
Each year the World Economic Forum anoints 100 early- to growth-stage startups as part of its annual roundup of Technology Pioneers. Inclusion in this prestigious club shines a much-needed spotlight on many businesses while also encouraging each selectee to further integrate their business through various means and “engage [with one another] to help scale the impact of [their] initiatives,” be it in the fields of climate science, healthcare, biotech, renewable energy, or decarbonization, to name a few key areas.
This year’s international cohort comprises an impressive list, representing 23 countries and a range of imperatives that, all things considered, demand deployment and scalability on a mass scale. Alumni companies include such household names as Airbnb, Twitter, Kickstarter, and Google, as well as climate-forward companies like EcoNation and Carbon3D. (The full 2024 list can be viewed here.)
The 2024 cohort, as one might expect, leans heavily on promoting advances in AI and smart-energy solutions. And while these areas may seem de rigueur to some, given the state of our global climate they must remain at the forefront if clean energy and green-building practices are to achieve mainstream status in the near term.
GBA reached out to a select grouping of companies on this year’s list to learn about the interrelated technologies that lie at the heart of their practices, and what specific problems they’re aiming to solve.
Scaled thermal storage
Right now, renewable energy infrastructure in the U.S. is growing faster than our grid’s ability to integrate what’s being produced. One company tackling this issue is Fourth Power, a producer of large, cost-effective thermal batteries that can store up to 100 megawatts of energy. “As the grid starts to rely on a higher percentage of renewables, you need to be able to store that energy for a longer period of time, because your resource adequacy becomes more reliant on a variable resource,” says Arvin Ganesan, CEO of the Cambridge, Massachusetts-based company.
Founded ten years ago in the labs of MIT and Georgia Tech, Fourth Power is now fully “out of the lab” and currently developing its first demo, located north of Boston, with a far smaller storage capacity of 1 megawatt but with the same dimensions and containing the same “full-sized parts and engineering” of the planned larger models. This “controlled case study” will not be tied to any grid, Ganesan says, but the company has designs on launching a slightly larger commercial pilot—up to 5 megawatts—and becoming an integrated “grid asset” by early 2026.

Fourth Power’s batteries draw electricity from the grid and use that energy to heat liquid tin to temperatures up to 2400°C. This heat is moved through graphite piping into carbon blocks, which burn bright white and can store heat for several weeks. (Naturally, the hotter you go the more energy you can store, although longer storage times do correlate with energy loss, especially if the system isn’t being constantly fed.) That heat is then converted back to electricity using thermophotovoltaic (TPV) cells.
Ganesan admits that, with this technology, the round-trip efficiency of the power being stored, converted, and delivered by a Fourth Power battery is less than that of a traditional lithium-ion battery—up to 50% less! The caveat is that Fourth Power’s thermal batteries are produced at about one-tenth the cost of traditional batteries and are designed for long-term storage. “With a variable grid, you’re going to need a lot more storage, and you cannot build that if the economics of storage remain the same,” he says.
Costs are kept to a minimum because the “supply chain is very simple to navigate in terms of material abundance,” Ganesan says. Fourth Power’s batteries are made principally from graphite, a derivative of carbon, followed by tin and TPV, comprising a supply chain that is (mostly) circular and requires no mining of raw materials. In theory, this approach also significantly brings down the cost per kilowatt hour of stored energy relative to baseline.
Full-scale deployment of these batteries is years off, to be sure, but the technology’s premise is based on a very acute need. “There’s a direct relationship with the amounts of renewables you have in a grid with how long you need to store it,” Ganesan says. “That’s why transmission needs to be paired with long-duration energy storage technologies like Fourth Power.”
Waste-to-value supply chains
Industrial waste from the cement, glass, steel, and even waste disposal sectors is a problem, both in terms of scale and the carbon it emits. One innovative measure to curb said waste has made strides in recent years in the form of low-carbon concrete solutions. Many companies operating in this space are substituting large percentages of high-emitting cement clinker (heating up limestone and clay) for supplementary cementitious materials like blast furnace slag (from steel) and fly ash (from coal). It’s a win-win; industrial byproducts find a new supply chain and less CO2 gets pumped into the atmosphere. But what happens when the byproduct is no longer useful?
Calgary, Alberta-based Carbon Upcycling has an answer for this. With a mission of “establishing a waste-to-value supply chain,” according to CEO Apoorv Sinha, the company wants to convert industrial waste in virtually all forms into sustainable feedstocks, starting with the cement industry. What sets Carbon Upcycling apart, however, is that they’re solving a problem born of a sustainable solution. The irony is palpable.
The problem in question (which isn’t really a problem at all) is that more steel producers are switching their operations from coal-based blast furnaces to electric arc furnaces, resulting is heavy decarbonization of the industry. But the byproduct from this process is not nearly as useful as its predecessor. “For every ton of steel you make, you produce between 150 and 200 kilos of slag. And that can go into cement all day long. But as you change that blast furnace to an electric arc, you make the same amount of slag, but it can no longer go into cement … it’s chemically inert,” Sinha says.
