Editor’s note: Carri Beer and Michael Hindle are renovating a 1954 house in Catonsville, Maryland. Hindle is a Certified Passive House Consultant and owner of Passive to Positive. Beer is a registered architect who has been practicing sustainable architecture for 18 years. She is an associate principal with Brennan+Company Architects. For a list of the couple’s posts, see the sidebar below.
So I know that most readers are interested in energy improvements, systems, insulation, and air sealing — but first things first. All in due course, dear readers.
Before moving children and ourselves into this house, we absolutely had to address some of the indoor air quality issues. For better or worse, we were in the slow and excruciating process of selling our little bungalow, so we stayed there while removing carpets and “detoxing” the new place.
This house was previously occupied by two large American bulldogs and one cat, and when we purchased the home, every window sill and screen was matted with dog hair. The perimeters of the tile floors and baseboards in the kitchen and entry were coated with a dried film of drool, dog hair, or both. It was a big job!
Removing the allergen traps
The three bedrooms, hallway, and giant family room upstairs had carpet — nasty, smelly, animal-stained carpet that was likely 15 years old. We removed the carpet and discovered plywood subfloors and remnants of variously colored shag snags on nails from carpets dating back over the course of 60 years. Animal stains on the carpet penetrated right down to the plywood.
Despite growing up with the luxury of 1970s shag, much like the remnants we discovered, we opted for no carpet, knowing that it harbors dust and allergens — not to mention being petroleum-based and laden with carcinogenic flame retardants. There are natural carpet alternatives, but they are still expensive allergy traps.
Therefore, we decided to install floating cork floors. Why cork? We needed something with a low environmental impact that we could do ourselves, and we wanted something that would provide a soft, warm surface for bedrooms. Cork was the obvious answer. In our previous house, we had it for eight years and were very happy with it.
With the help of friends and family, we replaced all the carpet in the upstairs bedrooms and hallway (645 square feet) with floating cork floor for $1,900. The cork is from APC and was purchased on Build.com. After examining many samples, we settled on plain ol’ cork pattern. It was the least expensive, and it turns out, quite beautiful just being itself. This particular cork company has a matte finish and it shows some footprints, but it’s easy enough to maintain and clean with a damp rag. We have a few installer defects that we cringe at in certain light conditions and from certain angles, but generally speaking, we love the floor.
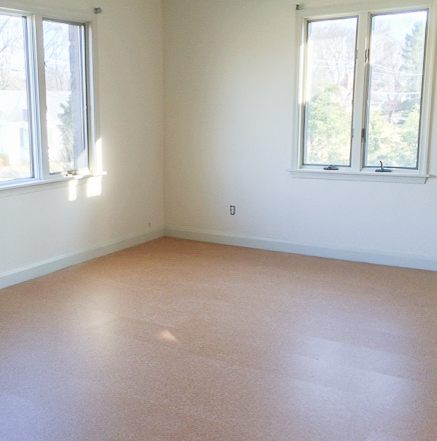
We also removed the carpet in the giant room and exposed the original asbestos tile adhered over the concrete deck above the garage. Once we’ve built our new exterior wall, we will add 1 1/4 inches of mineral wool insulation, plywood subfloor and, eventually, install cork in the future dining room.
Nothing like a fresh coat of paint
Before we moved in, our incredible parents came and stayed with us and helped us clean and paint the bedrooms. We are a bit frustrated by the current marketing of zero-VOC paint — it’s better than it used to be, but we believe that consumers are being misled and have been lulled into complacency about the chemical pollutants in paints.
Zero-VOC doesn’t mean zero-odor or zero-chemicals. The EPA allows paint to be called “zero-VOC” even if it’s not. In addition to having low levels of VOCs, zero-VOC paint also can contain formaldehyde, solvents, vinyl chloride, heavy metals, phthalates, and acrylic softeners — just to name a few. We were determined to find better.
