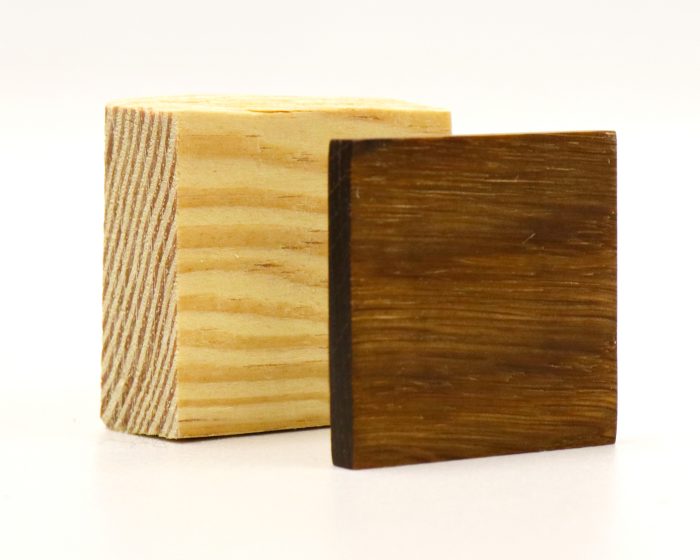
We have a complicated relationship with wood. For starters, industries ranging from shipping to construction don’t have scalable protocols for reusing and recycling the stuff, and consequently, 12.2 million tons of wood went into U.S. landfills in 2018, according to the most recent EPA figures. The sources of this waste include furniture, cabinetry, packaging, building materials, and miscellaneous items. And when it comes to the media darling that is mass timber, the end-of-life reuse applications for cross-laminated timber (CLT) and related engineered products remain largely unknown and will likely remain so for some time. (These buildings aren’t that old!)
Of course, innovations abound. California start-up Urban Machine is streamlining the reclaimed lumber market, and diverting a lot of waste in the process. In my home state of Maine, the University of Maine’s Advanced Structures and Composites Center famously built a 3D-printed home out of repurposed wood fiber and cellulose, and late last year, TimberHP began rolling out its three lines of wood fiber insulation (fill, batt, and continuous board), made from residual softwoods.
These innovations are each solving interrelated issues tied to pervasive waste. But in each case, the cellular structure of the raw source material remains largely the same. The composition may change, but the wood continues to behave like wood, more or less. This doesn’t always have to be the case.
From wood to “medal”
In Frederick County, Maryland, the start-up InventWood is currently fitting out a nearly 89,000-sq.-ft. manufacturing facility where it plans to ramp up production of MettleWood, the company’s first-to-market technology. (The company received a $20 million grant from the U.S. Department of Energy in 2022 as part of the agency’s innovation arm, the Advanced Research Projects Agency–Energy’s, or ARPA-E, SCALEUP program.) What makes this product stand out, relative to other wood-based building materials, is the degree to which the source material is manipulated to yield something that still looks like wood—because it is—but behaves quite differently.
“It feels very much like petrified wood, it’s very smooth. It doesn’t feel at all like regular wood,” the company’s CEO Josh Cable told me over Zoom, holding a small MettleWood sample up to the camera. To achieve this, lignin, the wood’s natural glue that binds cellulose fibers, is removed, thus allowing the cellulose (the key ingredient for wood pulp) to achieve a sponge-like consistency that can be compressed and concentrated, making a product that is one-fifth the volume of the original wood but with a 1200% increase in tensile strength. The removal of lignin, known as delignification, initially lightens the wood. Subsequent densification naturally darkens the wood, lending the end product a copperish patina.
