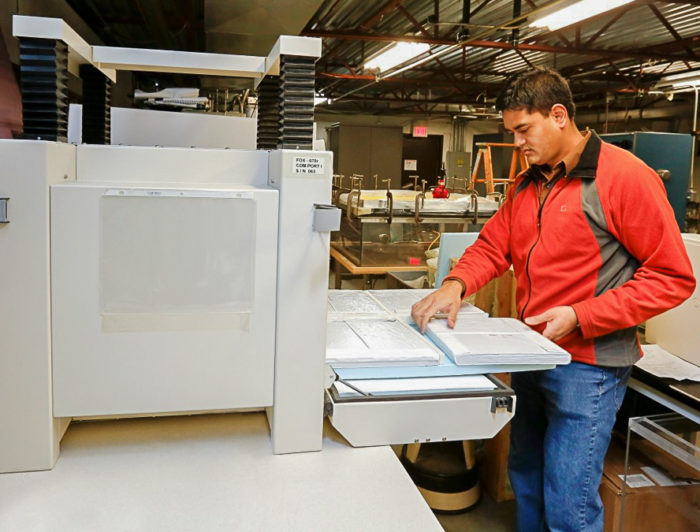
Researchers at the Oak Ridge National Laboratory have helped develop a type of building insulation that combines vacuum panel cores and rigid foam. The new composite boards have double the thermal performance per inch of insulation now on the market.
In an announcement, ORNL said that the modified atmosphere insulation (MAI) composite had resistance to heat flow “at least twice that of current building insulation materials made of plastic foams, cellulose or fiberglass.”
“We’ve proven that MAI-based composites are technically viable options for buildings, providing higher performance than current insulations,” study co-author Kaushik Biswas said in a prepared statement.
The results of their study were published in the journal Applied Energy. (A short summary of their findings can be viewed online for free, but the full article is behind a paywall.)
Vacuum insulated panels (VIPs) are an established technology, but their use is limited. VIPs are much better insulators than conventional products, but they are expensive, can’t be modified in the field, and may show a loss of performance over time as the vacuum seal gradually degrades. For those reasons, VIPs are a specialty product useful in some situations but not as a replacement for conventional types of building insulation.
The MAI composite boards were created in a semi-automatic operation and were much simpler to make than traditional vacuum insulation panels, lowering costs to within reach for some retrofit applications, according to researchers who worked on the project.
Real world testing is underway
In a telephone call, project manager André Desjarlais said Oak Ridge collaborated with two manufacturers — Firestone and NanoPore — to develop panels that combine fumed silica, barrier materials borrowed from the food industry, and polyisocyanurate foam board. Samples from a limited production run were installed in a low-slope rooftop in Caribou, Maine, over the summer (see the photos in the gallery above).
The new insulation consists of MAI panels completely encased in polyiso. The composite has at least two advantages over the vacuum panels that have been on the market for decades: they’re much cheaper to make, and they should last for 25 years without a significant decline in R-value. A 2-inch-thick MAI/polyiso panel has an R-value of about 25, or R-12+ per inch — about twice as high as polyiso foam alone. By themselves, the sealed MAI packages have an R-value of 40 per inch.
“The idea of having this encapsulated package and pulling a vacuum on it and getting a high R-value has been around for 40 years, maybe longer,” Desjarlais said. “The issue has always been one of cost.”
In its early work with NanoPore, the lab learned that 80% of the cost of vacuum panels is in manufacturing. To lower the cost, researchers started with fumed silica, a common and relatively inexpensive nano material that already has broad commercial uses (it’s used to filter swimming pool water, for example). They combined that with an outer barrier material similar to what is used in the food industry to keep products fresh.
“We’re basically taking a potato chip bag and filling it with dirt,” he said. “That’s what we’ve got.”
The lab also worked with Firestone, a major producer of polyiso panels for the commercial roofing market. The group adapted an existing foam line and found a way to insert a dozen MAI panels inside a 4×8 sheet of foam. The facing of the foam is printed to show where the panels are located, so that if the roofing contractor wants to use mechanical fasteners to install the sheets it can be done — providing the installer is careful.
In the Maine test installation, Desjarlais said, the roof was divided into thirds. In one section, installers used mechanical fasteners to put down the insulation; in another the sheets were fully adhered (no mechanical fasteners). On the last section, a double layer of polyiso was installed. So far, embedded sensors indicate that all parts of the roof are performing about the same. Desjarlais said he’d like to return to the test site with an infrared camera when it gets a little colder for a followup visit.
Costs are coming down
A major goal of the project was to find a way to make high-performance panels at an attractive cost. Loose-fill fiberglass costs between 3 and 5 cents per square foot per R, Desjarlais explained, while rigid foam insulation costs about 10 cents per square foot per R.
“We’re about in the 20-cent range, where it used to be a buck,” he said. “We’ve made a big dent in the cost.” Although the new vacuum panels are not yet competitive with conventional building insulation, “it’s getting close.”
