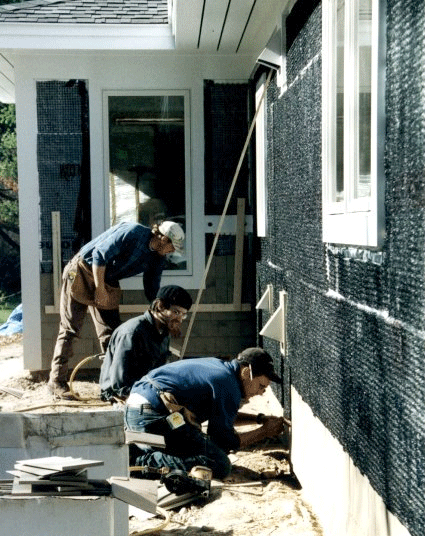
Image Credit: Design Concepts Company (dcchomes.com)
Last week I wrote about “deep-energy retrofits”—strategies for dramatically reducing the energy consumption of an existing house. In northern climates, such retrofits often involve adding a layer of rigid insulation to the exterior of a house. If you’re removing the siding to add insulation, this is a great time to provide a drainage layer—or “rainscreen”—before reinstalling siding.
A rainscreen detail provides an air space between the exterior siding or cladding and the wall sheathing (whether rigid insulation, as described above, plywood, or wood).
That air space does two primary things. First, it allows any moisture that gets through the siding or cladding to evaporate and dissipate up and out, or flow down to the bottom of the wall.
Without this air space, moisture can soak through into the wall cavity—where it can potentially cause rotting and mold growth, and (with fiberglass or cellulose insulation in the wall cavities) significantly degrade the R-value of the insulation. In fact, if siding or cladding gets wet and then heats up (such as when the sun comes out after a rain storm), that heat can create a strong driving force for water vapor—pushing that moisture into the wall.
Second, a rainscreen ensures that the back side of the siding or cladding will maintain similar conditions as the front side. This reduces stress on the siding or cladding, which improves the service life of both the material itself and any coating. Painted wood siding, such as clapboards or board-and-batten, installed over a rainscreen can dry out after it gets wet and won’t have to be repainted as often. In relatively rainy climates, most houses with wood siding have to be repainted or stained every four or five years to keep it looking good, but if the siding is properly primed and painted (see below) and installed using a rainscreen detail, it can last more than 15 years before repainting or staining is needed.
While rainscreen detailing doesn’t affect energy performance to a significant extent, it is particularly important with a highly insulated wall system that may have difficulty drying out if it gets wet. Building science expert Peter Yost suggests that we “manage energy and moisture with equal intensity.” Any time we make improvements to a home’s energy efficiency, we should look for opportunities to improve durability. Furthermore, less frequent painting or siding replacement indirectly saves energy, because of the energy that’s “embodied” in those materials we would be using.
Rainscreen detailing should be a part of standard construction practice. The rainscreen can most easily be made with strapping installed over the sheathing (1x4s, for example)—perpendicular to the siding. With horizontal clapboards, vertical strapping should be installed; for board-and-batten siding, horizontal strapping.
There are also some specially designed materials that provide a rainscreen, such as “Cedar Breather” from the Benjamin Obdyke Company. When providing a rainscreen, the window and door trim has to account for the added thickness.
While a rainscreen detail is important with wood siding, it also makes sense with fiber-cement siding and brick cladding. Brick can absorb a lot of water, which can be driven into the wall when the exterior heats up. Vinyl siding usually does not require a separate rainscreen, because it’s made in such a way that air can flow through it relatively easily. Creating a rainscreen takes a little extra work, but it’s a no-brainer as far as I’m concerned. In fact, I believe it’s so important that it should be required by code.
On the subject of the durability of paint, it’s worth noting that if new wood siding is being painted, it should be primed and painted on all four sides (and ends) before it is exposed to sunlight for a significant period of time. The best option is to do all the priming and painting before installing the siding (some siding is sold with factory priming). Once wood is exposed to sunlight, the surface begins breaking down, and it will not hold paint as well.
Weekly Newsletter
Get building science and energy efficiency advice, plus special offers, in your inbox.
6 Comments
MTI's Sure Cavity - rainscreen drainage plane system
For those of you looking for an environmentally friendly option to rainscreen drainage planes, check out MTI's systems. Our products are made from 100% post-industrial recycled material AND were used in the Margarido House (1st LEED-H certified, GreenPoint rated house in the country). We're dedicated to green building and would love to help you reduce your footprint, too! Visit http://www.mtidry.com for more information. Thanks! John Koester, President
Moisture retention in brick veneer walls in the humid South
It is common practice in our area (Gulf Coast: Humid, high wind) to build brick veneer walls to 1 storey houses. These are typically built with max 1" cavity, lots of mortar droppings in cavity, poorly galvanised crocodile brick ties and 6 mil polythene taken up 24" behind the osb sheathing and then taken across the cavity bottom and out through the brick beloww the weeps. To me the cavity will never be dry either because of blocked water egress or condenstion or both. The bottom of the OSB often contains critical nailing (into the bottom plate) to address uplift.
Has anyone experience of this or measures to combat it ?
They use 6-mil poly for through-brick flashing?
Six-mil poly used in this location is a code violation. Brick weep holes must be flashed with "approved corrosion-resistant flashing" according to the IRC, sections R703.7.5 and R703.8. If your mason is using 6-mil poly instead of flashing, the mason shouldn't be paid.
Unfortunately 6 mil poly is
Unfortunately 6 mil poly is corrosion resistant !
However the "approved" as with many parts of the code empowers an inspector to set his/her own level but there is builder pushback when you fly solo like that.
Has anyone any suggestions for:
1. Mortar droppings. Does "mortarnet" work ?
2. "Galvanized" brick ties. These seem to corrode in 15-25 years, and are expensive to retrofit.
3. The condensation risk from putting a vapor barrier behind the bottom 18" of OSB in a hot humid mixed climate where it can freeze nights for 3 nights at a time.
Flying solo?
Nick,
I'm not suggesting you "fly solo." I suggest that you follow accepted industry practice — that is, the recommendations of the Brick Industry Association. You should consult two of their Technical Notes, #7 and #7A. Here are the links:
Number 7, "Water Penetration Resistance - Design and Detailing"
http://www.gobrick.com/omnisam/common/getfile.cfm?file=/bia/technotes/TN7.pdf
Number 7A, "Water Penetration Resistance - Materials"
http://www.gobrick.com/omnisam/common/getfile.cfm?file=/bia/technotes/t7a.pdf
According to Technical Note 7A, "A minimum thickness of 30 mil (0.76 mm) is recommended for plastic and rubber flashings." As Jerry Carrier pointed out in an excellent JLC article, "The BIA recommends that most nonmetal flashing should be at least 30 mils thick, which means that polyethylene, housewrap, and #15 asphalt felt are not acceptable flashing materials."
To download Jerry Carrier's article (from the November 1999 issue of the Journal of Light Construction), "Keeping Water Out Of Brick Veneer," go to
http://www.jlconline.com/cgi-bin/jlconline.storefront/4a817468047a5e6b27170a32100a0661/Product/View/9911keep .
Cavity drainage
Martin,
Thanks.BIA seems a great source.
Is anyone aware of investigation work into exterior walls
that examines their performance (in dealing with moisture) over time ? (E.g. How they've actually worked say 20/30 years down the road ?)
Nick
Log in or create an account to post a comment.
Sign up Log in