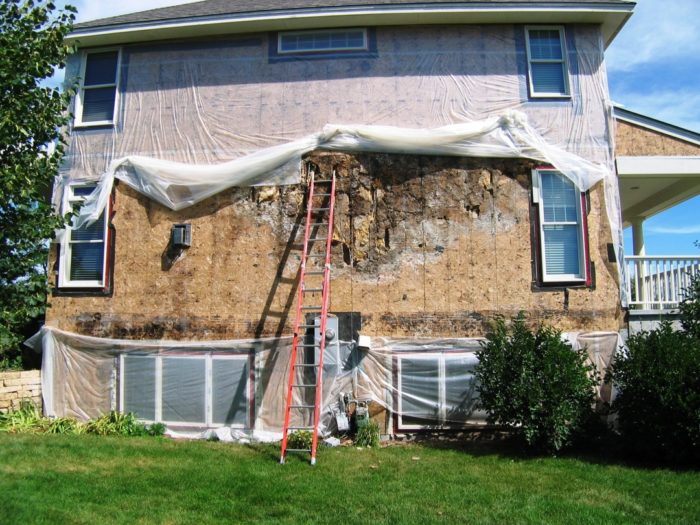
Image Credit: Images #1 and #2: Energy Design Update
In many areas of the country, hundreds of stucco-clad homes have suffered wall rot. Although building scientists are still researching the causes of wall rot behind stucco, it’s clear that all of these walls got wet and were unable to dry.
Among the reasons that have been proposed for the recent epidemic of stucco-clad homes with wall rot:
- Many of the houses had OSB sheathing, which is more susceptible to rot than plywood or board sheathing.
- Many of the houses had only one layer of Grade D paper or asphalt felt under the stucco rather than two.
- The homes lacked a ventilated air gap between the stucco and the sheathing.
- In many of the homes, interior polyethylene prevented the walls from drying to the interior.
- Many of the homes had flashing errors.
- Some of the homes had high indoor humidity coupled with an imperfect air barrier.
If you’re planning to install stucco on a wood-framed wall, you can benefit from the many lessons learned from all of the failed stucco installations of the last twenty years. Before we tackle the question of how to avoid such failures, however, let’s delve into some stories from the recent wall-rot plague.
A failure rate of 51%
I wrote a special report on rotting stucco-clad walls in Minnesota for the May 2006 issue of Energy Design Update. The article began, “In Minnesota, home inspectors have discovered that hundreds of recently built homes — especially stucco-clad homes — have rotting walls. In spite of years of efforts by construction experts to educate builders on improved water-management details, wet walls continue to take a staggering toll on builders and insurance companies.
“According to Ron Glubka, the chief building official in Woodbury, Minnesota, the city’s wet walls represent ‘the largest construction defect problem in local history.’ … Glubka…
Weekly Newsletter
Get building science and energy efficiency advice, plus special offers, in your inbox.
This article is only available to GBA Prime Members
Sign up for a free trial and get instant access to this article as well as GBA’s complete library of premium articles and construction details.
Start Free TrialAlready a member? Log in
72 Comments
Interesting Photo
Martin,
It looks to me like the "moisture" is coming from the interior.
Not from wet stucco
Notice there is almost no damage above each floor-line.
the first photo
my comment was about the first photo not the second
Response to John Brooks
John,
Your hunch about the house in the first photo may well be right, although I have learned over the years how difficult accurate diagnosis is without a site visit.
After interviewing a great many people for my report on the Minnesota problems, I came away convinced that there was no single smoking gun -- no single cause that explained all of the failures. In many homes, more than one factor contributed to the sheathing rot.
Stucco gets wet, like all types of siding. But stucco holds much more water than vinyl siding, and stucco dries slowly. Although you may be right that most of the moisture that damaged the OSB came from the interior, the stucco may have contributed the problem, since stucco slows drying.
Any time you have damp OSB, whether due to interior moisture accumulating during cold weather or due to flashing leaks or saturated siding, the most important thing you can do is encourage fast drying. That's why houses with vinyl siding have far fewer wet-wall problems than houses with stucco.
EIFS
Martin, we are using EIFS on one of our projects. Our contractor did install a drainage layer over our sheathing, and then applied the rigid foam. He also left a 1" gap around the edges of the foam. For example, over our front porch the EIFS does not run all the way down to the roof, instead there is a 1" gap between the foam and the porch roof. When I asked why he left a gap, he didn't give me a clear answer, just that it was how they always do it. Is it to allow ventilation? I'm concerned about water entering the wall system through those gaps and have been considering flashing those areas again. We are in the DC area and are using an R-3 SIS exterior wall.
Response to Vic
Vic,
I think it is appropriate to leave a 1" gap between the porch roof sheathing and the bottom of the foam sheathing on the wall above the porch.
My guess is that there is an air gap between the foam and the WRB. I hope that's what you mean by "drainage layer." If so, it's appropriate to have an air inlet at the bottom, to encourage ventilation drying.
3/8" actual or nominal?
Great article as usual Martin!
I notice that almost every drain gap manufacturer sells both a 3/8" thick version and also a thinner version, usually around 1/4".
Around our area (the DC area, Zone 4 with 4000 HDD and 1200 CDD) only the thinner material is typically available. When I've contacted the manufacturers, they say the 3/8" version is a Canadian spec that is not needed except in very cold climates. I noticed that all your examples are from places with about twice the HDD as we experience here. Do you suppose 1/4" is adequate in some parts of the country? Do you know of anywhere it has failed?
I would also like to add Masonry Technology ( http://www.mtidry.com ) to your list of suppliers. Their gap material is pretty neat, and they have useful accessories and good support to boot.
