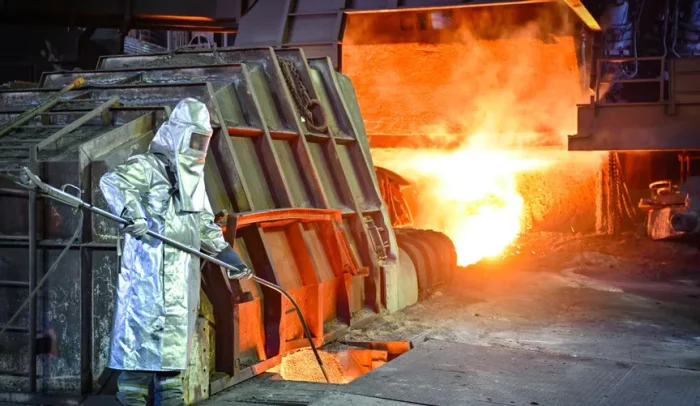
A shift toward greener steel production is starting to happen globally, giving experts a glimmer of hope that one of the world’s dirtiest industries might eventually decarbonize.
A new report by Global Energy Monitor (GEM) found that low-carbon technologies account for a rising percentage of the iron- and steelmaking capacity now under development around the world. Although traditional coal-based capacity is also expanding—and still chugging along in the United States—manufacturers are increasingly responding to growing demand for cleaner materials, experts say.
Steel is used in nearly every aspect of modern life, including buildings and vehicles, wind turbines and transmission towers, and refrigerators and washing machines. Today, steelmaking contributes up to 9 percent of global carbon dioxide emissions every year, while also emitting a witches’ brew of pollutants that harms neighboring communities.
GEM, a nonprofit research organization, has just released its fourth iron and steel report. The latest edition is the first to strike a more encouraging note, suggesting that, in certain areas, the industry may be moving in the right direction when it comes to achieving net-zero emissions.
Weekly Newsletter
Get building science and energy efficiency advice, plus special offers, in your inbox.
“In the last few years, we were really driving the point that we are so far behind, we are not on track, there’s so much work to do” on decarbonization, said Caitlin Swalec, one of the authors and GEM’s heavy industry program director.
“This report is a bit more like cautious optimism,” she told Canary Media, adding that “there are a few very important caveats”—namely, that projects actually need to be built as planned for the climate benefits to bear out.
Most of the world’s primary steel is produced using a two-step process. First, raw iron ore, purified coal (or “coke”), and limestone are dumped into a scorching-hot blast furnace to produce iron metal. Chemical reactions inside the furnace release carbon dioxide into the air. In the second step, molten iron is moved into a basic oxygen furnace, where it’s then turned into high-strength steel.
The main alternative for the basic oxygen furnace is what’s known as an electric arc furnace, which blasts bolts of electricity to melt iron—and, often, recycled scrap metal—into steel. When powered by clean electricity sources, this particular step of the steelmaking process can be virtually emissions-free.
In its report, GEM found that 49 percent of steel-related capacity under development involves an electric arc furnace, up from 43 percent in 2023 and 33 percent in 2022. If the new furnaces are actually built, and if enough existing furnaces retire, the global steel fleet could consist of over 36 percent electric arc furnaces in 2030. That’s nearly on track with the International Energy Agency (IEA)’s “net-zero aligned” roadmap for the steel industry.
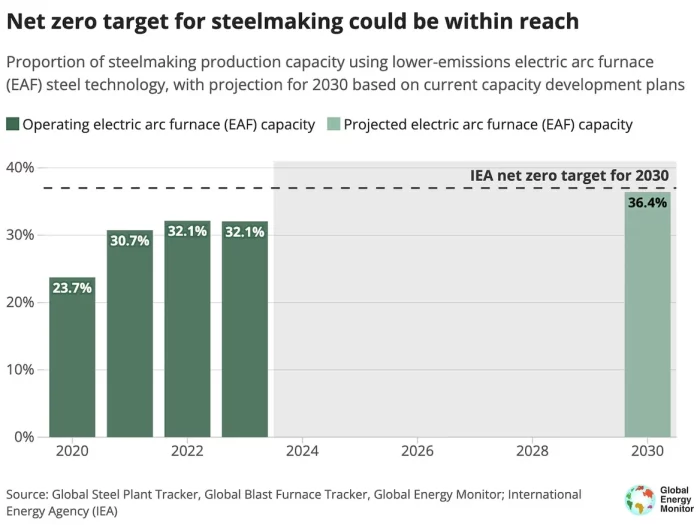
Much of the growth in electric arc furnaces comes from China, which is now the world’s second-largest steel producer after India. Even as China continues building new coal-based steel mills, the country is also expanding its steel recycling efforts, turning its old building beams and car parts into new metal using electric arc furnaces—a dramatically less carbon-intensive process than making primary steel.
As for replacing the blast furnace, the leading contender for that is direct reduced iron (DRI) production.
The process involves using a reducing gas to convert iron ore into hot briquettes of iron. A DRI plant that uses fossil gas typically emits 50 percent less CO2 than a coal-based blast furnace. But if the facility instead uses green hydrogen made from renewables, this process can achieve near-zero emissions.
Today, only 9 percent of global iron-making capacity is DRI, with the remainder being blast furnaces. But DRI accounts for 36 percent of global iron-making capacity now under development with a known production route, and with over 500,000 metric tons per year in capacity, according to GEM.
“That’s a pretty significant shift in the right direction, in terms of greening the iron-making world,” said Astrid Grigsby-Schulte, the report’s primary author and GEM’s steel project manager. “But it’s not quite significant enough to reach IEA goals.”
The 36 percent figure includes one of the two U.S. green steel projects in the works, which are each expected to receive up to $500 million in awards from the U.S. Department of Energy. Cleveland-Cliffs is planning to install a hydrogen-based iron-making facility at its existing steel complex in Middletown, Ohio. (Researchers weren’t able to confirm the planned DRI capacity for SSAB’s steel project in Mississippi.)
Grigsby-Schulte added that, most of the time, companies don’t specify whether they’re using fossil gas, hydrogen, or coal in DRI production, or whether they have plans to use only green hydrogen once supplies become more readily available. That makes it harder for researchers to know how exactly this shift toward DRI could impact emissions.
“It’s not super clear-cut,” she said.
Coal still on the rise
Still, the main cause for uncertainty—and the biggest threat to recent progress—is the ongoing expansion of coal-based blast furnaces.
Over 300 million metric tons per year of blast furnace capacity is planned in 16 countries, with most of those projects slated for China, India, Vietnam, and Malaysia, the report found. While those plans can change due to oversupply concerns, slowing economic growth, or unfavorable market conditions, they nevertheless suggest that the world is far from ready to ditch coal.
0 Comments
Log in or create an account to post a comment.
Sign up Log in