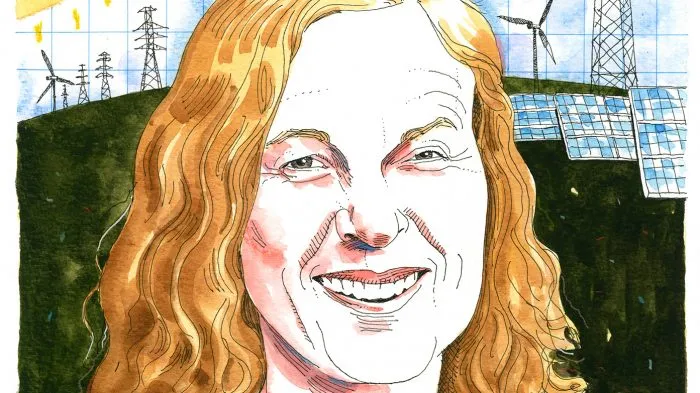
Katrin Klingenberg has been a driving force behind the adaptation and adoption of Passive House standards in the United States for the past 20 years. The underlying principles of passive building originated in the United States and Canada in the 1970s and were later enhanced and realized by the Passive House Institute (PHI) in Germany in the 1990s. Klingenberg reinvigorated the methodology for the United States in 2003, when she built the first Passive House in the country. Her home sparked such interest that she went on to found the nonprofit Passive House Institute US (Phius), which is dedicated to making passive building a mainstream best practice in the United States.
Klingenberg has developed and delivered building science–based training on how to design and build energy-efficient and zero-energy buildings, and over the past 10 years she has collaborated with federal and state government agencies to tailor and cost-optimize the Phius standard for each of the nine U.S. climate zones. She has also consulted internationally to adapt the standard for climate zones around the world. Phius continually refines the standard to meet increasingly stringent efficiency goals, to make buildings meet carbon-neutrality goals, and to make buildings the core building block of the 21st-century electrical grid: resilient, digitized, distributed, and interactive.
In Klingenberg’s role as executive director of Phius, she oversees the technical, research, and educational programs of the organization. She earned a B.S. in architecture from the Technische Universität in Berlin, and an M.S. in architecture from Ball State University. She is a licensed architect in Germany, and has designed and consulted on numerous passive-building projects globally, written magazine articles, and made several book contributions. Klingenberg has presented nationally and internationally on the topic of passive-building science. In 2015, she won the Woman in Sustainability Leadership Award (WSLA), and in 2017 she was one of 12 women entrepreneurs selected from around the world for the Global Ambassador Program of Vital Voices. In 2022, she won the Professional Leadership Award of the Northeast Sustainable Energy Association (NESEA).
Aaron Fagan: Could you walk us through the background of Phius?
Katrin Klingenberg: In 2002, I decided to build the first Passive House in the U.S. Once I had done that, it became clear it could be a great opportunity for affordable housing development, because the energy cost is essentially nonexistent. So we decided to form a community housing development organization in 2003, and we built three affordable homes with grants and land we received from the city of Urbana, Illinois.
As soon as we had those projects underway, we started to attract attention. Very quickly, we were drawn into the high-performance-building community around the Department of Energy (DOE). From there, we realized there’s huge interest and potential in Passive House principles, so we shifted our focus from building houses to education. We started teaching people the modeling process and the design theory.
Our growth was driven mostly by word of mouth. We never advertised. We started an annual conference, and from there we developed the Phius certification process. Of course, initially we worked with PHI in Germany to develop the process, but it was an immense challenge to adapt that standard to all the different climate zones in the U.S. So in 2012, we decided to switch gears. We realigned ourselves with the DOE here in the U.S. instead of PHI, and we have a memorandum of understanding with the DOE’s Zero Energy Ready Home (ZERH) program. That was also when we started collaborating with Building Science Corporation (BSC) under a DOE grant on the development of the climate-specific passive-building standards. That’s really when Phius as we know it today started.
AF: It seems like things are really ramping up with serious investment regarding the electrification movement. The moment is ripe for a culture change where energy is concerned. I would love to hear your point of view. Are you optimistic? Are you cynical? A mixture of both?
KK: I’m optimistic, because my passion is the building side of things, and we have the solutions. We have the technology for super-low-load buildings. We’ve known how to do this for the last 20 years. And Phius’s code for all multifamily buildings over 12,000 sq. ft. just went into effect this past December in Massachusetts. That’s tremendously exciting.
Right now, we’re trying to educate the powers that be that electrification cannot just happen by itself. We have an aging grid, and it’s not built for everything to go electric at once. There’s a connection between electrification and building energy efficiency—it’s the cornerstone of electrifying everything. If we don’t upgrade our existing buildings and bring our codes up to speed to be like Phius-type buildings, then the grid will not be able to handle what will come its way. With all the EVs and heat pumps, we will have a very unreliable grid. We have energy-efficiency solutions for new and existing building stock that will mitigate the grid issues, but we need to implement them.