1/4 inch will work
Doug,
I wouldn't sweat the difference between 1/4 in. and 3/8 in., especially if you are finding it hard to locate products with a 3/8-inch gap. By including a 1/4-inch gap, you are providing a much better detail that the failing houses I mention in the blog.
in the older neighborhoods
There are many examples in my neck of Minnesota of older homes (1900-1930s) which had stucco placed over the original lap siding. I took some photos of one over-stuccoed home where the owners were tearing the stucco off to reside. The metal lathe on this home was applied right on the original wood siding (no building paper.) The original wood siding was in surprisingly good shape. (This same house had evidence of being filled with insulation from the outside before the over stuccoing.)
There are many over stuccoed homes in this area. You can tell because the stucco comes out past the window casings and a band of wood is typically applied on the casing to flush out with the stucco. Judging from the exterior these applications seemed to have been performing just fine over the years.
I always wonder why I don't see more evidence of rot where the stucco butts up to the old wood window casings. I would think the stucco drys slow enough where this intersection would have common recurring rot.
Response to J Chesnut
J Chesnut,
These are among the differences between older homes and homes built in the 1990s:
1. Older homes have board sheathing and wood lap siding, with no OSB.
2. Older homes never have interior polyethylene.
3. Because older stucco formulations never had additives that reduce the drying potential, older stucco dries faster than new stucco.
4. Older homes have less insulation than newer homes. If walls have less insulation, the stucco stays warmer and therefore dryer.
Just curious
Do these failures favor any particular orientation?
Response to Garth Sproule
Garth,
As far as I know, no. But I'd be happy to hear more failure stories from any readers who have some to share.
Failure Photos
Martin,
I would love to see a blog with lots of "failure photos" and or links to such photos and stories.
Manufactured Stone
I've repaired a few walls with the same problem that had manufactured stone. All had the same issues: No drainage plane, grading issues (in one case the grade was above the sill plate), flashing issues. Since manufactured stone gets applied essentially the same as stucco (lath and scratch coat), I always include a rain screen behind it.
It's just bumpy stucco
John Zito,
You are absolutely right -- the same catalog of problems occurs with adhered manufactured stone veneer. That's why John Straube and Joe Lstiburek call stone veneer "bumpy stucco."
@ J Chestnut: older stucco is
@ J Chestnut: older stucco is LIME and sand, with almost no portland. Old lime plasters allow water vapor to pass through. Portland does not. Modern stucco has too much Portland in it. Portland doesn't "get wet" so much as it traps moisture. Too much Portland is the problem. In the historic districts I work, when we take non-original Lime stucco off a house with original lap siding, the lap siding and board sheathing is in very good condition 9 out of 10 times.
Waterproof Your Stucco ****
Seems like it would be a LOT easier to merely waterproof a Portland Cement based stucco that has been properly applied, knowing full well there is no more moisture transfer in - out - or through your stucco. Then you can concentrate on the Real source of the moisture that is causing these problems.
Rotting substrate that is getting wet won't be blamed on a waterproofed stucco material. You'll then be looking for other points of entry that breach the stucco cladding through penetrations other than the stucco surface itself.
A wind driven event will put enough water through a wall surface at an improperly sealed window or other opening to drench OSB and watch it explode! Enough moisture and time will swell the OSB to give the appearance that the stucco is falling off. In actuality, you have a substrate that will not support a stucco finish because it is wet and not suitable to have had the stucco put on it in the first place!
Easy to waterproof the stucco, the bigger challenge is to eliminate other sources of moisture from getting behind the stucco to compromise a material that your Hoping will qualify as a adequate substrate to begin with!
sheathing rot
lets see here.... we now apply plastic to the interior walls. do you really think the old timers waterproofed a wall much better than the current workers? they did not install window sill pans. usually one layer of felt. usually short overhangs. how much heating energy could these homeowners have puchased for the price of the fix its that also aren't working because the vapor barrier is still there. also during the 90's we found out the need for and developed elatomeric paint for stucco as the housing style was short overhangs.
Stucco Rainscreen Using Furring Strips?
Thanks for the informative article Martin. You note several drainage mat solutions for creating a rainscreen behind stucco, but I'm considering using furring strips (vertical) instead. I've seen this done for stucco, and would prefer it, but am wondering if the lack of a substrate behind the mesh will cause problems for the stucco (3 part/traditional stucco). Can you share any information and/or details for this?
Response to Glenn Summers
Glenn Summers,
I agree with you that the inherent problems of OSB are a significant element in these wall failures. However, I strongly disagree that "waterproofing" stucco makes a wall more robust. There is plenty of evidence that such waterproofing makes the situation worse.
Waterproofing -- achieved by using additives in the stucco mix or by applying a waterproofing coating to cured stucco -- is a way to reduce the tendency of the stucco to absorb water when it rains. But waterproofing also reduces the ability of the wall to dry to the exterior. As a result, once the wall gets wet, the water is trapped.
Old fashioned stuccos, whether lime-based stuccos or Portland-cement-based stuccos, dry quickly when the sun comes out or a breeze is blowing. Modern stucco mixtures with waterproofing additives dry very slowly, if at all.
There are many ways that water can saturate OSB. It can leak into the wall around windows, as you point out. It can also originate in the home's interior, piggybacking on exfiltrating air. Once the OSB is wet, you definitely want it to dry quickly -- which means you don't want waterproofed stucco.
Response to Greg
Greg,
You wrote, "Do you really think the old timers waterproofed a wall much better than the current workers?"
No, I don't. Old-fashioned walls were often leaky. However, these walls dried quickly. As long as the wall's drying potential exceeded the annual wetting, the walls did not fail.
