Insulating top of basement slab – Is moisture still a problem with a barrier?

Is insulating the top of a non-walkout basement slab floor in climate zone 6 really valuable if the slab has a moisture/vapor barrier beneath it? Goal is carpet on top for most to the space. What happens in the event of water flooding from a toilet or clogged drain?
My reading on GBA and Building Science have lead me to believe my greatest enemy is the dew point and possibility of mildew smell and maybe mold. National home builder of the neighborhood does not insulate the slab on either side when they install carpet. Floor temps in homes they build feel fine to feet in socks in the dead of winter.
I am struggling with the effort & cost to insulate the on top of the slab. I would do 3/4″ or 1″ XPS with 5/8″ OSB Tongue and Groove attached to the slab. On the effort side of things, framing is complete so additional blocking (double the sill plate in essence) will be needed to have a functional sill plate for drywall to rest on due to the new floor height (exterior walls will need spray foam trimmed to accommodate blocking), door openings would need some modification, and my strategically place air returns (just high enough to not necessitate notching baseboards) would need moving.
Background:
Climate zone 6 (Twin Cities, MN) Home built in 2014. Two story with a basement (not walkout. Roughly 6′ below ground). No ERV/HRV. Constant running fan in upstairs and a fresh air intake in the basement utility room. 2.2 air change per hour (door blower test by energy consultant). Basement walls and rim joist are sealed up with spray foam. Basement slab is uninsulated and has thick plastic barrier between it and it’s rock base.
In the summer I run a 70 pint portable dehumidifier in the utility room set to target 50-55 RH. With the dehumidifier running in the past with the uninsulated basement, the basement has felt dry and of course cool. AC is used heavily during the Summer. We typically target a 74* temp on the main floor which equates to roughly 78* upstairs (central return on main floor). Summer basement temps are unknown as I have not monitored them in past summers. As part of the basement finishing I have added multiple air returns throughout the basement which are situated a few inches off the floor to help circulate air.
Resources I have read through:
Dew point and slab temperature
https://buildingscience.com/documents/bareports/ba-0309-renovating-your-basment/view
https://buildingscience.com/documents/information-sheets/basement-insulation
https://buildingscience.com/documents/insights/bsi-003-concrete-floor-problems (Moldy carpet, latex floor adhesives. Both slab on grade in warm climates.)
https://buildingscience.com/documents/insights/bsi-059-slab-happy
https://www.greenbuildingadvisor.com/blogs/dept/qa-spotlight/what-s-best-basement-flooring-system
https://www.greenbuildingadvisor.com/community/forum/energy-efficiency-and-durability/98936/adding-insulation-floor-vs-adding-insulation- (comment 7)
https://www.greenbuildingadvisor.com/blogs/dept/qa-spotlight/what-s-best-basement-flooring-system (comment 2)
GBA Detail Library
A collection of one thousand construction details organized by climate and house part
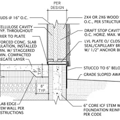
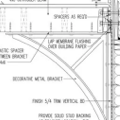
Replies
Bob,
Ideally, the rigid foam would have been installed under your slab at the time of construction. Since your builder didn't do that, you are in a tough position. You have to weigh the pluses and minuses of two imperfect paths: Raising the basement floor level with rigid foam, or dealing with the moisture and smell issues associated with a cold slab.
Aggressive dehumidification is one approach, of course, but it entails an energy penalty.
In short, there is no perfect solution. Once the house has been built without rigid foam under the slab, all solutions involve compromises.
Q. "Is insulating the top of a non-walkout basement slab floor in climate zone 6 really valuable if the slab has a moisture/vapor barrier beneath it?"
A. Yes. The polyethylene doesn't change the temperature of the first condensing surface (the top of the slab), so you still face the problem of condensation, mold, and funny odors.
Wintertime floor temp in socks is fine with a carpet on an uninsulated slab in zone 6, but in zone 6A (MN) the underside of the carpet risks dwelling below the summertime outdoor dew point, and getting mold issues.
Slab insulation is more about the "stinky basement smell" than it is about energy savings, though in zone 6 the lifecycle energy savings are still real enough. A tile floor won't have the same risks as carpet.
55% RH @ 75F air has a dew point of 58F. Deep subsoil temps in your area are in the mid-40s F.
https://www.builditsolar.com/Projects/Cooling/US-ground-temps.gif
With only ~R2 of carpet in a heated basement the summertime temperature of the slab and the bottom side of the carpet won't be in the mid-40s, but it'll probably be below 58F.
Fantastic, than you both. Moving forward with insulating the slab.
Is R4 (3/4" XPS) going to be enough to prevent condensation? I need to keep to close to 1.5" total height between the plywood/osb and XPS. 5/8" OSB is hard to find with tongue groove.
Is tongue and groove necessary if I am putting 6 tapcons into each sheet? Or maybe I am overthinking tapcons...and should use less and ensure that I have tongue and groove (may have to go 3/4").
For a not-too-shaggy carpet with a minimal-thickness carpet underlayment 3/4 of EPS (~R3, and MUCH greener than XPS) would be enough. If you're going full-plush pile with 1/2" of jute or foamy rubbery stuff for the full-on "padded room" feel under it it's maybe not quite enough.
Any XPS that gets put down needs to be derated to it's fully depleted R4.2/inch. That would make 3/4" XPS about R3.2 after a few decades. The climate-damaging HFC blowing agents give it a bit of performance boost for the first decade or so, but it's really lousy stuff from an environmental point of view.
EPS is the same polymer, but blown with hydrocarbons (usually pentane variants), which have very low global warming potential, most of which escapes the foam (and is recaptured) at the factory, and does not affect it's R-performance ratings. It's R-performance after 50 years will pretty much be the same as it was on day-1.
Thank you Dana.
Challenge with EPS is 10psi is what is available. My understanding is I should be putting at least 15psi down. Probably more so since I am likely going for the 19/32" (near 5/8") osb underlayment (fighting for headroom).
What's the magic with 10% deformation 15psi?
Even a half-inch subfloor would be distributing the weight over a much broader area, and a polka-party with a dozen 200lb Czechs dancing on it isn't going to take it anywhere near the elastic limits of 10 psi foam. The PITA aspect about using cheap Type-I foam is that you have to pay attention to the seams in the subfloor when installing the TapCons than with Type-II or denser foam. Screws can impart orders of magnitude more pressure (and more localized pressure) than even a 200lb break dancer doing handsprings, so you may have to adjust the torque on screws to keep the seams well leveled. The unevennes of a small rift would be masked by the carpet anyway.
Thank you everyone for your insight and encouragement. Slab is now insulated with 1" XPS with 5/8" tongue and groove OSB on top. Very happy I took the time to do this. The sub floor feel on the feet is nice. Both temperature (yes it is summer) and with the "softer" feel of the osb.
Should I use a silicone caulk around the perimeter of the rooms? What about at the joints of the OSB...should they be caulked also? Tongue and Groove OSB is designed to have a 1/16th+ space when tightly assembled.
Bob,
Unless you had air-leakage at the slab edges, there is no reason to caulk either the perimeter or the seams of the subfloor. It will make no difference to the amount of moisture that can dissipate though diffusion.
Another option for people in this position: tile floor, with carpet that's rolled out seasonally.