A symbiosis has been disrupted, and Carbon Upcycling’s answer is to make the benign useful. The company’s technology works by combining diverse, locally sourced industrial byproducts (as well as naturally occurring minerals) with a low- or high-purity CO2 source in a catalytic reactor, which “exfoliates the surface area of each particle.” The rougher the particles, the more surface area there is, “allowing for greater CO2 binding, improving sequestration, and product quality,” according to the company’s website.
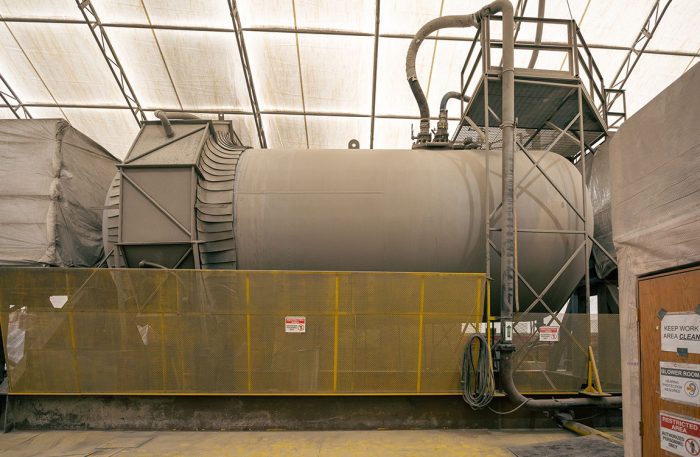
“We chemically activate these solid powders [with CO2] so that they can sequester CO,” Sinha says, ” and ultimately this new material can be a feedstock to make low-carbon cement.”
While facilitating wide-scale carbon reduction is integral to its process, Sinha frames his company more in terms of helping large industries better manage their waste streams and minimizing supply chain volatility. Financial health gets top billing, but at some point, heavy industry does need to take ownership of their own decarbonization path. “You don’t need to strand your assets to reach your carbon reduction goals by 2035, 2040 or whenever,” Sinha says. In that vein, Carbon Upcycling isn’t exactly playing in the sandbox with like-minded startups.
At present, the 40-person company is partnering with “3 of the 20 largest cement companies” in the West, Sinha says, representing building materials companies that have chosen to invest “not just in Carbon Upcycling but also in real construction projects” that are harnessing waste-to-value supply chains.
One production facility in Calgary is already in operation, with a modest 3000 tons worth of product entering the market in the last two years. Future facilities are planned for Toronto, the UK, and Belgium in the next year, with full-scale commercial production estimated at 400-800 tons per day for each plant.
Modular refining system
“Our modern industrial economy has historically focused procurement on the ‘tyranny of the lowest price,’” reads a recent op-ed in the Calgary Herald, co-written by Sinha. “On the occasions when we do include sustainability, the criteria are weak, and it is often not considered in the scoring of the bid or weighted very low against other considerations.”
One of those considerations is extraction, and the energy-intensive processes involved in refining raw materials. You don’t need to be a geologist to know the earth’s resources are finite, and even where not scarce, continually drilling and strip-mining and baking in an endless open loop is unsustainable in every sense of the word. Burlington, Massachusetts-based Nth Cycle is a metal refining company with a mission to put as much production-grade metal as possible—from industrial scrap, end-of-life batteries, low-grade ore, and refining waste—into the supply chain and keep it in circulation forever, to the nth degree, as it were.
The company’s proprietary technology, known as the Oyster, is a 2000-sq.-ft. modular refining system that replaces traditional smelting with an electro-extraction process, which “can recover critical metals needed for EVs, renewable energy, the electric grid and beyond. And it can seamlessly adjust to changes in input feedstocks and volumes,” says Nth Cycle CEO Megan O’Connor. The company claims its circular electrochemical tech contributes to a 92% reduction in CO2 emissions and up to 44% compared to existing recycling processes; consequently, Nth Cycle has garnered some high-profile investors who are keen on implementing more circularity into their own practices.
The company operates a facility in Fairfield, Ohio, in a repurposed industrial plant, where various scrap materials—sourced from partner recycling companies, miners, and manufacturers—are refined in the first operable Oyster and turned into a high-value nickel product. Eventually, each individual Oyster facility, which O’Connor says can be set up in less than 12 months, will be capable of producing up to 500 tons per year.
“It will take more than batteries, more than lithium and cobalt,” O’Connor says. “We need copper. We need dysprosium and other rare earth elements. The future we imagine depends on the full spectrum of critical metals. And using them depends on refining.”
She also points out that what her company has built isn’t a refining plant in the strictest sense, but a modular refining system that “accelerates net-zero targets by eliminating the environmental damage of smelting and the chemical waste of hydrometallurgy … without critical metals, there can be no clean-energy transition.”
_______________________________________________________________________
Justin R. Wolf is a Maine-based writer who covers green building trends and energy policy. His first book, Healing Ground, Living Values: Stanley Center for Peace and Security, was just published by Ecotone.
Weekly Newsletter
Get building science and energy efficiency advice, plus special offers, in your inbox.
0 Comments
Log in or create an account to post a comment.
Sign up Log in