Q. "If I need 2 inches of foam, how do I incorporate shear resistance into such a thick foam layer?"
A. If properly nailed, the OBS that you plan to install under the foam will provide bracing and shear resistance.
Q. "I was planning to just use vinyl siding. Can I just nail it on the sheathing through the foam?"
A. Maybe, but I don't recommend that method. You will be better off if you first screw vertical 1x4 furring strips through the foam into the studs.
Q. "Would I be safer just to put the foam and vapor barrier on the inside?"
A. No. It's better the install the rigid foam on the exterior, where it can help keep your framing and sheathing warm and dry. (Interior foam doesn't help insulate your rim joists.)
And you definitely don't want an interior vapor barrier; all you need is a vapor retarder. For more information on vapor retarders, see Vapor Retarders and Vapor Barriers and Forget Vapor Diffusion — Stop the Air Leaks!
Ok, thanks for the prompt reply, On a related topic, for my roof I'm basically planning to create a SIP. It will be an unventilated cathedral ceiling and I was planing to design it as J. Lstiburek shows in this months FHB, pg 71 option #2, except that I was planning to use 2 layers of 2" rigid foam between two layers of 5/8 OSB and the 2x10(24" O.C.) rafters will be dense packed with cellulose underneath. Given that it will be about a 6-12 pitch roof with 4" of foam between the layers is it ok to just screw and glue the sandwich together or do I need to do something more substantial to account for the shear loads? Also I was planning to ignore his comment about ventilating the roof deck in snow country since it is not really feasible given that I plan to add 2 sky lights and this roof is actually a shed roof between two gables. Do you think that's a bad idea?
Chris,
Q. "Is it OK to just screw and glue the sandwich together?"
A. Yes, but if you aren't sure about how many screws you need, it's probably worth consulting an engineer.
Q. "I was planning to ignore his comment about ventilating the roof deck in snow country since it is not really feasible given that I plan to add 2 sky lights and this roof is actually a shed roof between two gables. Do you think that's a bad idea?"
A. Even if your roof includes skylights, a ventilation channel can be beneficial. But hot roofs like the one you are designing can work well, as long as the R-value is adequate.
I'm finally at the stage where I'm ready to sheath my walls with the 2.5" of blue board but I have a question. If I install drywall on the inside and then paint it with latex paint, did I just create the dreaded double vapor barrier? Also I was planning to use insulweb to speed up the insulation process, given that my stud spacing is 24" on center how far back do I need to hold the webbing from the surface to prevent bulging beyond the plane of the studs? I asked my insulation contractor but they didn't know because they've never used the product before. Finally where can I find more info on the meticulous flashing details that are so important in this method of construction? I have five windows and one sliding door to install. I plan to install a tyvek house wrap over the foam and under the strapping. I'm assuming that this will buy me some time from uv light damage to the foam in the likely event that I don't get the addition 's siding on this year. Is this correct of should I just go with 15# felt?
Chris,
1. Latex paint is a vapor retarder, not a vapor barrier. The paint won't cause any problems.
2. For more information on InsulWeb and bulges, see How to Install Cellulose Insulation.
3. It isn't possible to explain good flashing practices in a single paragraph on a Q&A page. If you're not sure of what you are doing, hire an experienced contractor, or start studying. If you search on this website or other websites for information on "flashing windows" and "flashing wall penetrations" and "sill pans" and "WRBs," you'll get started on your educational journey.
I've been reading this thread w/great interest, but am still at a loss as to the best (or lowest risk) practice for siding replacement in North Central Vermont. There are many VERY cold days during the winter and yet plenty of driving rain and hot, HOT and humid days in the summer.
Our home was built in '86 w/sheetrock interior walls w/latext painting, 2x6 studs, 4 to 6 inches of fiberglass insulation in all walls, plywood sheathing (don't know the actual thickness), and 3/4" shiplap vertical cedar siding. The roof cap is vented the length of the house, there are vented soffets the length of the house front and back, and most of the roofing insulation is blown in cellulose over the ceiling w/open space to the rafters. There is one section of cathedral ceiling w/no attic space for venting - I am not sure if it has any airflow built into its design.
The previous owner did not maintain the exterior well at all and the siding needs to be replaced. We are redoing the roof, the siding, and the windows.