AF: Within the culture of home building, what are some of the most significant changes in understanding that you’ve witnessed over the last decade?
KK: Well, the Phius level of energy performance is really filtering into the building industry now, but for me personally, it’s the understanding that the Phius level of energy performance is what we will have to achieve in all new construction, for all building typologies, and for the existing building stock. Once we reduce our energy to that level, we’ll have the chance to reduce our carbon emissions globally to where we need to be in order to stabilize the climate. That was an important thing to learn.
Another lesson is that one size does not fit all. As we developed climate-specific standards, it became clear that a passive building in Miami has different requirements from one in Cleveland or Fairbanks. That seems like a no-brainer now, but we learned a lot from the mistakes we made trying to develop and adapt the PHI standards to the U.S.
Finally, there is the idea that building bigger buildings, such as multifamily dwellings, is really the ideal scenario. We are building large multifamily projects in New York and Massachusetts where the costs of detailing to get to Phius standards are minimal. If you start with an airtight building, it only takes a little bit more insulation than the best energy code already requires along with some better windows to raise the energy efficiency. The additional up-front cost for building larger multifamily buildings is only about 2% to 3%. There’s no compelling reason for developers to avoid making more energy-efficient multifamily homes.
That gives me a lot of hope, because most of those projects are also affordable housing. We’re addressing equality and economic mobility. Energy costs have been reduced significantly at the same time we have provided much healthier environments. If we can succeed at making Phius the national standard for buildings, which it should be, we’re on a great trajectory to meet climate and electrification goals. Those are the key lessons that I’ve learned over the last 10 years.
AF: Are there near-term goals you hope to achieve that play into this larger vision of making Phius the standard?
KK: The reason that the uptake is so successful on the East Coast is because New York State was ahead of the curve in trying to meet its climate-action goals. When we came along, Phius standards were a perfect fit. Together, we pioneered an approach of creating incentives, getting the standards into qualified allocation plans (QAPs) for affordable housing, getting the standards incentivized through utilities, and then having them incorporated into the stretch codes (which become de facto code in about two to three years). That created a model of how to move the adoption forward incrementally but quickly, and that model is now making its way across the country.
This past year, we’ve seen significant success in Illinois, where Phius is well-positioned to soon be written into the energy code. In Chicago, the Chicago Energy Transformation Code is following the same pattern that New York and Massachusetts pioneered. For example, ComEd is incentivizing a small group of demonstration projects, and once that is successful, the Phius code will move closer to mass adoption by other states. And like New York and Massachusetts, the work has begun to integrate the standards into the next stretch code in Illinois. If we can get that process rolling in a lot of states, we won’t be far from our original mission in 2003 to make Phius mainstream or code. At that time, it sounded like a crazy idea, but hey, don’t make small plans.
AF: So many of these things are about people having the will to see things differently. The knowledge base is there.
KK: The last couple of years we’ve seen an exponential growth curve. Phius now has three times as many people on staff as we did at the beginning of 2020. And we’re looking for the next frontier, like retrofitting. Nobody has really cracked that nut yet. The DOE is investing a ton of money into retrofitting to find out how we can use industrialized retrofitting like panelization to accomplish retrofitting at the scale necessary to meet goals. We’re calling this year “the year of the retrofit.” We had a retrofit summit in March.
The other thing on the horizon is microgrids. A microgrid is a small network of electricity users with a local source of supply that is usually attached to a centralized national grid but is able to function independently. How can we integrate solar production into microgrids to reach net-zero? Once you have the low-load building envelope and you add solar, then we can start to work on sizing and optimizing the solar for maximum efficiency. We have rebranded ourselves, so our slogan now is “Zero is the goal, and Phius is the means.”
The existing grid won’t be able to handle the demands of the government’s electrification goals. The only way to attain the goals will be to reduce load, and optimizing buildings is essential to that end. With solar, you may very well add energy to the grid rather than draw from it. That is our current research focus: How can we get this holistic solution market-ready? How can we describe the relationship between the microgrid and the building envelope to manufacturers and suppliers so that they create more products, and to developers so that they use solar more readily as part of their builds? That’s our most recent endeavor, and while I can’t say we’re close, we’re working on it.
AF: Retrofitting will be an essential part of the equation with electrification, and we have a huge amount of existing building stock that will need to be compliant. How does that work in terms of industry and materials?
