Image Credit: Lyndon Than
Image Credit: Lyndon Than Basement insulation consists of two layers of mineral wool batts. Insulation is held above the concrete slab by pressure-treated lattice and pressure-treated wood blocks, along with a layer of landscape fabric.
Editor’s Note: Lyndon Than is a professional engineer and Certified Passive House Consultant who took a year off from work to design and build a home with his wife Phi in North York, a district of Toronto, Ontario. A list of Lyndon’s previous blogs at GBA appears below. For more, you can follow his blog, Passive House Toronto.
A basic decision early in the design of a superinsulated building is the strategic choice of interior and exterior insulation placement and thermal mass. This a strategic decision because it has far-reaching implications and ripple effects.
Think of the building as a shell on all sides, including the parts in the ground. If we are designing an airtight envelope without thermal bridging, then we want to avoid having some of the insulation inside, and some on the outside. It can be done, but this frequently leads to thermal bridges and air-sealing problems.
For example, if we have insulation under the footings (outside the structure of the shell), but then we want to have insulation inside the basement walls, how do we to connect the insulation under the footings to the insulation inside the basement? Making this more difficult, insulation materials are generally weak and soft, while structural materials are hard and conduct heat.
To simplify the design and construction greatly, and improve the effectiveness of the insulation system, work to have all the insulation either outside the shell, or inside the structural shell. Cross-overs are to be avoided. In our case, we decided to place all the insulation inside the shell, and forego the benefits of thermal mass. I believe thermal mass benefits are less well proven than insulation benefits, and that “thermal” mass can be achieved without “mass” (for example by the use of water — a very thermally massive material without much mass that can be moved around).
Flooring can be removed for access
Our basement floors are installed over our interior insulation (15 inches of Roxul, rated at approximately R-54), which is located just above the concrete slab. As posted earlier, the flooring is removable and is a common material — regular construction 2×12 lumber. That means we can remove and replace pieces, but we also can remove the flooring to look underneath.
The insulation consists of an R-32 batt under the 2×6 floor joists, plus R-22 batts in the spaces between the floor joists. Below the batts is landscape fabric that is held off the concrete by pressure-treated lattice and blocks. This assembly keeps the insulation away from the concrete while providing an unimpeded drainage path for any water that does get into the basement. Nothing in the assembly will retain water.
We were able to get the pressure-treated lattice super cheap — it was culled material, an entire load for $50 — and the landscape fabric was about $8 for 150 square feet.
We’re currently pretty happy with these floors, and the system feels very solid to walk on, as if the floors were resting directly on concrete. It turns out the wood has shrunk a little in the two months since we installed it, but only the pieces that were wetter. Some planks did not shrink at all.
Some astute observers have commented that the floors will allow moist interior air to go into the spaces below. What will happen to this moist air when it reaches the cold concrete some 17 inches below? Well, we have Tyvek under the floor boards in one area to prevent this bulk movement of air, but most of the floor is left without any kind of air barrier.
Since the flooring is removable, we can make a correction if this turns out to be an issue, but I have a feeling the issue is fairly minor for a couple of reasons. If we think of regular basements, many have no insulation under the concrete slabs, and they are perhaps a bit damp on muggy, hot summer days. In Toronto’s climate, this problem is short-lived. In our case, there is a floor assembly blocking the bulk movement of air to some degree, and in addition, the space beneath our floors may be warm for much of the summer due to our under-floor (sub-slab) heat storage strategy. This raises the temperature of the basement concrete slab right when the chances of hot moist air condensing on it may be highest, which should reduce that whole issue quite a bit.
Hedging our bets
However, just in case there is a problem we placed some sensors at the bottom of the floor insulation in three locations. The photo at left shows a small pump with tubing, a water level sensor, and a temperature/humidity sensor in the background.