You also wrote, "During the 90's we found out the need for and developed elastomeric paint for stucco as the housing style was short overhangs."
I don't believe that modern stucco formulations or elastomeric paint are a good substitute for skimpy roof overhangs. As I explained in my answer to Glenn Summers, elastomeric coatings just slow down drying, and that's not what you want.
Response to Keyan Mizani
Keyan Mizani,
You can definitely install stucco on top of furring strips. In my article, I suggested the technique:
"If you’re installing stucco over foam, here’s how to create a ventilated rainscreen gap:
* Install 1x3 or 1x4 vertical strapping on top of the foam, screwed through the foam into the studs.
* Fasten paper-backed metal lath to the strapping, and proceed with a standard installation of three-coat stucco."
For many decades in California, stucco was installed directly over the studs, without any sheathing whatsoever. Asphalt felt, then metal lath, then stucco -- that was all.
These days, it makes more sense to start with wall sheathing: rigid foam, diagonal boards, or plywood. Then feel free to install vertical strapping and stucco.
Hi Martin, I've been reading up and trying to learn as much as I can about building the best possible building envelope (searching articles here, reading Pretty Good House, etc.), but most of the information is focused on colder climates than here in Southern California. We're renovating a house in Los Angeles built in 1938, and I'm convinced the only reason its still standing is because it was so leaky (had/has just about every issue you can think of when it comes to waterproofing and drainage).. It has standard 2x4 walls and we plan to recess the windows (do an "innie" installation) with a stucco finish so I've been asking installers about continuous exterior insulation and they just look at me with a blank face. I'm sure there's a lot of carryover but I am having a tough time figuring out whats overkill and what might actually cause problems in our climate. Do any articles or books come to mind that focus more on best practices here in CA? Thanks for your help,
Curtis
Curtis,
California is a big state, with a great many climates, so it's hard to generalize. In your area (Los Angeles), energy bills for heating and cooling are relatively low, so it's no surprise to learn that few builders bother with continuous exterior insulation. The reductions in energy use attributable to such insulation are too low to justify the investment.
Perhaps some GBA readers will suggest the names of books or articles that are relevant to your climate.
Curtis,
You will find more information if you search for EIFS. EIFS (Exterior Insulation and Finish System) became popular in the 1980's due primarily to its ease of installation and quick completion compared to traditional 3-coat stucco. The insulation was almost secondary in most projects. Without a long-winded lecture, EIFS and stucco are parts of a continuum of products, with the chief difference between "EIFS" and "stucco" being that the finish coatings in EIFS consist of primarily polymer with some cement stucco mixed in for ruggedness and texture. 3-coat stucco is primarily cement stucco with a little bit of polymer (usually) mixed in for flexibility and consistency.
In sunny So Cal, you can use any of these products successfully. It is entirely acceptable to install 3-coat stucco over insulation and there are some systems that use the acrylic finishes from EIFS directly over cement board or gypsum sheathing. Any contractors who routinely install "EIFS" and "stucco" would be able to install the "stucco" part over continuous insulation. As with most claddings, the devil is in the details. You will find lost of installation details at the system manufacturers websites. Sto (www.stocorp.com) is one of the larger companies and has extensive detail libraries for their finishes. You especially want to focus on "drainable" or "water managed" system details, as these all have the ability to drain water from behind the system to the exterior.
That said, your climate is very stucco-friendly. With only about 19" of rain a year, you are nearly in a desert climate. Nearly any moisture details will work.
stucco over other than wood framed walls
I'm designing a house using AAC block and intending to cover it with 1" to 2" rigid foam and then stucco over it. Would you recommend a drainage plane either under the rigid or on top of strapping? Or is this necessary at all with the AAC as the wall?
Response to Joseph
Joseph,
The wall assembly you describe is robust and is not subject to rot, so I don't think you need an air gap under your stucco. Just be sure that you have good fastening details for your rigid foam and your stucco lath.
Stucco issues
If you substituted marine ply for OSB would this help?
Response to Anonymous
Anonymous,
Many studies have shown that plywood responds much better than OSB to repeated cycles of wetting and drying. Plywood is more robust and durable than OSB.
I'm not familiar with the properties of marine plywood, except that I assume it is expensive. I imagine that few builders or homeowners are able to afford to build their homes from boat-building materials. I imagine that other solutions are more affordable.
protecting existing stucco
Quite an interesting...and scary article.
My question is: What can a homeowner do to prevent rot to an existing stucco home. My house was built 12 years ago and stuccoed using the one coat method of 1/2 inch Portland cement substrate topped with a synthetic stucco product. The walls is a 2x6 filled with faced fiberglass but no polyethylene. Thankfully, the sheathing is 1/2 inch CDX and not OSB. No special admixtures (latex, fibers) were put in the substrate. And only one layer of asphalt paper was installed. In one room I've noticed that water must be getting behind the stucco because the mdf baseboard has swollen in places. I thought that it must be coming around the windows so I renewed the caulking even though it looked to be in pretty good shape. There are a few cracks in the stucco field but I didn't think these to be a problem since the building paper should prevent water entry. After reading the article, I'm now having serious second thoughts.
Besides caulking all cracks is there something else I can do to ensure the maximum longevity for the stucco? I live in Missouri where I get about 45 inches of rain per year (and lots of humidity).
Response to Paul Marshall
Paul Marshall,
You wrote, "In one room I've noticed that water must be getting behind the stucco because the MDF baseboard has swollen in places."
You have no choice but to open up the wall behind the swollen MDF. Most homeowners find it is easier to open up the wall from the interior, but you could also open up the wall from the exterior.
If your windows were poorly flashed -- for example, if there is no pan flashing on your rough sills -- and if water is leaking in at your windows, you really have no choice but to remove your windows are do the job right.