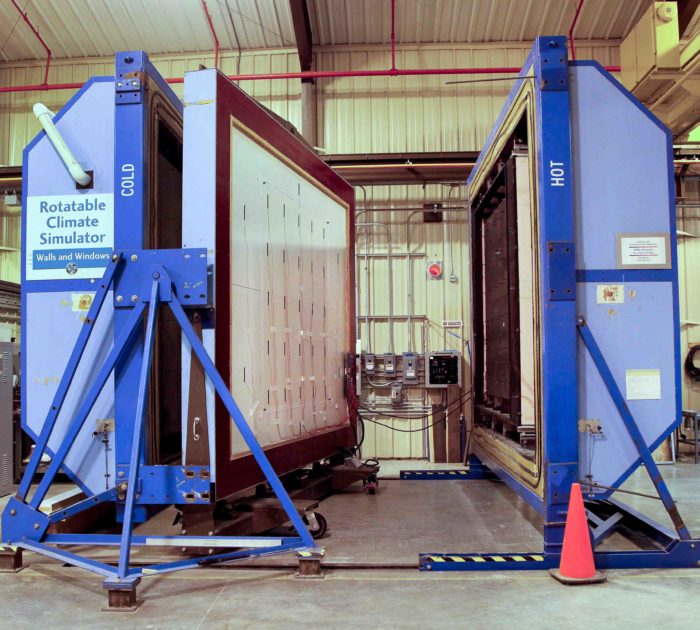
With lower costs, Desjarlais thinks the panels could have two important applications: retrofits for low-slope commercial roofs, and residential energy retrofits.
Rooftops of commercial buildings are often crowded with mechanical equipment and access hatches, making it difficult if not economically impossible to add layers of conventional polyiso during an upgrade. Having R-25 panels only 2 inches thick would be a breakthrough when space is a key issue.
Roofers would find the insulation very familiar. “We wanted to come up with packaging similar to what contractors see today,” Desjarlais said. “What better place to put it then right inside the foam board they’re used to handling. It looks like, it tastes like, it smells like a piece of polyiso foam. The only time you’ll know that it’s not is when you pick it up. It weights about five times more than a piece of polyiso foam.”
Residential energy upgrades also are a likely target for producers. A 2-inch-thick panel applied to the outside of the house would be enough to meet current energy codes in the continental U.S., even if the house had no cavity insulation, Desjarlais said.
One problem would be wall areas where standard 4×8 sheets or half sheets wouldn’t fit. Like the old vacuum panels, MAI sheets can’t be cut in the field without piercing the barrier and ruining the vacuum. The solution would be for a contractor to have standard polyiso on hand to fill in spots where the vacuum-panel sheets wouldn’t work.
Better performance over time
One advantage of making the cores of the vacuum panels from fumed silicate is that high R-values are possible without pulling a very “hard” vacuum, Desjarlais said. And, when plotting R-values against pressure, the curve tends to be very flat over a wide range of vacuum pressures, from 10 to 100 torr (torr is a unit of measurement for vacuums). That means the panels can afford to lose a relatively large amount of vacuum before their thermal performance fails.
“We can over-evacuate it and have quite a bit of cushion in vacuum loss before we see any significant loss of R-value,” Desjarlais said. “We think we can get 25 years of service out of a panel if we evacuate to a certain level. Even if it leaks, the R-value loss is minimal.”
Leaks should be less likely because the barrier material that’s used to encase the silica also is much better than what was available 25 years ago. Back then, vacuum panels relied on a two-component barrier of aluminized Mylar. Today, barrier materials are six or seven layers thick and don’t cost any more, he said.
Coming to market?
It’s one thing to develop a promising prototype in the lab, and another altogether to invest in manufacturing and marketing to get it to consumers. The panels appear to be working exactly as designed on a roof in Caribou, Maine, but will either NeoPore or Firestone feel good enough about its commercial prospects to bring it to market?
That’s not a question Desjarlais can answer. Both firms are apparently weighing their options at the moment and have not made a decision.
“I would say I’m cautiously optimistic,” Desjarlais said.
GBA emailed inquiries to both companies seeking comment on how likely it was that the ORNL research would result in a commercially available product.
In a reply, Firestone spokeswoman Laura McCaslin confirmed the company is working on the insulation, adding, “We can’t comment on any additional details at this time regarding commercialization or future plans for going to market as they have not been determined.”
NeoPore did not respond.
This post was updated on Sept. 25 to include new information from Firestone.
Weekly Newsletter
Get building science and energy efficiency advice, plus special offers, in your inbox.
5 Comments
"The facing of the foam is printed to show where the panels are located, so that if the roofing contractor wants to use mechanical fasteners to install the sheets it can be done — providing the installer is careful."
I'd be curious to know more about how easily damaged they are by fasteners, and how easy it is to find that damage before it all gets covered up. The proviso about the installer being careful means some training is required.
I'm really curious now, how long does more conventional forms of insulation last? 25 years seems like a pretty short period of time for something like this. I think I'd rather give up the couple of inches to not have to replace the insulation in 25 years.
I think they were looking at 25 years since that's about the replacement rate for some types of roofing. In commercial buildings it's pretty common to replace some or all of the rigid foam when re-roofing, upgrading to any new code standards, etc. That supplies a steady stream of still servicable used foam board at a highly discounted rate.
If replacement upon re-roofing is the standard they're shooting it has to be pretty cheap to make that worthwhile.
Thanks, that makes much more sense.
“[Deleted]”
Log in or create an account to post a comment.
Sign up Log in