Is my basement actually a crawl space and should I treat it as such?

As part of the complete renovation to my century-old, balloon-frame house in Atlantic Canada (zone 6), I think I should encapsulate, insulate, and condition my basement / crawl space. I will never want to “finish” it into a “living” space so it will only ever act as a mechanical/utility room and storage for outdoor seasonal stuff. Although the foundation walls are sturdy (no bowing, major cracks, or crumbling), most of them are old porous beach gravel concrete (8”-10” thick, 62” tall) topped off with five double courses of old red chimney brick (8” thick, 12”-14” tall). I had to replace a corner section of the walls that was still stone and mortar and was falling apart so I formed and poured a new 18” wide by 8” thick footing, a new 8” thick by 64” tall concrete wall, and built a 16” tall wall on top of that out of pressure treated 2x6s and 6x6s 12” o/c with sill gasket underneath and on top of it. I extended the new wall beyond the footprint of the house to create an exterior stairwell that is covered by a hinged metal roof (there is no stairwell or any access to the basement from inside the house). I will build an insulated wall and large door out of pressure treated plywood and lumber plus foil-faced EPS with weather stripping to close off the stairwell from the rest of the space. The floor is cracked, broken up, and uneven concrete/dirt/gravel (remnants of a rat slab) with lots of irregularities including a built-up area in the middle where the chimney and furnace used to sit. The height from the floor to the bottom of the joists is anywhere from 72” to 76” and the joists are 9.25” high. Outside the grade is at least 16” below the sill and slopes away from the house. Inside I have about 5’ below grade and 2’ above (up to the underside of the first floor boards). The first floor is the original two layers of ⅞”-1” thick boards and I installed ⅝” T&G OSB continuously over the whole thing and then built all my new walls on top of that.
(Is there any benefit to me taping the seams of the OSB on the first floor, caulking around the bottom plates, and sealing any penetrations in an attempt to achieve an air barrier between the different spaces?)
My electrical panel is down there and I will also probably put my electric water heater and a central vacuum down there. I may install a crawl space dehumidifier or just stick with the portable one if it can keep up. I may want to put an ERV and possibly a ducted heat pump down there both with mastic-sealed rigid ducts but there will not be any combustion furnaces or appliances anywhere in this house.
(Since I don’t think I want to mix the basement air with the two stories of living space above, does it make sense for me to not have any supply or exhaust down there?)
It is not uncommon for all of my neighbours to have water in their basements in the spring but our house sits a couple feet higher and, although we have never seen any standing water, it is always quite damp. One time, during a sudden February thaw, I did see water trickling down the inside face of the walls (picture a water feature in a hotel lobby) but it just instantly drained away into the floor/ground. Since then, I have excavated about halfway around the outside of the basement (when replacing the corner walls) and covered the exterior of the walls with dimple mat and installed a burrito-like footing drainage tile system of 4″ perforated PVC set in about 18″ of drainage stone wrapped in landscape filter fabric. I have also already dug a trench all the way around the perimeter inside the basement and installed an interior drainage system similar to the exterior; it will dump into a sealed sump basin with two sump pumps (one as a battery backup). I’m hoping to have the interior setup pull double duty by also being used as part of a radon mitigation system in the future if I seal everything off. I was thinking that once I’m done with the mechanical rough ins I should put 2”-3” of foil-faced EPS on the walls, 10-mil poly on the floor (run it up the face of the insulation by about a foot and tape it), and top it off with a yet-to-be-determined approach to the “rim joist” (balloon-framed) area – see below.
(Is 2” of foil-faced EPS appropriate and is it acceptable to install multiple layers of foil-faced EPS to fill the old window holes and the short studded wall?)
As for the “rim joist” area, I am planning to have the above-grade walls (which are original balloon-framed and a new 2×4 wall with a gap to create an 8” deep double-stud wall) dense-packed with cellulose. At the bottom of the balloon-framed stud bays the cellulose will occupy a 4” thick by 4” high area which is technically part of the exterior wall assembly but also part of the “rim joist” area. I was thinking about stopping my wall EPS a couple inches below the bottoms of the floor joists and having up to 3” of spray foam applied to the “rim joist” area and across the top of the EPS tying everything together.