I would start with the windows that are most exposed to the weather.
Before you jump to any conclusions, however, you much do a thorough investigation to be sure you have properly diagnosed the source of the moisture. This takes a home performance contractor or a home inspector with wide experience, building science knowledge, and a good brain. In many parts of the country, it's hard to find people like that.
Good luck.
One more thought for Paul Marshall
Paul,
Installing stucco over only a single layer of asphalt felt is probably a code violation and is certainly a violation of best practices in the industry. That means that it's possible that the contractor who installed your stucco is liable for damages to your house, so you may want to talk to a lawyer familiar with construction defect cases.
Thanks for the advise
I was afraid of that (having to open up wall). I'm sure there is a rather nice mold culture thriving there that needs to be dealt with even if the sheathing is sound. The only wall that shows any leakage is an east wall that doesn't show problems unless the rain is coming from that direction, which is about 10% of the time. This leads me to believe it is not due to the porous nature of stucco but to free water that is penetrating cracks. I guess I put too much faith in the asphalt paper and should assume it to be essentially worthless. Is it a safe conclusion that making sure the cracks are well sealed should be the line of first defense?
The windows are well flashed at the top, but at the bottom the only protection is the asphalt felt. The mdf baseboard is swollen at one of the windows and at a spot about halfway between the two windows in the room. In fact, I noticed last summer that a picture that was hanging right between the 5 ft space between the windows was discolored behind the glass. It was not wet but I theorized that water vapor had moved through the wall and then through the picture back. This could indicate the cracks in the field are contributing to the problem. I'm sure it will all be obvious when the wall comes off.
Unfortunately, I doubt there is any legal recourse. I didn't watch the contractor that closely when he installed the building paper, but it seemed like it was only one layer. My bad memory is not the only problem however. It's quite possible that contractor is now deceased as he was getting up in years, but my biggest problem is that at the time the house was built, there was no code in my county. I designed the house in conformance with the extant UBC at the time, but left the stucco details to the contractor as I trusted him as a professional.
This sounds like a warm weather project where I can leave the walls open for a couple of rain events to see where the problem is. If the sheathing is still sound and I'm able to stop the leaking from the inside is there a product I can coat the exterior with that will help repel the water? Or would you even recommend that?
Thanks for all your help.
Forget caulks and coatings
Paul,
Forget caulks and coatings. You're barking up the wrong tree there.
Open up your wall on the inside, and get a friend to spray the wall and the window with a garden hose. You don't have to wait for rain.
how to match (E) stucco
Thanks for the article.
You mentioned that often a 2nd or 3rd rebuild is still done wrong.
Do you have any advice on how to patch stucco in a remodel situation? For instance, where you are extending an existing stucco wall that never had a drainage material in it? How to deal with the added thickness of the rainscreen?
If a typical 3-coat system is 7/8" thick, what do you find to be the added thickness of a 3-coat system with a rainscreen layer once the whole 3-coal system is completed?
Response to Anonymous
Anonymous,
Q. "Do you have any advice on how to patch stucco in a remodel situation?"
A. Here's a good article from JLC:
http://www.jlconline.com/cgi-bin/jlconline.storefront/4cf69cb80973a9cf27170a32100a06aa/Product/View/9709patc
Q. "How to deal with the added thickness of the rainscreen?"
A. If you intend to rebuild a portion of a wall with a rainscreen, while leaving an adjacent portion of the wall without a rainscreen, there will be no way to disguise the transition. You will have a bump. Finish the bump with your choice of trim board.
Q. "If a typical 3-coat system is 7/8" thick, what do you find to be the added thickness of a 3-coat system with a rainscreen layer once the whole 3-coat system is completed?"
A. If you include a rainscreen gap, then the depth of the gap represents the added thickness of your system. In general, most rainscreen gaps vary from 3/8 in. to 1 in.
3 part stucco application to residential bldg The Falcon Theo
I have applied 3 part stucco to my two story with suscess over 5 years ago. I have studied the issue and here is a few suggestions.
1. Consider the sheathing: 1/2 " plywood is he best use 5/8" if you can afford it. If you choose to use OSB, do not apply it within 2 feet of window and door openings or 4 feet from the bldg. corners. Instead, use plywood. This is a critical issue to the strength and indurance of your bldg.
2. Wrap your bldg with a fiber web based bldg house wrap. Do not use the continious film type here. That paper will cause issues by trapping moisture in the walls from the interior sources.
3. Cover the house with 1/2 to 1 1/2 " extruded polystrene foam board. A product like Owen's Corning is excellent. Prior to, furr out the boards to 1/4 to 3/8 gaps from the walls. I suggest a 1/4" Owen's Corning Fan Fold strips (1 1/2") will do. No need to go and buy lumber for this, keep it simple.
4. Cover the foam board with 30 lb building paper. The heck with kraft D paper. It should be outlawed, scrapped and buried and sprinkled with iron so that it does not come back. After covering with 30 lb building paper coat the paper with black asphalt foundation or roof grade moisture barrier. This will make the paper 100 lb or better and you can make more than one application. This coat when cured will survive direct element exposure 10 year after application, so you will have plenty of time to finish your bldg.
5. Apply your self furring lathe. Do not use none the furring lathe, your are asking for trouble if you do that. The self furring lathe will channel and drain water better. However, you must apply weep screeds and proper flashing with this lathe in order for it to work properly. The application of the lathe is a art and individuals will vary in their mehod. I choose to be traditional and adherent o the old school of live and learn. I will say that it is extremely important that one flashes windows, door and corners properly.