KK: I don’t think that technology is necessarily the hurdle. Once the market is there, I think the industrialized processes and factories will figure out how to produce what we need. For the time being, we’re still in the assessment phase. We’re working with the Rocky Mountain Institute and the DOE on the industry guidance report for retrofits that is based on industrialized production of panelized building products and of systems. From our perspective of standard setting, we’re analyzing that approach. The question becomes this: If we can make those panels and we can upgrade everything quickly, how do we make it work when one solution does not fit all conditions? You might say to just take the regular Phius standard and make it the rule, but that’s asking for a lot of insulation. And if you retrofit the entire building stock of the country with a whole bunch of insulation, which has a ton of up-front carbon emissions in it, over a short period, you’ll actually be hurting the planet with emissions.
We can’t do that, so we have to think about it differently and try to reduce the insulation (i.e., the embodied carbon). How low can we go without losing resilience? We’re trying to find the sweet spot between resilience and added insulation. If you build without insulation because you’re trying to reduce the embodied carbon, you wind up creating an energy hog. If you overinsulate, you have so much embodied carbon expended that no amount of energy savings will balance out in operating carbon. To emphasize the importance of resilience, we’re creating a new certification program, Revive, which will be based on resilience criteria rather than energy use intensity (EUI).
AF: Is a carbon budget a concept that interests you? When you think about carbon, what do you think about?
KK: To set our standards in the first place, we looked at the total global carbon reduction that we must come up with based on the 2018 UN IPCC report (to stay below a 1.5°C temperature increase). We basically walked our way back, asking what level of efficiency all buildings need to have to meet the goal. That’s essentially where we ended up with the EUI for current Phius standard. It’s nonnegotiable. So, carbon budget? No—the only objective is neutrality.
New construction should not be built to anything less than Phius standards, period. However, we’re in a bind with the existing building stock because we have such little time. So for existing stock we are going to try to reduce carbon emissions while also getting faster electrification and more renewables, which need to make up for what we might not be able to put into the building envelope. We can’t just say we need to stop using carbon today; our entire economy is dependent on carbon. It’s a very complex problem. How quickly can we reduce our use of carbon, by how much, and where?
AF: What’s the biggest pain point or resistance that you face?
KK: It’s still cost—also, the common growth mindset in our economy. Everybody is trying to maximize growth. We have to rethink our economy completely. A growth mentality leads to developers and builders wanting to make the most money when they design and build a building, which keeps them from investing in materials and technologies that allow the planet to continue to exist. That whole economic model needs fixing.
The pain point for the person who’s trying to incorporate planet-friendly approaches is a direct result from the growth economy, because that person is competing with all the other people who are still just maximizing profit. Even if a person wants to do the right thing, it means they are disadvantaged in competition with the other people who are focused on growth. That’s obviously not sustainable, so we have work to do on that economic end.
AF: When you think of our readership, what are some things that come to mind?
KK: I assume your readers build mostly single-family homes, maybe small multifamily homes too. I would encourage everyone to make a personal choice to build so that they’re not a liability for the planet, aligning themselves with our targets right now. I would also encourage folks to get really involved in the retrofit market and master it, because I think it will be the biggest single business opportunity in the near future.
You’ve interviewed a few building-science stars, and building science is so important in the retrofit market because you must know what you’re looking at. You need to assess your building correctly; otherwise, you can quickly create a biological building-science experiment. I think we need some really dedicated professionals who make building science their mission. I would love to see the stars of Fine Homebuilding and GBA take up that challenge.
AF: That’s a great charge. Are there any closing thoughts you’d like to add?
KK: It might be time to rethink trades education so that people come with certain pride to the construction site. I think that a rigorous building-science training program would give people pride in what they do because they would see clearly how their part is connected to the whole building and beyond. And they’d be helping save the planet.
________________________________________________________________________
Aaron Fagan is a senior editor for Gear Technology and Power Transmission Engineering magazines. The original article appeared in Fine Homebuilding magazine, issue 315.
Weekly Newsletter
Get building science and energy efficiency advice, plus special offers, in your inbox.
One Comment
Thanks to GBA and FH for sharing this article. With a degree in architecture I’ve had an interest in Passive House for several years, and later stumbled into the DOE’s Weatherization Assistance Program (WAP). This program hits so many key points to what Katrin mentioned, especially in affordable housing, multifamily work and retrofitting. WAP has been around for 40+ years, was instrumental in bringing blower door and IR camera usage into the mainstream, and comes with a multitude of benefits including it’s non-partisan, helps low-income folks, supports local economies, saves money and energy, teaches trade skills, etc.. The list goes on.
However (why is there always a ‘however’?), we’re also a proverbial canary in the coal mine at the moment. Due to rising construction costs, increased retirement, an inability to get younger people in the trades and other factors, we’re starting to struggle in ways that weren’t evident even a few years ago. There needs to be a national educational and financial incentive to push the importance of this type of construction to make it succeed. But in the meantime, it’s heartening to see someone of this stature being so optimistic and forward-thinking about something that affects us all. Keep up the good fight, Katrin.
Log in or create an account to post a comment.
Sign up Log in