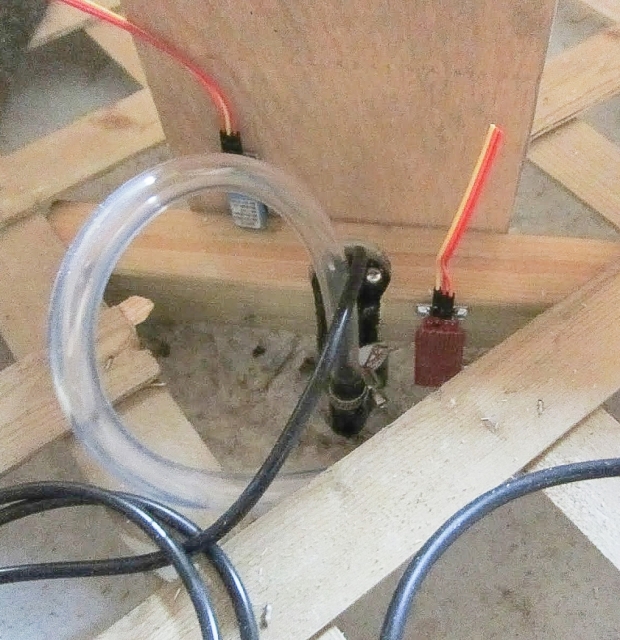
The sensors are inexpensive — about $5 each. The pump is from Princess Auto and was about $20. We had some problems with our basement floor pour. There was not enough slope in some areas, and during the big Toronto flood in July 2013, we noticed a little water in three locations on the floor. We marked these spots and placed these little pumps to transfer any water that does collect there to the sump pit.
Later, as the systems become live, we will be able to report the fluctuations in temperature and humidity at the bottom of our basement floor assemblies. We will also probably place sub-slab soil temperature sensors as well, one day…
We screwed the 2×12 pine to the joists, burying the screw heads 1/8 inch so we could sand the floor and get a somewhat finished surface later. The main reason for using this kind of floor was low cost. We were able to purchase the material at a 25% discount from regular contractor pricing, about $1.25 a square foot. Air sealing is not required at this floor. This was determined from previous airtightness test on the building, so we know we are already down to Passive House levels of airtightness.
Weekly Newsletter
Get building science and energy efficiency advice, plus special offers, in your inbox.
10 Comments
Thanks in advance for the data
I for one will be very interested to see that data on whether you get any moisture detected by the sensors. Thanks for setting that up and sharing the thinking about what might or might not be problems, and thanks in advance for sharing the data as to what actually happens.
Dew Point Calculations
Very interesting, thank you for posting. Your approach is similar to an example that was posted back in November at https://www.greenbuildingadvisor.com/articles/dept/green-building-blog/practical-approach-passive-house but without the foam. I posted what is currently the last comment on that article asking about just such an approach.
Your average annual temperature in Toronto is around 47 F. Ignoring your heat storage strategy, the assumption would be that your slab will hover around 47. Using the same calculations as in my above-referenced comment, the dew point of your indoor air should vary between something like 45 in the winter and 50 in the summer. If the slab temperature is 47 then you probably will get some condensation.
In my area the average temperature is 56, which I think means that I can insulate between the slab and floor with less concern over condensation. However I'm just doing back-of-the-envelope calculations and hope an expert might chime in to correct me if I'm missing something.
Look forward to hearing what you discover as time goes on.
Too complicated?
I don't follow the logic of not putting foam under the concrete slab and simply separating the slab from the foundation wall with more foam. What is the benefit from being able to take up a few floorboards and observe any moisture? Then what? How do you fix the problem?
Building this floor required an additional 18" or so of foundation height (to get the same headroom), plus the lattice, expensive insulation and the floor system. And then, the result is a floor made from framing lumber that will shrink and the resulting spaces will fill with the usual basement crud. How much additional cost is this over putting reclaimed foam under the slab and eliminating the condensation risk altogether?
As Gordon points out,some condensation is likely. Why risk that, especially when it could be avoided by putting the insulation under the floor?
Stephen
I agree. It would have been helpful if the logic behind the various building assemblies had been laid out a bit more, as opposed to the steps taken to deal with the problems choosing them may pose in the future.
Basements never flood or leak... and subslab Roxul
I've seen many homes on site visits with wood subfloors made with 2x3 or 2x4, either flat or standing. It seems to have been popular in the 1970's and later renovations. The clients are typically planning major renos and usually they have moisture problems with those subfloors. One house had a major plumbing leak from the well pump and it flooded a thousand square feet or so of the subfloor. The solution was to remove that soaked wood subfloor and not reinstall it. Most basement renos are done with dricore panels or a dimpled Hdpe membrane. If the clients wants a bit of insulation, then 1.5" of XPS with 2x4 sleepers on the flat, or no sleepers if it's floating laminate flooring. As they are older homes, there's not much headroom to be wasted.