6. Last, the type of finish coat is important. I use a hand trowel smooth with a faux texure o creat shadows. I feel that it is the best way, you may not agree. However, I find it easy to water proof the stucco with a smooth finish. By the way, If you don't want rain water adsorpion coa you finished walls with a sealer, use the industrial srength mixtures. Semi gloss works well.
I hope that this helps. If you want more info concerning my study and results including pictures contact me here and I will respond.
Note: a bone to pick with the bone heads: Stucco 3 parts should be 2 parts portland and 1 part masonary cement. You can increase the masonary cement to increase flow and adhesion. One shold be concerned with the aggregates, in your first coat use concrete sand and in subsequent coats use mason sand. You won't regret it.
how should that building wrap lap?
Building a house and the stucco sub is putting on two layers of building paper (Super JumboTex); however, I'm concerned about how he's lapping the paper. Rather than lapping each layer independently to create a drainage plane between the two layers, he's lapping the upper two layers over the bottom two layers. By my eyes, if the stucco bonds, he's created truncated drainage planes. He disagrees.
I've pointed him to R703.6.3 of the International Residential Code which suggests that each layer lap itself, but he says that doesn't apply to our case because we have the Zip System underneath it all.
I find lots of posts about using two layers of building paper but very little about how the layers should lap.
How should that building wrap lap?
Response to Robert Mace
Robert,
I think that your proposed lapping method is better than the contractor's lapping method.
However, as my article makes clear, the key element of a long-lived stucco installation is the air gap between the stucco and the sheathing. If you don't include an air gap, no amount of lapping will be enough to let you sleep well at night.
EIFS
I am wondering if it is still necessary to have a drainage plane behind the rigid foam layer of an EIFS system if the the foam is designed to be thick enough to prevent the dew point from reaching the exterior sheathing(For my project in Climate zone 6 this would be R-11.5). This is assuming that the exterior flashing details are correct. I am also planning to use plywood sheathing, no interior vapor barrier and an HRV to control interior moisture.
Also, If you use foam with the a pre-manufactured drainage plane don't you loose any added R-Value that could be gain by the added foam layer.
Response to Damian Mast
Damian,
If you are specifying EIFS, the system (a) should be installed by an EIFS contractor who has been trained and certified by the EIFS system manufacturer, and (b) every detail of the system should exactly follow the recommendations of the EIFS manufacturer (for example, Sto Corp.).
That way, if something goes wrong, you call negotiate with Sto's insurance company.
rainscreen behind stucco & brick
I am doing a remodel & 2nd floor addition and live in zone 3 (Oakland Ca. area). The first floor exterior walls will have stucco with brick pilaster corners. The walls will be 2x6 with dense pack cellulose and an inch of rigid on the exterior. If there is 1/2" of plywood then the polyiso and the vertical strapping is there need for any wrb anywhere? What vertical strapping do you suggest behind both the brick (old clinker bricks) and 3 part stucco? I plan on sealing the foam seams with dow weathermate ,should I place two 1/2" layers of foam to stagger the seams? Can I tape the plywood seams with dow weathermate or should I use 3m all weather? Thank You.
Response to Marsha Broquedis
Marsha,
Q. "If there is 1/2 inch of plywood then the polyiso and the vertical strapping, is there need for any WRB anywhere?"
A. Every wall needs a WRB. In fact, a WRB is required by code. The WRB can be housewrap, rigid foam, or one of several other materials. For more information, see:
All About Water-Resistive Barriers
Using Rigid Foam As a Water-Resistive Barrier
Q. "What vertical strapping do you suggest behind both the brick (old clinker bricks) and 3-part stucco?"
A. You don't need any strapping behind brick. If your mason is suggesting the use of vertical strapping behind bricks, I would choose another mason. If you want to have an air gap between your stucco and the rigid foam, use vertical 1x4 strapping screwed through the rigid foam into the studs. Then fasten paper-backed metal lath to the strapping.
Q. "I plan on sealing the foam seams with Dow Weathermate. Should I place two 1/2-inch layers of foam to stagger the seams?"
A. Two layers of rigid foam with staggered seams are always preferable to a single layer of rigid foam.
Q. "Can I tape the plywood seams with Dow Weathermate or should I use 3M All Weather?"
A. When I tested a variety of tapes on plywood, Dow Weathermate failed the test, while 3M All Weather was one of the winners. More information here: Backyard Tape Test.
moiture barier and codes and location
On the one hand this problem of moisture barier and mold has created employment in the repair construction industry. Thats good. However i am hoping each state will create laws allowing home builders to choose to aliminate the inside plastic moisture barier which traps moisture. Any home built in a wet season or frozen ice on stud will be traped. This is certainly true with vinyl sideing and most likely a factor in stuco applications.
Also most rural areas and small towns do not have these codes and allow the builder to decide. One idea is for the lumber industry to treat the lumber with a mold preventitive treatment. Or sealant. My guess is its already been invented but like so many great ideas are blocked by a stuborn political and industry that work hand and hand for there own benifit.
Black mold is dangerus and has killed people and causes many illnesses. Its not to be used to profit from.
Same is true for fiberglass insulation which has been proven to be less insulating qith moisture in it.
Response to Patrick Lymard
Patrick,
Vinyl siding does not trap moisture. In fact, of all the common types of siding, vinyl siding is probably the best ventilated, and most likely to encourage drying to the exterior. Vinyl siding is far less likely to trap moisture in a wall than stucco.