To the best of my knowledge the house has not had a problem w/moisture given the current configuration. The heating bills are low-to-reasonable given the age of the house and the depth/length of the winters. I'd like to replace or improve on the R-value provided by the cedar siding, which will be removed, while still protecting the sheathing from wind-blown and seam-leaked wather as well as excessive condensation when the siding is cold. There have been many good suggestions in this thread, but also many have been aimed at new construction instead of retrofit/refurbishments where there are existing constraints. For example, removing all the existing plywood sheathing, or gutting most of the insulation in the walls, are not practical options for me.
Suggestions, examples, guidance or links would be appreciated!
Thanks in advance,
Matt
Matt,
Your best bet is to install a layer of rigid foam between your existing sheathing and your new siding. If you are feeling experimental, you could use high-density mineral wool panels instead of rigid foam.
If this is a new idea to you, I suggest you read the following articles:
Roofing and Siding Jobs Are Energy-Retrofit Opportunities
How to Install Rigid Foam Sheathing
Calculating the Minimum Thickness of Rigid Foam Sheathing
Installing Mineral Wool Insulation Over Exterior Wall Sheathing
We are renovating a home in Northern New Jersey, which appears to be in Climate Zone 5, but close to Climate Zone 6. We are currently contemplating the following wall assembly, but would love to hear any thoughts or comments before we finalize the plans:
1) 2x6 with R-19 unfaced batt insulation
2) 1/2" plywood
3) GreenGuard Raindrop house wrap
4) 2" XPS
5) Vinyl Shake Siding Nailed through foam to the studs
The main concern is ensuring that condensation will not occur on the inside of the wall cavity, but would appreciate any guidance or thoughts that anyone has to offer.
Thanks!
Orrin,
Two comments:
1. Polyisocyanurate is more environmentally friendly than XPS.
2. Check with the siding manufacturer to be sure that the company allows fastening through 2 inches of foam.
Martin,
Thanks for the response. Other than cost is there any downside to using Polyisocyanurate. One concern that i had was than its r-value would fall below the r-value of the XPS over the long term.
The siding manufacturer does not recommend installing over more than one-inch of foam, but if you are nailing through the foam into the studs and penetrating the studs by 1.5 inches, then what would the downside be other than having to use the longer nails?
Would there be any concerns about dew point related issues based on the amount of foam and the climate? Would the thoughts on dew point change if the insulation was increased from R-19 to R-21?
Thanks,
Orrin
Orrin,
The lowest reasonable assumption for the R-value of polyisocyanurate older than 15 years that I have read is R-5.6 per inch. Between the time that the polyiso is manufactured and the time it is 15 years old, its R-value will be considerably higher.
Even at R-5.6 per inch, polyiso outperforms XPS.
Your wrote, "The siding manufacturer does not recommend installing over more than one-inch of foam." Well, there's your answer, then. All building codes require materials to be installed according to manufacturers' recommendations.
It's always possible to violate manufacturers' recommendations and violate the building code (as long as you don't get caught, or as long as you live somewhere where building codes aren't enforced). But you won't have a siding warranty, and you'll be performing an experiment.
In climate zone 6, 2x6 walls with exterior rigid foam must have foam with a minimum R-value of R-11.25. If you determine that you are in climate zone 5, the minimum R-value of the foam drops to R-7.5. For more information on exterior foam thickness, see Calculating the Minimum Thickness of Rigid Foam Sheathing.
Hi Martin,
What then would the R-value of old polyiso in cold weather be?
I have an odd thickness of old polyiso at 2-3/4" installed on the exterior of my 2x6 wall assembly. I calculated my continuous insulation thickness using an R-value of 4.5 per inch because I live in a cold climate: Columbus, OH— climate zone 6a. (I got that 4.5 R-value per inch from some numbers I found in your article, Calculating the Minimum Thickness of Rigid Foam Sheathing https://preview.tinyurl.com/y3ke6dby. I just averaged the "...R-4 or R-5 per inch".)
So I came up with R-12.38 for my c.i. (2.75"x R4.5/"= R12.38) which put me safely over the R-11.25 minimum necessary for where I'm at in climate zone 6.
So I thought I was good, because I took into account polyiso's poor cold weather performance. But what I didn't take into account was the fact that the polyiso I used is old— salvaged from a commercial roof. I didn't calculate for "thermal drift." So is the above R-5.6/inch value assumed at a mean temperature of 75°F or assumed at temperatures below 50°F, where "...polyiso performs worse..."? https://tinyurl.com/y6dabfol
I guess another way I could ask my question is: will 2-3/4" polyisocyanurate boards that are over 15 years old perform adequately in climate zone 6 in a 2x6 wall assembly? Or do I need to start removing it because in the long run it will cause moisture issues in my walls?
Thanks very much!