Also, it's possible to install Roxul under the slab, as they did at Ecohome's Edelweiss demo house.
Logic behind the assembly
Bit slow to respond to some of these comments - my apologies.
The moisture we might expect is from flooding - not so much condensation. Thats really the reason for the removable floors. The house that sat on this location in the past had a number of floods. These were a result of what seems to be climate change. It seemed the basement was fairly dry until recent years, in which many many houses in Toronto flooded in their basements.
In my neighbours' house, the basement slab came up one year. He had no insulation under the slab at the the time - but I think there was no relief for the water - and the whole slab just cracked and lifted up in the centre. Floods happen for a variety of reasons, including sewer backups, ingress from the grade, and rising water tables. We've implemented a few flood defense features in this house, but keep in mind the following: Water is about 40% the density of concrete. If your sub-slab insulation is more than 2.5 times the thickness of your concrete slab above it, I would say there is a risk the slab will lift and buckle if groundwater levels rise to something like the slab level, due to flotation of the sub slab foam.
This gives some reason to consider insulation on top of the slab. But the major reason we took to having insulation above the slab was to keep the concrete on the outside of the building, avoiding the thermal bridges (or complex thermal details) that tend to result when there are crossovers.
There is also something I'm not really sure I understand properly. The idea of condensation on a cold concrete wall - If this happens, it means the moisture in the air contacting that wall is being removed - provided the condensate has a place to go. Well, if no new air is provided to that space, then the condensation stops after the air dries. In other words, I don't really understand the concern if there is no bulk movement of air to provide a constant supply of moisture. That means this arrangement should work fine as long as we provide an air barrier at the finish floor level or thereabouts. There is a moisture barrier under the slab. We've even placed a layer of rigid foam under the slab - i had purchased a little too much of it. With so much insulation above the slab, the insulation below should do very little to raise the slab temperature. However, the paths for moisture to enter the floor cavities would be virtually nil - other than in a flood situation.
Same with our walls. We have roxul insulation in contact with cold concrete walls - but so what? There are air barriers to prevent the bulk movement of air.
When there is a flood, however, (and I've been through a few, in finished basement space), we can remove the floor boards and ensure the concrete at the base of the floor cavity is drying out. We can also physically remove this water using pumps, etc. I imagine removing only sections of insulation where the concrete surface is lowest. Despite having a sump pit that the concrete surface slopes toward, there are still a couple of slightly low spots.
LT
BeOpt is about cost effectiveness, PassiveHouse is not (@ Jon R)
The focus of PassiveHouse is about hitting particular energy performance targets, not about the cost effectiveness of hitting those targets. If it were about cost effectiveness you'd never see the levels of slab insulation found in most PassiveHouse designs.
If flotation of the slab during high water events was a primary driver of the decision to go with slab-top rock wool, splitting the difference putting a lesser amount of foam under the slab, with the remainder of the R as rock wool above would mitigate the summertime moisture accumulation potential.
Why not eliminate the slab altogether?
If you are going to go this route, why not consider, as the builder in this JLC article (http://www.jlconline.com/how-to/foundations/a-basement-floor-without-concrete_o) does, eliminating the slab altogether and just putting your insulation, subfloor, and flooring above your crushed stone and vapor barrier?
> If your sub-slab insulation
> If your sub-slab insulation is more than 2.5 times the thickness of your concrete slab...
In such a case, I'd review BEopt results regarding the cost effectiveness of so much foam (as compared to other options achieving the same net result). Or consider not building a basement where flooding is known to occur.
Constantly humid cavities can create a mold problem - even if there isn't enough airflow to create continuing condensation. And unless you are going to depressurize it, the mold odor will escape to the interior.
Why not Eliminate the basement slab altogether
Eliminating the slab is an interesting idea. In our case, the footing were large enough and the design of them is such they could have been designed as grade beams so the slab is not needed. Most of the time, the slab is a structural member holding the basement walls against earth pressure.
Log in or create an account to post a comment.
Sign up Log in