Stucco drainage details
Great article, have read it many times over. I am considering stucco/EIFS exterior finish for a new home construction (wall assembly being debated for, cost, thermal performance, durability etc..), in the event of 2x6 stick framing with a plywood exterior wall, I get the detail described for all the good reasons you point out. However, in the event of an ICF wall, no drainage plane is needed correct? I've looked at some sources, have yet to consult a local EIFS contractor:
http://www.stucoflex.com/wall_assembies.htm
http://www.icfmag.com/how-to/ht_great_stucco.html
It seems the thinner, elastomeric EIFS system goes right over the ICF (after a base coat, screen and case coat) is directly applied as the wall is not considered to "breathe", (http://www.cement.org/stucco/faq_icf.asp). You agree? If so, the lower cost to finish an ICF wall should be considered as part of the "wall cost" since a plywood wall would need the requisite moisture gap and application system to put it together whereas with ICF it ready to apply.
Thanks
Response to Sal Lombardo
Sal,
You are correct that when EIFS (synthetic stucco) is applied over ICFs, you don't need an air gap between the synthetic stucco and the EPS foam. Of course, your EIFS contractor is the one providing the warranty -- so the installation must follow all of the recommendations of the EIFS manufacturer, and you shouldn't attempt to direct the EIFS contractor concerning installation details.
Another subdivision plagued by stucco failure
Here is a link to an online news article about a residential subdivision in Ottawa with houses that are less than 10 years old -- houses with leaking stucco and rot.
Repairs to these houses are costing between $25,000 and $40,000 per house. The only people who are happy are the lawyers: Stucco leaves Ottawa homeowners stuck with repair bills.
[Thanks to Andrew Henry for letting me know about this particular cluster of failures.]
stucco and airgap question
Thanks for the article. I have a question I cant seem to find the answer too.I am remodeling my house down to the studs. Put In cellulose insulation and OSB. Going with stucco on bottom half. I forked out the bucks and bought Homeslicker stone and stuccoto to create a 1/4 inch air gap. We have installed standard tyvek on the OSB and have the home slicker stone and stucco over it. So my big question is do we need another layer of felt down on the outside of the homeslicker or is the layer of stucco blocking fabric that comes with the product good enough ?
To be more explicit. Code requires two layers of felt due to the fact that stucco binds to the first layer leaving the second an intact weather barrier. Is this kind of protection needed with homeslicker stone and stucco product? Would adding a layer of felt on the outside of the homeslicker air gap creat some kind of unintended consequences?
Response to Joel Kauffman
Joel,
There are really three questions here:
1. What does the manufacturer of Home Slicker Stone and Stucco require?
2. What will your local building inspector require?
3. How much risk are you willing to accept?
For the answer to question 1, see this document: Home Slicker Stone and Stucco Installation Instructions. That document recommends that lath and stucco can be installed on top of the product in question, as long as there is a WRB between the wall sheathing and the Home Slicker. (See illustration below.)
For the answer to question 2, contact your local building department. Your inspector may want to see an additional layer of building paper or asphalt felt on the exterior side of the Home Slicker Stone and Stucco, because the wording of the building code gives your inspector that latitude.
The answer to question 3 is hard to pin down. However, after researching stucco failures, which are very common, I would include a layer of asphalt felt (or use paper-backed lath) on the exterior side of the Home Slicker product if I were building a home with stucco. Asphalt felt is cheap, and the insurance is worth it.
.
follow up question about home slicker
That all makes sense. I was just worried about creating some kind of unanticipated problem by having a 1/4 inch air gap with WRB on both sides. Is there any concern in that regards as felt and tyvek has different permeability properties. The felt inside of the stucco would not be flashed so lots of water would be entering the air gap.
Second response to Joel Kauffman
Joel,
Q. "I was just worried about creating some kind of unanticipated problem by having a 1/4 inch air gap with WRB on both sides. Is there any concern in that regards as felt and Tyvek has different permeability properties. The felt inside of the stucco would not be flashed so lots of water would be entering the air gap."
A. Installing one or two layers of asphalt felt on the exterior side of the air gap will not cause any problems, even if there is a WRB on the interior side of the air gap.
That said, flashing details are crucial, and must be carefully thought out. I'm not sure why you anticipate that "lots of water will be entering the air gap." Hopefully, your meticulous flashing plan will prevent that.
Leak on top of lower sliding door
We have a west facing stucco covered wall that has had recurring leaks. That side of the house is two stories, with a deck and ledger hanging off the second floor. The second floor has two sliding glass doors and a window, the bottom has a large sliding glass door beneath the deck. When the deck was rebuilt two years ago, extensive dry root was found on the ledger and it was determined the ledger was never flashed correctly. As a result, the entire lower wall was rebuilt (temporary wall built to support the upper floor, lower wall removed completely, and then rebuilt from scratch). Two layers of 60 minute paper were used on the new lower section of wall that was built, but since they did not touch the upper section of the wall, they just shoved the new paper as far up as they could behind the existing stucco. The inspector signed off on this.
Water leaked the next year on top of the lower sliding door during heavy rain. We then had all of the sliding doors and windows replaced on that side of the house since they were all retrofit. We had them replaced with new construction, so enough stucco had to be removed to do the install, and then stucco patches were applied.
We still have water leaking on top of the lower sliding door during heavy rain. I found one leak on the roof, which allowed water to slide all the way down the wall, which has since been repaired, but the leak remains (though diminished).
So my question is, at the bottom of the wall where it meets the ground, there is a weep screed for drainage. I can see this and it is not below the soil. However, the lower sliding door poses a barrier to the downward flow of water, yet I do not see any drainage plane for how water exits the wall if it has penetrated through the stucco above and is flowing downward. The lower sliding door has no visible metal flashing above it, the stucco just extends right to the edge of the door on the outside. It all passed inspection, but any thoughts on where to go from here are appreciated.