(Will that assembly be ok? Should it be closed-cell or open-cell? Should I leave the rough 2x4s in place that block off the stud cavity from the basement and spray over them or should they be removed for some reason? Is there a better way to do this?)
Thanks everyone,
Pat
GBA Detail Library
A collection of one thousand construction details organized by climate and house part
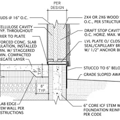
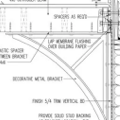
Replies
It is very difficult to fully separate the basement/crawlspace air from the living space air, so I recommend making the air quality in your lower level as good as it can be. If you do that, you don't need to seal the first floor framing. You should condition the lower level air with heat, and dehumidification if necessary.
For insulation, I recommend using either Thermax polyiso foam, which is available with a white foil facing and is rated to remain exposed, or closed cell spray foam with an intumescent coating. EPS can only be used if it's covered with a fire-resistant material.
Thank you Michael,
If I don’t air seal between the two spaces and do get pretty good air quality down there would I still want to purposely mix the air between the two spaces with shared ducts from an ERV or furnace or should the lower space have a dedicated heat source like a baseboard heater or something?
I will look into Thermax and see if I can find a dealer near me. The reason I was thinking EPS is because ‘I know a guy’. So I’m guessing if I can’t get Thermax or the cost difference warrants the following, I could go with EPS but would have to strap it and install a layer of drywall? Any chance intumescent coatings will adhere to foil faced EPS if that cost isn’t more than Thermax?
Should I continue to worry about the awkward “rim joist” detail? (I wish I knew what to call that area.)
Yes, in fact mixing the air is a code requirement. There's a lot of good info in this article: https://www.greenbuildingadvisor.com/article/building-an-unvented-crawl-space.
Thermax is expensive but it's the only insulation product that is code-compliant and safe to remain exposed. I'm not sure but I imagine intumescent coatings would adhere to foil, or at least some types would, but they aren't cheap either.
I don't understand your description of your rim joist plans; can you share a section drawing?
Thanks for the article suggestion, I’ll read through it tonight.
I’ll start rounding up quotes on Thermax and the other options discussed.
I don’t know how to draw up CAD details and my sketches with pen on paper will not suffice. Hopefully the notes on the attached drawings will help. When the walls are packed with cellulose the small area at the bottom of the original exterior wall (balloon framed) will be filled with cellulose as well as it is actually part of the wall. So behind the “blocking” and between the bottoms of the balloon frame studs and the ends of the joists will be pockets of dense-packed cellulose 4” thick. If I keep the blocking in place (thinking it serves a purpose of containing the cellulose and acting as a fire block) then the finished assembly of that little 4” thick section would be:
-vinyl siding
-house wrap
-1” rough sheathing boards
-4” thick of dense-packed cellulose
-2” thick of rough 2x4 block
-one of the following two options
—2” foam board insulation (or thicker, or extra layers to build it out to a flat plane in line with the inside face of the concrete wall) sealed in place with can foam/caulk,
- or -
—up to 3” of spray foam (plus intumescent coating) between the joists and overlapping the rigid foam boards below
I have read dozens of articles and other Q&As on here. There were a lot of similar questions to this but they all had slightly different conditions such as exterior insulation, interior fibrous insulation, the joists were embedded, or they were in a different zone, etc. Some touched on the potential for wicking from the masonry of the foundation and that moisture being trapped by foam or other barriers could cause mold and rot in the sill, joists, studs, and/or sheathing. I remember one expert commenting on less issues with wicking on certain types of foundations but now I cannot find which Q&A that was out of the 100 links in my browser history. So far, the wood in this area has lasted over a century and is in great shape but there has never been any insulation or air sealing and it was heated with coal, wood, and oil before I came along.
Ah, that helps, thank you. Stone foundations are less prone to wicking than concrete, which is porous. In your climate, drying is usually to the exterior so as long as you don't have an impervious coating on the exterior (such as Ice + Water Shield) I think your proposed assembly will be fine.
Deleted