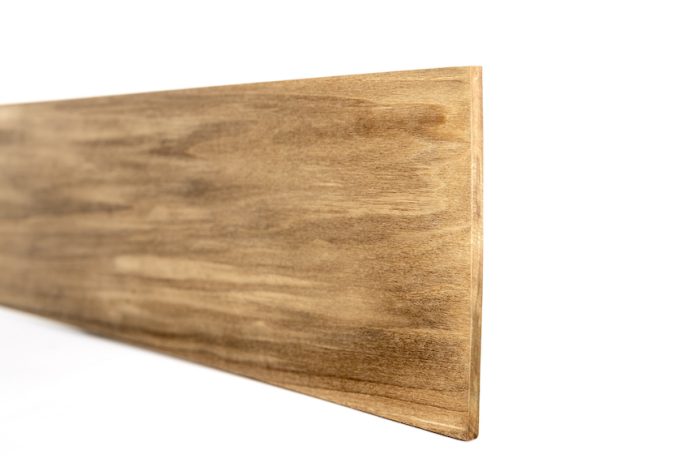
The company claims that MettleWood is 80% lighter and 50% stronger than steel, with a tensile strength of 85,000 PSI. It is also cheaper to manufacture, sustainably sourced, and highly resistant to moisture, infestation, and fire. (InventWood is targeting a Class A fire rating.) The company also says this product has the potential to replace up to 80% of the world’s steel and concrete, thus largely eliminating, in theory, the combined roughly 15% of global GHG emissions that stem from these building materials. And unlike mass timber products, which are made almost exclusively from softwoods like spruce, pine, and fir, MettleWood is an aggregate of various hardwood and softwood species, including invasive species, the removal of which can help restore ecosystems.
For the time being, InventWood’s pilot facility is using several species of Poplar to feed early production. Cable says they are looking at several possible feedstocks, including the so-called “tree of heaven,” a highly invasive, resilient, and self-cloning species, now found throughout the U.S. and parts of Europe, that botanists have called a “noxious weed.” “The question isn’t about the technology or even the economics of it, but about supply,” Cable says. “We’re going to need a good amount of supply to make the MettleWood volumes that we want to.”
The most abundant material
Once the Maryland facility officially comes online, with a target date of 2025, InventWood is intent on manufacturing 1 million square feet of MettleWood every year, all using materials that have been certified under Sustainable Forestry Initiative (SFI) or Forest Stewardship Council (FSC) standards. “That number still makes us a small player in the wood industry, at least in the beginning,” Cable says. “And so the idea is, as we grow, we’ll be able to exert more leverage over suppliers to ensure sustainability.” He estimates that InventWood can eventually scale up in the form of multiple facilities that can individually produce between 50-100 million square feet per year. Cable’s target date for this iteration is some time in 2026.
While things like supply and responsible stewardship are top of mind for the company’s CEO, the technology at the heart of its operation is far from an afterthought.
Cellulose is the most abundant biomaterial on the planet. When the first paper-based materials were created in China, more than 2,000 years ago, the process, according to a 2020 study in Forest Products Journal, “was based on the hydration of plant tissues in water, followed by cutting and pressing of the material. By doing this, a thin network of cellulose fibers was formed onto a fabric leading to the production of the first paper sheet.” Of course, with a steady decline in paper consumption and production over the last 50 years, industry has had to pivot and find more practical (and sustainable) applications for the base material.
InventWood’s founder, Liangbing Hu, director of the Center for Materials Innovation at University of Maryland’s school of engineering, knows the history of cellulose-based technology inside and out. But his real trade is finding innovative and low-impact ways to harness wood nanotechnology.