Should we redo the stucco and paper on that entire side of the house? Only above the lower sliding door to add some drainage above it? Is it normal to have enough water soak through stucco that it can pool above a door without proper drainage and eventually leak onto the floor?
stucco failure images - bulging of stucco walls
Great post, thank you! Is it common or possible that a stucco wall that is bluging by about 2 inches(and cracking) is caused by an improperly secured metal lathe or would you suspect wet OSB to bulge that much?
[Editor's note: The read an answer to this question, and to read other comments, advance to Page 2 by clicking on the "2" below. ]
https://isthisgoodorwhat.files.wordpress.com/2015/07/location1.jpg
https://isthisgoodorwhat.files.wordpress.com/2015/07/location2.jpg
https://isthisgoodorwhat.files.wordpress.com/2015/07/location3.jpg
.
Response to Adrian Jo
Adrian,
It's impossible to determine what's going on without a site visit. I can make some guesses, but they are just guesses.
In any case, if you have stucco that is bulging out 2 inches and cracking, someone is going to need to remove a section of stucco to investigate and repair the problem. Once the damaged area of stucco is removed, you will be able to see what's going on.
Here are my guesses:
1. In Photo #1, ineffective kickout flashing on the roof above the problem area is somehow allowing water to enter the wall. If my guess is correct, the solution will involve flashing corrections.
2. In Photo #2, the mold on the wall is due to spashback from the nearby roof. The splashback occurs when water from the higher roof dumps water onto the lower roof. There may be nothing wrong with the stucco here.
3. In Photo #3, the mold on the stucco and damage to the window casing is due to splashback from the nearby roof. Again, the splashback occurs when water from the higher roof dumps water onto the lower roof. One possible solution to this problem (and the problem shown in Photo #2) is to install a gutter on the higher roof.
One other thing I noticed: the soffit vents are all dark. This probably indicates that you live in a dusty area, or an area with polluted air.
plaster, lath, studs, boards, tar paper, 1923 stucco ....
We bought a 1923 stucco bungalow 20 years ago. It came with many layers of old paint under a locally made "waterproof" paint loaded with mica flakes that we were warned would have to be removed once it started to peel (no way to re-adhere it). We got that done properly, including removing the underlying paint down to the original stucco. (Wet hot grit blastng, suction through filters -- the residue was so high in lead it had to be trucked to Nevada for burial -- the bottom layer of paint was upwards of 20 percent lead, apparently the standard in the 1920s.) Expensive, precautionary, glad we did it.
Now, with a 1923 stucco over tar paper -- the question is, what next? Had many of the walls open to install new plumbing, no sign of rot, tar paper surprisingly intact but for screw and bolt holes here and there. One honeybee nest in one wall. House was heated constantly by the previous owners, several generations all elderly (they didn't have a pilot light on their gas heater, it just ran all the time, so the house stayed dry.)
Now what?
Advice is split between regular sulfate stucco and then paint it, or carbonate stucco with a smooth surface that will dry readily.
Response to H.R.
H.R.,
We need more information.
1. What is your location or climate zone?
2. Do you plan to install any insulation between the studs? If so, what type of insulation?
3. Are the windows in good shape? Do you plan to replace any of the windows?
4. Does the building have generous roof overhangs or stingy roof overhangs?
SF Bay area.Windows are in
SF Bay area.
Windows are in good shape, some have been replaced with double-pane; old ones kept rainproof by a reliable local painter who does touch-up. Plastic heatshrink film we put up inside the old windows during the winter prevents condensation.
Roof overhang about 15 inches
Stud insulation? not easy -- lots of fire blocks and X-bracing in the walls (as we know from those we've opened up for plumbing -- those, we replaced lath and plaster with plywood screwed and anchored to become shearwall). I've read that blow-in settles leaving gaps on this old construction.
A longtime contractor friend says in this area in old construction, air circulation in the stud bays prevents moisture from condensing inside the walls. He's seen old houses here get rot in the walls within a few years after people put insulation in stud bays, and patch and paint their stucco with vapor barrier acrylic paint, a big mistake apparently since otherwise stucco here dries itself pretty quickly. (That's why we're looking into calcium carbonate stucco without the slow-drying additive)
Proper bathroom and kitchen moisture removal fans, by the way.
But see the note I put in the roofing section -- moisture under a new cool roof is being handled by a dehumidifier in the attic.
We could probably replace the old gas heater with a dehumidifier in the living space -- cutting the humidity is effectively making the living space warmer. Around here high humidity in cold weather pulls heat right off you.
Response to H.R.
H.R.,
It sounds like you have made up your mind not to insulate. I'm not going to try to convince you otherwise.
But your question is rather vague: "Now what?"
I don't know. You could go out for ice cream if you're all done. You tell me.
Seriously, if you don't want to insulate, your walls are likely to stay pretty dry. Just talk to a stucco contractor and have the exterior finished in stucco if that's what you like.
Most water-entry problems are due to rain, so you need to make sure that your window rough openings are well flashed. In most older homes, they aren't.
Your method of avoiding water entry problems -- "old windows are kept rainproof by a reliable local painter who does touch-up" -- is a faith-based method. Trust me -- you can't depend on paint to keep your windows rainproof.
Siding over stucco
Thanks for all of the excellent advice in this article and responses to others.
I have a client in central Vermont that has a house built in 1981 with a stucco first floor exterior. The existing wall construction for the first floor from interior to exterior is: 1/2" gypsum, 2x6 wood stud with batt insul. infill, 1/2" PB (which I'm assuming is really OSB) and wire lath & plaster. There is no mention of building paper or any other WRB in the wall detail, but I can't imagine that they didn't use it.
