
The modular construction industry is undergoing a shift, prioritizing the prefabrication of complex, high-value components over entire buildings. This change addresses the challenges of high transportation costs, labor shortages, and escalating project timelines.
In this first post of a four-part series, I will delve into this evolving strategy. It highlights innovative solutions from industry leaders such as Green Canopy NODE and Tedd Benson, as well as insights I gleaned from attending Batimat 2024, Europe’s counterpart to the International Builders’ Show (IBS). In subsequent posts, I will explore panelized facades and the growing popularity of bathroom and kitchen units.
Rethinking prefab
In conventional modular housing, the ideal is to construct entire homes offsite, transport them, and install them on a lot—promising speed, factory-level quality control, and lower costs. However, many in the modular industry are rethinking this approach due to high transportation costs for bulky, low-skill sections like bedrooms and living areas.
A more efficient method is to prefabricate only the complex, high-cost components—such as kitchens, bathrooms, or wall cassettes that integrate plumbing, HVAC, and electrical systems into a single module.
Weekly Newsletter
Get building science and energy efficiency advice, plus special offers, in your inbox.
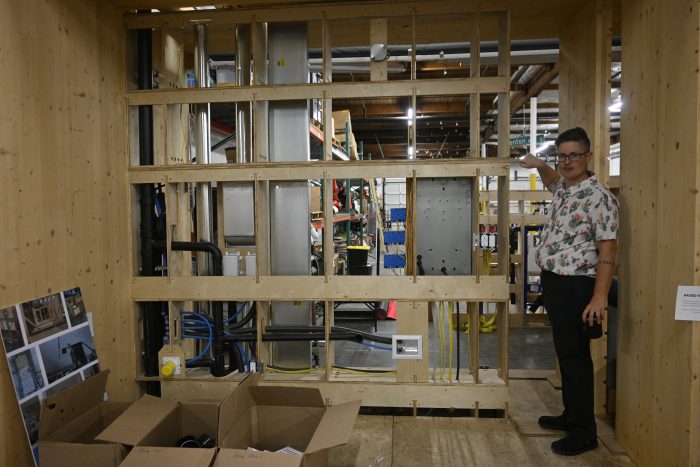
I met Bec Wilder, co-CEO of Green Canopy NODE, at the Washington Mall during HUD’s 2024 Innovative Housing Showcase. They exhibited a prefabricated, modular mass–timber building system, including a proprietary utility wall that caught my eye. Wilder calls it a “building kit” designed to turn construction into assembly. Two people can carry and install the plywood cassette in minutes.
The concept had heavyweight institutional support including Housing and Urban Development, the U.S. Forest Service, the American Wood Council, the U.S. Endowment for Forestry and Communities, and Mercer Mass Timber. They were…
This article is only available to GBA Prime Members
Sign up for a free trial and get instant access to this article as well as GBA’s complete library of premium articles and construction details.
Start Free TrialAlready a member? Log in
0 Comments
Log in or become a member to post a comment.
Sign up Log in