How do you assess flash-and-batt installations?

We have begun to see more Builders and Insulators use flash and batt installation and I am not sure how to assess the R-value of the installation and if the installation actually meets the intent of code and programs. Let me make the case… First premise it that RESNET grade one installation is equivalent to meeting the intent of the code as the code only say that insulation must be installed in accordance with manufacture instructions.
I can assess the R-value of blown foam in a 2×6 cavity so 2” would be the equivalent of R-13 if the foam is 6.5 per inch. If an R-19 6” batt is installed perfectly in the remainder of the cavity (no gaps, voids, but some compression) I know that its R-value is diminished due to the compression of the batt. There is no codified or other method that I am aware of to assess the R-value of an R-19 6” batt that has been compressed to fit into a 3.5” space. The 2009 IECC in footnote “A” of the insulation table tells me that I lose 1 R-value for a half inch compression so in a 2×6 5.5” cavity I get an R-18 but it does not line out how to reduce R-value beyond that, just that R-value is lost. RESNET helps by allowing me to assess the batt as a grade 3 for modeling the performance of the batt in the cavity, due to compression, but there is not a direct link to code which says I would need to fail the installation.
So the question is… If I have a 2×6 5.5” cavity with 2” of closed cell foam and a 6” R-19 batt what is the R-value of the cavity and does it meet the intent of code. As a Rater I believe that it would be correct to evaluate is for the purposes of generating a HERS Index as 2” of closed cell foam and an R-19 grade 3 installation. In my neck of the woods most code officials are requiring Grade one as this level of installation is deemed to be equivalent to manufacture installation.
What do you think?
GBA Detail Library
A collection of one thousand construction details organized by climate and house part
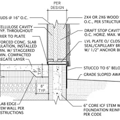
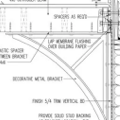
Replies
Robby,
Below is a chart the shows the effect of fiberglass compression. While the chart doesn't cover every possible case of compression, it gives you guidelines that allow you to extrapolate.
Don't overthink this. At best, you'll get a close estimate of the center-of-cavity R-value. Actual R-value depends on the depth of the spray foam (which isn't uniform and can only be estimated) and the quality of the installation of the air-permeable insulation -- and, of course, the effect of thermal bridging through the studs.
As I said, it's an estimate, so don't overthink it.
.
An R19 batt is the same weight per square foot as an R13 batt, and performs at R13 when compressed to 3.5". If after the 2" foam you have a 3.5" cavity you get the same benefit from installing R13s, provided there are no thin spots in the foam to create voids.
With a 1" flash & batt and a compressed R19 you'll have to interpolate- at 4.5" it's somewhere between R13 and R18, but somewhat closer to the R13 end, so call it R15.
Since it's all being thermally bridged by the framing, the net effect on the U-factor of the wall is pretty small. A 2" flash & batt with R6.5/inch foam with R13 fiber gives it an R26 center cavity value, but the whole-wall value after factoring in the thermal bridging is only about R1 ahead of 2x6 / R20 walls.
Thank you for your responses! I think the issue is that we would like to see flash and blow vs. flash and batt. The batt is an issue if we are really working with true verification and code compliance. Nothing has been quantified to be able to assess R-Value, so does it really meet the intent of Code and or EnergyStar for example??
Robby,
Q. "Nothing has been quantified to be able to assess R-Value, so does it really meet the intent of Code and or EnergyStar for example?"
A. Just because this type of R-value calculation isn't precise, doesn't mean that "nothing has been quantified." Use R-6 or R-6.5 for closed-cell spray foam, and R-3.7 for the air-permeable insulation. Close enough -- and stop worrying.
I think Martin's R-3.7/in approximation is good enough given all the other factors such as thermal bridging and uneven foam thickness that Dana discusses. The actual R/in on that table varies from about 3 to about 4.4, so its R3.7 +/- 0.7 per inch. For most purposes, that's all you need. But if you want a better approximation, read on:
For the most part higher density after compression leads to higher R-value per inch, but in some cases the density can get high enough that it starts to get worse again. You can see that in the R22 vs. R21 batts compressed in a 2x4 cavity--the R22 is actually slightly worse than the R21. You've gone beyond the optimum density at that point. ASHRAE fundamentals has a nice graph vs. density that shows that, but it's not much help in real applications because you don't know the density per se. So I came up with a curve fit equation hat you can use to get very close to the values on the table, but also get values for other thicknesses that aren't listed. I'd type it in, but Martin and Dana have argued convincingly that it's not really needed ... and I'm not sure it will meet your objectives anyway: My formula isn't sanctioned by the manufacturer or any standards organization. Let me know if you want to see it.