The client would like to cover over the stucco with a wood siding. They're leaning towards horizontal reverse board and batten. I've been scouring the internet for concerns with siding over stucco and wonder if you could offer your advice? My inclination is to install vertical 1x furring secured to the studs, then run the 1/2" thick horizontal battens with the outer boards over those. I would leave a slight gap at the top of the siding to allow air to pass between the vertical furring, and a gap below with bug screen. It seems as though this would work fine to keep air movement over the existing stucco and allow the new siding to breath as well. The other option would be to only attach vertical furring and then have horizontal boards with a 1/8" gap between them for a shadow line, eliminating the horizontal battens completely. This seems like it would offer the best air circulation between the new siding and the exist. stucco, however I'm concerned about the insect/hive building potential between the two.
Any thoughts would be appreciated.
Response to Jennifer Lane
Jennifer,
There are lots of issues here. How much to delve into the issues depends on the owner's expectations and budget.
1. Is the sheathing sound? Or is there sheathing rot? Lots of stucco walls have rot. If you want to explore a little, start by looking under the lower corners of windows.
2. Where's the WRB? If you don't know, it's time to install one.
3. What about the windows? Extending the plane of the siding will require new window jamb extensions and a window flashing plan. This can range from a quickie job using caulk (not recommended) to a conscientious job that involves removing and reinstalling each window.
4. Is horizontal reverse-board-and-batten a good idea? Water will sit on the horizontal siding seams. This is a recipe for rot.
As I said, there are lots of issues here.
Siding over stucco
Martin,
Yes, issues abound, I realize.
1. I have to discuss and dig around a bit more with the client to find out about any issues they might be having with the existing wall construction. I'll suggest we do a little exploring before we get much farther along.
2. If we can't determine if there is a WRB in the existing construction, it doesn't seem correct to add one over the existing stucco...even if we did install a rainscreen layer between the stucco and new WRB and then another over the WRB...is this correct? That leaves us with removing the existing stucco (windows too) and starting from there.
3. One thought I had was to hold the new siding away from the perimeter of the existing window returns, leaving essentially a picture frame of existing stucco. There wouldn't be a way to flash this, but if I keep an air circulation layer behind the siding would this be enough to allow the water that infiltrates to dry? Tricky detail.
4. They've seen it installed before (in images) and liked the look of the horizontal boards but are wanting a more modern look than clapboards. I suppose you could bevel the top of each board slightly to allow for some run off.
5. My main concern is whether adding any sort of wood (or other material for that matter) directly to the stucco (for instance, the vertical furring I mentioned) would hold enough moisture against the existing stucco that it wouldn't be able to dry out, even with sufficient air space behind the siding itself.
If they went with the scenario of only using vertical furring and horizontal boards (no battens) with an air space, that seems like it would increase air circulation, but it would also allow more water infiltration.
They're intent on covering over this stucco.
Thanks
Response to Jennifer Lane
Jennifer,
It's better to install a WRB over the existing stucco than it is to cross your fingers and hope there is a WRB somewhere.
In any case, it's a good idea to install a WRB -- so that you have a layer that you can tie your flashing into.
If the clients want horizontal boards, it's up to them -- but if I were doing the installation, I would probably ask them to sign a disclaimer -- "The clients acknowledge that they have chosen a siding that is contrary to the builder's advice, and the builder is not responsible for disappointing siding performance..."
If you include a vented rainscreen between the existing stucco and the new siding, I wouldn't worry about moisture. But you need to work out the window flashing details.
After reading this and other articles about ventilated rain screens behind the stucco, I definitely buy into the idea. But do you need one in coastal California where rainfall and humidity are pretty low. I'm considering it for the stucco areas of my home (mainly the garage) and it just doesn't seem necessary. The areas will be non-conditioned spaces with no plastic sheeting on the inside. Delta-Dry and other systems seem great but not needed for my project. What do you think?
Jay,
I think that you are probably correct that stucco on an unconditioned garage in California doesn't necessarily need a rainscreen gap.
Remember, though, that flashing details and water-management details are always important, with every stucco job. Any time that stucco is installed over OSB sheathing (instead of over stone-and-mortar, brick-and-mortar, or CMU-and-mortar), flashing details have to be close to perfect if you want the job to be durable.
There needs to be some sort of capillary break between the stucco and sheathing, since stucco adsorbs dew, and wicks & stores moisture. An air gap is a pretty cheap & effective capillary break.
If there is no wood sheathing (just stucco on metal lath, and let-in bracing on the walls) and the stud bays are open that's not an issue- the whole garage is the air gap.
Jay,
Needless to say, I am assuming that you will be in compliance with building codes -- codes which require, at a minimum, two WRB layers (for example, asphalt felt or building paper) under stucco.
Martin, Dana,
Thanks for the responses. Yes, I'm using a fluid-applied WRB on the plywood (not OSB) and putting an additional 2 layers of building paper behind the stucco.
“[Deleted]”
Hi Martin, why in the GBA library there is no air gap suggested with stucco?
Cococchio,
When I was hired as a GBA employee in November 2008, the detail drawings were already created. I didn't have any input into these details.
That said, it looks to me as if the GBA detail drawings recommend the use of rigid foam sheathing under stucco rather than the use of OSB sheathing under stucco. (See, for example, this detail.) Using rigid foam sheathing under stucco rather than OSB sheathing goes a long way to preventing the sheathing rot problems that have plagued stucco installations in damp climates.
Regardless of the details shown in the drawings found in the GBA library, I still recommend inclusion of an air gap between stucco and wall sheathing.
Thank you for the clarification Martin
I believe the the use of a grooved rigid insulation board is normal for the application that Martin is speaking about (see https://www.buildingscience.com/sites/default/files/migrate/jpg/2014_HighR_wall_08_web.jpg)
It facilitates a sort of rain screen behind the insulation.
Log in or become a member to post a comment.
Sign up Log in