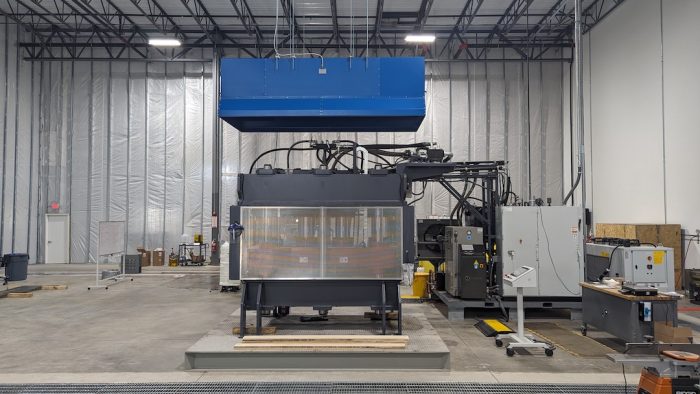
“The smallest dimension of wood is the nanofiber,” Hu says. (The diameter of a nanofiber is about 5 nanometers; 1 nanometer = 1/10,000,000 of a centimeter.) “These have amazing properties and are stronger than the best carbon fibers. The question then becomes how to assemble them.” About eight years ago, by Hu’s estimate, he and his colleagues devised a way to manipulate cellulose nanofibers without separating the fibers from the wood, but rather “exposing” them and “chemically altering the pores of the wood.”
This molecular intervention has led Hu and his team to develop a number of other cellulose-based products, including “moldable” wood, a process that uses cell wall engineering to shape flat sheets of hardwood into versatile 3D structures; and “aesthetic,” aka transparent wood, in which wood is “selectively delignified” and rendered nearly clear while preserving the wood’s natural patterns.
Does steel deserve the bad rap?
In terms of applications, it not just floors, walls, and structural columns that InventWood is eyeing to disrupt with its MettleWood product, but the aerospace and shipping industries, HVAC equipment, automobiles, and even wind turbines. The company also promotes its product’s advantages over steel in terms of weight, safety, material sourcing (harvesting vs. strip mining), and costs related to transportation and manufacturing. That is all fair game. Yet the company’s stated intent of replacing upwards of 80% of the world’s steel and concrete, while laudable on its face, does feel like a hasty figure to be throwing about.
The steel and concrete industries would do well to police themselves and green up their act, from supply chain to installation. As time has shown, particularly in just the last ten years, there are innovative, scalable, and cost-efficient ways of manufacturing steel and concrete on just a fraction of the carbon budget that has been the standard for centuries.
America’s largest steel producer, Nucor, also happens to be the largest recycler of steel in North America, which it achieves by largely using electric arc furnaces for melting and recirculating of scrap steel in place of high carbon–emitting blast furnaces to melt pig iron. Meanwhile, low-carbon concrete products are already being used to revamp large chunks of the country’s infrastructure. And finally, while engineered wood has enormous potential—both realized and theoretical—to supplant ubiquitous steel and concrete in select cases, it is far from the panacea many want it to be.
That said, it is premature to position this product as a wholesale replacement, and it is disingenuous to lump MettleWood in with other engineered wood building materials like CLT and the like. The latter, when you think about it, are simply examples of ancient technology being done a whole lot better. MettleWood does indeed represent a new frontier in building technology, and any degree of scaling up its manufacturer can achieve in the coming years is inarguably a good thing. If we can operate in a world where its most abundant biomass source is also its most durable building material, that would come to embody the very definition of sustainable and regenerative industry.
_______________________________________________________________________
Justin R. Wolf is a Maine-based writer who covers green building trends and energy policy.
Weekly Newsletter
Get building science and energy efficiency advice, plus special offers, in your inbox.
2 Comments
That is an incredibly high PSI rating. The types of woods we typically use in construction can handle 500-1500 psi in tension; simply removing the lignin increases that by 85 times?! I'm not sure where they got the 1200% figure; that math doesn't make sense to me, but maybe I'm missing something. The steel we use in construction these days is usually capable of 50,000 psi in tension, which would be a 70% increase, not 100%. But some steel is rated for 36,000 psi, so maybe they're just using an average. In any case, impressive feat.
I'm not surprised that this amount of strength is achievable after removing the lignin. But since the material is compressed to 20% of it's original volume, that's a lot of wood consumption. Good thing the goal is to use invasive species eventually. Are synthetic adhesives required so that the material holds its compressed size and shape? If not, will the material swell after exposure to water?
Log in or create an account to post a comment.
Sign up Log in