In doing some materials research for a Living Building Challenge project, we came across ECOS paint. The company has some great research on its website. Basically, ECOS has none of the aforementioned toxins and is great for those with asthma or chemical sensitivities, and for maintaining the general health of those who apply the paint or live in a painted space.
The price was a bit more than Sherwin-Williams zero-VOC paint, but it was well worth it. The paint colors are beautiful and it’s really wonderful to use. We lived and worked in the house as we (mostly the parents) painted it and could not even tell — honestly — that painting was going on. So far, we used family labor to paint 85% of the spaces and have spent $900 on paint, with enough paint left over to finish some accent walls or smaller spaces.
Don’t forget the basement!
As mentioned above, the entire basement also has carpeting. It’s only four years old, but it will be removed when we insulate the slab.
The basement bath and laundry demo started a little sooner than we anticipated. Perhaps it was the toilet constantly backing up, or the dank smell, or (most likely) it was our daughter finding a giant house centipede on her toothbrush.
In an effort to discover the source of the problem, we decided to look inside a mysterious box built into the laundry room. Come to find out the mysterious box was housing a sewer ejector pump serving the laundry and this bathroom. The top of the ejector pit was, shall we say, not sealed properly. So if you want to talk indoor air quality, let’s not forget sewer gas!
This space was immediately demolished to reveal all the plumbing and seal off the pit. We discovered sagging waste lines, copper supply lines embedded in the plaster on exterior concrete walls, and other fun plumbing follies. This, of course, has turned into one of those unforeseen uses of contingency money.
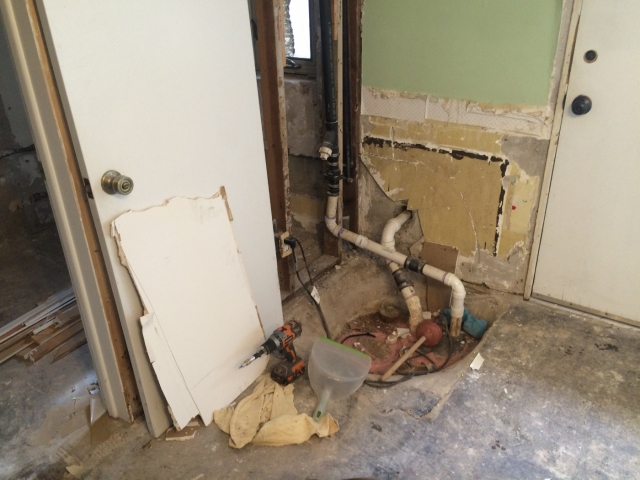
What’s more, it is freezing down there in the winter and spring and cool but damp in the summer. As we’ve said previously, whether we like it or not, basements are being used as livable spaces by many people (and now us), so we want to devise safe and healthy methods for properly protecting these spaces from moisture, air (and bug) infiltration, and go give them adequate insulation to reduce energy consumption and improve comfort.
Damp sills, black mold
As we considered our plan of attack, we did some exploratory demolition and found what we expected: damp sill plates, black mold on the back of the drywall, spalling mortar, and efflorescence on the block walls. The sill plates were pressure-treated, but there was no capillary break between them and the floor, so the plates soaked up water and transmitted it up the bottoms of the studs (see the photo at the bottom of the article).
We are big advocates of avoiding toxins in buildings and avoiding global warming potential of insulation materials, so rather than filling the stud cavities with foam, we removed all the drywall and studs in order to properly moisture-proof and insulate.
All the extra work is worthwhile. We sleep better at night knowing we will be creating a healthy space for our children and parents and any future residents. Details of how we will be retrofitting this are still in progress and will be explored with drawings and photos very soon. We need to make this space livable, so we are moving quickly.
The previous installment of this blog series by Carri Beer and Michael Hindle was called No, We Are Not Crazy.
Weekly Newsletter
Get building science and energy efficiency advice, plus special offers, in your inbox.
0 Comments
Log in or create an account to post a comment.
Sign up Log in